With advancements in digitalization and technology, simulation in oil and gas field is becoming more essential and indispensable for this industry. It becomes the key to deliver detailed analyses that improve performance by decreasing operational time and cost to maximize profits and increase production capabilities.
These simulators are convenient for young professionals in their projects, and very practical for students in their assignments and research. Unfortunately, most of these simulators are unaffordable since complex and advanced simulators are expensive and exclusively purchased by petroleum companies.
This article provides information about software available that can be used for free. We discuss seven open-source simulators and their features and advantages.
OPM Flow
The Open Porous Media (OPM) flow simulator is an open-source software for simulating, upscaling, and visualizing processes in porous subsurface reservoirs. It was developed in collaboration with Equinor, NORCE, and Ceetron solutions and is one of the black-oil models designed to run standard simulation models. It requires no license management for its numerous features. OPM can formulate many models such as the polymer module, the solvent module, and the foam model used to simulate surfactant-injection operations.
In addition, this simulator can control bottomhole pressure, surface and reservoir rate, well lists, action conditions and command processing, along with controlling history matching wells. In general, data inserted (input) and results released (output) are flexible and can be read using Eclipse software. Finally, OPM flow simulator is characterized by its flexible assembly and rapid development of new fluid models through its automatic differentiation framework.
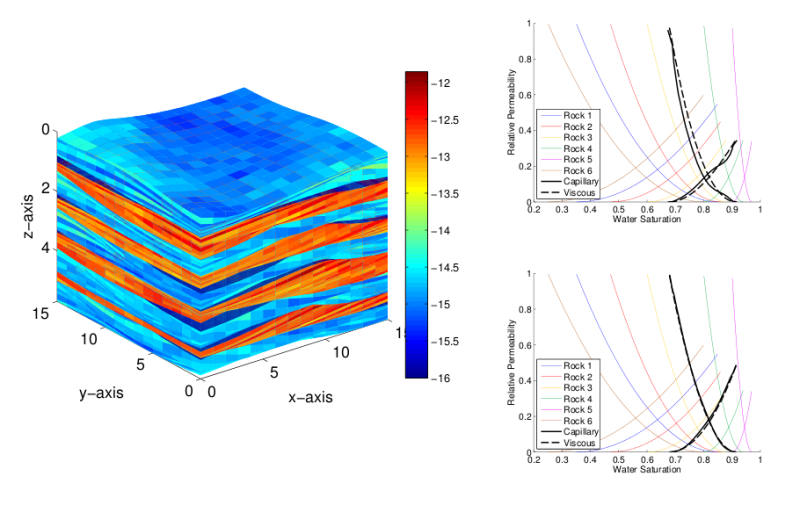
The Matlab Reservoir Simulation Toolbox (MRST)
The Matlab Reservoir Simulation Toolbox (MRST) is a free open-source software for modeling and simulating subsurface reservoirs. It was developed initially by the computational geosciences group from the mathematics and cybernetics department at SINTEF Digital. This software has a big international database that can be accessed by the user. It also includes different modules that were developed by Heriot-Watt University researchers. It is generated to ensure a fast framework and examination of the problems encountered in the reservoir simulation.
MRST is an extension of the black-oil model due to the addition of new relationships and features such as polymerflooding, thermal effects, and reactive effects. This simulator is characterized by its highly vectorized scripting language combined with automatic differentiation to authorize the user to simulate using advanced high-level mathematical objects. Finally, MRST offers special and important features such as upscaling of different parameters, grid coarsening, steady spatial discretization, and interactive visualizations.
