Flowback is a critical phase in the life of a well. After a well is hydraulically fractured, temporary equipment is needed at the surface to remove the frac ingredients that flow back during first production and prevent them from traveling to the permanent facility. The particular equipment needs will vary based on a number of production, fracture, and facility parameters. The Delaware Basin presented a particularly challenging scenario for Anadarko due to the company’s tankless development approach and the use of 100-mesh proppant in the frac design. We found out that sand filtration is a perfect fit for this application and allows us to flowback directly to a permanent tankless facility.
Handling 100-Mesh Proppant in a Tankless Facility
In 2017, Anadarko began moving toward tankless wellsite facilities in the Delaware Basin as a means to improve the overall efficiency of operations, while significantly reducing surface impacts, truck traffic, and associated emissions. These facilities consist of
- Flow from the wellhead through temporary flowback equipment to a permanent separator
- Gas directly to the sales line
- A pump that sends water to a saltwater disposal
- A pump that sends oil down a line at high-vapor pressure to an oil gathering facility
This development approach enables us to eliminate tanks and flares on location, which ultimately provides many benefits such as reduced emissions, reduced facilities costs, and largely eliminates reliance on trucking. While these benefits are significant, early implementation of the tankless development approach presented quite a few challenges to our flowback operations.
Around the same time that we began implementing tankless facilities, our frac design evolved into using 100-mesh proppant. We began seeing significantly more sand at the surface than in our previous frac designs and noticed considerably more sand carryover from our cyclonic sand traps (“cyclonics”) to the permanent facility. With the tanks removed at the facility, there is not a “wide spot in the road” for the sand to settle in after the separator. This caused the sand to carry over cutting out seals on pumps, which if left unaddressed could present cost and potential environmental concerns. This prompted us to go back to the drawing board to research how to get higher sand-separation efficiency out of our flowback equipment to mitigate and/or eliminate sand carryover to the pumps and gathering lines.
After testing different types and amounts of cyclonics in our setup, we discovered that the cyclonics were not able to effectively separate 100-mesh sand at high liquid rates (5000+ B/D) and high sand rates (2000+ lb/day). We then learned that horizontal sand filtration is a perfect fit for this application where the biggest goal is to prevent sand carryover to the permanent facility. Using two cyclonics and two parallel sand filters, we effectively eliminated all occurrences of washing out pump seals and consistently measured the system efficiency at more than 97%. The cyclonics caught the large majority of the sand, and the filters played clean up by catching the finer sand that slipped by the cyclonic. The sand filters became a mainstay of our flowback operations on tankless facilities.
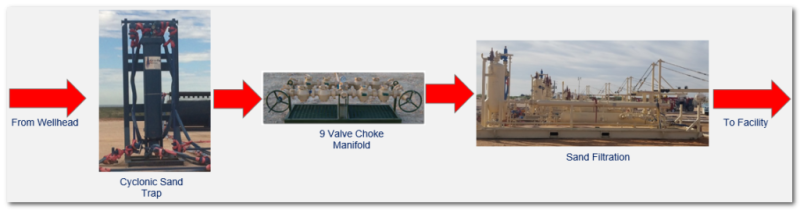
Operational Lessons Learned
While the sand filters met our goal of eliminating sand carryover to the permanent facility, the labor needed to pull and wash screens when they build up sand caused an increase in personnel requirements and associated daily cost increase for extra equipment during flowback. As our wells produce sand for 1–5 months, we had to reduce our footprint during flowback. After many tests at various production rates, we determined a rate where the efficiency of the cyclonics increased significantly, and we were seeing very little, if any, sand slipping by to the filters. Since the filters were no longer catching sand at this phase, we began the practice of releasing sand filters and the second cyclonic whenever the sand production dropped below this rate. This resulted in significant cost savings for our flowbacks.
Just as we were able to optimize our equipment, there were opportunities to optimize our personnel requirements as well. Traditionally, we operated our flowbacks with third-party well testers who stayed on one or two wells 24 hours a day for the life of the cleanup. After the filters were unnecessary below a certain rate, we observed a significant decrease in personnel requirements for the flowback once filters are released, as all that is needed at this point is someone to dump the cyclonic every few hours. This allowed us to release third-party testers around the same time as filters and then turn the flowbacks over to a newly formed in-house flowback team that takes care of the remainder of the flowback. This practice has allowed us to increase the well count per flowback operator and also decrease the costs of third-party testers.
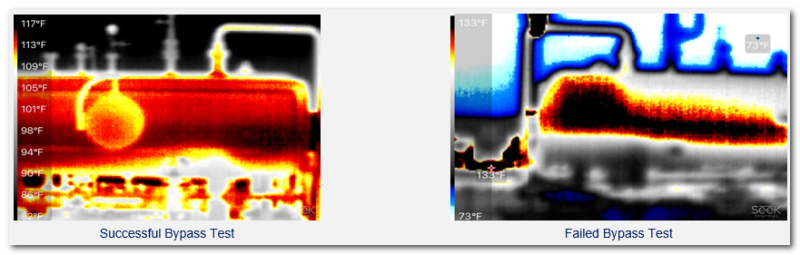
The final learning curve came in tackling the question of when is the appropriate time to release flowback from a well. Is it when all sand production has ceased? Is there some acceptable level of sand production? We decided that the point to release flowback is when periodic sand cleanouts of the production separator becomes more economic than the daily cost of flowback. In order to make this determination, we began using equipment bypass tests. These tests consist of taking a baseline thermal image of the separator, bypassing the flowback equipment for 5 days, and then taking another thermal image of the separator at the end of the test period to determine if there was an appreciable amount of sand buildup in the separator. This practice significantly increased our operational efficiency and ability to release flowback with a consistent methodology across the field.
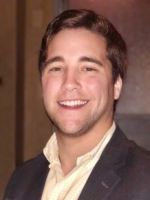
Cole Paxson is a completions engineer for the DJ Basin asset at Anadarko. After graduating from the University of Texas in 2016 with a degree in petroleum engineering, he began work at Anadarko as a production engineer for the Delaware Basin asset. In this role, his responsibilities included well surveillance, workover operations, and serving as the lead engineer for the sand control program. Paxson focused his efforts on developing the equipment standards and operational philosophy required to flow back wells directly to tankless facilities.