Oilfield disasters shine a light on industry shortcomings. Below are three of the infamous events in industry history and the changes to equipment, procedures, and culture that have since been made to prevent their recurrence.
Name: The Lakeview Gusher
Date: March 1910–September 1911
Location: Kern County, California
What happened: In 1909, Julius Fried, a grocer, purchased land in Kern County, California, and founded the Lakeview Oil Company. In March 1910, after months of unsuccessful drilling that forced the sale of a controlling stake to Union Oil, oil struck at 2,200 ft. While running a bailer, the workers heard and felt a rumbling from under the well. They ran for it. What followed was the world’s largest oil spill on land. As the well blew out, the geyser was reported to have reached up to 200 ft in the air and was so forceful it not only demolished the wooden derrick sitting above it, but it also turned the top of the wellbore into a crater. The well flowed uncontrolled for 17 months, releasing an estimated 9 million barrels of crude to the surface. In September 1911, a subsurface collapse of the wellbore obstructed further flow. During the well’s blowout, workers scrambled to build berms to contain and direct the flow of oil in order to collect as much of the bounty as possible. Despite their efforts, it is estimated that only half of the 9 million barrels was recovered. At the time, the oil price was $0.61/bbl, which means that the Lakeview Gusher earned only $2.745 million. Adjusting for inflation, at approximately $16/bbl today, it would have brought in a modest $72 million.
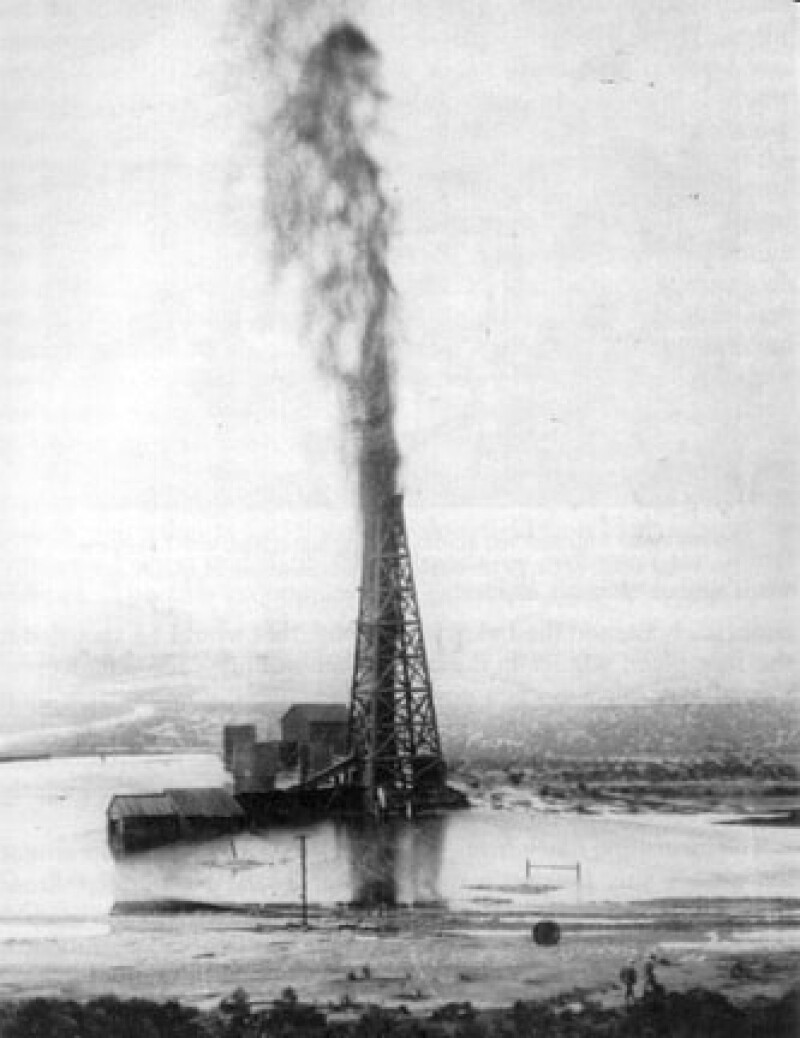
What changed: Large and well publicized industry disasters usually lead to a change in best practices. However, in its time, the Lakeview Gusher was not considered a disaster at all. In fact, it was considered a good omen as it suggested an abundance of oil in the area, and even became something of a tourist attraction for its duration. Despite the era’s nonchalance about the worst oil spill in history, innovation did eventually find its way to the drilling process. In particular, the world’s first ram-type blowout preventer (BOP) was described in a patent application in 1922 and on the market in 1924 thanks to a collaboration between James S. Abercrombie and Harry S. Cameron (of Cameron Wellhead Systems).
