Wherever you are working in the world, the low oil-price environment has likely affected costly megaprojects in your sector. As the industry continues to cut back on spending and capital investments, is it worth getting into or staying involved with a high-risk, long-term project? A fellow young professional, Sophia Holtsnider, facilities engineer for Encana Oil & Gas, and SPE technical director for the Completions discipline and assistant department head and associate professor in the Petroleum Engineering Department at the Colorado School of Mines, Jennifer Miskimins, share their views on the landscape for oil and gas megaprojects.
-Angela Dang, Colter Morgan, and Chieke Offurum, TWA Tech Leaders Section Editors
What is the largest project, loosely defined as most expensive, most production, etc., on which you have worked?
SH: I participated in the design of the sixth terminal and third runway at Heathrow Airport (>GBP 15 billion) as well as the Tailings Expansion Project for Kennecott Utah Copper (USD 2 billion). Both projects took 10+ years to design, were suspended while I worked on them, and have since been restarted. The Heathrow expansion was suspended due to national politics and the Kennecott expansion was suspended due to low copper prices.
JM: My experience in large or megaprojects has been in a different aspect than some others’ might be. The largest projects that I have worked on have been multiwell horizontal shale projects—specifically in the Bakken, Eagle Ford, and Permian Basin areas. Although these are not traditional megaprojects, they do fit the definition in regards to total volume of production, preparation time, and money spent.
What were the turning points or major decisions you made in your career that led you to these projects? Were there specific skill sets from your earlier positions that helped you when working on a megaproject?
SH: The overarching theme of my career has been “Be flexible and follow the capital.” The shale industry barely existed when I graduated so I did not consider a career in oil and gas. As a civil engineer, I chose a job designing municipal infrastructure for an engineering consultancy. That pump and pipeline design experience led to a company transfer to England to work on airport water systems. When I returned to the US, the mining industry was hiring and my new, large-scale systems experience was a good fit for that work. When copper prices fell, I moved to the oil and gas industry, where my experience with complex industrial systems was in demand.
JM: In hindsight, there were numerous turning points and skill development that led me to these projects. And yes, there were definitely skill sets from earlier projects in my career that helped with the success of these later projects. Technical skills were important, and I was able to develop those on smaller, less risky projects earlier in my career. At the same time, management and people skills were equally important to develop. As projects grow in size, so do the teams that work and manage them. Developing communication (both written and oral) skills was absolutely critical and having mentors or knowing the right person to call was equally so. I also learned that my mentors were not always going to come to me—I needed to seek them out and their advice.
Wikipedia defines an “oil megaproject” as a project that brings more than 20,000 B/D (3200 m
3
/d) of new liquid fuel capacity to the market. What did megaprojects look like in the past and how do they look today?
SH: In my opinion, a 20,000-B/D oil facility is not “mega” because it can be designed and built in less than a year. To me, a megaproject requires a major capital commitment over 5+ years. The frequency of these projects is increasing as the full extent of the hydrocarbon resources in Canada and the US are better understood.JM: I do not think the volume components are going to change that much. However, I do think the costs will continue to increase as the megaproject areas become more challenging to development. Future deepwater projects will occur in more difficult areas and will possibly include additional environmental challenges and development of unconventional resources outside the North American continent will need large influxes of capital to move forward. Each type of system brings different complexities with it.
What are the biggest challenges facing oil and gas megaprojects in the future?
SH: Increasingly detailed regulatory reviews have extended the time required to execute a project. Even upstream projects that are below federal approval thresholds can take 2–5 years. Consolidated, downstream projects such as refineries take far longer (15–20 years). There is also limited political will to support large projects due to either real, or perceived, environmental impacts.
JM: Obviously right now the biggest challenge facing most projects is the oil price situation and the instability that goes along with it. Most megaprojects at this time likely have very borderline economics associated with them. That being said, megaprojects can take several years to come on line, and if the timing is right, will be poised to take advantage of prices when they start coming back up. There were several large projects that started in the late 1980s that many people were shocked at but they laid the foundation for large returns in the 1990s.
As crude prices continue to stay low, what strategies do you see changing in the execution and planning of megaprojects?
SH: Planning of megaprojects is perpetual. Constant re-evaluation is critical even in a low price environment in order to determine the cost of re-entry into a field. Some projects are all-or-nothing in terms of execution; if they are under construction during a downturn they will likely be finished because the cost of walking away is too high. For new projects, however, the focus is on maximizing capacity in existing facilities by taking advantage of natural production declines and building smaller, modular facilities that can be adjusted as forecasts change.
JM: Megaprojects require long-term planning. Although the direction of our industry has always been hard to predict, it has become even more so in the current situation. Commitment to mega-projects will be harder to come by in the near future, and it will take some risk to move forward. But, of course, with high risk comes high reward in certain situations. Companies and teams that plan with that risk in mind and have bailout plans at certain points could stand to benefit greatly in 10 or 20 years’ time.
