The growing desire of offshore operators to speed up subsea field development while reducing costs has fostered many compelling innovations. Among those systems under development to meet this demand, and one with broad applications, is a subsea storage unit (SSU) created by Kongsberg Oil & Gas Technologies.
The growing desire of offshore operators to speed up subsea field development while reducing costs has fostered many compelling innovations. Among those systems under development to meet this demand, and one with broad applications, is a subsea storage unit (SSU) created by Kongsberg Oil & Gas Technologies.
The SSU employs the new concept of a “flexible bag” protected by a dome for oil storage on the seafloor (Fig. 1). Depending on field conditions, the dome can be made of concrete, fiberglass, or steel. The system offers oil companies a safer, more cost-effective method of developing subsea fields in extreme weather zones or in the Arctic where ice floes are prevalent. The SSU is also being qualified for extended well testing (Fig. 2) and early production startup, and it may enhance the economics of fields with insufficient reserves to support full field development. Furthermore, the SSU could be used in place of subsea storage cells, fixed platforms, floating storage units (FSUs), and pipelines.
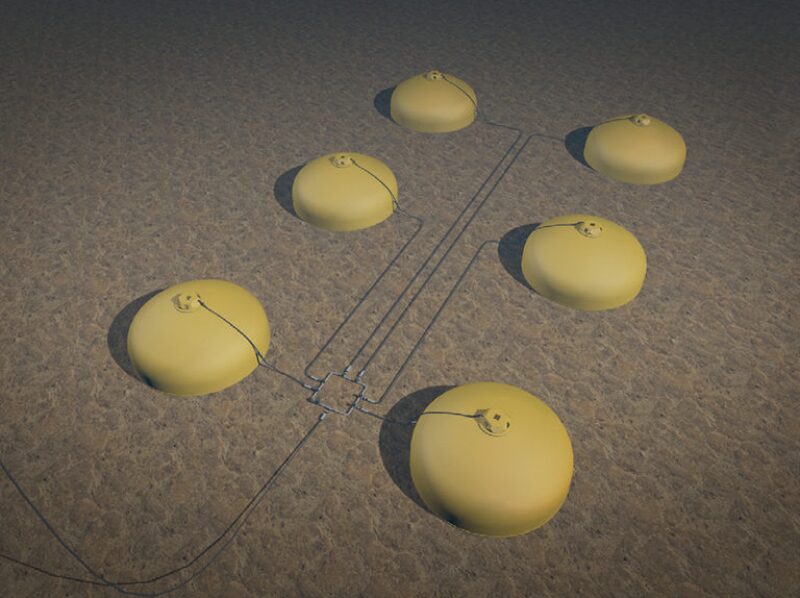
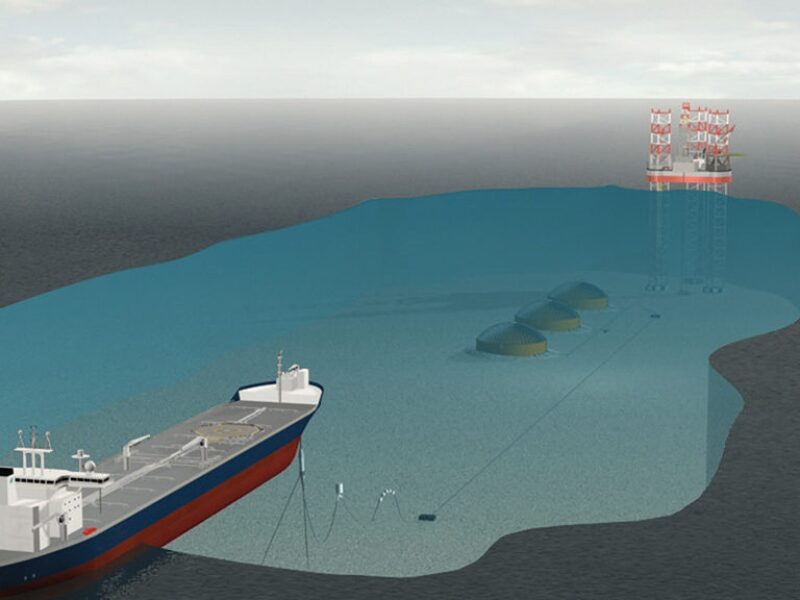
“It is an alternative to existing storage facilities and could also potentially commercialize the development of marginal fields,” said Astrid Rusås Kristoffersen, a subsea systems product and technology manager at Kongsberg. “The [SSU] will increase profitability of marginal fields, because the oil can be stored subsea. And then, using small shuttle tankers for more frequent offloading will precipitate the cash flow and reduce operational costs.”
