The Way Ahead Technical Leader Interview invites senior figures who have become pioneers of innovation and technical excellence within the E&P industry to share their wisdom, experience, and deep knowledge with young E&P professionals around the globe. Each interview will be a candid conversation that explores the careers, advice, and vision of these successful individuals while aiming to uncover lessons learned that have made each of these individuals prominent technical leaders. Interviews will include representatives from such technical disciplines as drilling and completions; production and operations; reservoir description and dynamics; formation evaluation; facilities and construction; health, safety, and environment; and management and information. The editors of The Way Ahead hope that these interviews will be enlightening to young E&P professionals who want to become technical or managerial leaders, or perhaps both.
For our first interview, we travel to America’s heartland to meet Carl Montgomery, Senior Engineering Fellow with ConocoPhillips, in Bartlesville, Oklahoma, the location of ConocoPhillips’ technology headquarters and home of Frank Phillips, legendary oilman. Montgomery earned the 2006 SPE Drilling and Completions Award for his pioneering contributions to nonconventional well-stimulation techniques and his numerous achievements that have advanced completion technology.
Tim Crumrine, Technical Leader Section Editor
Anthony Onukwu, Technical Leader Section Editor
Considering that your background is in biochemistry, what in your early life led you to choose a career in the E&P industry?
Mostly hunger. One thing that does not show up in my E&P history is that I was a secondary-school science teacher for 6 years. It was in a small school in southeastern Colorado (Wiley, Colorado), and I taught all the junior and senior high school science at that school. It was a wonderful experience, and I was good at it—I was elected to Outstanding Educators of America in my fourth year and was runner-up as Colorado’s teacher of the year in my fifth year. But it certainly did not pay the rent. There were a couple of things I took away from the experience, though, that I still use today. The first is the ability to get up in front of a group of people and express myself in a manner and method that keeps the group interested and involved. The ability to explain or demonstrate something at a level that gets everyone involved quickly has been one of the keys to my success. The second is the fact that the best way to learn something is to teach it. I taught all the sciences including chemistry and physics, along with some of the math classes, and I can tell you that being versed in the basics of those subjects has been invaluable.
What was your first job in the industry, and what was your impression of the industry when you first joined? How has your view of the industry changed?
When I was a teacher, I was going to the Colorado School of Mines during the summer under a scholarship and studying petroleum engineering. We had a field trip to a well location, and Dowell was doing a cement job on a well. The engineer on the job asked me if I was interested in a job and to give him a call. I did that the next day, and they offered me a job that paid three times what I was making as a teacher. I wanted to work in their research laboratory, but they told me to stay in the field for a year, learn everything I could, and then they would see. They also had a training course I had to pass before they would consider the move. I took that job, and during that year I learned to operate every piece of equipment that Dowell operated, from sand truck to DC8 cementer. Before the year was out, I passed that training course, and I was designing and treating wells and in charge of a frac crew. The region wanted to keep me, but I still wanted to go to the research laboratory. Dowell honored that promise, but I can tell you that the field experience I got that first year is still a big plus in my job.
Today the industry is a completely different place to work than it was when I started. We did a lot of things when I was first “breaking out” that are almost laughable when you think about them today. The industry is much more caring and people sensitive today. Things like safety glasses, Nomex coveralls, and obeying U.S. Dept. of Transportation work rules were talked about, but managers viewed them as costs rather than cost savers. On the other hand, people talk about how much better the technology is today than it was then, and some of that is true, but I think it was much easier to introduce new technology then than it is now. Everyone had an active research laboratory in those days, and we were doing real research, not just tech service. Things like coiled tubing, high-strength proppants, sand-control gravel sizing, horizontal-drilling technology, and more were being developed and tested in the field. The industry seems to be much more risk-averse today and unwilling or unable to fund and develop new ideas. I know those ideas are out there, but getting them to a field-practice level is very difficult.
What advice would you give to professionals in the early stages of their E&P careers who are seeking a technical career track?
