In North America, midstream companies have a long and successful history of building and operating crude oil transportation infrastructure. Midstream operators serve as the storage and transportation conduit between the upstream and downstream sectors, safely and efficiently connecting the supply of crude oil with refineries. This transportation solution may entail new construction or a build-out of additional infrastructure within an existing facility. New midstream infrastructure enables efficient market access by providing increased capacities to the refineries.
The primary modes of transporting crude oil across the continent include pipelines, rail, and road. However, based on comparisons of transportation records, pipelines are considered by far to be the safest option. An analysis of data from 2005 to 2009 shows that pipelines had approximately three times lower incidents per billion ton miles than that of rail and 34 times lower than road (Furchtgott-Roth 2013).
TransCanada is one of the leading midstream energy companies in North America. The company has a strong focus on pipeline transportation with some 90,300 km (56,100 miles) of natural gas pipelines, and liquids pipelines totaling an additional 4,920 km (3,060 miles). The liquids portfolio includes the 4,247-km (2,639-mile) Keystone Pipeline system, which also includes crude oil terminals at Hardisty, Alberta, Canada; Cushing, Oklahoma; and Houston. The initial phases of this system have a capacity of 590,000 B/D and transport approximately 20% of Western Canada Sedimentary Basin crude oil exports. The crude is shipped to key refineries in the US, where it is processed into gasoline and other petroleum products. Since it began operations in June 2010, the Keystone Pipeline system has safely transported more than 1.3 billion bbl of Canadian and US crude oil to US markets in the Midwest and Gulf Coast regions.
For midstream companies to gain a competitive advantage, it is necessary to apply cost-effective strategies for the reliable transportation of crude oil while ensuring public safety and minimizing the impact of operations on the environment. Due to the physical and chemical composition of hydrocarbons, their storage and transportation require sophisticated infrastructure that integrates science and innovative technology.
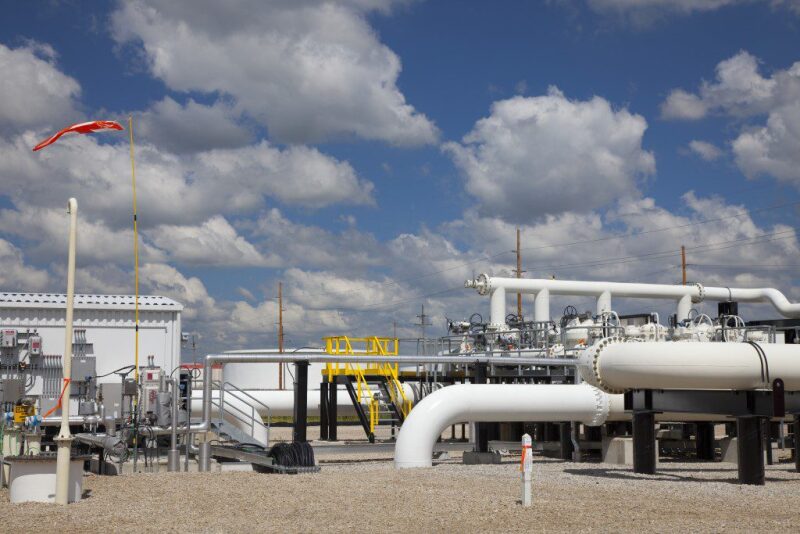
Pipeline Technology Innovations
To maximize the value of its midstream operations, TransCanada uses advanced technology in its new and existing projects. The company maintains an active innovation and technology program in regards to research and development. To illustrate the huge amount of innovation in the midstream sector, some recent key developments in midstream technology will be discussed in depth.
Sunk Costs, Literally
The Keystone crude oil pipeline reused a portion of TransCanada’s existing Canadian Mainline natural gas pipeline. This project involved the conversion of 864 km (536 miles) of installed pipeline, mainline valves, and right of way corridors that were repurposed to oil service in lieu of using new construction materials. This conversion helped to safely advance the project’s schedule, save on the cost of new materials, and at the same time, reduce the project’s environmental footprint.
Trenchless Construction
Another example of innovation is horizontal directional drilling (HDD), a trenchless construction technique that enables the installation of pipelines at crossings to avoid congested, urbanized, or environmentally sensitive areas. This technique was used during the construction of the 36-inch Houston Lateral Pipeline for roughly one-third of its route.
