If all technological innovations produced by the oil and gas industry were added up, they would probably rival NASA’s space program or the Industrial Revolution. Driving these innovations have been the increasing challenges of locating, accessing, and exploiting hydrocarbon reserves. As oil and gas gets harder to find and extract, the costs of extraction escalate, and this drives innovation that makes the process more efficient and cost-effective. Before we speculate on the technological future of the oil field, let us look at some fundamental questions, such as what drives innovation, what does it cost, who pays for it, and who performs it?
What Drives Innovation?
In general, innovation relates to the application of new ideas, products, or techniques. In oil fields, it pertains to anything that extends our ability to access resources that are harder to reach, or to do so more efficiently, effectively, cleanly, and safely. We would not be talking about technology and innovation if we could take a bucket to a bubbling stream or a pond of crude and gather at will. Recent oil and gas finds and major developments have been a result of pushing the limits of existing technologies. The oil and gas industry has responded with innovative solutions to meet its business needs, bringing together exploration and production (E&P) operators, service companies, and academia (Table 1).
The following are some key drivers for technology innovation:
Access to resources. Many recent technology innovations have been instrumental in enabling access to resources in deeper waters, or developing unusual reservoirs such as high–pressure, high-temperature, underpressured, depleted, or unconventional (shale and tight sand) reservoirs, as well as oil sands and heavy oil.
Operational improvement. The ability to do the same thing better, cheaper, or quicker, or doing it safer or “greener,” is also a common motivation for several technology innovations recently introduced in the oil field. Another example is field life extension. Several fields, onshore and offshore, were originally planned for a 20- to 25-year project life, but being able to continue operations beyond that initial field life has also provided an opportunity for new ideas on how to make it happen safely and reliably.
Competitive advantage. Technology leadership brings the advantage of being perceived as a preferred partner or employer. Skilled resources are often attracted to technologically progressive companies. National oil companies (NOCs) sometimes have specific technological needs they cannot meet in-house. In those situations, an international oil company (IOC) that brings a technological edge to the table has the opportunity to be a partner in the exploitation of those resources. A service company with a technological edge may also stand a better chance at winning business from operators.
Strategic investment. A portion of technology innovation is a result of investment in new technologies and techniques in anticipation of their ultimately being required to serve the continuously evolving business needs of the industry. Examples include investments in information technology (IT), nanotechnology, biotechnology, and alternative, cleaner energy sources. Anticipating those needs and investing in a diverse research and development (R&D) program to develop corresponding solutions requires forethought and commitment to long-term, continuous improvement.
Incubation Sites and Funding Sources
Directly or indirectly, much of the cost of innovation is borne by E&P firms. However, in many cases suppliers and service providers are performing significant R&D. Nonetheless, it is reasonable to expect that these expenditures are eventually passed along to the operators in the form of cost premiums for the goods or services rendered. Some common models for R&D incubation, including typical location and funding sources, are shown in Table 1.
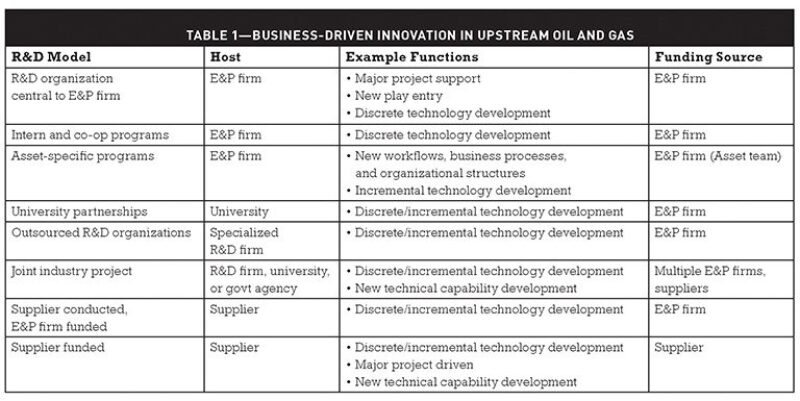
What Impedes New Technology?
