Case studies from around the world prove that big rewards await companies that optimize the artificial lift systems keeping their mature fields alive. The success stories involve a mix of monitoring, automation, and performance tracking. Through upfront sacrifices of time and money, companies that have taken the initiative are now enjoying the benefits of better production and reduced operation costs.
For Australian production company Santos, the off-the-shelf technologies it adopted for mature fields went from “nice to have” to “must have” after its operating costs on more than 200 wells were dramatically reduced. Such improvements are even more important amid today’s low oil prices.
“Your dollars per barrel is only going one direction right now, so we need to be smart about it,” said Blair Gardner, a production optimization engineer at Santos, who led the effort to automate his company’s lift systems.
On a grander scale, the world’s largest supermajor, ExxonMobil, overhauled its artificial lift operations on approximately 1,000 oil wells in Africa with monitoring and automation systems and gained 10,000 B/D in added production.
But by and large, these are the exceptions. Some industry experts say the status quo remains that in most mature fields, lift systems break down long before reaching the end of their expected run life. Shauna Noonan, completion technology manager and artificial lift expert at ConocoPhillips, said the technology is not to blame.
“To make a long story short, when it gets to mature fields, it is not the fact that the lift systems will not work. It is that we really need them to be reliable,” she said. “If you want the reliability, you have to be willing to pay for it and put the time into it.”
Of all the factors involved with the problem, Noonan said most of the time it comes down to a preventable human error, which she explained might be made by the manufacturer, distributor, installation crew, or the operator.
Sometimes the lift systems are not designed for the environment they are used in. But more often, companies are knowingly running the systems out of their operating range. This is usually done when there is pressure on engineers to increase production by speeding the pumps up. “When we do that, let us not pretend to be so surprised that the system will fail 6 months later,” said Noonan.
Bill Lane, the vice president of emerging technologies for Weatherford Artificial Lift Systems, characterized the industry’s shortcomings in this area as a “chronic condition.” He said the prevailing focus of most operators has been on their greenfield projects, leaving much room for improvement in how they run their older assets.
“You have a field that has been producing for years, and it is not the most exciting property you have or the most challenging,” he said. “So we tend to put our most inexperienced people on it as a training opportunity, and yet that is the field that is really the cash cow that is funding everything else we do.”
One of the negative outcomes of this general practice is increased maintenance costs on equipment because companies commonly wait until a lift system fails before they do anything about it. In the worst cases, the repair and operating expenses become high enough that companies begin thinking about shutting the field down.
Downsides of the Downturn
Noonan said the recent swing in oil prices is highly likely to play a role in how lift systems in mature fields will perform over the next 2 years. When the price was considerably higher, she said operators focused on ramping up production as much as possible. As a result, they shortened the run life of many lift units.
The scenario Noonan predicts that will play out when those pumps eventually fail is something of a cycle of doom as the burden of making up for lost production will be placed on the lift systems left working. “It happens all the time,” she said.
And in the mature fields where the upkeep of lift systems was prioritized, the outlook is also turning gloomy. “When we are in a cost-cutting mode, which is what everyone is going to be doing this year, one of the very first programs to get cut is equipment maintenance,” Noonan explained. “We may not start seeing failures now because everybody was probably maintaining them last year. But starting next year, we could start to see our artificial lift failure rate go up because we cut the maintenance schedule back in 2015.”
Francisco Alhanati, managing director of C-FER Technologies, an engineering firm that tracks the performance of artificial lift systems, had similar cautions for mature field operators during these uneasy times. “With USD 100 oil, you can do a lot of things wrong and still get away with it,” he said. “At a much reduced oil price, you have to optimize your operations and your profit, or you may be out of business. It is as simple as that.”
