Expectations and requirements for subsea-well emergency response preparedness were stepped up as a result of the Macondo blowout and oil spill that began 20 April 2010 in the US Gulf of Mexico. A key change is the requirement to have subsea capping stacks ready to be deployed that are capable of handling the specific blowout scenarios projected for each GOM well, no matter how challenging.
It is very important to distinguish between a subsea blowout preventer (BOP) and a subsea capping stack. The name of each piece of equipment gives some useful clues. As the names implies, a BOP is a safety device meant to prevent a blowout from occurring—that is, to prevent an uncontrolled flow of liquids and gases from reaching the surface. The BOP is always present when drilling, and any time the drilling team suspects fluids and/or gases could be released from the wellbore in an uncontrolled manner, they can activate the BOP to prevent such an outcome.
A capping stack is not needed when drilling. It is the centerpiece of a containment system kept in readiness at an onshore location. It is only deployed after the BOP has failed to serve its purpose and a blowout has occurred. A “capping stack” is a piece of equipment that is placed over the blown-out well as a “cap.” Its purpose is to stop or redirect the flow of hydrocarbons and to buy time for engineers to permanently seal the well. It is massive and can weigh as much as 50 to 100 tons, presenting logistical challenges in quickly transporting it to the emergency occurring at the blown-out offshore well.
Before the capping stack arrives, a remotely operated vehicle (ROV) inspects the seabed site and engineers zero in on precisely what equipment is needed. Then debris is removed and the wellhead is prepared. After the equipment arrives, the capping stack is carefully maneuvered into place over the wellhead.
Once fully operational, the capping stack provides a dual barrier for containment—a BOP ram, plus a containment cap. The stack’s valves can be closed to cap the well (“cap only”) or, if necessary, the flow can be redirected to surface vessels through flexible pipes and risers (“cap and flow”).
Macondo Changed Requirements for Offshore Blowout Intervention
A capping stack had never been developed for or used before 2010 specifically to contain a deepwater blowout. In 2010, while the Macondo well was still leaking, other ways of containing the flow of oil were tried—including a containment dome (7 May), top kill and junk shot (26 May), a cap for funneling oil and gas to a surface ship (3 June)—all of which failed.
Meanwhile, the first capping stack specifically designed for the leaking Macondo well (Fig. 1) was being put together. It was a basic design consisting of three rams, a wellhead connector, a mandrel on top, a couple of double-block drilling valves on the choke-and-kill outlets of the middle ram, and associated ROV panels. It was installed on the lower marine riser package on 12 July.
