The Federal Energy Regulatory Commission is responsible for overseeing US oil and gas activities, and the reduction of fugitive emissions is fast becoming one of its main focuses. The release of natural gas into the atmosphere can prove damaging to the health of personnel and the wider public—as well as the environment—and undetected leaks can lead to millions of dollars’ worth of unrealized revenue in large operations.
However, detecting these emissions is no easy task, especially considering the thousands of miles of pipeline based in remote regions of the country, prompting the industry to seek out novel technologies that can bolster leak detection and repair (LDAR) strategies. This article takes a deep dive into the challenges of LDAR, as well as delving into some of the solutions that can help companies increase efficiencies, minimize waste, and ensure environmentally friendly operations.
Fugitive Emissions
Natural gas and petroleum systems were responsible for 29% of all US methane emissions in 2021, prompting the Environmental Protection Agency to publish strict national standards designed to curb the release of this greenhouse gas into the atmosphere.
A large proportion of methane emissions arises from fugitive emissions caused by everything from pipe corrosion and earthquakes to unintentional pipe excavation and equipment failure. Even relatively small leaks can add up to vast amounts of gas over time, making it essential to be able to detect and fix these hotspots as quickly as possible.
Unfortunately, the identification of small leaks can prove challenging, since the corresponding pressure changes are far too small to register on the widely spaced gauges that have been specifically calibrated to monitor routine variations within the pipelines.
One solution to is to rely on aerial leak detection—using thermal imaging helicopters or drones—which allows vast lengths of remote pipeline to be monitored for methane clouds that indicate areas of damage. Advances in space-based imaging technology have also made satellite leak detection feasible, providing operations with continuous real-time monitoring of high-priority areas. Once the rough position of a leak has been identified, specially trained sniffer dogs can then be sent to pinpoint its exact location, allowing necessary repairs to be carried out. However, the use of animals makes it challenging to comply with strict industrial standards, and handheld laser methane detectors are increasingly being used in their place.
Several modern techniques can help to reduce the manual nature of this activity, including acoustic leak detection solutions that employ externally mounted sensors to identify the sound of gas flowing through cracks or holes. With systems like this in place, the pipeline can be continuously monitored, allowing leaks to be detected as soon as they occur instead of relying on sporadic manual searches.
Larger leaks are often easier to diagnose due to the considerable pressure changes involved. These can be detected by in-line gauges that signal for the gas flow to any damaged lengths of the pipeline to be shut off. However, these sections must then be removed and replaced to fix the leak, and it is common practice to purge the contents of the pipe for safety reasons, venting large amounts of methane into the atmosphere.
To avoid this, it is increasingly common to insert a “pig”—a cylindrical or spherical device with an outer diameter that forms a seal against the inner diameter of the pipe—upstream of the affected section. Inert gas is then pumped into the pipeline behind it, propelling the pig forward and forcing the downstream gas beyond a shutoff valve. The damaged length of the pipeline can then be removed and replaced, leaving only inert gas to be purged into the atmosphere.
Other Sources
Pipeline damage is not the only source of fugitive emissions; the seals of the centrifugal compressors used to maintain constant pipeline pressure are also known to release small amounts of methane into the atmosphere.
These seemingly insignificant leaks can quickly add up, especially with the industry continuously operating an estimated 25,000 compressors. Techniques such as recompression—which captures the leakage across the seals and injects it back into the gas stream—can be employed to prevent this.
While this solves the fugitive emissions issue, compressors—like most combustion engines—also emit exhaust fumes containing greenhouse gases. These so-called “combustion emissions” are similarly produced by generators, gas-fueled equipment, and flares. Fortunately, flare gas recovery systems are now available that can capture this waste gas to be used as fuel for a variety of other applications.
Hard to Gauge
A further source of fugitive emissions is the swathe of valves stationed along the vast lengths of pipeline in the US. Since it is almost impossible to supply electricity to the most remote areas to operate these valves, most conventional pipelines employ passive gas-actuated valves, using the pressure of the pipeline contents to open and close. The gas used for actuation is then vented into the atmosphere, which adds up to significant levels across the countless valves fitted to a typical pipeline.
One zero-emission alternative is to employ units that similarly rely on pipeline pressure to operate, but cleverly employ small electric motors that propel the natural gas back into the supply line rather than venting it into the atmosphere. These motors can typically be run on solar power to avoid the need for mains electricity.
Prevention Is Cheaper Than the Cure
Detecting emissions is paramount to an effective LDAR strategy, but employing methods to identify issues even before leaks can occur should become the ultimate goal for any operation. Devices known as “smart pigs” can be used for this very purpose, allowing areas of pipeline to be inspected via magnetic flux leakage testing.
As the pig traverses the pipe, it magnetizes the pipeline wall and observes the shape and strength of the corresponding magnetic flux lines. Any changes to wall integrity—such as corrosion or pitting—will cause these flux lines to deviate from those of an undamaged length, flagging areas of concern. If these issues are highlighted early enough, a protective composite sleeve can be wrapped around the exterior of the pipe to reinforce it rather than having to remove and replace large sections.
Transitioning from reactive to proactive maintenance has the potential to create a step change in pipeline safety and reliability. The use of advanced computing methods—such as machine learning and artificial intelligence—to continuously analyze real-time data streams from a whole host of sensors is allowing the development of powerful predictive tools that can minimize manual process input and eliminate the chance of human error via rule-based strategies.
These tools are developed by analyzing historic data to determine failure indicators—like predefined temperature or pressure limits—that, if breached, will result in automatic adjustment or shutdown of the pipeline to mitigate the risk of damage. Similarly, with past data to compare against, it is often possible to predict equipment malfunction before it happens, prompting preventive maintenance.
Conclusion
Environmental guidelines are likely to become increasingly stringent if recent trends are anything to go by, and it is essential for the oil and gas industry to invest in new technologies to minimize emissions whatever the source. State-of-the-art aerial monitoring and satellite imaging solutions can offer prompt detection of remote methane leaks, allowing repairs to take place before any serious environmental damage can take place. Closing the loop between real-time monitoring and process control could be the key to revolutionizing LDAR, allowing potential issues to be predicted and remedied before leaks can even occur, safeguarding the environment, decreasing waste, and boosting profits. Of course, the upgrades required to make this a reality won’t be cheap, but falling foul of industrial regulations could end up being a much costlier alternative.
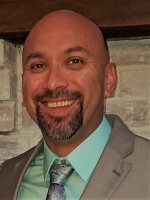
Benjamin Fuentes joined Thermo Fisher Scientific as regional sales manager for the flow computer product line in July 2008. Fuentes has over 20 years of experience in hydrocarbon measurement, sales leadership, and product management. Within Thermo Fisher Scientific, he has held roles within the commercial team and marketing teams leading to the implementation of keys sales strategies and development of innovative products for the hydrocarbon measurement. Over his career, he’s worked for various technical companies such as Cameron Measurement systems, NuFlo Technologies, and Superior Optimization. Fuentes has a BS in business administration from University of Texas of Permian Basin.
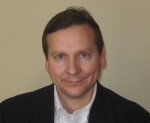
Bob Gallagher joined Thermo Fisher Scientific as the product line manager for the Industrial Hygiene Strategy at the end of 2017. Gallagher has over 35 years of experience in engineering and product management roles in the area of LDAR, site remediation, dust monitoring and other various industrial applications. Over his career, he’s worked for various technical companies such as Texas Instruments and Pentair and has successfully launched several innovative global products. He has a BS in materials science and engineering from Penn State University and an MBA from Boston University.