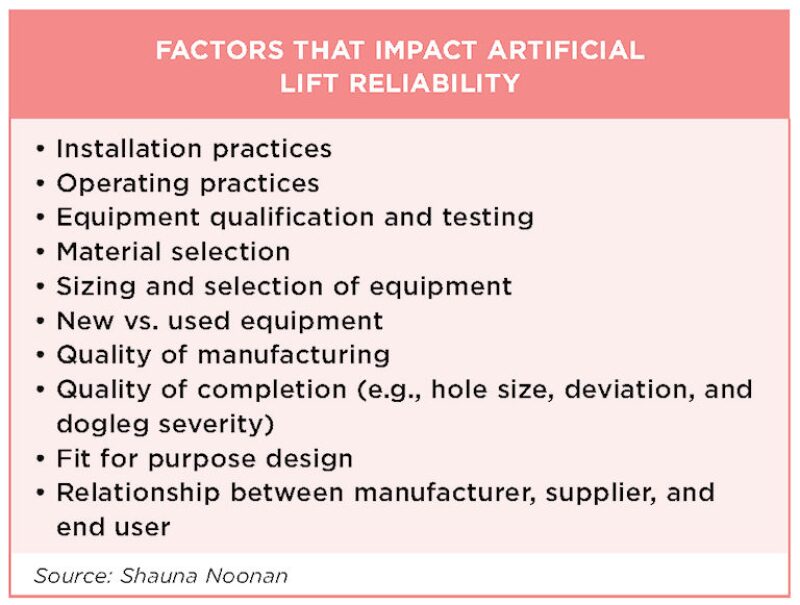
Decisions, Decisions
Since the late 1990s, C-FER has been running two joint industry projects that provide operators with a tool to track the reliability of the progressing cavity pump and electrical submersible pump systems, and forecast well workover rates. The effort has involved building a database of tens of thousands of artificial lift run-life performance records that allows operators to learn from others working in fields with similar conditions as theirs.
Alhanati said the data clearly shows that the industry is learning how to improve the reliability of lift systems, albeit slower than what many would like to see. “If you know what is achievable, and you are not the best in your class, there is an opportunity there to improve,” he said. “And if you do not have that information, you never know what is possible.”
In short, operators who have access to the database are able to make better choices, and in a mature field, there are many to be made. One of the most important and obvious is how much capital to invest in the lift equipment. However, Alhanati said he believes that companies place too much emphasis on the expenditure aspect of their operations and, much of the time, that leads to recycling parts instead of buying new ones.
“If you try to reuse a lot of equipment, you have to really be careful because you may be shooting yourself in the foot,” he warned. The problem with recycled parts is that they may result in a shorter run life, leading to higher workover costs and production losses.
And generally speaking, as time goes by, mature fields produce more and more water and gas. It is a perpetually vexing issue for operators ultimately seeking oil. “What do people then try to do? They try to get the most production they can from each well, which means pushing the limits,” Alhanati said. A typical example is pumping the well with as low of a downhole pressure as possible and, without close monitoring, the pump will soon operate in a dry condition or the equipment will become overloaded, which will eventually cause a failure.
Another decision many operators are faced with in aging fields where water and gas rates are increasing is how to handle corrosion and scale. The chemicals used in mitigating these problems are not cheap, and neither are the operations required to deploy them. If companies invest in a chemical program, they can hold off failures, or they avoid the associated costs and accept premature breakdowns. Alhanati said the right decision comes down to economics.
If paying for workovers and replacements is cheaper than paying for a chemical treatment program, then companies will be better off with a shorter run life on their lift systems. “It is all about achieving a balance,” he said. “Your objective is to make a profit. Not necessarily to produce the most you can from the well or minimize the number of failures.”
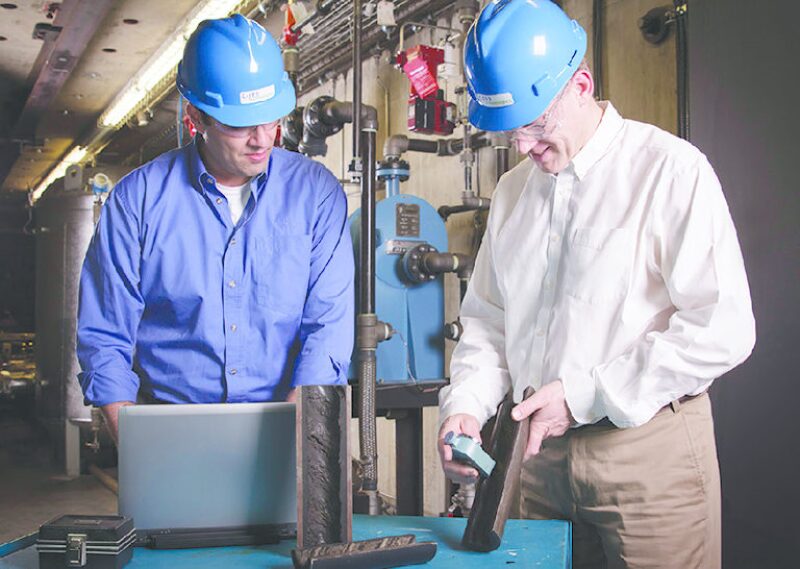
Monitoring the Situation
Lane said Weatherford has worked with clients in mature fields where minimal investments in basic monitoring and surveillance equipment reaped significant savings. Despite the positive results, this practice is not exactly catching on like wildfire. “I think there is a definite trend towards monitoring,” he said, but largely in new developments. In mature fields, he said, “That is where [operators] do not want to spend the money to put monitoring systems in place.”