In any discussion of factors that drive innovation, it is important to acknowledge the barriers to innovation. Managing those barriers is critical to safeguard innovation. The cyclical nature of the oil field is a fact of life, but cycles in R&D spending can interfere with the need to bring innovations to maturity. Every time the pendulum of oilfield finance swings back, budgets are tightened, and it is not uncommon for R&D spending to get axed by virtue of being “nonessential” to daily operations. In some cases, the operational nature of the oil field causes a tactical day-to-day focus such that long-term vision is relegated to the back burner. In recent years, many E&P companies have shut down their own R&D efforts to focus on core operations, leaving their service providers to invest in technology and provide leadership in that sphere.
The following are some additional factors that impede technology innovation in the oil field:
Cultural barriers and communication. In an industry that is more than 150 years old, it is not surprising still to encounter old-school affinity for the status quo and resistance to change. Longstanding business practices and relationships between stakeholders such as IOCs, NOCs, and other government entities sometimes make change difficult, thus hindering the introduction of innovations. Some argue that at times, a change of ownership can even be helpful to stimulate new ideas and projects—for example, to produce more barrels at the end of a field’s life.
Budgetary cycles. Annual budgetary processes and shareholder review cycles make it difficult to incubate long-term R&D initiatives whose development may often span many years before any tangible results are expected.
Partnership arrangements. When operating with partners, such as in an upstream joint venture, there are potential complications with ownership of intellectual property (and possibly licensing, if a new technology were developed). That difficulty sometimes makes it easier to avoid innovation rather than invite a new set of complications.
Recent Examples and Trends
A brief review of some recent technology innovations in the oil field—whether as a new creation or adaptation of existing technologies—can give an idea of the sorts of business challenges that arise.
Offshore development. The industry’s move into deeper waters and more hostile environments has for years stimulated upstream technology innovations. The development of floating drilling vessels spurred the introduction of many new technical elements, such as drilling risers and flex joints, dynamic geostationary positioning, subsea and subsurface safety valves, and mechanisms to safely and rapidly disconnect the floating vessel from the well in an emergency.
Digital technologies. These have enabled new modes of operation. Supervision of drilling and production operations in remote areas is particularly complex, and access to experts has been difficult in the past because of location and communication constraints. However, high-speed data links to operating bases, combined with data sharing and video-enabled telepresence, have enabled the operating base to become a virtual extension of the control room at the field—enhanced by ready access to remote experts around the world. Another interesting innovation, made possible as a result of numerically intensive computing power and robust data communication, is time-lapse seismic, which enables geoscientists to visualize reservoir drainage over time and better manage reservoir development.
Heavy oil. Deposits such as the Athabasca oil sands consist largely of bitumen. Although very large on a resource scale, these deposits were long considered uneconomic for development, extraction, and processing. In recent years, many innovations have improved the economic viability of those deposits—albeit with some assistance from strong crude prices. Originally, extraction primarily relied on surface mining combined with hot water extraction processes. More recent approaches enable crude recovery by means of in-situ processes, such as steam-assisted gravity drainage (SAGD) or cyclic steam stimulation (CSS). Other evolving pieces of the heavy crude process chain have been the bitumen upgraders and the fluid catalytic crackers at various refineries.
Unconventional resources. Shale gas development, in particular, has taken off in recent years. The presence of hydrocarbons in tight shales had been known for decades. Typically, wells were drilled past the shales, and these zones were cemented in because of extremely low permeability that made extraction uneconomic. In recent years, shales have turned into prolific natural gas sources, as a result of many combined innovations. Most of them comprised minor advances to existing technologies, but together they led to a quantum leap in natural gas development. Among the innovations were improvements in geosteering and associated logging-while-drilling and measurement-while-drilling tools; fit-for-purpose “flex” rigs with smaller footprints, and higher mud-handling and drilling capabilities optimized for efficiency; and high-volume multistage hydraulic fracturing of the productive formation, along with associated tools such as packers and three-dimensional fracture treatment simulators.