This BOP and the many subsequent iterations and improvements to it over the past century can be credited with improving both the safety and environmental records of the exploration and production process. The types of disasters that make headlines when BOPs fail (such as the Deepwater Horizon oil spill) are a further testament to just how much the invention of the BOP improved the industry.
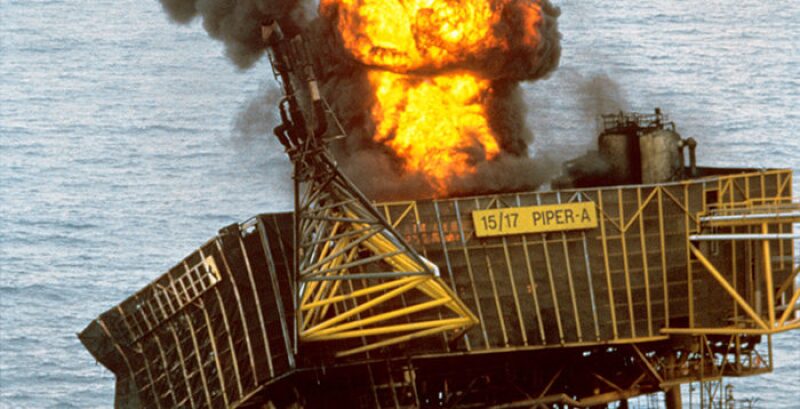
Name: Piper Alpha
Date: 6–7 July 1988
Location: The North Sea, approximately 120 miles northeast of Aberdeen, Scotland
What happened: The offshore platform, Piper Alpha, situated in the Piper oil field, was built in 1975. This platform was owned by a consortium of international companies and operated by Occidental Petroleum. In its time, Piper Alpha was the most prolific platform in the North Sea, responsible for 10% of oil and gas produced by UK, about 300,000 BOPD.
On 6 July 1988 there were 226 crew members onboard the platform. At 2145, Geoff Bollands, the chief control room operator heard an alarm, indicating a problem with one of the platform’s two condensate pumps. To maintain power for ongoing construction work, the second condensate pump was restarted. This pump had been taken off line for maintenance earlier in the day and maintenance had not been completed. At the time it was restarted, the second pump was still missing a safety valve, the absence of which permitted a high-pressure gas leak.
At approximately 2155, gas leaking from the second condensate pump ignited, causing an explosion. Damage caused by this explosion catalyzed three further explosions caused by ruptures in the pipelines connecting Piper Alpha to surrounding platforms. The resulting fires exceeded 700°C and decimated the 14,000-ton platform. The intensity of the flames prevented onboard crew from accessing evacuation routes and lifeboats and prevented rescue vehicles from approaching. By 2350 the platform began to collapse. The fires took more than 3 weeks to extinguish.
A total of 167 people, 165 platform personnel, and 2 rescuers lost their lives, most due to smoke inhalation. Only 61crew members survived. In addition to this tragic loss of life—the worst in offshore history—financial losses totaled an estimated £2 billion (the equivalent of $5 billion today).
What changed: Offshore operators acted on factors that were perceived to have caused or contributed to the severity of the tragedy. These included improving permit-to-work systems—which if properly implemented would have informed the night crew that the second condensate pump was off line; relocating pipeline emergency shutdown valves and installing subsea pipeline isolation systems—either of which may have prevented neighboring platforms from continuing to pump fuel to the Piper Alpha after the initial explosion; and mitigation of smoke hazards and improvements to evacuation routes—both of which might have allowed more crew members to escape from the platform after the explosion.
In addition to these changes, Scottish judge William Cullen reviewed the incident and summarized his findings in the two-volume, 400-page Cullen Report filed in 1990. TheCullen Report included 106 safety recommendations, of which 37 pertained to equipment operation, 32 to communicating information to platform personnel, 25 to platform design, and 12 to communcating with emergency services.
Perhaps the most significant of Lord Cullen’s recommendations was codified in the Offshore Safety Act 1992 and the Offshore Installations (Safety Case) Regulations 1992, requiring operators to provide a safety case for each offshore installation, detailing how a platform could be run safely, providing for the management of personnel health and safety, and providing for the handling of major accidents on the installation. These were revised in 2005 to improve effectiveness and remain in force today.
