In the oil and gas industry, the question “What do you do for a living?” will get you the typical responses: “I’m an engineer.” “I’m a geologist.” “I’m a scientist/physicist.” It is not often that you will hear: “I keep pipelines from blowing up.”
In an industry that is constantly developing upstream technologies to meet the global demand for oil and gas, we rarely shine a spotlight on the transportation of these commodities. Even less glamorous? How the industry ensures “safe” transportation of natural gas and oil from wells to processing plants, storage, and to end users.
The industry downturn and the associated oil glut has helped to highlight the world of pipelines and has allowed engineers entering the market to learn more about the growing field of pipeline integrity management.
For this Discover a Career article, TWA editors interviewed Christian Calvi from G2 Integrated Solutions, a pipeline engineering consulting company. He provides an inside perspective of pipeline integrity management and how the industry views it today.
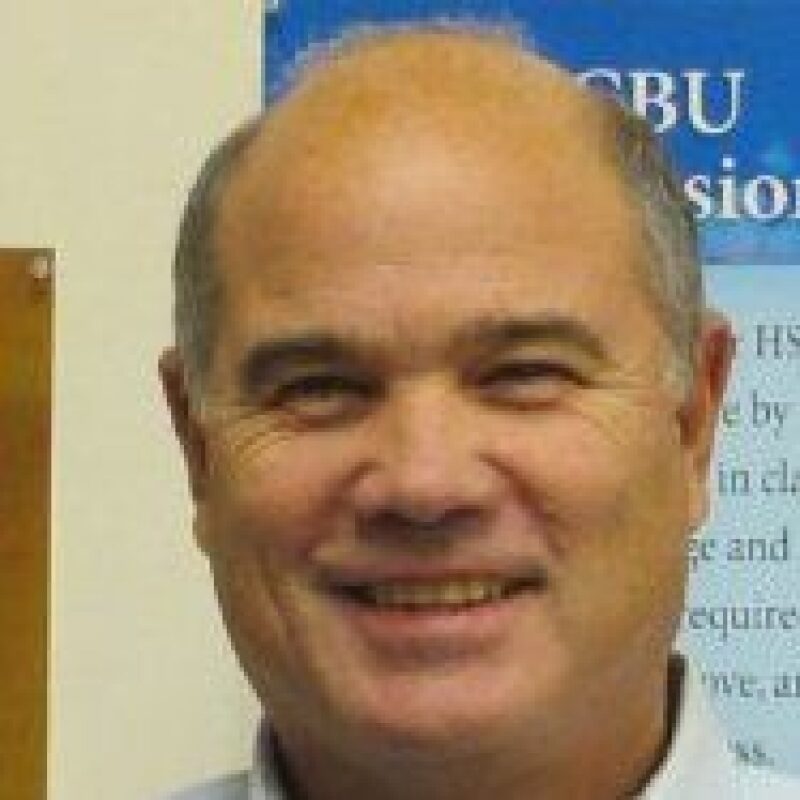
Christian Calvi is a senior management consultant at G2 Integrated Solutions, a pipeline engineering consulting company. For the past 12 years, he has led significant integrity program improvement projects in Indonesia, Canada, and US with special focus on program health, processes, and metrics. He has identified pipelines as a potential risk to companies’ bottom line and the general public and is a coleader in global pipeline integrity improvements. He has several years of experience in the oil and gas sector in engineering, construction, and maintenance roles—from developing production facilities in the Ecuadorian jungles and offshore platforms in Norway and Indonesia to roles in refinery maintenance. Previously, he also worked a 5-year stint in environmental engineering designing cleanup solutions for hazardous waste sites under the US Environmental Protection Agency’s Superfund program in Houston. Calvi holds a BS in civil engineering from Purdue University.
Can you give us an overview of what is pipeline integrity management?
Pipeline integrity management (PIM) is a broad subject and covers everything from achieving at a minimum, regulatory compliance to using integrity programs to drive higher operational reliability, improved safety, and lower costs than the competitors. Operators who have the best PIM programs achieve it by successfully integrating their processes, documentation, program metrics, and organization to achieve higher levels of integrity into a well-functioning system. And they achieve better integrity while spending less over the life of their assets.
To accomplish this, best-in-class operators have dedicated staff that review their pipelines, regulated or not, to anticipate integrity problems, scrutinizing data and analyzing failures when these occur. Most failures come from corrosion, poor construction, poor operating practices, and third-party damage. The focus is to eliminate small problems before they become major headaches, and their integrity programs address these and other issues in detail. And finally they do not rely on the status quo but are continually refining their integrity systems to improve.
How has pipeline integrity management changed over the course of your career?
