Early in its development, the Cline shale was hyped as the next Eagle Ford or Bakken with more oil and gas than they have combined.
The lofty projections of the Cline shale’s potential, located in west Texas on the eastern side of the Permian Basin, were extrapolated from information presented by Devon Energy to financial analysts in April 2012.
At that time, the company’s data regarding the emerging play suggested the possibility that as much as 3.6 billion BOE lie trapped within Devon’s 500,000 acres of Cline shale. Analysts looking for North America’s next major unconventional resource then calculated that the entire formation, roughly 140 miles long and 70 miles wide, held between 30 and 35 billion BOE, which would make it one of the largest discoveries in the world.
That hasty estimate did not take into account how much of the potentially mammoth resource could be economically recoverable. Devon said it is not far enough along in its Cline shale operations to share information.
Other operators in the Cline have encountered issues that make producing from the formation a challenge, such as heavy-clay content, and as a result, the production quality is not consistent across the play.
“There was a lot of optimism up front,” said Benjamin Shattuck, an upstream analyst at Wood Mackenzie in Houston. He said that the variability in initial production rates among the handful of operators drilling horizontal wells in the Cline has revealed the best acreage to be in the west Texas counties of Glasscock and along the western side of Sterling. “That doesn’t mean that there have not been decent results outside of that area,” Shattuck said, “but I think some of the excitement has been tempered a little bit.”
Tempered perhaps, but not all the way gone. The operators with early success in the Cline and even those facing setbacks are moving forward on their investments in drilling the shale and building up the infrastructure needed to support field development for years to come (Table 1). What remains to be determined is whether the Cline will be a uniform and commercially competitive formation across the vast area that it encompasses, or be limited to small pockets in which the shale is conducive to production.
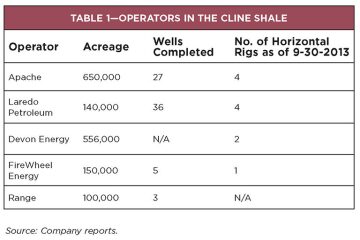
Three-Finger Black Shale
