Ask a group of university engineering students to name the most technology-driven companies in the US today, and the odds are against any oil and gas businesses turning up on the list. But while the energy industry is certainly a mature business compared with, say, the electronics industry, there is no reason to believe that the evolution of the underlying technological basis of our business has somehow come to a halt. In fact, a close examination of current projects and future trends in global energy markets paints a far different picture.
While some doomsday critics insist the world is running out of oil and gas, many energy analysts believe that we have produced only about one-fifth of our known resource base. That leaves 80% of our global oil and gas resources yet to be developed. In reality, we are likely to be closer to the start of the petroleum era than to its conclusion. Of course, the caveat here is that the most easily accessible oil and gas deposits have, for the most part, been discovered and extracted. More and more, producing the remaining portion of the global energy resource base depends on returning to reservoirs that were written off in the past as being not economically viable, too remote, or too challenging technically.
As a result, the development and application of technological breakthroughs have increasingly become the key to unlocking our industry’s future. This, however, cannot be accomplished without energy companies coming to terms with two important challenges: enlarging the pool of talented E&P technical professionals and creating effective organizational environments that allow these talented people to thrive.
New Technical Challenges
To understand the kinds of technical challenges faced by the industry today, we have only to look at the Chevron Jack #2 test well, which recently set new depth records for a well test in the US Gulf of Mexico. This successful well would not have been possible without engineers and scientists pushing the technological envelope at every point—from state-of-the-art seismic processing to record-setting deepwater performance from perforating guns, test trees, and other drillstem-test tools. In fact, more than a half dozen world records for test-equipment pressure, depth, and duration in deep water were set during the well test.
We are also seeing more and more examples of advanced technology being used to revive production in mature fields once thought to be past their prime. Chevron’s Kern River field in California is a case in point. Discovered in 1899, this reservoir of more than 3 billion bbl of heavy (13°API) oil would appear to be on its last legs after more than 100 years of production. Today, however, Kern River boasts 8,000 producer and 1,000 injector wells, along with 600 thermal observation wells. Using key technologies such as steamflooding, the reclamation and reuse of produced water, and 3D visualization to meet the challenges of producing the field’s heavy crude, Chevron engineers are setting new production records as they pursue their goal of extracting as much as 80% of the crude oil contained in the field.
A similar story can be found in the case of Indonesia’s Duri field, a 1941 discovery that was judged to have reached peak production in 1963 at 65,000 BOPD and then entered a period of steep decline. Today, Duri is the largest steamflood field in the world. More than 75% of the field is under steam injection, and total production is running at 200,000 B/D.
Steamflooding may also play a role in the revival of production in the onshore Partitioned Neutral Zone (PNZ) between Saudi Arabia and Kuwait. A precedent-setting application of steam injection into a carbonate reservoir, this enhanced-oil-recovery method has the potential of significantly increasing the recovery of heavy oil in the PNZ reservoirs, as well as in other areas in the Middle East.
Jack#2. Kern River. Duri. PNZ. These examples of increasing production by raising the technological bar are increasingly typical of an industry once characterized by the frantic search for undrilled acreage.
New Roles for Technical Professionals
Market-driven forces are pushing companies to make dramatic increases in their technology investments, as well as to find innovative uses for existing technologies. At the same time, rising production costs and increased downside risks increase the penalty for poor performance. In this new economic landscape, companies are looking for an integrated approach that links all engineering and Earth-science disciplines into large-scale, technologically sophisticated solutions yielding above-average returns on investment. Far from being limited to outdated industry-standard practices, E&P technical professionals are now expected to develop and apply innovative solutions to complex, multifaceted problems, constantly pushing the limits of existing capabilities.
Increasingly, technology specialists in the energy industry are finding themselves working in a multidisciplinary-team environment, contrasting sharply with the technical “silo” approach that formerly kept the different disciplines from interacting with one another. Moreover, this new team-focused approach often takes place in a multinational or multicultural setting that requires high levels of technical, soft, and teamwork (TST) skills on the part of the participants to make the project successful. For energy companies, a diverse multiethnic technical workforce able to function at an extremely high level across a wide range of business environments around the globe remains not just a desirable goal, but a necessity.
A Changing World
Thanks to recent revolutions in the global information environment such as the Internet and the emergence of 24/7 news media, world public opinion of our industry can change with breathtaking speed. For example, environmental concerns about energy production are at the forefront of media attention, and E&P projects are now under unprecedented public scrutiny. In many cases, the levels of environmental protection provided by past practices are no longer acceptable, and E&P professionals will be responsible for offering new and more comprehensive solutions to some of the most complex technological problems ever faced by science.
Public concerns with energy industry are not limited to environmental concerns. Across the globe, E&P organizations are being asked to address myriad pressing economic and social questions arising from their host communities in politically sensitive areas such as west Africa, the Middle East, and Southeast Asia. Technical professionals must be willing to look beyond a narrow focus on their E&P disciplines and help play a positive role in developing solutions that benefit both their companies and their host communities.
None of these challenges can be overcome without our next generation of technical leaders finding themselves in engaging, employee-friendly working environments with a balanced approach to job and family responsibilities. Only by addressing these issues can our industry hope to keep talented people over the course of productive and long-term careers.
