The Fourth Industrial Revolution, or Industry 4.0, has ushered in several changes in the oil and gas industry—all with a unified goal of improving, optimizing, and digitizing existing processes and techniques. Within a few years of its introduction, Industry 4.0 practices have become ingrained in the system. In the areas of well exploration, 4D seismic data is helping geologists analyze the throughput from a potential reservoir and provide decision pointers. Site drilling data can now be recorded and processed, leading to a significant reduction in well drilling times. Digitization of the supply chain faction offers the potential of reducing procurement costs by 20%, reducing supply chain process costs by about 50%, and enhancing revenue by 10% (Rigzone, 2019). Downhole sensors (drilling, monitoring) now enable keeping a tab on important reservoir characteristics in real time, while acting upon those data will essentially help with preventive health maintenance of tools deployed downhole with high service life. Automation across the whole value chain of the industry—exploration, production, supply chain, engineering, and manufacturing—has now enabled systems and processes to be connected in the Industrial Internet of Things (IIoT) framework.
[Click to expand.]
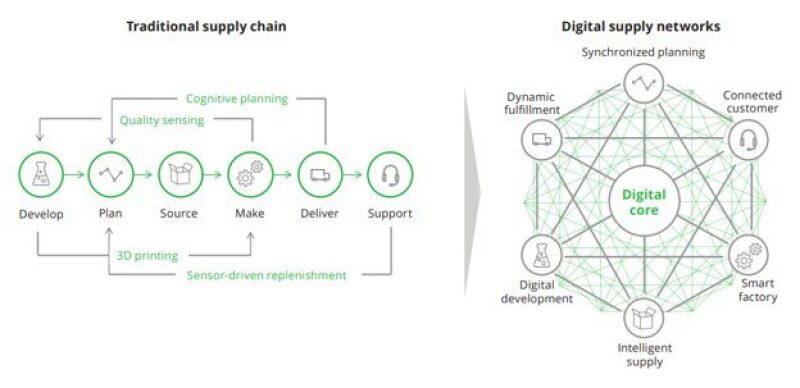
Fig. 1—Shift from traditional supply chain to digital supply network. Source: Delloite Insights
While the façade painted by IIoT and data-driven processes is one of an environment that is heavily guided by computers, it actually calls for an evolved workforce that is able to use the data to enhance their design and decision-making skills. “Agile development” and “sprints” are finding ways into the traditional design engineering process, with sizeable projects being broken down into minimal viable products. These can be further iterated, improved, and optimized for maximum project throughput. With data becoming every company’s most prized asset, data thinking is evolving into a critical workforce skill through all strata of the industry. This disruptive growth environment also means that strategies that worked for the business yesterday may not be as promising today, calling for the need for personnel to adapt and be flexible with frequent changes. Additionally, while data automation and artificial intelligence can add more meaning to conventional processes, creativity, and critical thinking to use these techniques to obtain maximum throughput remains a prerogative on the people involved in the process.
With the evolving industry, the workforce needs to evolve as well—with a growing emphasis on the ability to adapt, explore, and incorporate digitization in their day jobs. Take for instance design engineers in industries as diverse as oil and gas, automotive, and aviation. Apart from designing products that fulfill basic customer requirements, there is a growing emphasis on minimizing the efforts and time spent over design iterations and being able to visualize the repercussions of smallest design changes in the grand scheme of things. Software that allows an engineer to develop digital twins are becoming prolific in the design process and thus enabling rapid digital prototyping and concept selection. This requires engineers who are working on these projects to now invest their energy towards breaking down the big project into small, individual tasks, and to develop interfaces between all moving parts and be able to replicate them all digitally.
With the wheel cogs moving towards increased automation, it is necessary for the industry’s workforce to be prepared with essential skills that will help them, and the products they create to adapt to the changing demands. Data being the key driver towards automation and intelligence, it is essential to collect and analyze data and maintain usable databases. With an increasing number of sensors being used in the oil field, there is a need for engineers, analytics specialists, and instrumentation technologists to develop modules that build on this data (Oil and Gas IQ 2017). This also calls for information technology and instrumentation technologists to install, maintain, and upgrade more systems in the field.
Field engineering jobs that were traditionally reserved for petrotechnical experts will now see an increasing surge of diverse skillset workforce coming in; thus making the entire process coherent. Overall, industry professionals, on-the-field and off-field alike would need to develop technology-based proficiencies that are deeply rooted in traditional knowledge about the industry, along with the ability to analyze field data in real-time, make course-corrections, and innovate (PetroLMI 2018).
[Click to expand.]
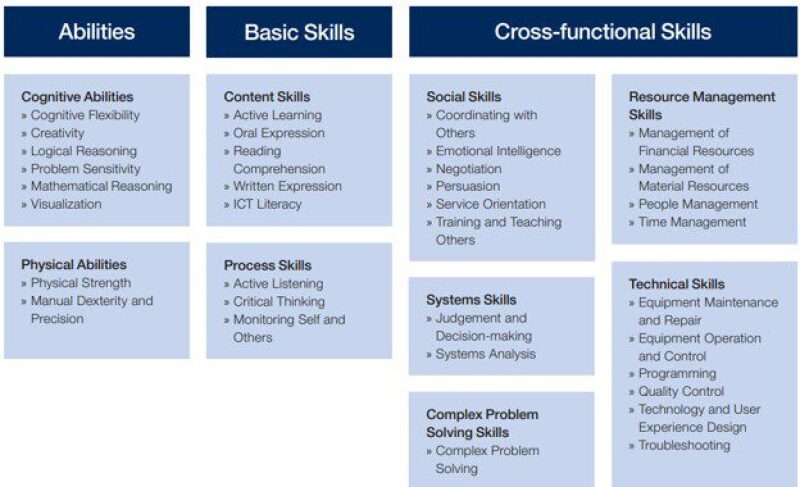
Fig. 2—World Economic Forum Core work-related skills as listed in the Future of Jobs Report, 2020
In addition to all key technological skills discussed above, the World Economic Forum highlights ten essential skills that will boost the Industry 4.0 transformation. Cognitive skills such as creativity, logical reasoning, and problem sensitivity will be crucial to make the most advantage out of multiple systems connected through IIoT. Following in similar veins, systems skills such as judgment/decision making, and systems-level analysis will come handy; for example, while designing digital twins of an entire oil well and taking a call over what could be the best production strategy. At the same time, people and resource management, and social skills such as emotional intelligence and multidisciplinary coordination will ensure fluid communication across different strata of the industry undergoing disruptive changes.
In conclusion, digitalization and Industry 4.0 bring to the oil and gas industry a brilliant opportunity to develop and implement highly efficient processes to maximize its returns. As the people driving this change, it is essential that we face this challenge head-on, and be aligned to the ever-changing demands during the times ahead.

Umema Bohari is a mechanical engineer at Schlumberger's Flow Control & Reservoir Monitoring technology group in Houston. Her work involves dealing with different aspects of design, development, and qualification of different flow control valves in the company’s portfolio. She completed her master’s degree in mechanical engineering from Texas A&M University, where her research involved engineering design, optimization, and data-driven & machine learning enabled product design. Before pursuing her MS, Bohari worked at Eaton Technologies’ Industrial Support & Electrical Systems portfolio in India.