Before it came to be known as the Cline, the nickname for the formation was the “Three-Finger Black Shale” because of its rich darkness seen in core samples, and the distinctive resistivity peaks identifying its location during vertical well logging (Fig. 1). Operators have drilled more than 1,500 vertical wells through the formation in the past several years. The vertical drilling programs provided oil companies with the geological and petrophysical data that they are using today to understand and successfully deplete the formation of hydrocarbons by drilling into it horizontally.
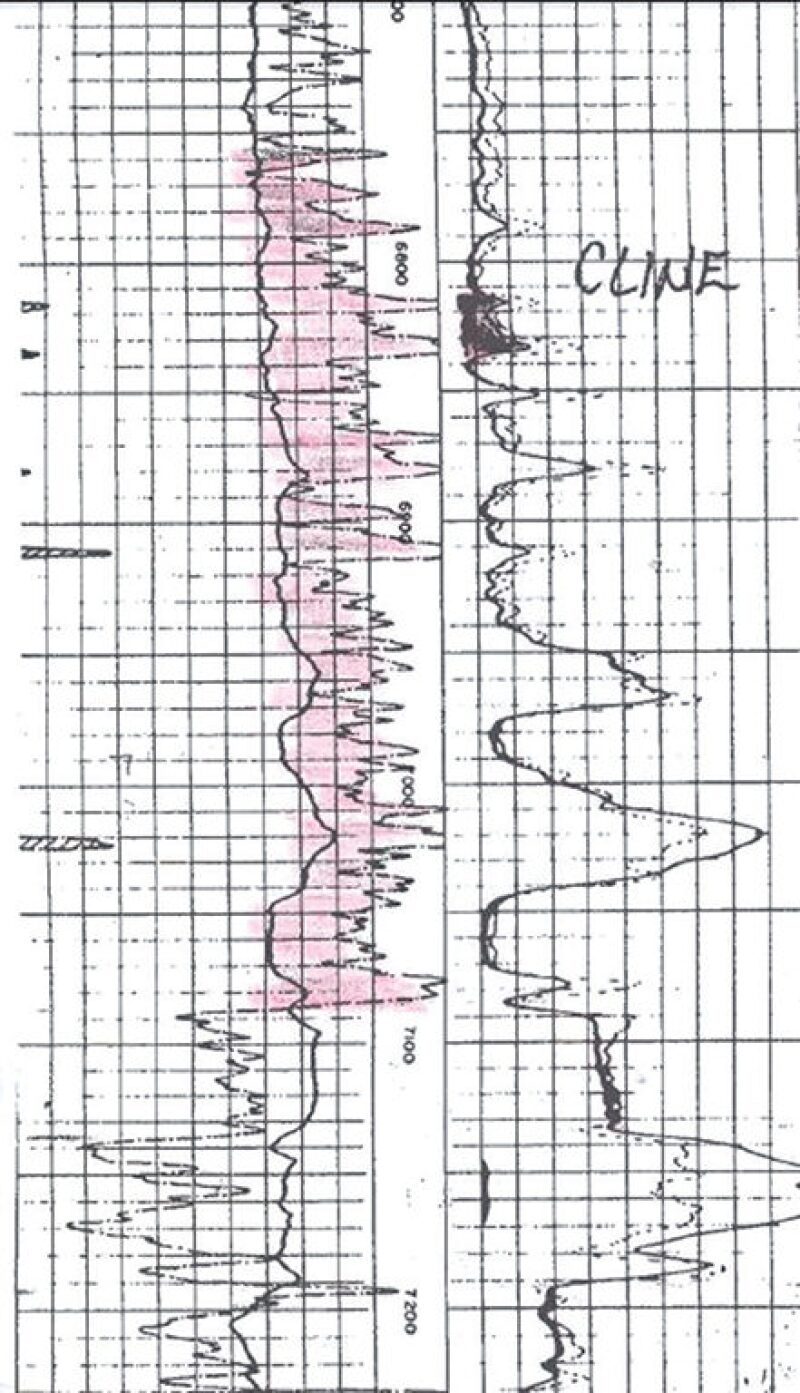
Located in the central Midland basin, the Cline extends eastward until it runs onto the Eastern Shelf. During its depositional period, or time of formation, the sediment and organic material that makes up the Cline flowed down the Eastern Shelf and settled into the deeper Midland Basin. The Cline reflects this direction of flow in its makeup. The closer the Cline is to the Eastern Shelf, the higher its clay content and inversely, the western section consists of less clay and more brittle rock.
The depth of the Cline ranges from 5,000 ft at the Eastern Shelf to 9,500 ft in the Midland basin (Table 2). The formation’s thickness ranges from about 500 ft on the eastern side and narrows to 200 ft on the western side. The percentage of total organic carbon, an important measure of a shale play’s productive potential (Table 3), in the Cline is relatively high compared with other formations and ranges anywhere from 2% to 7.5%. The shale’s thermal maturity is in the range of 0.85% to 1.1%, which is an indicator that the oil is of good quality, wet gas is present, and there is enough pressure to push the liquids out of the tight rock. “These numbers are exceptionally good for Cline shale,” said Gary Dawson, a geologist with more than 30 years of experience working in the Permian Basin. The results of early chemical analyses were so good that many people thought they had found the next Eagle Ford. “However, we haven’t seen that kind of response with production,” he said.
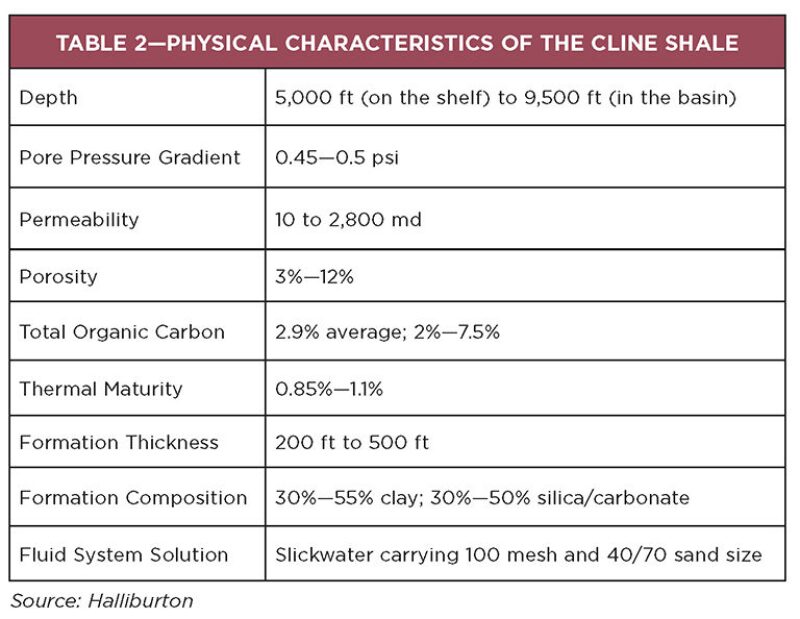

Dawson said the lower-than-expected production problems in parts of the Cline may be because of a lack of “impurities” inside the rock that include sand grains and carbonate debris, such as bits of limestone and soft silt. Because a shale formation has relatively little to no connected pore space, it needs these bits of rock and sand to help create flow paths for hydrocarbons, or permeability. “In a shale formation that has no connected pore space, the oil has no avenue to escape the formation,” Dawson said.