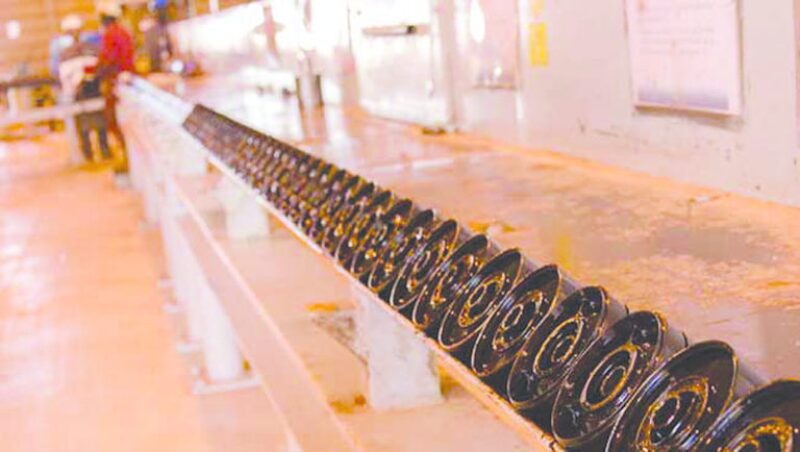
He estimated that 30 years ago, less than 10% of the world’s wells used monitoring systems compared with today whereby Weatherford alone has installed optimization software in more than 480,000 wells. Lane said that figure represents somewhere between a quarter to a third of all wells in operation.
To his point, Lane described a case study in which a customer reduced its repair rate of lift systems with monitoring technology in a mature field by 50%. The incentive for the company was to reduce its intervention rate, which had increased from about one per well each year to two per well each year.
After having a taste of success, the company then installed Weatherford-developed software to track failures and organize its maintenance services. “The result was that their repair rate was almost cut in half again,” Lane said, noting that the annual savings for the field amounted to almost USD 6 million a year. “A lot of this is not really that complicated. As with any problem, if you can see what is happening, then the solutions are quite obvious,” he said.
Slow and Steady
When companies run lift systems too fast, they break down more frequently. But when companies optimize the speed of the pumps, they tend to live long and prosper. ExxonMobil was faced with replacing an electrical submersible pump nearly every day in a 1,000-well field in Chad. As a consequence, production capacity in many wells had dropped by 80% only a couple of years after going on pump. So the company decided to conduct a thorough review of its operations and in the end realized an improvement in mean time before pump failure from an average of 2 years to 10 years which resulted in an additional 10,000 BOPD.

Part of the success was achieved through the installation of variable speed drives (VSDs) to slow down the pumping rates and the coupling of that technology with a stronger surveillance program to identify which wells needed to have pumping rates adjusted. Another key improvement was to simply stop flicking the on-and-off switch.
“Things will last longer if you develop strategies that just leave them running longer without interrupting them so much,” said Robert Tester, a senior reservoir simulation consultant at ExxonMobil. “We have areas of the world where we have pumps that are lasting 20 years. But the key to those operations is that they have maybe been turned off a couple of times in 20 years. They have redundant power supplies, and are set up to run smoothly for a very long time.”
Once the new monitoring technology was installed, the company also learned that it would need 1,000 interventions per year compared with the 200 it previously expected. While increasing the number of intervention jobs by fivefold, the company actually drove down costs by 50%. The assembly line intervention process created an economy of scale for the required equipment and minimized the downtime of the service teams.
Tester said probably the highest tech aspect of all the improvements came from lessons ExxonMobil had learned elsewhere using data analytics. He said this technology allows operation engineers to effectively “triage” the pumping issues and focus on the most important problems.
“There was no technical rocket science here,” he said. “Rather, it was more about having the production surveillance people working closely with the operations people so that when problems were detected, they were able to get on them and work them before they became very large problems.”
Today, when the field’s operation engineers sit at their desk each morning, instead of poring over a performance report of hundreds of wells, the software program only flags the ones that are behaving differently. “That is a much smaller scope for them to look at,” Tester said. “The manual process of looking at the daily production from 500 wells or so takes a significant amount of time.”
Patience Required
In a mature field where there may be more than a hundred wells on pump, solving a systemic problem can take years. Noonan advises that companies heed this and be realistic in what they can accomplish in a given period of time.
If a company is seeking to double the average run life of a fleet of lift systems from 1 year to 2 years by replacing them all with new ones, Noonan said the goal would not be reached for 3 or more years. Pragmatism dictates the replacement of a working pump only after it failed. As such, it would take a year or more to replace each pump in a large field followed by 2 more years to verify that the goal was achieved.