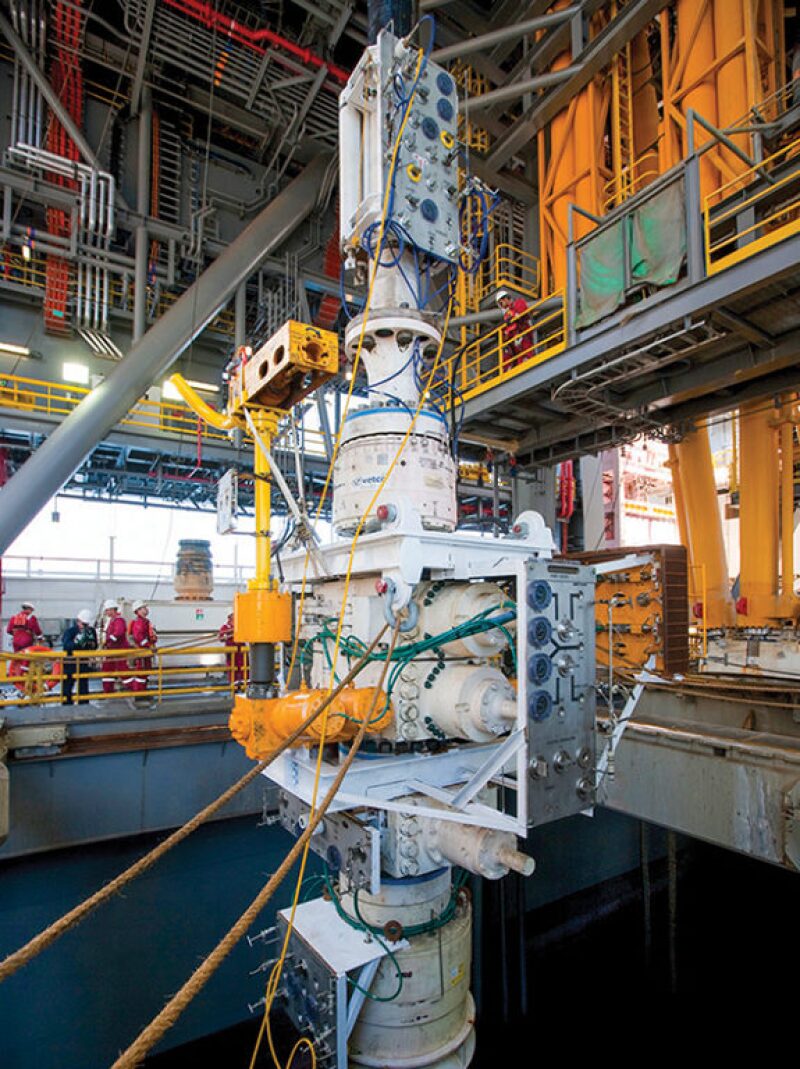
This system did successfully cap the well, and provided the opportunity for engineers to perform a static kill (3 August), drill a relief well during August, and finally complete a bottom kill, which led to the US federal government declaring the well dead (September 21).
One of the immediate deficiencies noted was the lack of a readily available backup capping stack for use should the first one fail. Fortunately, it didn’t fail, but until the well was declared dead, several alternative designs for capping stacks were quickly generated.
On 22 July 2010, four major GOM oil and gas operators committed to establish a nonprofit company devoted to providing always-ready state-of-the-art emergency well containment services and technology to all operators in the US GOM. The resulting company, the Marine Well Containment Company (MWCC) consortium, was created 10 December 2010 and by 31 March 2011, consisted of 10 member companies.
Today, consortia such as the MWCC, the Helix Well Containment Group in the US, and the Emergency Preparedness Offshore Liaison Group in the UK continue to advance their capabilities so their members can go on safely exploring for new sources of oil.
Offshore Deployment
The basic operational need of the stack is to attach and seal on a subsea well during an active blowout, then shut in safely. To achieve this, first a mandrel or hub profile must be exposed (either at the wellhead or on top of the BOP). In special circumstances, a “crossover” transition spool can be installed for interface to the capping stack, similar to what was done to install the Macondo capping stack.
The running tool for the stack must take into account the flow coming from the blown-out well. Computational fluid dynamic (CFD) studies have been conducted showing that when installing a capping stack in deep water on a high flow rate blowout well, as the stack is positioned over the plume and as it approaches the wellhead interface, a water post-effect occurs allowing stability and centralization of the stack in relation to the wellhead. This is very convenient!
In fact, Bernoulli’s principle helps explain the water post-effect in that the fluid flow out the top of the well and through the capping stack bore creates a force-centering effect on the stack when it is being landed, thus aiding in the make-up of the stack to the wellhead mandrel.
Running to Depth and Installation
There are typically two types of running tools available for use with capping stacks to date.
One type is a connector designated “H4” with a large-bore perforated pipe section or open pipe section that allows the same through-flow as one single 18¾-in. bore. The second type is a spreader bar that attaches to a frame with the bore completely unimpeded.
The stack can be installed with the outlets open or closed, but each blowout scenario has to be analyzed to determine what will handle flow best.
