To state the obvious, it’s been a turbulent 2020 for the oil and gas industry. We’ve come up against continued weakness in commodity pricing, reductions in capex and opex by virtually all operating companies, and frequent demonization by the popular media. In addition, the outbreak of the coronavirus effectively brought the global economy to its knees. Though it seems grim, I can say with confidence that the industry will overcome these challenges, as it always does. What we do—our critical mission of providing the world with abundant, low-cost energy—is here to stay.
What we can, and must, do, however, is change the way we look at drilling and completing wells. Much has been said on this topic, which I’ll reiterate: We need collaboration between and integration of the drilling and completions disciplines, such that drilling better wells primed for completion activities becomes the norm. For some time, drilling faster has been a driving performance metric: If we can just increase rate of penetration, just drill that well one day or one hour or one minute ahead of schedule, then we’ve succeeded. This approach saw benefits in its early stages as the time to drill wells fell dramatically. As we’ve gone to complete those wells, however, it’s been apparent that many are not high quality; they’re riddled with tortuous sections and other problems that ultimately decrease production and cost millions of dollars. To this we must say, “enough is enough.” Simply talking about drilling better wells isn’t an option—we must act.
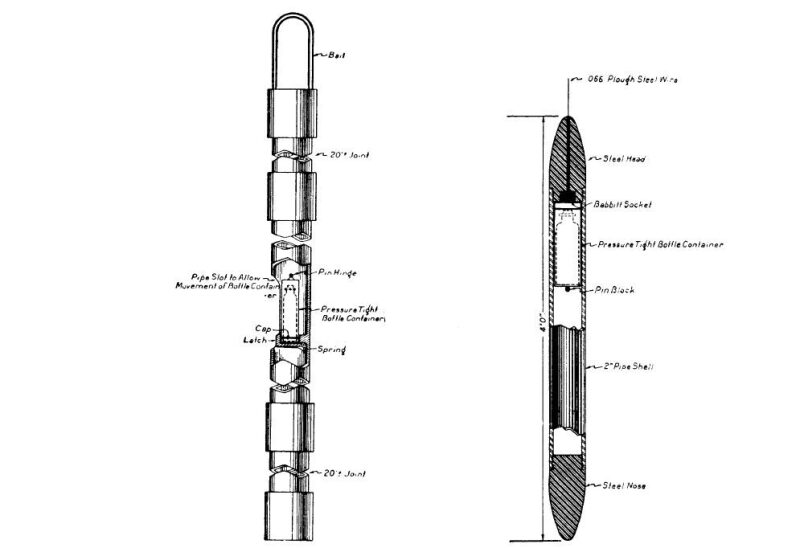
Fig. 1—In this image, taken from a technical paper written in 1929, acid-bottle surveying instruments are shown. At left is the instrument for running through casing; at right, the version for running through a 6-in. drillpipe. One of the earliest methods of subsurface well surveying, the procedure involved filling a bottle half-full of acid, placing it in the instrument, and lowering it to the desired depth for approximately 10 minutes. Upon retrieving it to surface, the acid etching on the bottle indicated the angle of inclination. Source.
Wellbore placement accuracy is a topic relevant to anyone in the directional drilling field and, by extension, anyone in completions. When the industry used acid bottle surveys to obtain simple information on well inclination (Fig. 1), gyroscopic surveying represented something of a quantum leap in making better wells possible. Evolution in gyro surveying technology through the years has yielded smaller and smaller systems and sensors (Fig. 2) that are more accurate and more precise than their predecessors. It’s clear we should consider wellbore placement as a cardinal performance metric. If a well is accurately placed in a hydrocarbon production zone the first time, there is less risk to personnel, less impact to the environment, and of course, a better return over the life of the well for the operator. This can be difficult to prove, especially in the offshore environment, as reservoir life can stretch on for 10 or 20 years. Data take a long time to collect and analyze, but think of it this way: If a well is placed with pinpoint precision right into a high-yield reservoir zone vs. outside or on the fringe of uncertainty, the recovery factor is improved. Imagine getting even 1% more production out of an offshore well over the life of the project; the impact would be huge. And in cases where we’re using an electrical submersible pump or rod pump, we can ensure that the production equipment is placed right where it needs to be in the well, not in highly tortuous zones due to lack of information—another benefit of running a gyro survey paired with wellbore tortuosity logging technology, which provides insight into microdoglegs in the wellbore at 1-ft intervals.
Fig. 2—As gyros evolved, their design and size have changed. In this picture, taken in 2014, a penny is placed on top of two gyro sensors to show scale. Earlier gyros were much larger, and previous surveying methods required additional equipment. Source: Gyrodata.
New drills are typically steered away from existing wells to quickly eliminate magnetic interference at surface, which causes high-side loads. High tortuosity in shallow sections can cause wear issues in surface casing and cut a well’s total depth (TD) short. If gyros are utilized for longer sections, they can move away at a slower pace, thus decreasing wellbore tortuosity. This would make the production engineer’s life much easier. Using dual gyroscopic sensors allows for smaller ellipses of uncertainty, which is helpful when wellbore collision is a significant concern.