“And when people say they want to go from a 2-year to a 5-year run life, that is going to take you almost 10 years to really see if you achieved your goal or not,” she said. “In most cases, people are not willing to wait that long.
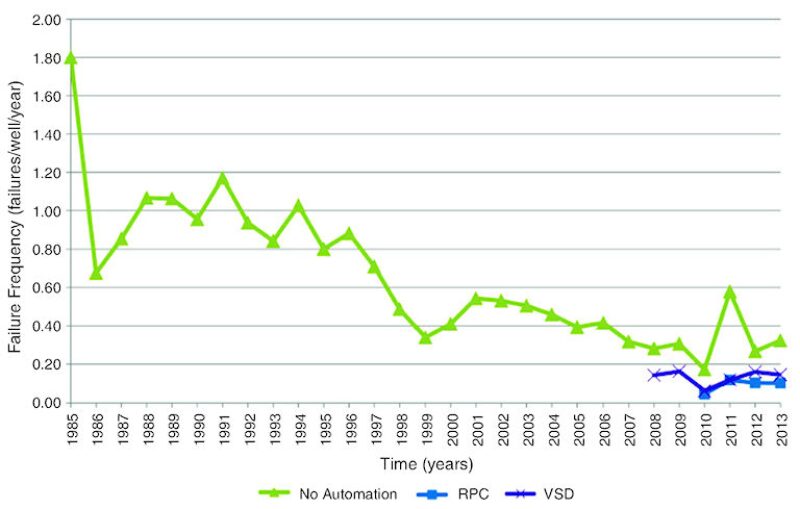
Automation Journey
Patience paid off for Santos. In 2007, the company realized the beam pumps used on nearly 150 oil wells in the Cooper Basin were failing before their expected run life. To turn the tide, Gardner said he and other engineers embarked upon an “automation journey.”
“We had a beam pump population making money but [for some wells] it was marginal,” he said. “If we could spend money to install technology that could extend run life and increase oil production, then it was a win for us.”
The primary objective was cost reduction since procuring replacement parts and equipment Down Under can be more costly than in most other areas of the world. Gardner said other financial challenges included high labor and service costs for the remote operations in the country’s eastern desert. Because of this, response times were sometimes long when pump failures occurred. And as the fields, which came on stream in 1984, grew older, the new oil wells were increasingly drilled in more remote locations.
To convince managers that the retrofitting of an entire artificial lift fleet with automation and monitoring technology would pay dividends, the optimization team staged the project in multiple campaigns. As the incremental benefits were seen, Gardner said management gave the green light to roll out the project across the entire operation.
“No one likes to spend additional Capex on existing wells and we were aware that we were fighting a battle there,” he said. “But ever since we made the switch over to automation, those systems really have experienced a step change and considerable improvement in failure frequency.”
The technologies that the company invested in included VSDs for the higher-rate and new wells, and rod pump controllers (RPCs) for the lower-rate wells. The VSDs cost more but offered optimum performance over the RPCs, which is a shutdown device that prevents the pump from essentially pounding itself to death. Gardner said the VSDs had the benefit of being a “set and forget” technology, but the initial RPC installations revealed that almost half of the installation base was failing because of fluid pounding. The lesson learned, and later applied to the nonautomated wells, was to pump at a lower speed.
When the project began, the field had 145 oil wells on pump with no automation and over 50 lift systems were failing each year. By last year, there were an additional 90 new wells and the average failure rate of wells using VSDs or RPCs dropped by 70%. Of 237 wells, 99 used RPCs, 104 had VSDs installed, and only 34 wells were left operating with no automation systems at all.
The project also included building the company’s first failure database with more than 2,000 historical records. This allowed the engineers to hone in on the root causes of the failures. “We all thought that the rod string parts and tubing leaks were our biggest issue. By installing automation, that effectively reduced those failure categories and then brought pump failure to the top of the list,” said Gardner.
The next step for Santos is to carry out a post-mortem examination of the failed pumps by boxing them up and sending them back to the vendor for a complete teardown. Until the recent automation effort, when a pump failed, it was simply pulled out of the ground, thrown away, and a new pump was installed.
For Further Reading
SPE 171372 Reliability Improvement in Beam Pumps by use of a Unique Methodology Combining Real-Time Automation and Failure Analysis by Blair Gardner, Santos.
SPE 148333 ESP Failures: Can We Talk the Same Language by F.J.S. Alhanati, C-FER Technologies.
SPE 165432 Got Steam? Understanding ESP Steam-Handling Capabilities in Centrifugal Pump by Shauna Noonan, ConocoPhillips, et al.