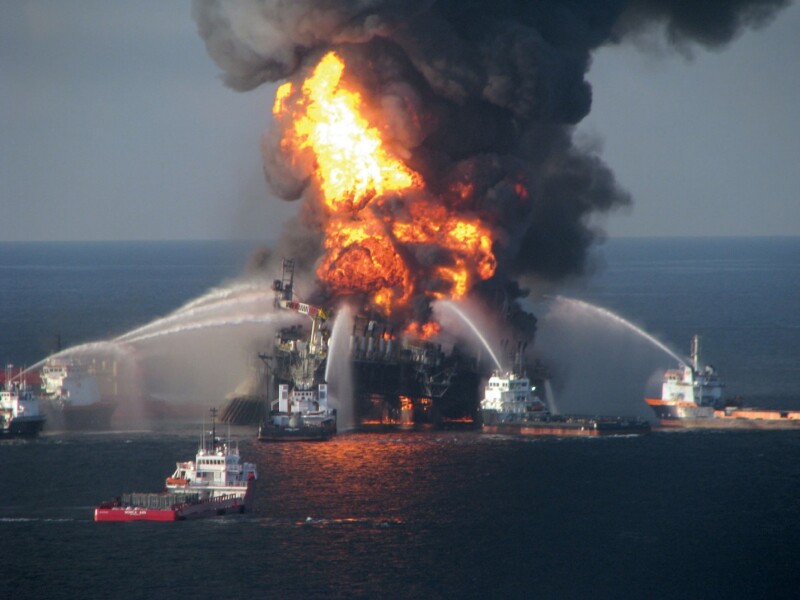
Name: Deepwater Horizon/Macondo
Date: 20 April
Location: Gulf of Mexico
What happened: A horrific scene erupted the night of 20 April 2010 when a deadly blowout occurred during the temporary abandonment of BP’s Macondo exploratory prospect, which was being drilled by Transocean’s Deepwater Horizon. Approximately 50 miles off the Louisiana coast, the well was situated 18,000 ft below mean sea level and involved operations at depths of up to 5,000 ft. Incident investigation reports highlight an combination of causes facilitating the disaster. However, the main culprit was a bad cement job, which failed to prevent gas from escaping through the marine riser up to the rig floor where it subsequently ignited and exploded. Multiple opportunities to identify and contain the leak were missed due to a combination of human error and equipment failure: a pressure test showing the leak was misinterpreted; the leak was diverted to a mud/gas separator that could not handle the volume; the gas alarm failed to shut ventilation to ignition sources; and multiple BOPs failed to close.
The well could not be closed, and the oil continued to spew to the surface and the flames engulfed the rig platform. Witnesses described the scene as huge fireballs visible from miles away. At the time of the incident, theDeepwater Horizon was inhabited by 126 crew members. Eleven of the 126 were never found and were presumed dead. Seventeen rig workers sustained critical injuries during the evacuation procedures. Thirty-six hours after the incident, the Deepwater Horizon sank while oil continued to flow from the well. It took almost 90 days to seal the well, during which time an estimated 4 million barrels leaked into the Gulf of Mexico. Cleanup took substantially longer, with oil-coated debris arriving on the Gulf shore up to 3 years after the incident.
What changed: The events surrounding the Deepwater Horizon disaster highlighted the role of the exploration and production industry in environmental responsibility and the need for robust well integrity management systems (WIMS) to prevent future incidents. The response has been dynamic, growing over the past 11 years with multiple initiatives taken to enhance the technical and managerial aspects of WIMS.
Before this event, regulations were formed using a prescriptive approach that utilized a lessons-learned methodology. However, this process is dependent on the occurrence of events/incidents which can have far-reaching consequences, as was demonstrated by the Deepwater Horizon incident. An incident would be followed by calls for action and intentions to prescribe safe practices. This pattern was observed following the Montara oil spill just 8 months prior to the Macondo event.
Following the Deepwater Horizon incident, a more proactive approach was adopted. Concrete steps have been taken and significant resources invested to prevent another catastrophe rather than simply addressing the causes of the Deepwater Horizon.
A review and reform was conducted for existing standards surrounding possible culprits such as cementing practices, cement bond log practices, and pressure-test analysis. The response to this incident was not limited to the immediate parties, rather it propelled joint industry collaborations focusing on improvement of procedures. This also led to improvement/review of various well integrity standards including those from American Petroleum Institute; NORSOK, the Norwegian standards agency; and International Association of Drilling Contractors.
Further, the Minerals Management Service, responsible for overseeing drilling, was dissolved, and replaced with three new agencies that divided oversight so that a focus on regulation and safety was not clouded by leasing and revenue collection.
Finally, even after capping the well, research continued into controlling the subsea release of oil, including focus on well containment at the seafloor, intervention, and containment within the subsea well, subsea collection and surface processing and storage, and relief wells.. This component—ongoing research—indicates the desire not just to learn from the most recent disaster, but to be prepared for potential iterations should such a misfortune occur.
Conclusion
While equipment failure often plays a role in oilfield disasters, it is often augmented by human error. While the industry has become significantly safer and infinitely more environmentally conscious than at its inception—in part because of lessons learned from the disasters in its history—it still has the potential to be both disastrous and deadly when not approached with the caution and respect it is due.