In the past, some occasional leaks (small) were tolerated but there has been a shift in attitudes. Major incidents in the past 20 years have reinforced this paradigm shift. The full cost impact of a large leak can be very expensive. The consequences of these incidents have been increased regulations and greater focus on cost management, and even societal pressures have driven the fact that leaks are unacceptable. In support of the quest to anticipate problems and eliminate leaks, better tools have been developed to identify sources of leaks (such as smart pigs) and technology is used to identify potential problem areas before any failure. In addition, it is necessary to make an integrity program into an integrity system. This occurs when the integrity system combines all of the elements of the program together—competent people, sound data practices, robust analysis, and program metrics, among others. For PIM programs to improve, the focus on integrity has to be relentless and never-ending. Corrosion never stops and neither should PIM programs.
Are there differences between onshore and offshore pipeline integrity management processes? And if so, can you describe the differences?
Yes and no. The onshore and offshore are regulated by different jurisdictional entities with different rules but the pipelines are mostly subject to the same challenges—internal and external corrosion, construction issues, operational practices, and third-party damage. Offshore, pipelines are also subject to being uncovered by scour and movement by currents and can be subject to damage by boat anchors, fishing nets, and other damage mechanisms. However, attention to the details usually enables operators to successfully and profitably move large quantities of gas and liquids at significantly lower costs than their competitors.
What technologies are available today that help to assess pipeline integrity?
The smart pig revolution has changed significantly how we can assess the pipeline condition and take proactive measures. In one instance, my team found a line that had not been previously assessed and a pigging plan was developed. It was a 12-in. pipe carrying methane with a high concentration of hydrogen sulfide (H2S) into a H2S removal unit, and the methane gas was compressed and sold. The existing line was heavily corroded and any release would go into the nearby town and cause significant health problems for the population. Although the plant was to be shut down during the pipeline replacement, resulting in a loss of revenue, management understood the impact and immediately approved a replacement project, which was successfully completed with no adverse impact on the population.
In addition, pipeline materials have improved significantly. Recently, I was shown a piece of pipe that was used to carry gas to light the street lamps in a town in west Texas around 1920. The pipe section was an ax-hewn block of wood that had been bored out to carry gas and it fit in the adjoining piece with a beveled end. The gas in those days was very wet and the water that was transported within the pipeline probably made the wood swell and close the gaps so it would not leak too much. That wood pipeline was replaced with cast iron pipeline some years later. Today pipelines are made of high-strength and special steels for significant pressures and corrosive environments. In some cases, special plastics are used where the corrosion is severe in low-pressure situations.
What are some current industry challenges that affect managing the integrity of pipelines?
The main challenges are threefold. The first is the major personnel changeover that is occurring within many operating companies and engineering and construction companies with the corresponding loss of experience. Unfortunately, with the departure of these industry veterans, some of the mistakes of the past will happen again as many of the lessons learned the hard way will have to be relearned. Secondly, most pipelines in the US were built prior to 1970, and with the advanced age comes more corrosion and degradation issues. And lastly, the documentation systems for many operators are still fragmented whereby the relevant pipeline information is in both digital and hardcopy format. This fragmentation impedes the ability to rapidly manage pipelines with fully integrated documentation systems and in retrieving the right information needed for the best analysis and decision making.
How does integrity management of pipelines differ among the sectors of the oil and gas industry?
In the US, there are regulated pipelines and unregulated pipelines which means that the regulatory programs for each are different. However, ongoing age degradation and corrosion have an impact on all pipelines and components, whether these are regulated or not. The key is to have the right integrity management program for each pipeline, but the difficulty is getting that program right. An integrity plan that is tailored for a pipeline carrying gas across west Texas will be different from the program for an oil pipeline in coastal Louisiana marshes.
What are some crucial components of a well-rounded pipeline integrity management system?
A well-rounded PIM plan has a defined and written integrity program, which includes defined integrity goals, sound written processes and procedures (covering design, construction, operations, maintenance, and removal from service), change management, risk analysis, documentation systems, emergency management protocols, external audits to gauge the program itself, and defined metrics to judge the program efficiency and efficacy. It is supported by management with a defined budget to meet the integrity goals.
Why is pipeline integrity management an ongoing task for owners of pipelines?
Pipelines are subject to ongoing changes throughout their operating life due to aging and the PIM must adapt to those changes. There are changes in tools, procedures, operating conditions (temperature, flow rates, flow directions, pressures, and composition of the medium transported), weather (storms, hurricanes, and floods), development (new construction next to the pipeline), new construction going over the pipeline exposing it to third-party damage, etc. And as mentioned before, corrosion never stops. We attempt to slow it down for the life of the pipeline; most of the times we are successful.
Are there any current regulations that are driving pipeline integrity management?
The regulations are always slightly changing and becoming more stringent. However, a good integrity program usually exceeds the minimum requirements of regulations by quite a margin. Not only are these top-of-the-line programs cost-effective, they can be leveraged for additional revenue. For example, we were faced with an opportunity to transport the gas for another operator for additional revenue during one of their unplanned outages and our pipeline had spare capacity. The other operator did not have a robust PIM program and we did. To summarize, best-in-class operators review the regulatory requirements in order to assure themselves of meeting the regulations but then find ways to leverage that compliance in order to be cost-effective. This does not happen by accident.