For example, in some cases, having the outlets open could cause a “Venturi effect”—a jet effect that results in a reduction in fluid pressure and could create hydrate formation problems in deepwater scenarios as seawater is inadvertently sucked into the bore. If possible, it is preferred that the bores are opened when installing the stack because this reduces the number of subsea operations that must be performed by the ROV to cap a well, thereby reducing overall response time.
On at least two outlets there is also a subsea connector with a choke package. The chokes are used to “soft shut in” the well, meaning that the chokes slowly constrict flow from the well by gradually restricting the outlet bore size such that the flow gradually reduces to near zero. As chokes are wear items and take the full differential pressure of shutting in the well, they are placed on subsea connectors such that they are removable and serviceable with the stack in place.
Each choke is individually shut in by the ROV. Since a closed choke is not considered a barrier, once the choke is shut in, the gate valve in line with it will also be shut. As a result, erosion wear on the valve sealing surfaces is minimized since there is little to zero flow and pressure drop through the valve during actuation, providing a recognized sealing barrier on each outlet.
More Capping Stack Capabilities
During the capping operation, chemicals can be injected into the well through several strategically placed chemical injection ports (Fig. 2). These ports are located upstream of all sealing devices in the diverter spool central bore, and on the four outlets on the stack. This allows an operator the option of injecting into multiple locations on the stack.
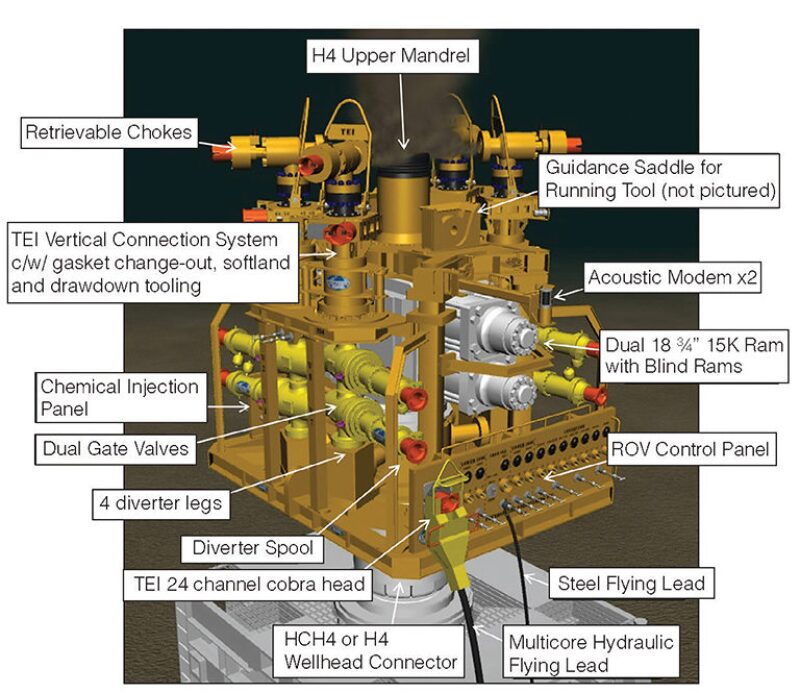
For example, dispersant could be injected into any or all of the ports to minimize the environmental impact of the oil flowing out of the blown-out well thereby minimizing the oil sheen on the surface. Methanol or glycol could also be injected to mitigate the formation of hydrates in deepwater capping scenarios.
In addition to the ports, sensors are placed on the diverter spool to monitor pressure and temperature during all shut-in operations. To transmit this information to the surface, an acoustic system is fitted on the stack that transmits pressure and temperature readings through acoustic signals. The signals are picked up at the surface by a computer and a dunker that contains a surface-deployed directional acoustic transducer and the transceiver electronics. The acoustic system is powered by a local replaceable battery on the capping stack, eliminating the need to run a cable or subsea umbilical during capping stack installation operations.