Future Technologies To Watch
Future innovations will continue to be driven by business growth challenges, as we saw in past examples. Innovations from other industries— including IT—will also find application in upstream oil and gas. In any case, there is every chance we will see some profound transformations in the oil and gas technology space over the next 25 years. Let us look at some of the business imperatives and niche technologies that could drive those changes:
“Green” operations. Oil and gas operations increasingly have started to intersect with urban settlements. Additionally, the high density of activity related to unconventional resources has caught the attention of environmental groups, regulators, and community residents. To succeed, E&P operators have to develop additional ways of reducing their environmental footprint. Focus areas could include the use of chemicals and additives in drilling muds, cement, and hydraulic fracturing water; produced water handling; emissions and flaring; and noise pollution. In addition, the use of solar and wind energy for steam and power applications is receiving close attention. The need to remove pollutants could stimulate the commercialization of more futuristic research ideas such as laser drilling.
Operational integrity and digital technologies. Data gathering and sharing, advanced collaboration, and telepresence are likely to continue playing an increasing role in more effective and efficient management of existing fields and new developments. In existing fields, these technologies fundamentally help to extend asset life, more proactively maintain equipment, predict failures by means of condition monitoring, reduce personnel exposure, and prevent downtime. Digital monitoring and control technologies also are a key to continuing efforts to mitigate risk of operational disasters.
Unconventionals. The evolution of unconventional resource extraction continues. Fracturing technology in unconventional gas plays yields an estimated 10% to 20% recovery factor. One concept under development is to focus the fracturing process more on “shattering” the rock matrix than on creating planar flow paths. This could tremendously boost recovery factors.
Improving field recovery. There is great upside to improving recovery from declining fields. Besides traditional means such as infill drilling and enhanced oil recovery (EOR), there will be a push to increase recoveries from a range of reservoir monitoring approaches (e.g., time-lapse seismic) and a growing suite of EOR techniques. One interesting potential technology is the use of microbes to break down heavy oil into lighter fractions that are more easily recovered. Application of nanotechnology, smart fluids, and improved sensors hold promise in the areas of equipment durability, corrosion resistance, and precision flow.
Ultradeepwater and smaller offshore projects. In past decades, the operating water depth limit for drilling and production has progressed from a few hundred feet to more than 10,000 ft. Those depths call for very specialized equipment at the seabed and the surface. In addition, the diminishing size of the average offshore discovery presents challenges in operational efficiency because of the huge upfront capital outlays required.
There are many promising technologies on the horizon, and it is impossible to do justice to all of them. Instead, let us look at one example and walk through some of the wide spectrum of its applications. In recent years, the use of radio frequency identification (RFID) chips has emerged as one of the innocuous technologies that can become ubiquitous in its many potential applications. When a tubular string—or drill bit, valve, or joint—is lowered downhole, each tagged element of that string can be tracked over the course of its service life, including data on operating hours downhole and exposure to pressure, temperature, and corrosive environments. Any shop maintenance or repairs can be tracked, and relative position in a tagged casing string can be accurately determined. When fluid is pumped down tubulars, injection of an RFID chip at fluid interfaces can help determine the precise arrival of those fluids at various valves or the formation face. Smart valves can be open or shut by means of pump-down RFID chips carrying programmed commands. Or a set of perforating charges can be triggered by an RFID chip. All surface equipment and machinery can be tagged and geolocated. When necessary, spares can be located quickly. When crude leaves by rail, each rail car can be tagged and located, or when crude is pumped through a pipeline, each operator’s batches can be tracked by RFID chips carried at the interface, thus enabling precise inventory management. Even for this one technology, trying to recount all the conceivable applications seems impossible.
The oil and gas industry has powerful business drivers, as well as creative technology innovators. For the foreseeable future, as resource access, development, and exploitation become harder, the industry is bound to produce technological innovations to meet its many challenges. The Chinese proverb, “May you live in interesting times,” will surely apply to the oil field.