Clay-Rich Formation
A high proportion of clay in the Cline, which ranges from 30% to 55% depending on the location, has led to other completion and production complications that service companies such as Halliburton are working to solve. Operators have encountered a problem in the Cline known as sloughing, or heaving, where the shale expands as a result of the high-clay content and in extreme cases, causes wells to collapse. “If the clays are part of the rock matrix, or fabric, as they swell then the rock will tend to fall apart,” said Kenneth Borgen, Halliburton’s chief technical professional in the Permian Basin. “In other formations, if the clays exist within the pore spaces, the rock remains competent, but the flow path for oil and gas to move through the rock becomes impeded by the swelling.”
While there is clay in the deeper part of the Cline close to the Midland basin, Borgen said it may have already reacted with weather, water, and other environmental forces that lessen the likelihood of it reacting to drilling and completion fluids. Closer to the Eastern Shelf, the clays have had less exposure to the elements over time and are more reactive to water. To reduce the reactivity of the clay, Halliburton is using various types of salts and in very severe cases, stabilizing polymers, to render the clay unreactive to fluids. “Before your bit reaches the clay seats of the formation,” Borgen said, “you would want your mud systems to have the right additives in it. If properly applied, the polymers are very effective but they have to be applied in the right concentration and quantities.” If the mix is not right, the condition of the well may not show any noticeable difference, or it could become substantially worse.
Dealing with the Cline’s clay also means that perforation charges inside the perforating gun must be modified. “The standard perforating charges of yesterday that were designed for hard brittle rocks will tend to go too deep and be too narrow in a soft rock,” Borgen said. The charges developed by Halliburton for the Cline are less powerful and have a different shape that creates a broader cone of broken rock to allow more hydrocarbons to flow into the wellbore.
What Is Total Organic Carbon?Geophysical well logs are used to measure total organic carbon (TOC) to determine the quality of the source rock as it relates to hydrocarbons. Shale rocks that have a TOC of more than 2% are considered worthy of exploration. Increased TOC percentages indicate how rich the shale rock is with organics. What Does Thermal Maturity Tell Operators?A rock’s TOC is correlated with the presence of kerogen, an organic substance formed from the remains of plant and other living matter and is a precursor to oil and natural gas. Thermal maturation refers to how the kerogen changed into hydrocarbons. Deeper rock that was deposited at an earlier geologic period than shallower rock will tend to have a higher thermal maturity. Operators can use the thermal maturity data to determine if a shale oil play is immature, in the early oil window, at peak oil generation, in the late oil window, in the zone of condensate and wet gas generation, or in the dry gas window. |
Natural Fractures Aid Production
As of September, Apache was operating four horizontal drilling rigs in the Cline—all of them in Glasscock County where it has more than 130,000 acres leased in what the company believes is the “heart of the play.” Apache estimates that it has an additional 520,000 lease acres in the Cline.