Career Ladders for Technical Professionals
To attract and retain the kind of world-class technical expertise needed to succeed today, energy companies must be willing to invest in extensive training programs that focus not only on the “hard” technical skills but on such “soft” skills as interpersonal communication. This approach will allow a new generation of employees to flourish in a fast-moving, team-driven workplace that technology solutions increasingly require. In this environment, energy companies must be willing to create clearly defined career ladders for their top technical people. These career ladders must provide challenging assignments and full engagement across a broad range of company interests to guarantee a continuous pipeline of talent from which to construct a well-rounded leadership team at the corporate level for promising young managers.
None of this is possible, however, without a rewards system that is focused on aggressive pay progression and results-based incentives for the top-flight technical talent—one that removes the barriers to a rewarding career for those who choose to stay working in their scientific discipline. To understand the challenges our industry faces when hiring and developing outstanding technical personnel, we have only to look at industrywide compensation practices. For example, in November 2006, SPE conducted a survey of more than 2,700 members that yielded the results indicated in Fig. 1.
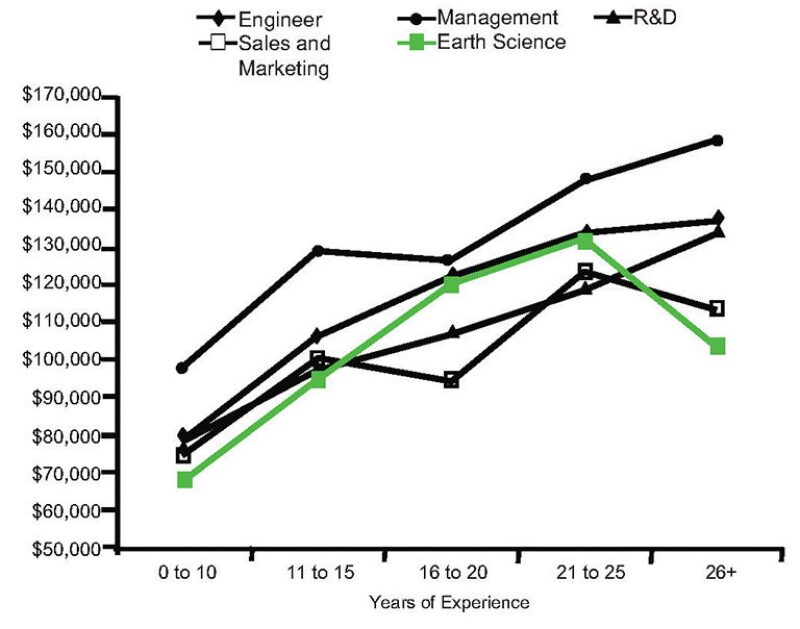
As the information for new hires and experienced professionals indicates, there is a strong financial incentive for technical people to move to management ranks as quickly as possible. While the gap between technical and nontechnical salaries narrows somewhat during midcareer, managers see a hefty increase in earnings as their careers come to a close, while technical professionals experience a gradual flattening of pay increases during the final years of their careers. To remedy this disincentive for skilled employees to remain in technical fields, companies must establish technical career ladders that are similar to executive grades in terms of compensation and benefits and that reduce the monetary gaps that increasingly differentiate managerial and technical career paths as the employees gain experience.
Challenges for Technical Professionals
For technical professionals, the challenge we face is one of continuously expanding our TST skills, while taking an active role in our own career development. This active ownership includes demonstrating a willingness to embrace the global nature of the modern energy industry, as well as the ability to interact positively with people of different cultures and backgrounds.
Networking and professional visibility are necessities in this environment. We also must be capable of communicating the economic importance of our industry to a wider audience, educating the public about our business and its critical role in our society. Above all, however, we must be able to demonstrate that we can deliver technological solutions that represent extraordinary increases in value over current systems for our customers and our companies.
Summary
Both E&P professionals and their employers face new challenges as the economic and technological environment of the global energy industry continues to evolve. For energy companies, success in hiring and maintaining teams of world-class technical experts depends on ensuring that their organizational strategy allows for the development and advancement of their top-performing employees.
- Provide an exceptional reward system—remove the perception that technical professionals must switch over to a management track to further their careers.
- Invest in training and in long-term career development.
- Provide technical experts with challenging assignments, and fully engage them in the business.
- Create a constant pipeline of new employees—use top and experienced employees to mentor new hires.
For individual employees
- Continue to develop skills that encompass a wide range of business solutions, including TST skills.
- Adapt to the global nature of our business.
- Create exceptional benefits for the business and its customers—become invaluable to the company.
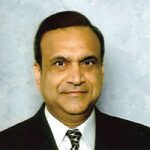
Ganesh Thakur was appointed Global Adviser–Reservoir Management for Chevron in 2005 and is currently responsible for championing reservoir-management technologies and practices throughout the corporation. Additionally, he is responsible for mentoring professionals, developing relationships with national oil companies, serving as a technology ambassador worldwide, and advancing “International Company of Choice” initiatives. Thakur is a recognized leader in petroleum engineering, including reservoir management, secondary recovery, reservoir and well productivity improvement, simulation, and enhanced oil recovery. He was SPE’s first Technical Director for Reservoir Description and Dynamics on the Board of Directors. Thakur has been active in professional societies including SPE, the American Association of Petroleum Geologists, and the Society of Exploration Geophysicists. He received SPE’s Reservoir Engineer of the Year Award in 2005, is an SPE Distinguished Member, and was an SPE Distinguished Lecturer.