Regarding megaprojects being canceled due to current low oil prices,
a June 2015 article published by Reuters
said, “The delays in multibillion dollar projects that can take up to 10 years to develop…could create a shortage in the future.” Could you explain this statement for our readers? Do you agree?
SH: Yes. Low commodity prices do delay projects, which then reduces how much new product can be brought into the market when prices go up. Ironically, that tightening of supply (combined with a presumed increase in demand) is what produces the higher prices that cause operators to restart their dormant megaprojects. This cycle is fundamental to all market-based commodities. The only way to mitigate the effect is to provide continuity of funding for major projects during low-price periods. This is unlikely within the shareholder-driven culture that exists today because prudent companies do not want to take on debt or reduce profit to build for an uncertain tomorrow.JM: I definitely agree with this statement. Every year that capital spending on megaprojects is halted or slowed is a year’s delay in the potential production from that project. In 5 or 10 years, current production will have decreased to the point that it can no longer keep up with supply. If multiple projects around the world become delayed, they will not be on line and ready to make up for this demand. It will take additional time for them to become ready for startup and come on line. This situation can leave a large gap in the supply/demand profile for hydrocarbon production.
It is not often that social responsibility takes center stage in a science or engineering education curriculum. In a world where safety and the environment are our most important considerations, how do young professionals (YPs) (and seasoned professionals alike) become well-versed in these topics?
SH: YPs in the oil and gas industry are lucky to work in an age where safety is the number one priority of all operators. As engineers it is our responsibility to minimize risk to life and the environment through good design. The best way to learn good design is through work experience and spending time in the field with operators. No class or guidance document can substitute for seeing firsthand how people actually work.
JM: As in many educational situations, I believe it becomes the responsibility of the individual to take the initiative and keep up with associated safety and environmental topics (just as it is for technical topics). Companies and employers need to support these endeavors through training and educational opportunities, of course, but we all need to take the responsibility to learn what might impact our daily operations, whether it is a megaproject or something smaller. Any incident, small or large, can impact our entire industry, and a focus and culture on how to prevent such incidents and provide proper maintenance is critical. This culture is developed by a company, but also by the people in that company. Additionally, we are all the face of our industry and need to be able to communicate with the public and demonstrate the safety and environmental protocols that are in place.
As the risk of taking on large projects grows for companies, should YPs be wary of joining teams working on them? What is your advice for YPs who want to join megaprojects?
SH: Absolutely not. There is always something to learn in a megaproject, regardless of whether the project is completed. In my opinion, megaprojects do not need to be sought out. My advice is to find a company that works on interesting projects and then learn everything you can at each level as you progress.
JM: No, absolutely not. Risk is present in almost everything we do, so I do not believe that there is a way to avoid it. And, even if one could, I do not believe they should. It might sound clichéd, but taking risks can lead to great rewards. Megaprojects might have some challenges at this particular point in time, but that is really nothing new—challenges always exist. Addressing them head-on and taking initiative in any type of project will always have benefits.
Our education never really ends. I have three degrees in petroleum engineering, and I still learn something new each and every day. Do not expect to know everything; do not expect to be expected to know everything. Seek out advice, seek out mentors, do your homework, and learn from past successes and failures in your company and outside of it. Taking the initiative for your own career is critical—whether you are working on a megaproject or not.
This interview is directed toward large facility projects, but in the exploration and production industry the development of any oil or natural gas field is equivalent to a megaproject. Do not be afraid to look past the official definition. As an engineer, “mega opportunities” are everywhere.

Sophia Holtsnider is a facilities engineer for Encana Oil & Gas. She has 14 years of experience in strategic infrastructure planning and execution for industrial, municipal, and surface water projects. Holtsnider holds a BS in civil engineering from the Colorado School of Mines and a MS in civil engineering from the University of Colorado at Denver.
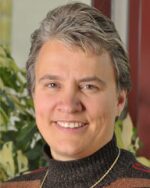
Jennifer L. Miskimins is the assistant department head and an associate professor in the Petroleum Engineering Department at the Colorado School of Mines, where she teaches classes in completions, stimulation, and multidisciplinary integration. She is also the codirector of the FAST Consortium and conducts research in the areas of stimulation and hydraulic fracturing.
Miskimins serves as the SPE technical director for the Completions discipline. She was an SPE Distinguished Lecturer on hydraulic fracturing in unconventional reservoirs during 2010–2011 and 2013–2014, and served as the executive editor for SPE Production & Operations from 2008 to 2011. Miskimins holds a BS from Montana College of Mineral Science and Technology and MS and PhD degrees from the Colorado School of Mines, all in petroleum engineering.