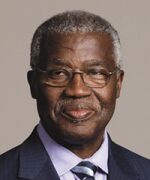
The first wells used to search for oil were drilled more than 150 years ago. Since then, various innovations have been adopted and adapted to enable us to drill deeper and deeper wells, with longer and longer reach, and in ever-increasing water depths, resulting in access to oil and gas reserves that have fundamentally changed the world. We have encountered various challenges over the years, but by seeking new ways of getting the bit down to the depth required in a safe manner, our industry has allowed billions of barrels of oil and trillions of cubic feet of gas to be produced for industrial growth and development. Those first wells were drilled with very
basic tools. The floaters of today, drilling in thousands of feet of water, are clearly far advanced from the early efforts, which used a steam engine powered by a wood-fired boiler.
Edwin Drake is famous for his pioneering drilling work, and as with most innovators, he met head on with potential failure when he drilled his first well. Drake encountered losses and potential hole collapse that would have prevented him from drilling to his planned total depth. He is reported to have driven a surface pipe and then proceeded to drill and reach into deeper horizons. This fundamental principle of isolation has served the industry well and forms the basic design of wells drilled today. However, innovation has permitted some operators to drill through surface sections that present swelling problems that lead to premature setting of surface pipe, which in turn lead to delays in drilling operations and increased well cost. Some operators have successfully applied innovative casing-while-drilling techniques, which use large pipes as the drilling string. This technique allows the operator to minimize exposure of the wellbore to the drilling fluids and reach surface setting depth as planned (Sánchez, Houqani, Turki, and Cruz. 2012).
The history of drilling is rich with innovations. They are too many to cover in one column, but I think two are noteworthy: the advances that permitted drilling in deeper and deeper waters and the development of mud motors.
The early move away from land operations took place approximately 120 years ago when wells were drilled from platforms that were constructed on piles in fresh water and then on piers in various areas offshore the US. As explorers found prospects in deeper and deeper waters, new technology was needed to drill from barges, artificial islands, or concrete barges. Today’s jack-ups and semi-submersibles are a far departure from the rudimentary equipment used for early offshore drilling.
With most breakthroughs, innovation comes with an acute observation of events that go unnoticed to less focused minds. This was the case with the emergence of semisubmersible rigs. Some credit the work of Edward Robert Armstrong in the 1920s with the concept of an anchored, stable, floating deep-sea platform. His “seadrome” was designed and tested for the purpose of operating aircraft. But the first use of a semisubmersible rig was actually a four-column submersible rig built by Blue Water Drilling Company for Shell. By accident, it was discovered that at a certain draught, wave motion was very small, so Blue Water Drilling and Shell jointly decided to try operating the rig in the floating mode. The first purpose-built drilling semisubmersible, Ocean Driller, was launched in 1963. Since then, many semisubmersibles have been purpose-designed for the drilling industry mobile offshore fleet (Wikipedia. 2012).
Along with the capacity to drill in deep water came the necessity to complete and service these wells without the use of divers, who could not be deployed in such environments. Marine equipment that was used in other types of activities, like remotely operated underwater vehicles, are now a permanent feature of deep and ultradeep operations. These operations are now used to explore, develop, and produce from fields located in very deep waters in many regions of the world, especially in the Golden Triangle of deep prospects located along the Gulf of Mexico, Brazil, and west Africa. Giant fields that have been located in these areas are manifestations of innovation.
The other technology that I believe has made a significant impact on drilling operations is the mud motor. Ever since the introduction of rotary drilling, various new techniques have been researched and introduced to improve the reach of wells. Operators have sought ways to drill targets that are of considerable distance from the actual location of a drilling rig. While it was possible to deliver necessary horsepower to the bit in vertical holes, this capacity is very restricted when the target is thousands of feet away from the surface location. The use of mud motors also presents a number of improvements in drilling operations related to reduction in the failure of drillstrings, reduction on the wear and tear of pipe, and better hole stability. Their use has also permitted the targeting of small beds and chasing of reserves that would ordinarily be left behind.
Today’s drillers have access to many innovations that have allowed access to reserves of oil and gas in various geological settings. The future will demand that we contain the cost of well delivery in an effective and safe manner in increasingly complex geological and geographic settings. I am sure that there are many fertile minds within NOCs, IOCs, service companies, and research centers working on new techniques that will allow us to deliver. The world will need more energy and we in SPE must continue to contribute toward meeting the demand by promoting the technology behind drilling innovative wells.
References
- F. Sánchez, S. Houqani, M. Turki, and M. Cruz. 2012. Casing While Drilling (CwD): A New Approach to Drilling Fiqa Formation in the Sultanate of Oman—A Success Story. SPE Drilling & Completion 27 (2): 223-232. SPE- 136107-PA.
- Wikipedia. 2012. Semi-submersible (28 November 2012 revision), http://en.wikipedia.org/
wiki/Semi-submersible (accessed 28 November 2012).