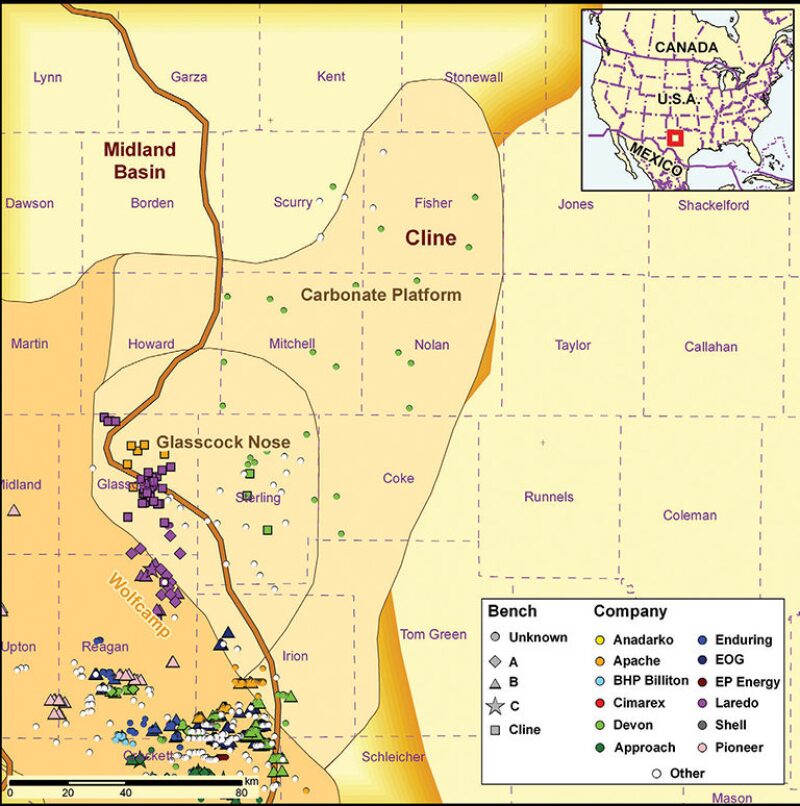
The company is focusing on five areas within that acreage where it has drilled 27 wells through August and is projected to complete a total of 40 by year’s end. At the end of August, Apache’s production from the completed wells in Glasscock County was 2,000 B/D and 4 MMcf of gas. Two Cline wells in Irion County, located in the southern Midland basin 60 miles southeast of Glasscock County, had 30-day initial productions ranging from 90 to 600 BOEPD, with peak initial production rates ranging from 240 to 800 BOEPD. Within the formation, Apache is targeting a section about 300 ft thick and has completed horizontal wells in the top, middle, and bottom portions of the Cline shale play. Each well’s location is determined by running logs, identifying where the oil shows appear within the Cline, modeling, and then executing a proper fracturing job.
John Polasek, Apache exploration manager for the Permian Basin, described his company’s first Cline well as a “failure” after it achieved a 30-day average production rate of only 90 B/D. Since then, Apache has learned a lot about the formation and has tweaked its well and hydraulic fracturing designs to optimize the results (Fig. 2). Apache’s typical horizontal wells in the Cline now have lateral sections of 4,500-ft and 12 fracturing stages (Table 4). Polasek said Apache experimented with longer lateral lengths up to 6,500 ft, but found that once initial production rates leveled off, those wells did not necessarily produce more than the 4,500 ft lateral wells. Recent wells with tighter clusters and more fracture stages have responded positively with higher initial production. “We also found that certain areas are more prolific than others, so there is a variability of rock in the Cline,” Polasek said.
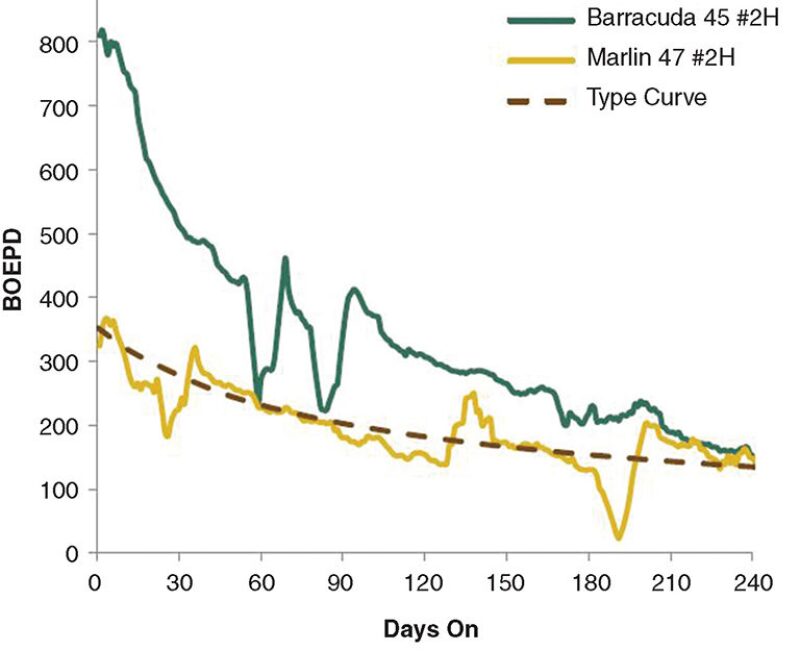
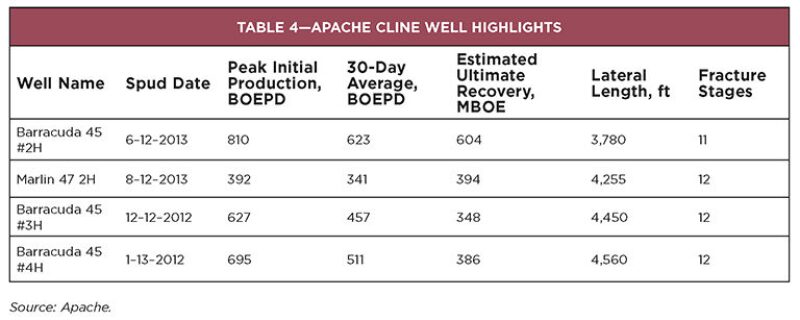
Apache has discovered that natural fractures inside the rock can positively affect the flow patterns of oil and gas through the shale. Fracture stages associated with these natural fractures, which in some cases run for just 2 or 3 ft, contribute significantly to production. “We’ve done core samples and you can see that the fractures are open,” said Polasek, who added that he has not seen natural fractures like that of the Cline in any other Permian formation. If long enough, the natural fractures can transfer, or communicate, hydrocarbons from one area in the rock to another. And while some of Apache’s best Cline wells are related to these natural fractures, what they give they can also take away by accelerating the depletion rate of other wells, forcing operators to rethink how close horizontal wells should be to each other. When offset wells are drilled next to completed and producing wells, “which may be 6 months to a year later, they don’t come on as strong,” Polasek said. “The wells are obviously communicating with one another.” In response, Apache will likely only drill a maximum of four horizontal wells per section in certain areas, instead of the five to six that its original development plans called for.