Ideally, two or more SSUs could be used to maximize the allowable output volume that could be uploaded into a tanker. As production increases, SSUs could be added to the cluster. Kongsberg is considering standardizing the dimensions of the SSU to fit different needs, with the largest version on the drawing board being 131 ft (40 m) in diameter with a capacity of 120,000 bbl of oil.
Subsea storage technology has been used before in limited applications, but never has the design used a collapsible bag to store the oil. The bag is partly made of a polyester woven yarn that is coated with an impermeable layer on both sides to eliminate the possibility of seawater and oil mixing. Were that to happen, an emulsion layer could form, leading to bacterial growth that could cause corrosive damage inside steel pipelines and valves.
Subsea Storage Unit Operation
Openings at the base of the SSU allow seawater to flow in and equalize the pressure. So there is no need to design against pressure and the unit can be deployed to any water depth. The bag can then expand and contract as the volume of oil inside increases and decreases. Depending on the type of soil, a combination of weights, suction anchors, and piles could be used to secure the SSU to the seabed.
The SSU’s intake valves allow the product to flow inside, and once the bag is filled to capacity, the oil can be transported to a tanker through a standard flowline and offloading system. If an operator wishes to use the SSU for chemical storage, the unit would work in the same fashion. Only the source of fluids entering the SSU and the final export flow destination would differ.
If the internal sensors detect a leak inside the bag, they will shut off the intake valves while alerting the operator to the problem. The SSU’s design creates a “double barrier” that protects the environment from exposure to hydrocarbons. “In case the bag should rupture, the outer dome is capable of collecting all the source fluids, preventing spillage into the sea,” Kristoffersen said.
With the dome serving as the second containment layer, the leaked oil can be safely extracted to a sister SSU or discharged to a shuttle tanker on the surface. A removable hatch atop the SSU provides access to the bag and allows easy retraction when replacing the bag.
The SSU’s weight will depend on field conditions and hydrostatic uplift forces from the stored oil and other fluids. In its base configuration, the SSU is designed to float so that a wide variety of vessels can perform the installation work, which eliminates the need for heavy lift vessels.
Expected Service Life
The dome and shell of the SSU will typically have a service life of 25 years and the bag is being qualified for a life span of 10 years. Kongsberg is looking for ways to extend the bag’s life.
The inspiration for the SSU arose from Statoil’s quest to eliminate the need for surface production systems and put the entire “factory floor” directly on the seabed. “This is one piece of that puzzle,” said Kristoffersen, who added that the SSU also provides a measure of safety for operators who are aggressively seeking new ways to eliminate hazards.
“Currently a lot of oil is stored on FSUs and [floating production, storage, and offloading units], and there is always the risk of collisions with a tandem-loading shuttle tanker. So by storing it subsea, you eliminate that risk,” he said.
During a fire or an onboard explosion, the oil stored in the SSU will not continue to feed the fire. Additionally, if an operator uses several SSUs instead of a floating or fixed storage facility, operating costs will be greatly reduced because subsea storage removes the need for a manned crew or helicopters and boats that provide supplies and transport. Instead, the SSU can be integrated into a remotely controlled subsea production system or a topside production facility that removes the water and gas before transferring the raw crude into the storage unit.
System Flexibility
The flexibility to suit the operator’s field needs is another advantage of the SSU over traditional storage systems because each SSU can be picked up from the seafloor and be redeployed to another field.
If used for extended well testing, the SSU provides another economic incentive by allowing the operator to collect first oil rather than “burning off” the product. Compared with traditional surface storage, the SSU in operation has a considerably lower environmental footprint because the system requires no routine vessel or aircraft support that would emit greenhouse gases.
The SSU technology is being developed for use in the North Sea and is supported by Norwegian oil com-panies Statoil, Lundin Petroleum, and Det -Norske Oljeselskap, and by the Norwegian Research Council. Kongsberg will start laboratory tests in 2014 after which the company plans to begin a pilot program that would include the subsea installation of a full-scale SSU.
The SSU is being designed to meet the requirements of Norway’s offshore regulations and is to be qualified for the North Sea. However, Kristoffersen said, “The SSU is providing a global solution for storing stabilized oil on the seabed.”
Because the SSU is a new design, Kongsberg is offering studies to show the feasibility and concept of subsea storage for specific fields, including the studies of risers, subsea manifold systems, interconnecting pipes, and the control system logic required for SSU operation and process integration with specific offshore infrastructure.