In October 2024, James Blaney began his term as TWA editor in chief. Blaney is an application engineer for Chevron's MidCon Business Unit, holding bachelors degrees in economics from Georgetown University and petroleum engineering from the Colorado School of Mines.
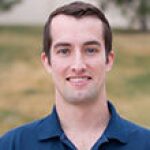
He cut his teeth in the Permian Basin as a field engineer for Liberty Energy before progressing to a software development role working on pump-control software, integrating their new electric digiFrac and natural gas-powered digiPrime pumps.
He sees plenty of room for the role of tech in industry to grow and firmly believes if you're going to do anything twice you should automate it once.
TWA: What inspired you to pursue a career in the oil and gas sector, and what was your first role in the industry?
JB: I was attracted to the industry by a number of factors—the centrality of its product to modern life, how close engineers are to the dirt both figuratively and literally, the colorful history, and the wide variety of professional opportunities from both a technical and geographic perspective.
My first position was working as a field engineer on a fracturing crew in the Permian Basin, which was a great way to learn firsthand about the translation of theory into practice.
TWA: Could you tell us about your educational background and how it prepared you for a career in the oil and gas industry?
JB: I completed a bachelor’s in petroleum engineering at the Colorado School of Mines (CSM) where I also dabbled in computer science coursework.
My petroleum engineering coursework familiarized me with industry terminology (units, jargon, equipment, etc.), the basic calculations and assumptions that now operate in the background of modern software, and possibly most importantly, a ballpark range for reasonable values. While I have never solved engineering problems by putting pencil to paper in my professional life with anywhere near the frequency I did in the classroom, this ballpark is an important part of being able to 'smell test' results or readings from software or systems.
I reference my computer science coursework because it prepared me (unintentionally) for advancement from my first role as a field engineer into my subsequent work at the interface of industry and technology as a software engineer working on fracturing pump control software.
The Venn diagram of software engineer and petroleum engineer is a small but growing sliver, and I have found it extremely rewarding to work at that interface, translating between worlds.
TWA: Were there any pivotal moments or experiences early in your career that shaped your professional path?
JB: First, my initial role as a field engineer was pivotal to driving home that the translation from theory to practice hinges on good communication (and relations) between engineering and operations. And good communication demands engineers understand how theory is translated into practice.
Second, and slightly more generally, pursuing opportunities even if I didn’t feel 100% ready for them. I was able to do this because of developing a strong relationship with in-house mentors who knew my abilities and interests and encouraged me to take on new challenges when suitable ones appeared. They helped me reframe unfamiliar situations from 'I don’t know' to 'I have the knowledge base and skill set to figure it out as we move forward.'
TWA: How did you first become involved with The Way Ahead?
JB: After completing my engineering degree, I was looking for a way to stay involved in SPE. My rotational schedule as a field engineer made it difficult to commit to in-person involvement on a set schedule so I was looking for more flexible opportunities. A fellow student at CSM had joined the editorial board following her graduation and recommended it to stay involved. I applied and was invited to join the TWA HR Discussion department. Since then, I have also been a content creator for the Business Benchmarks department and lead content creator for the History and Pop Culture department.
TWA: What has been your most rewarding experience during your time with The Way Ahead?
JB: It’s hard to pick just one, but I think I can narrow it down to two.
First, the opportunity to write on such a wide variety of topics—from the future of petroleum engineering studies during back-to-back 'once a lifetime' industry downturns to a tongue-in-cheek review of oil and gas portrayals in Hollywood to (my personal favorite, and still highly read!) an analysis of how Standard Oil’s antitrust legacy from 1911 is relevant to today’s tech titans—and have my work read. It was particularly rewarding when former professors reached out to comment on my work!
Second, I have had the privilege to do this with an incredible team of fellow young professionals (YPs). People from all over the world (which, I’ll tell you for free, can make finding suitable meeting times a challenge!) working in all different facets of the industry provides a great opportunity to grow your network and gain exposure to a variety of viewpoints and unique industry facets.
TWA: What are the keys to keeping The Way Ahead relevant and engaging for YPs in such a dynamic industry?
JB: The topics of interest and concern to YPs change over time, and it is important that TWA’s content evolves to reflect them. When I started in 2017, coming out of the downturn, job finding, marketability, and skills development were all hot topics. During the COVID-19 pandemic years, remote work and the impact of 'the new normal' on industry were on everyone’s mind. In the past 2 to 4 years as supermajors spun up alternative/green energy initiatives, these were interesting areas of opportunity for YPs. Many now seem to be winding these down or scaling them back, and I suspect YP focus will continue to grow on big data, data science, and artificial intelligence/machine learning opportunities until the next big trend emerges.