Offshore Capping Stack Controls
All controls on the stack are direct hydraulic from an ROV stab or operated by an ROV torque tool. This control philosophy is robust, and easy to understand and operate under emergency capping scenarios. Once all gate valves on the outlets and the BOP are shut in, the well is considered capped, though the operator can continue to inject chemicals as needed and can continue to monitor pressure and temperature.
It is an industry-recommended practice that two barriers (e.g., rams and gate valves) exist between hydrocarbons and the environment. To achieve this once the stack is shut in, the running tool is removed and a secondary cap is installed to seal the bore with a metal VX-type seal on the upper H4 mandrel instead of relying on the rams’ rubber seal. Also, the subsea connectors with chokes are removed and replaced by connectors with blind rams to provide the secondary barrier on all the outlets.
In some well control cases, it may make sense to pump kill fluids down the stack. In that scenario, the subsea con-nectors with chokes can be replaced by subsea connectors with flowlines running to the surface for pumping down kill fluids such as mud or cement. The idea is that the capping stack will only be shut in long enough to drill the relief well to kill the well at its source and cement it in.
The Future of Well Containment
Today, specialized service companies have built a portfolio of capping stacks for every offshore scenario, including systems uniquely designed for shallow-water Arctic drilling operations, for which glory holes (also known as well cellars) are excavated below the seafloor to protect well equipment such as BOPs from ice ridge scouring. Capping solutions have also been developed for tension leg platforms that have a forest of risers underneath them, with some risers no farther apart than 15 ft, requiring a very compact capping stack that can be maneuvered and installed in close proximity to other wells.
International communities of operators, such as UK-based Oil Spill Response Ltd. (OSRL), formed in 1985, now have specific efforts devoted to emergency subsea well intervention services and technology. OSRL’s Subsea Well Intervention Service stores and maintains capping stack equipment across four regions, with locations in Norway, Singapore, South Africa, and Brazil.
In addition, emergency offshore containment companies have evolved the containment system approach to address the time and vast amount of resources it takes to mobilize a capping stack after an incident has occurred. Since a capping stack’s immensity and weight present time-consuming logistical challenges, the next step in subsea source control hardware is to bring response capability closer to the drilling operation. The Mudline Containment Device (MCD) is a type of capping stack that provides direct capping and containment capability in a drill-through package.
Having an MCD in place in lieu of or while waiting for the arrival of a capping stack could greatly reduce emergency containment response time should a well control incident arise. The MCD is installed directly on the wellhead and features an independent control system and power supply to act as a backup to traditional drilling control systems.
Regardless of the type, subsea capping stacks’ existence and deployment-readiness are now the norm. As the subsea drilling industry continues to evolve, more solutions are emerging for subsea blowout containment. Subsea capping stacks are undoubtedly here to stay and have added greatly to the offshore oil and gas industry’s emergency preparedness and response capabilities.
Mauricio Madrid is director of projects at Trendsetter Engineering, Inc. In addition to being responsible for overall project management oversight, he also manages multiple project teams with technical and commercial disciplines to develop, register, and commercialize multiple high quality, differentiated, and proprietary products for the company. Madrid serves Trendsetter Engineering in overall project coordination, planning and execution, cost and schedule management, and design management, ensuring the company meets its commitment to quality and safety. Beginning his career at ExxonMobil Development Company, he has worked exclusively in the oil and gas industry as a subsea engineer/project manager. Madrid earned a BS degree in mechanical engineering from Texas A&M University.
Tony Matson, project manager, is responsible for the execution and delivery of multiple projects at Trendsetter Engineering, Inc., including managing their commercial and technical aspects. He has an extensive background in project controls disciplines. Since joining Trendsetter Engineering, Matson has developed and implemented fundamental project controls processes enabling improved project performance. Responsibilities include project planning, coordination and execution, cost and schedule management, and design management. Matson joined Trendsetter Engineering in 2012 after working in downstream petrochemical construction for a major engineering, procurement, and construction contractor. Before working in oil and gas, he worked in automotive manufacturing and earned a BS degree in management from Kettering University in Flint, Michigan.