When I was first going to work, the most memorable piece of advice I remember my Dad giving me was, “Carl, they hired you to solve problems, not make them.” I have tried to take that to heart and remember it whenever I start getting discouraged. There are several other pieces of advice I would give. The first is to take advantage of all the learning opportunities that are available and to be proactive in creating them. Second is to learn to express yourself in a manner that is easy to understand for everyone and that sells your ideas or thoughts at a level appropriate to the audience. Third is to take every opportunity offered to you. Don’t worry about the promotions; just take the opportunity, and the promotions will come.
It seems that many young professionals, almost two-thirds, are hoping for a career in management. Would your advice change for these young professionals?
People want to be managers because they think they will make more money or have a bigger influence on the things they think are important. There are a few managers who make more money than a senior technical person, but when you look at it realistically, there are not that many. Although he may not have anyone “working” for him, a senior technical person has a tremendous impact on what is done in an area. When I was a manager, I can tell you that I wasn’t having much fun. I spent almost all my time dealing with people issues, budgets, time lines, and monthly reports. Some people like that, but for me it was not where I wanted to be. I wanted to be as close to the wellhead as I could get. I wanted to solve problems that had a direct impact on the productivity of the well. I wanted to work on new ideas. I wanted people coming to me and asking questions because I was the best technical person on the subject in the world. A good technical person should strive to be a “leader” in a chosen field, and influence will quickly be there.
What issues do you care most about in your work and your life? With these in mind, what advice would you give young E&P professionals?
Of course the love of my life, my wife, and the family always come first. I travel a lot in my job, but at one time it was much more than now. One of the main reasons I changed jobs when I left Dowell was to have more time at home. There is always a balance between work and your private life, and if work is taking too much, you need to think about your priorities. There is actually a lesson that the human resources community can take from this to help retain employees. It is my experience that people who were born after about 1970 are motivated mainly by free time, not money. They would rather have some additional vacation or days off and will work much harder during their work schedule to get this benefit.
What are the key technology challenges you see for the E&P industry now and in the next 10 years? What can young E&P professionals do to help?
Unconventional resources have been and will continue to be the big challenge. We continue to discover conventional hydrocarbon sources, but they are coming at a higher price. At some point, the price curve for conventional is going to cross the cost to recover unconventional resources. I don’t think it has yet, but when it does, the companies or individuals that are ready will make a lot of money and be in huge demand. The first thing that will come to the front is heavy or viscous oil. This is already happening, but you will see a large increase in areas where this oil is currently more difficult to recover. As demand outpaces supply, you will see an increase in activity in oil shale. On the gas side, we are going deeper and into tighter, hotter reservoirs where stimulation is the big key. If gas demand increases, hydrates will come into play. A lot of people I meet have these preconceived notions that a particular technology won’t work. A young professional who is free thinking and has a strong drive with the ability to sell and develop his/her ideas will help get these resources to market.
Do you think the industry as a whole values technical roles as much as managerial roles?
Probably not. People like power, and the big power is with the management. People like to have control, lots of control, and they think that unless they are a manager they cannot get this control. I think if you work smart and tough, you can have a tremendous impact on your work that will have a much longer positive effect than most managers. People remember who Babe Ruth was but ask them who his manager was and nobody knows.
How did you get involved in SPE? What has your SPE membership meant to you?
Continuing education is a difficult thing to do when you are busy, but I knew to be successful you needed to make a conscious effort to keep trained. SPE offers that opportunity. I started by getting involved in the paper review process. Committing to review one paper a month forced me to read and understand at least that many papers in a year. I did that for 18 years and was then asked to be the Executive Editor for the SPE Production & Facilities journal, which allowed me to read and understand the best of the best. Because SPE has been so beneficial to me, I felt I needed to give something back, so I also got involved in the management strategy of the Society. I started at the regional level by being proactive at the meetings. It wasn’t long before I was a Regional Director. I am now serving as the Technical Director for Drilling and Completions on the Society’s Board. As I became more adept technically, I was asked to be a Distinguished Lecturer. This experience is one of the highlights of my career. I went more places and made more contacts than I ever imagined possible. I enjoyed this so much and had such good reviews (this comes back to putting your knowledge forward in a manner everyone can understand) that I was asked to be a member of the Distinguished Lecturer selection committee. I did this and finished my service there as Chairperson. The involvement I have had in the Society has been invaluable to my career. SPE provides the technical information there for the taking. All you have to do is reach out and grab it.