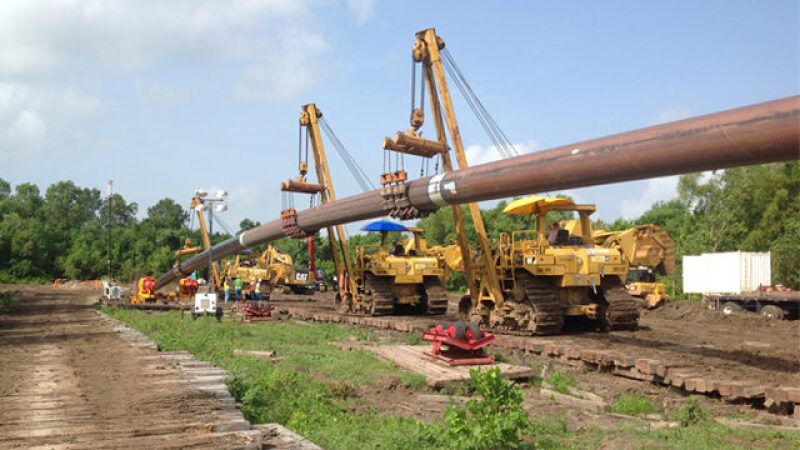
Reducing Viscosity and Improving Efficiency
The Northern Courier Pipeline (NCP) Project currently under construction is not a typical 24-inch pipeline (see picture on top of the article). It will transport heated bitumen at 140°C (300°F) from the Fort Hills oil sands mine to the East Tank farm, which is situated approximately 30 km (18 miles) north of the town of Fort McMurray, Alberta. The pipeline will not use the typical corrosion-resistant fusion bond epoxy coating. Instead, in order to safely transport the product at this temperature, the pipeline will be insulated with 3-in. of polyurethane foam and protected by a ¼-inch polyethylene jacket. The operations control center will receive continual updates on the integrity of the insulation system via four moisture detection wires located within the foam and running the length of the pipeline.
Using a heated bitumen pipeline significantly increases the amount of heat integration and reduces the number of associated upstream and downstream facilities required to process the product. A conventional nonheated bitumen pipeline would require the upstream producer to install heat exchangers for cooling prior to the pipeline, and diluent blending facilities to assist with product mobility. On the downstream side, an upgrading facility would be required to separate the diluent used to enable the viscous oil to flow, and then reheat the bitumen for processing.
This heated bitumen pipeline will be completed during frozen ground conditions due to the swampy nature of the muskeg terrain it is built on. Through the implementation of these concepts, TransCanada and its client Fort Hills are achieving operating efficiencies and reducing their project footprint.
Continuous Welding Innovation
Mechanized welding is TransCanada’s standard practice on large-diameter pipeline construction. The method has seen increased implementation on cross-country pipelines across North America. The company has developed and implemented a number of key production welding, inspection, and weld assessment technologies to improve quality performance and productivity on cross-country pipeline construction. Technologies to complement mechanized welding include automated ultrasonic testing and alternative weld acceptance standards. It is estimated that the cost of alignment, welding, nondestructive testing, and weld coating can be reduced by about 25%, which result in savings of total pipeline capital expenditures of approximately 5%.
Inspecting the Inspection Forms
Inspection forms are used to record critical information during pipeline construction, such as details on welding and coating. Traditionally, this is achieved by filling out forms by hand and then scanning the forms for electronic record keeping. This approach results in project documents that are difficult to search through as the forms are generally scanned images and are not text searchable. In order to improve on this system, TransCanada and a contractor developed a program to capture real-time information during construction of the Houston Lateral Pipeline project. This was achieved by using inspection templates preloaded on an iPad and filled out by inspectors. Once the inspector submits the form, data are transferred to a database where they are automatically analyzed based on predefined parameters. Any data inconsistencies or values outside a predefined range are instantly flagged to engineering and construction staff. Similar databases have also been used during operations to reduce the amount of time to electronically search for inspection information.
Conclusion
Technology development and innovation applied in a safe and environmentally responsible manner will continue to ensure that midstream operators in North America build on their successful history of the development and operation of critical energy infrastructure projects. This will ensure that refineries have access to a crude oil supply that is readily available, and can be safely delivered. This will in turn mitigate disruptions in the refining of petroleum products for consumers’ daily needs.
Reference
Furchtgott-Roth, D. 2013. Pipelines are Safest for Transportation of Oil and Gas. Issue Brief No. 23. June. Manhattan Institute for Policy Research.