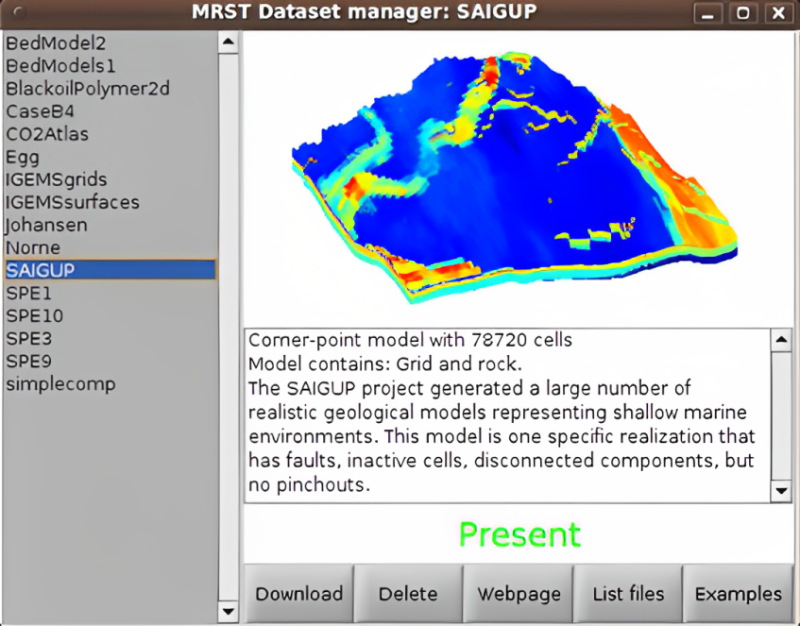
BOAST 3-PC
BOAST 3-PC is a black-oil applied simulation tool (BOAST) used routinely for performing evaluation and design work in petroleum reservoir engineering. In 1982, the US Department of Energy released the original black-oil model called BOAST. BOAST II, released in 1987, was designed to provide more flexibility and to overcome some of the limitations of the original BOAST. Many features were added to improve the versatility of the model.
BOAST 3-PC simulates isothermal, Darcy flow in three dimensions. It assumes that reservoir fluids can be described by three fluid phases (oil, gas, and water) of constant composition with physical properties that depend on pressure only.
BOAST 3-PC has a wide range of applicability. It can simulate oil and/or gas recovery by fluid expansion, displacement, gravity drainage, and capillary imbibition mechanisms. Some of the typical field production problems that can be handled by BOAST 3 include but are not limited to
• Primary depletion studies.
• Pressure maintenance by water and/or gas injection.
• Evaluation of waterflooding operations.
BOAST 3-PC is a finite-difference, implicit pressure/explicit saturation (IMPES) numerical simulator. It includes options for both direct and iterative solution techniques for solving systems of algebraic equations. Some of the features and options of the model include
• An option for simulating steeply dipping reservoirs.
• Allowances for multiple rock and pressure/volume/temperature regions.
• A bubblepoint tracking scheme.
• An automatic time-step control method.
• Material balance check on solution stability.
• Allowances for multiple wells per grid block.
• An option for rate or pressure constraints on well performance.
In addition, BOAST 3-PC includes two post processors: B3PLOT2 and COLORGRID. B3PLOT2 is a line graphics package used to plot data such as production, pressure, and saturation vs. time. The package has two modes:
• Plotting simulated data, allowing comparison of the results from up to five different simulation runs
• History matching using oil, water, or gas production data, Gas/oil ratio or water/oil ratio; the average reservoir pressure or bottomhole well pressure can also be matched.
COLORGRID is used to view the finite difference grid on the screen as either a plan or elevation. The range of the parameter selected determines the color of the grid. Various arrays (maps) of input or output data may be represented by a 12-band color legend. An annotation option, which displays the numerical values of the parameter selected within each grid block, is provided. Any portion of the grid may be expanded to fill the entire screen.
DuMux
DuMux, Dune for multi- {phase, component, scale, physics, domain … } flow and transport in porous media, is a free and open-source simulator for flow and transport processes in porous media. Its main intention is to provide a sustainable, consistent, and modular framework for the implementation and application of porous media model concepts and constitutive relations. It has been successfully applied to many applications in the oil and gas industry.
DuMux is based on the Distributed Unified Numerics Environment (Dune), an open-source scientific numerical software framework for solving partial differential equations and is thus part of a larger community that goes beyond the simulation of fluid–mechanical processes in porous media. Dune and DuMux are written in C++, using modern C++ programming techniques and C++ template meta programming for efficiency and generic interfaces. The Dune core modules provide, among other things, multiple grid managers implementing a versatile common grid interface, linear algebra abstraction, and an iterative solver back-end, as well as abstractions facilitating parallel computing. DuMux is designed and developed as a Dune module depending on the Dune core modules and optionally interacts with several other Dune-based extension modules.