Fortunately, by virtue of being staffed entirely by YPs, TWA's article mix is largely self-correcting. YPs know what issues are important to them!
TWA: How do you see the role of YPs evolving as the industry adapts to new technologies?
JB: Tools with increasing capabilities and growing automation do not obviate the need for good engineers, the same way autopilot does not obviate the need for a pilot in the cockpit. Autopilot can handle routine scenarios and common deviations, but unprecedented issues require the ability for intervention from a knowledgeable, skilled, and dynamic individual (think Captain Sullenberger and the 'Miracle on the Hudson').
Increased capabilities come with increased complexity, meaning more potential points of failure. With respect to tools they use on a regular basis, a skilled YP will know how to use tools from the front end, what a reasonable result from the tool should look like given a set of inputs, and eventually, how to debug anomalous results independently (i.e., without involving more experienced individuals, developers, or vendors). This goes back to the ballpark values/smell test I mentioned earlier.
All tools (and manual calculations) are also susceptible to the 'garbage in, garbage out' problem—even if all the calculations are correct; if the starting numbers are bad, the output won’t lead to optimal decision making. With more data going through varied collection processes (e.g., some manual, some automated production entry, depending on facility construction) and 'black box'” processing before reaching a point for end-user consumption, familiarity with these processes and failure modes will enable YPs to identify bad data before and avoid using it to generate unactionable output.
TWA: What opportunities do you think the energy transition presents for YPs in oil and gas?
JB: The energy transition is still in its early stages and presents YPs with 'big risk, big reward' situations. The primary industry players in the transition are the supermajors with the capital to explore new ventures, and new ventures are always one of the first on the chopping block when a downturn looms. That said, as a nascent facet of industry, there are lots of opportunities to position oneself as a technical or thought leader in the energy transition. There are opportunities through translation research in overlapping areas such as carbon capture, utilization, storage, CO2 flooding, geothermal and shale fracturing, or through stepping into more novel/technologically independent solutions such as green hydrogen, solar, or wind.
As I mentioned earlier, the current industry trend seems to indicate a pullback from energy transition initiatives, so YPs who wish to fully commit to the related technologies may struggle to find relevant opportunities with companies whose core business is oil and gas extraction. As a result, YPs eyeing energy transition-related opportunities need to consider the career trajectory it might put them on if their desire is to ultimately remain near to oil and gas.
TWA: Are there any skills or experiences you believe are essential for success in today’s industry landscape?
JB: Field and operational exposure is a must. Knowing how things are executed helps inform where there is room for improvement vs. where ostensible “easy wins” are not feasible in practice. It also gives insight into real operational challenges, failure modes, and tolerance levels as compared to the textbook answer.
TWA: What role do networking and professional organizations like SPE play in building a successful career?
JB: They help build a successful career in a variety of ways. First, the obvious direct benefit is being made aware of opportunities that you might not have found or been referred to—my first position after completing my engineering degree was a referral by a graduate student whom I met through SPE to a hiring manager whom she met through SPE.
There are plenty of less direct positive career impacts. As a technical professional, involvement helps keep you in the loop of up-and-coming trends and technologies that may be of interest to your company.
SPE also provides an opportunity for YPs to start developing leadership skills and building experience in leadership roles by managing a committee (or publication); even opportunities to develop those skills aren’t immediately available in their current role.
TWA: What lessons have you learned during your time in the industry that you wish you had known when you were starting out?
JB: Not knowing something isn’t a failure; not being willing to figure it out is. The only way to continue growing and learning as a professional and engineer is to take on challenges, opportunities, and situations that are unfamiliar and therefore things you don’t already have all the answers to. Imposter syndrome is a sign of growth, not inadequacy.
TWA: Looking ahead, what are your goals for The Way Ahead and your work with SPE?
JB: Unfortunately, my journey with TWA is coming to an end after this year as I will be aging out of the YP demographic. During my 8 years as a member of the editorial board I have been fortunate to have had far more opportunities than I ever could have anticipated when I first joined.
I am excited to find new ways to keep myself involved with SPE with my recent relocation to Houston. Personally, I have an interest in the PetroBowl competition given my history as a competitor when I was a student, and professionally in managing and displaying large volumes of data. I expect that these will guide me to my next roles in SPE.