Midway through the learning curve, Apache is making significant reductions in well costs and zeroing in on the most productive areas to drill. At the outset, Apache’s average well cost up to USD 9 million to drill and complete. Since drilling those first experimental Cline wells in 2011, the company has brought its cost per well down by almost 28% to USD 6.5 million. Some of the savings came from a growing familiarity with the formation and improvements in operational efficiency that have lowered the number of days it takes to drill and complete each Cline well from 45 to 26 today. “Even though we are 2 years out, we are still learning. But the learning part isn’t necessarily about the geology, rather it is about maximizing your rate of return on this large resource asset,” Polasek said.
Stacked Completions and Pad Drilling
Holding leases on almost 140,000 acres in the Cline, Tulsa-based Laredo Petroleum is another early front-runner in the development of the play and drilled its first horizontal well in July 2010. As of August, the company said it had a total of 36 Cline wells. Laredo’s best horizontal Cline well was completed in early August with a lateral length of 6,933 ft, and based on 22 days of production, the well’s projected 30-day initial production rate was 1,331 BOEPD (Table 5). Based on its reservoir modeling, Laredo determined that drilling wells about 660 ft apart created the optimal “pressure interference” between wells to maximize long-term production. This spacing should allow for eight horizontal wells per each square mile section.
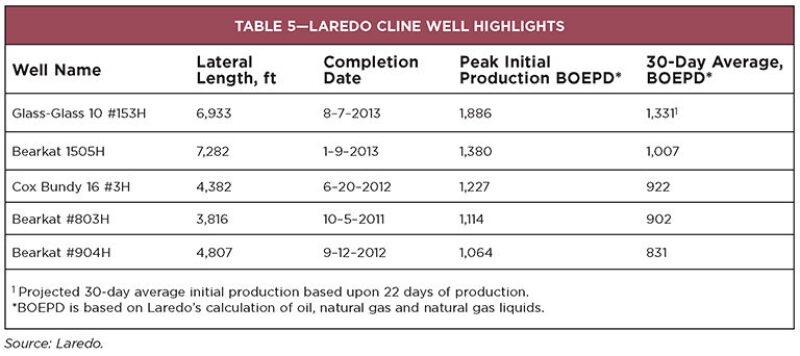
The Cline is not alone in the Permian Basin. Sitting on top of the Cline are several layers of younger source rock called the Wolfcamp shale, which is divided into three sections: upper, middle, and lower. Wells drilled in the Wolfcamp are cheaper than Cline wells and have a higher rate of return because the formation is shallower, contains a higher content of brittle rock, and on average, produces more hydrocarbons. Laredo’s cost to drill and complete horizontal wells with 7,500-ft lateral sections in the Cline is USD 9 million, compared with Wolfcamp wells that cost between USD 7.8 million in the upper section and USD 8.5 million in the lower section with the same lateral length. Laredo’s goal is to reduce the cost of a Cline well to USD 8 million by next year.