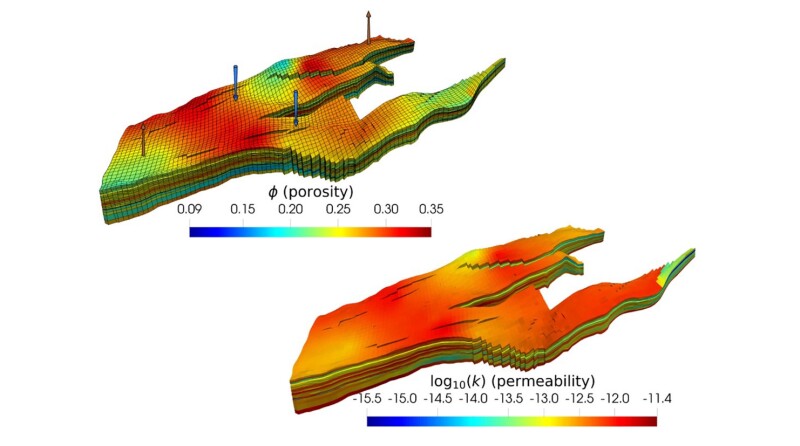
UTCHEM
UTCHEM is a multicomponent, multiphase, 3D chemical compositional reservoir simulation model. The solution scheme is analogous to IMPES, where pressure is solved for implicitly, but concentrations rather than saturations are then solved for explicitly. Phase saturations and concentrations are then solved in a flash routine. In this simulator, the flow and mass-transport equations are solved for any number of user-specified chemical components (water, organic contaminants, surfactant, alcohols, polymer, chloride, calcium, other electrolytes, microbiological species, electron acceptors, etc.). The latest development is designed for large-scale reservoir simulation on parallel computer.
UTCHEM oil reservoir applications include:
· Waterflooding
· Single well, partitioning interwell, and single well wettability tracer tests
· Polymerflooding
· Profile control using gel
· Surfactant flooding
· High-pH alkaline flooding
· Microbial enhanced oil recovery (EOR)
· Surfactant/foam and alkaline surfactant polymer (ASP)/foam EOR
· Tracer tests to characterize both single- and dual-porosity oil reservoirs
· High-pH chemical flooding for EOR
· Profile control of oil wells with polymer gels
· Modeling formation damage of oil wells
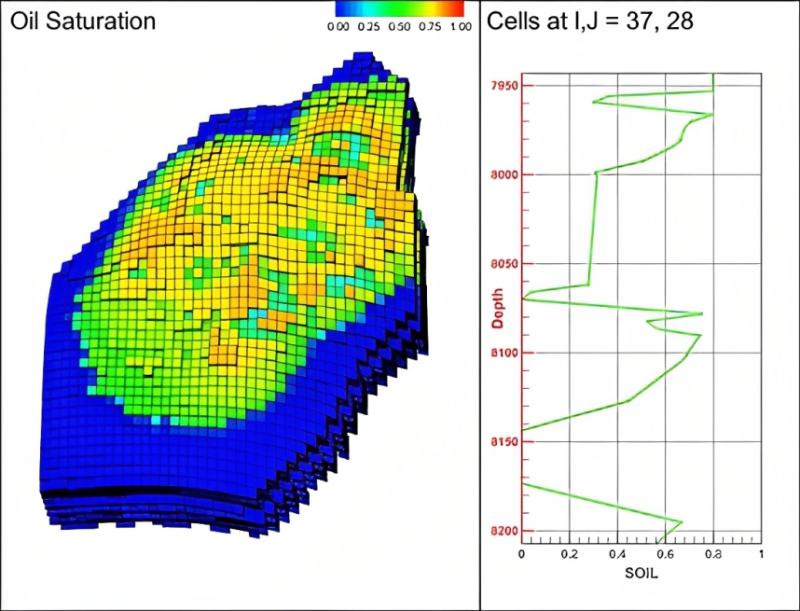
OpenLab Drilling
OpenLab Drilling is a simulation software used for virtual drilling and well operations that combines a web-based online drilling simulator, drilling control room, and a functional full-scale on-site drilling rig, developed by the Norwegian NORCE’s drilling and well modeling group in collaboration with University of Stavanger.
