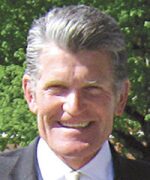
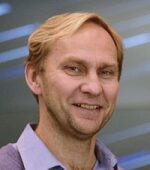
Questions posed by 2015 SPE President Helge Hove Haldorsen.
Answers provided by Rune Mode Ramberg, Chief Engineer Subsea Technology & Operations, Statoil.
Steve Thurston, Chevron’s vice president of deepwater exploration and projects compares developing US Gulf of Mexico oil fields like Jack and St. Malo in 7,000 ft to the 1969 moon landing: “Except we are going to the moon every day!” It really is impressive to see how offshore and subsea technology have evolved over the years. Of the world’s current oil demand of approximately 93 million BOPD, some 27 million BOPD or 30% comes from offshore fields and the offshore contribution is expected to continue to grow according to Douglas-Westwood World Drilling & Production Market Forecast 2005-2021.
The Norwegian Continental Shelf (NCS) is among the front-runners in subsea technology developments and applications. It is like a giant “subsea and offshore 2.0 laboratory” for the rest of the offshore world.
- According to Statoil, it has more than 500 subsea wells and is the world’s largest operator in water depths greater than 100 m.
- The Troll-Oseberg Gas Injection subsea template installed in 1991 supplies gas subsea from Troll to Oseberg, 48 km away, making a gravity drainage recovery mechanism on Oseberg possible, resulting in a very high oil recovery factor.
- Through more than 150 multibranched subsea wells (two to six branches per well), individual Troll oil province development wells can connect with nearly 45,000 ft of productive reservoir.
- Subsea water separation and subsea reinjection units have been successfully used on the Troll oil and Tordis field developments. At the Tyrihans 10% additional recovery is achieved with injection of raw seawater from pumps on the seafloor.
- Snøhvit and Ormen Lange are all-subsea offshore gas developments and send unprocessed wellstreams to shore 90 and 75 miles from shore, respectively.
Efficient subsea gas compression is the next challenge that the industry must face to continue subsea development. When an offshore gas field is developed 100% by a subsea development and the pressure falls because of production, compression will be needed at some point to maintain the production rate. But, there is no platform to put it on—unless you build one. What about installing subsea compression and skipping the platform altogether? Is this even possible? I posed questions to Statoil’s chief engineer in subsea technology, Rune Mode Ramberg, regarding the latest subsea compression developments on the NCS.
Why is subsea compression a good idea?
Subsea compression is one of the most important contributors to recovering additional oil and gas reserves, and provides future opportunities for improved recovery from a number of fields. Compression on the seabed also provides greater effect than a conventional topside compressor. The closer the compressor is to the well, the more effective it is, making extraction more energy-efficient. In addition, the platform avoids the extra weight and space required by a topside compression module, which makes it more cost-effective as we cut capital and operating costs. A compressor sited on the seabed can be operated remotely from a land-based facility, also cutting support costs. In addition, a study for Åsgard subsea compression shows that the carbon footprint of a subsea compressor is half that of a platform compressor because a subsea compressor is unmanned and improves personnel safety.
Why have so many subsea technologies come out of Norway and the NCS?
Statoil is not afraid to try new things if it makes good business sense. We have a long-term perspective when we put efforts and resources into breaking technology barriers. Testing and qualifying new solutions are vital to the success of our technological developments. In Norway, we have a long and strong tradition for qualifying new technology at near field conditions before a new project is making its final concept selection decision. A purpose-built test facility for subsea gas compressor technology at Statoil’s large test center, K-lab, has been instrumental in order to qualify the new subsea compression technology.
Tell us how we got to where we are today?
Statoil’s subsea story began when we first put a subsea well in production on Gullfaks, 22 December 1986. Since then, we have developed subsea technology systematically and have taken courageous technology steps in good collaboration with our partners and the supplier industry. Collaboration is key as we are better together. Subsea technology has made all our field developments in greater than 200-m water depth possible, among these: Åsgard, Norne, Snøhvit, Tyrihans, Kristin, Troll oil province, and Aasta Hansteen starting up in 2017. Future resources are farther from shore, in deeper and colder waters. Innovative subsea technology is key to developing these resources commercially. The idea of subsea compression began 30 years ago—now it is soon to be realized.
On which fields will it be installed and what is the value creation potential?
Statoil is currently developing two subsea compression projects together with its partners: subsea dry gas compression on Åsgard and subsea wet gas compression on Gullfaks, both vital technology innovations to increase oil recovery.