Laredo is moving away from one-off wells targeting just one pay zone and toward stacked completions in which horizontal wells are drilled from the same drill pad at different depths, with up to eight wellheads placed just 25 ft apart (Fig. 3). Stacked completions require pad drilling to provide a foundation to support the drilling of multiple wells from the same location, thereby reducing the time it takes to “rig up” and drill each well. To optimize pad drilling, Laredo is using so-called walking rigs that can move from one spot to another on the pad in just a few hours instead of 2 or 3 days for traditional rigs. Pad drilling also enables a completion technique known as a “zipper frac,” in which adjacent wells are fractured in sequence while one well maintains pressure as another is hydraulically fractured.
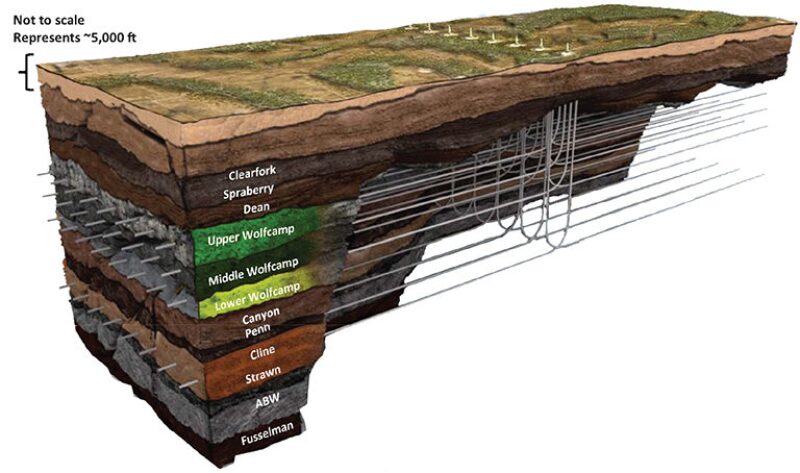
The company’s first stacked well pad was in the final stages of completion as of late September and is expected to begin producing from each of the three sections of the Wolfcamp by the end of the year. Next year, the company plans to drill and complete two-stacked horizontal wells in the Upper Wolfcamp and Cline, four-stacked horizontal wells with lateral lengths of 7,000 ft to 7,500 ft, and an experimental well with a 10,000-ft lateral section.”
With six horizontal rigs operating, Laredo said that it is now entering a “manufacturing stage” of development and hopes to complete 50 to 60 wells next year, in both the Wolfcamp and the Cline. “We’re essentially building a hydrocarbon manufacturing plant,” Jay Still, Laredo’s chief operating officer, said during an investor presentation in September. “It is not just developing an oil field by drilling wells, we are building a factory.” The factory that Still is referring to includes miles of processing equipment and pipelines to take away wet gas, oil, and produced water and deliver high-pressure gas for artificial lift, water for fracturing jobs, and dry gas to run the generators that power drilling and hydraulic equipment. By using natural gas to power its drilling and completion equipment, Still said, Laredo can save up to USD 2 per equivalent energy unit on the 1,500 to 2,000 gal of diesel fuel it uses every day.
Laredo is building an infrastructure to address one of the major challenges facing the shale boom in west Texas: water supply. Laredo and other companies in the area are building water pits, water treatment systems, and drilling wells into brackish aquifers in order to provide their operations with a constant supply of water needed for drilling, and especially for completion operations. “We can localize all the water from a pretty large geographic area to one spot on the map when we are doing four fracs in a row, which requires a lot of water in one place,” Still said. “If you tried to do this with trucks, it would take 2,500 to do that frac job. There is no way you could that with that many trucks on the road.”
As Apache, Laredo, and other companies find solutions to successfully develop the Cline, the Permian Basin as a whole is seeing a resurrection in production. While technically challenging, the Cline is being developed to become a significant piece in the mosaic of shale plays and an important asset in its operators’ portfolios. If progress continues in the Cline and several other major plays, the likelihood that the Permian Basin will live up to expectations and produce more than 2 million BOEPD in the next 5 years increases with each successful completion.