An ellipse of uncertainty models the uncertainty around the wellbore trajectory where the lateral dimension is proportional to the azimuth error and the high-side dimension is proportional to the inclination error. By decreasing the ellipse of uncertainty in directional wells, operators can mitigate the risk of wellbore collision. This is especially critical in multizone developments, pad-drilling applications, and other areas where tight well spacing makes it a challenge to successfully navigating a crowded field (Fig. 3). Accurate well spacing can vastly improve a well’s recovery factor, leaving less oil behind and improving the overall economics of a field.
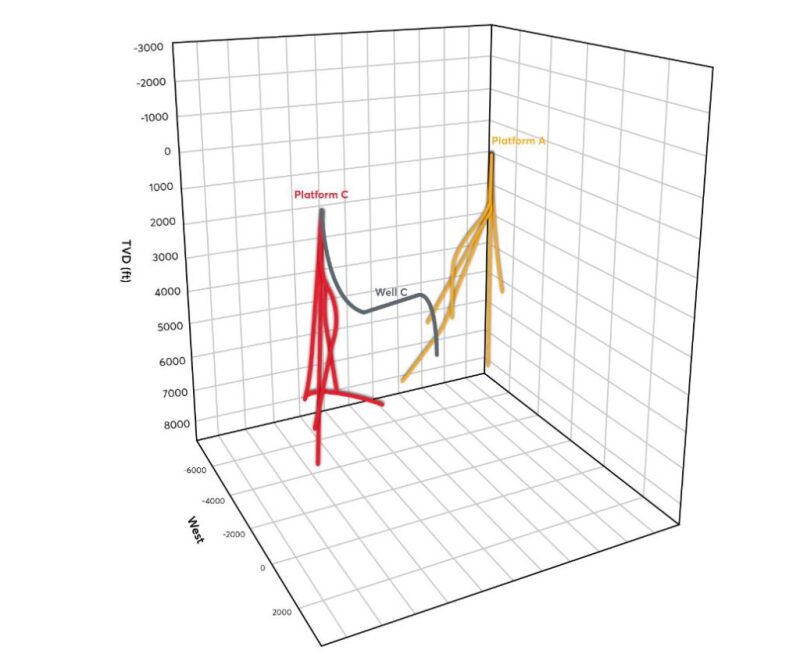
Fig. 3—A 3D view of a crowded field in the Gulf of Thailand. Mubadala Petroleum needed to drill a well in a complex oilfield containing multiple stacked sand reservoirs, largely comprising individual oil and gas water contacts.
One of the major challenges associated with the field was accessing the remaining bypassed oil, highlighting the criticality of wellbore placement. The aging wells were drilled very closely together, making wellbore collision a significant concern. The new well had to be drilled from a second platform due to slot limitations on the first platform. To accomplish drilling the fragile wellbore in a congested area, the new well required an S-shaped trajectory with a long tangent section at an inclination of 78°. Source: Gyrodata.
Another concern is that magnetic anomalies, left unchecked, can lead to wells moving over lease lines. Without accurate survey information, protecting the adjacent lease-holder’s interest becomes increasingly difficult. You may recall that Shell drilled what has now been dubbed the “horseshoe well”—which had a 180° turn that created two lateral sections at more than 11,000 ft—in the Permian. As reported in JPT, “One reason Shell was drilling 5,000-ft laterals in this area of the Permian is because of lease restrictions—an issue particular to the US shale sector whose acreage maps are often dictated by private land ownership and contract terms. This constraint is not unique—there are many so-called 'square-mile leases' in the US—highlighting that the first horseshoe well might not be the last.” Operators are getting more creative when it comes to making sure that they don’t intrude upon a lease line, lest they face operational and financial issues. As such, putting the well in the right place the first time with a high-accuracy gyroscopic wellbore survey should be a priority for all parties involved.
Well Placement—A Critical Skill for YPs
When we think of today’s young professionals, there is still a great deal of division and segmentation in their functional disciplines, the genesis of which lies at the university. If you’re planning to be, say, a drilling engineer, the ultimate location of the well probably isn’t first on your list; what “is” first is achieving TD with as few problems as possible in the shortest amount of time. When you save your company money, you look good. Your skills as a driller who can finish that well efficiently will help you advance in your career.
Or will they? When we’re looking at a world where sustained commodity prices don’t look like they’ll exceed USD $50/bbl any time soon, we’re also looking at a world where operators need to adapt. They’ll need people who will not only help them drill those wells faster—a task which has become significantly easier as companies across the operating and oilfield services (OFS) spectrum innovate with new technologies—but also those who can ensure that the wells meet financial goals in production. This industry, whether we like it or not, is in a period of contraction. It’s time for each of us to think more critically about how we can use our talents in cross-discipline applications to derive the most value for our employers.
We don’t have an easy road ahead of us. It takes time and perseverance to transform the way we approach business, particularly in oil and gas where we’re typically slow to adapt and averse to sweeping change. Acknowledging these issues and moving toward a solution is the first step, and whether it’s in conversations with operators, other OFS companies, or even regulatory bodies, we should strive for the better well, not the faster well. In the March 2020 guest editorial in JPT, John Clegg of Weatherford asked the industry, What Do We Want From Our Wells: Drilled Fast, or Drilled Right? We’ve addressed many of the safety concerns on the rigsite and continue to innovate with equipment and technology that works better, in harsher environments, with fewer people in harm’s way. Now, we must take the next step and drill better wells that might cost a little more up front but will prove more valuable in the long run.