The user can choose one of numerous premade configurations/templates, then can run a simulation with no need for input editing interactively through a web browser, or also programmatically through NORCE’s Matlab or Python packages. In addition, OpenLab can run downhole 3D simulations with different scenarios.
The most important feature in this simulator is that the drilling and well operations are performed using the world’s most advanced drilling test site and a type drilling rig Ullrigg, with access to a number of wells, and where OpenLab simulator will be used for surface and downhole artificial measurements from virtual wells. This software is used by Equinor, University of Calgary, MAERSK drilling, etc.
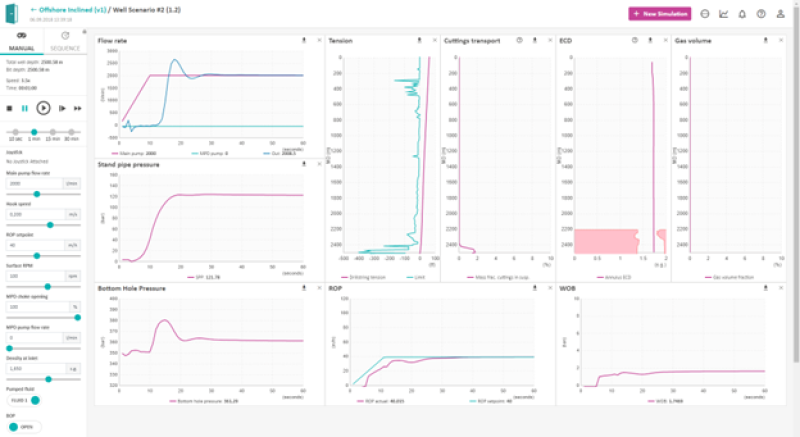
Well Control Simulator
Well Control Simulator, one of the best-priced simulators in the industry, was developed by LearnToDrill in collaboration with Chevron (where they globally launched the drilling simulator), Lone Star College, and BP, where it complies with IADC WellSharp well control guidelines.
This simulator is cloud-based with modern technologies on various devices (iPhones, iPads, or laptops); thus, no hardware is required. It allows unlimited simulator practice with an AI instructor.
Well Control Simulator is used for all IADC-required simulations, including completion, well servicing, well control and kick detection with kill problems. First, you can start with a setup of 10 preset templates and configurations. Second, you can create custom wells (with parameters like piping sizes, kick timing, etc.). Then finally the expected output is presented in detailed graphs showing pressure behavior at different stages of the kill operation where these graphs can be saved as PDF files ready to be exported.
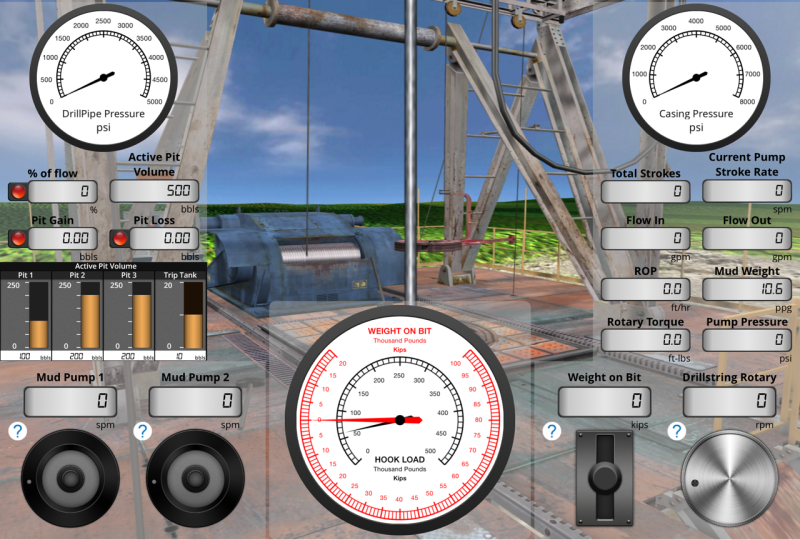