At the 15-year-old Åsgard field on the NCS, we installed two 11.5-MW compressors expected to extend the life of the field by up to 20 years, increasing the recovery rates by about a third, and adding approximately 282 million BOE in reserves. That is the size of a new medium-sized field. This spring, we are installing the compressor trains consisting of 22 modules on the seabed at approximately 300-m water depth.
We are also working on a smaller pair of compressors (5 MW each) to be installed at the same time in a field close to the giant Gullfaks field, increasing recovery from the Gullfaks South Brent reservoir by 22 million BOE. The recovery rate can be increased from 62% to 74% on Gullfaks C using this solution combined with conventional low-pressure production in a later phase. This is very good for a subsea field. Realizing subsea compression is an important milestone to reach in our ambitious technology development strategy. With it, we will be able to realize the subsea factory.
What were the key technical and other challenges to solve?
It is important to understand that the project is not only a subsea compressor project, although the compressor is “the heart” in the system. A comprehensive technology qualification program has been carried throughout the whole period from 2007 to 2014. Testing and completion of the subsea modules took place during the last 2 years. Pipeline, pipeline end manifold, and spool installation were carried out during the 2013 season. Subsea structures and topside power module heavy lift installations were completed in 2013. Umbilical and module installation were started in 2014 and will be completed later this year. We also had to build a new onshore base for storage and maintenance. To be able to install the modules on Åsgard, we have upgraded one of the existing offshore construction vessels, Technip’s North Sea Giant, with a new module handling system.
Are there still residual risks?
The actual compressor for the first compressor train on Åsgard is currently being tested as it has been submerged in a big pool at Statoil’s test center at Kårstø, providing operating conditions that are similar to those awaiting the compressor at the Åsgard seabed. The requirements for equipment to be placed in 300 m of water, inaccessible to most, are strict.
The compressor train modules have been tested prior to installation to ensure that they are compatible and intercommunicate properly. We are also using very strict checklists and control procedures for this project. For the Gullfaks subsea wet gas compression, testing has progressed through the final system integration tests. The results have been very positive.
Will we see subsea compression spread globally in a hurry, like a subsea revolution?
Natural pressure in large gas fields will become too low over time to maintain a stable flow and a high production profile. To compensate for this decline, the operator needs to invest in a precompression system either on an existing platform, a new platform, or a subsea compression factory. For the Åsgard field, Statoil decided to install seabed compressors near the wellheads to increase the pressure. At the moment, we are working on several other business cases for subsea gas compression. It will take some time before we will see subsea compression spreading globally. But the combination of large gas fields and long tiebacks of subsea wells will create additional demands for subsea gas compression. So we should not be surprised if the next wave of subsea gas compression is in Australia or East Africa.
What is the next subsea frontier and are there still many “terra incognitas” in subsea in your view?
At the moment, we are very concerned with the large cost increase the oil industry is facing. Statoil is promoting subsea industrialization and standardization for more cost-efficient field development through establishing visions and the steps to reach these through sharing technical specifications and participating in joint industry projects. This will create opportunities if we are able to cooperate with the vendor industry to develop cost-efficient subsea solutions giving us high recovery rates. At the moment, development of large gas fields in deep water down to 3,000 m is a new subsea frontier. In a longer time frame, developing subsea facilities in the Arctic may well be the next frontier.
Explain this vision of a subsea factory?
A subsea factory is a process plant on the seabed making it possible to utilize remote-controlled transport of hydrocarbons at any offshore facility. Statoil has gradually matured and developed the idea of a subsea factory as the resources are farther from shore, in deeper waters, and in harsher areas. We believe compact separation facilities on the seabed will be a key to success in Arctic areas or deepwater areas like the Gulf of Mexico (US and Mexico) and Brazil. We have already taken the first technological steps. We have made the world’s first complete subsea solution for separation and injection of water and sand from the Tordis wellstream, and developed the first subsea facility for injection of raw seawater on Tyrihans. Projects such as the oil-dominated multiphase transport on Tyrihans and Snøhvit’s gas condensate transport are at the forefront in the development of multiphase transport over long distances. The next step is to realize subsea gas compression later this year.
With subsea compression, we now have all the main elements. We can extract the oil and gas; we can separate oil, gas and water on the seafloor; inject the water back; and boost the oil and gas to a nearby facility.
Why has Statoil focused so much on subsea technologies?
The future of the oil and gas industry is out at sea. It is farther from land, at greater depths, and in colder, harsher environments. The subsea factory will be vital to realize business opportunities for Statoil in these areas. We have been in the forefront of subsea technology for 25 years. We have the experience and the courage to take more brave steps subsea.
Conclusion
So there you have it. Another world’s subsea first has seen the light of day on the NCS. And there is no reason why the subsea story should end there. What does it take? Head, heart, guts, and collaboration! Think about it!