Do you believe the industry recognizes the value of involvement in SPE activities? Do different segments of the industry value it more?
Because I sit on the management board for the Society, I see a huge difference in the value various companies place on SPE. Companies like Chevron, BP, Shell, Halliburton, BJ Services, and Schlumberger really encourage their people to participate and put their money out there to prove it. If you look at the eLibrary on spe.org, you will see Chevron’s name because they gave a very generous contribution to support enhancement of the website. Several companies have made contributions to get younger SPE members involved in SPE. Halliburton pays the dues for SPE student members, and BJ Services pays for an eLibrary subscription for universities that have an SPE student chapter. Schlumberger and Saudi Aramco sponsor The Way Ahead. Companies like this understand the tremendous value SPE offers, and they take advantage of that value.
On the other hand, many companies do not understand the value of SPE. They want employees to be working on issues that will impact their bottom line and do not encourage much involvement in SPE. As an employee, you need to be sensitive to this issue and try and work your SPE activities into your schedule without interfering with your normal workload.
Finally, because you have had a varied career working for a service company and operators, what would you say if you had to give a brief speech to young E&P professionals about the attractions of the industry, and specifically the technical challenges of working for an operator vs. a service company?
When I quit Dowell, Ken Nolte (pioneer of the famous paper on the Nolte/Smith analysis techniques we use today), who had worked for Amoco and then Dowell Schlumberger, wrote me a long letter telling me that it was a mistake to quit and go to work for an operator. In essence, he told me that the really great thing about working for a service company is the very wide variety of problems and reservoirs you get to work on. However, I was struggling some because I never saw the results of my work (except, of course, when the work failed). I wanted to see what happened to the wells I worked on, to see the benefits of a good completion and to have more control over what was being done on a particular well. I was somewhat naive in this view because, after working for an operator for some time, I found that in many cases the operator just turned the well over to the service company and did what the service company told them to do. Service companies have put “desk engineers” into the operators’ offices, and they have a lot of say in what is to be done in a particular well. The really great thing about this is that it keeps me in a job. By having experience on both sides, I know how the service company thinks, and I also know what is best for the wells that are now mine.
Do you want to know more about this topic or comment on this article? Visit the Young Professionals Network at www.spe.org.
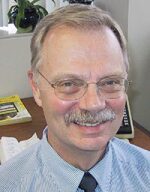
Carl Montgomery joined ConocoPhillips in Bartlesville, Oklahoma, in 2000 and has more than 30 years of experience in the industry. Before joining ConocoPhillips, he worked for Arco for 11 years and Dowell Schlumberger for 17 years on assignments that took him all over the world. Montgomery is recognized within the industry as one of the leaders in all areas of stimulation, including hydraulic fracturing, acid fracturing, matrix stimulation, cavity completions, waste/cuttings injection, rock mechanics, and scale prevention/removal. He also has considerable experience in cementing, sand management, conformance control, perforating strategy, and formation damage.
Montgomery was appointed Special Member of the petroleum engineering graduate faculty at the U. of Oklahoma from 1993 to 1995. He is the recipient of the 1996 Arco E&P Award of Excellence and the 1997 Special Meritorious Award for Engineering Innovation. Currently serving as SPE Technical Director for Drilling and Completions, Montgomery’s lengthy involvement with the Society includes serving as Director of the SPE Mid-Continent Section, SPE Distinguished Lecturer, and Executive Editor of SPE Production & Facilities journal. He has been session chairperson at several SPE conferences and chaired the first SPE Applied Technology Workshop on Applied Multilateral Technology. Montgomery earned an MS degree in biochemistry from Ball State U.