A Surprising Announcement
On 1 July 1922, roughnecks discovered oil in the Smackover Field of Union County, Arkansas. At the end of an exhilarating (albeit dramatic day), a photographer captured an image of the weary, oil-coated crew. The image depicts them standing amongst the tall pines of the Southern Arkansas wilderness, which is not exactly what you picture when you think of the future capital of the American electric vehicle (EV) industry.
But ExxonMobil thinks differently. In November 2023, the company announced its acquisition of 120,000 gross acres in the Smackover Formation in southern Arkansas, stating its intention to become a leading producer of lithium, a critical metal for EV batteries and the global energy transition.
ExxonMobil’s interest in lithium isn’t necessarily surprising. While lithium is certainly different from oil, it still is an extractive, which is ExxonMobil’s specialty. In 2015, less than 30% of lithium demand was for batteries and by 2030, batteries are expected to account for 95 percent of lithium demand. According to some estimates, the demand is increasing exponentially.
In 2021, 540,000 tonnes of LCE were produced globally. By 2030, demand estimates range from 2 to 3 Mt, a four- to sixfold increase. Many predict there could be a shortfall of approximately 40,000 to 60,000 tonnes of LCE in 2025 due to potential regional shortages and intermittent delays in the near future. These delays are attributed to the time required to develop a discovery mine (roughly 10 years). Obviously, ExxonMobil is preparing to fill this gap in the market.
But, lithium in an Arkansas oil field? Yes, you heard that right. As the song by Chris Stapleton goes, “If you want to get down, you gotta get to Arkansas.” Lithium-rush miners are getting there, and fast.
Why the Smackover?
The Smackover Formation is enormous, sprawling over parts of Texas, Arkansas, Louisiana, Mississippi, Alabama, and Florida. Since the initial discovery of oil in the Smackover, over 1,000 oil wells have been drilled in approximately 600 former and currently producing oil and gas fields. While there is still oil production from the Smackover, it is no longer newsworthy compared to the vast reserves in neighboring US basins.
Thanks to the Smackover discovery, however, wildcatters serendipitously found something else: bromine-rich brine, produced alongside hydrocarbons. The bromine is recovered from the brines, and the remaining brine is reinjected back into the well. Arkansas is now the second leading producer of bromine, which is used in fire retardants, agriculture, pharmaceuticals, and certain drilling fluids.
In the 1960s, something else was discovered in the Smackover brine, particularly in brine deposits in southern Arkansas: lithium. And not just a little lithium. A lot of lithium.
Several of the Arkansas brine deposits contain over 300 mg/L of lithium in the composition. For perspective, operators must have a brine composition of at least 80 mg/L of lithium to be profitable. Interestingly, other areas within the Smackover do not necessarily have such high concentrations of lithium. Nor do neighboring formations. Though we don’t know exactly why this is, some studies suggest that the shape of the formations caused the lithium to pool together in this specific area.
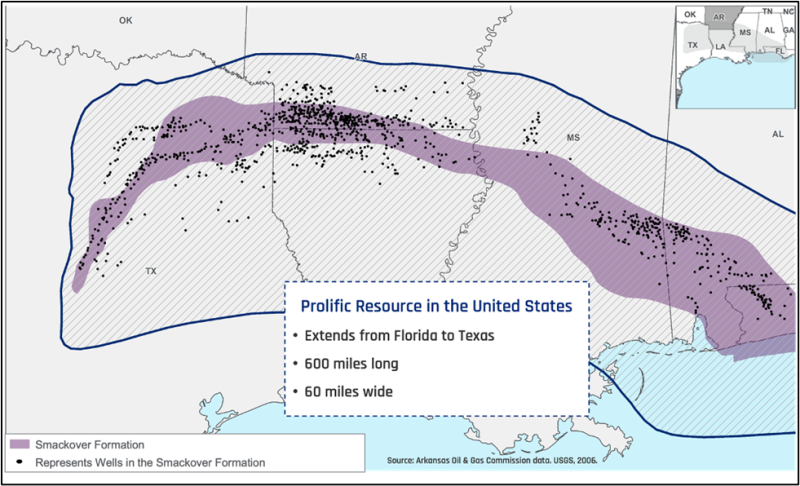
Traditional Lithium Extraction
Traditionally, there are two major ways to extract lithium: Hard rock extraction and brine extraction.
Hard rock lithium extraction is only possible in areas that have, well, hard rock. Hard rock containing a mineral called spodumene (LiAlSi2O6) is particularly desirable as it contains the highest lithium concentration.
Unfortunately, spodumene is a miserly mineral, trapping lithium within a strong, α-monoclinic crystal structure, releasing the lithium only at great cost. To wrest the lithium from the spodumene, producers must pulverize the rock and, often, send it on a transcontinental journey to specialized processing facilities. In these factories, the spodumene is subjected to intense temperatures, in excess of 1,832°F (1,000°C), and unique and harsh chemical reactions requiring large volumes of sulfuric acid (H2SO4). The intermediate material must be further converted and purified into “usable” lithium for EV batteries. The final result is usually a measly 1 tonne of lithium (LCE) for every 8 tonnes of spodumene. All in, LCE costs from hard rock sources to final product are approximately $2,500/tLCE. The process is intensive and expensive.
The other lithium extraction method is brine. Globally, 31 Mt of lithium is estimated to be available in brine reserves. Unsurprisingly, most brine sources come from oil fields. In countries like Chile, Bolivia, and Argentina, this brine is stored in large lithium extraction reservoirs, also known as salars, where the sun slowly evaporates enough water to concentrate the lithium. From there, the lithium is processed into a usable product.
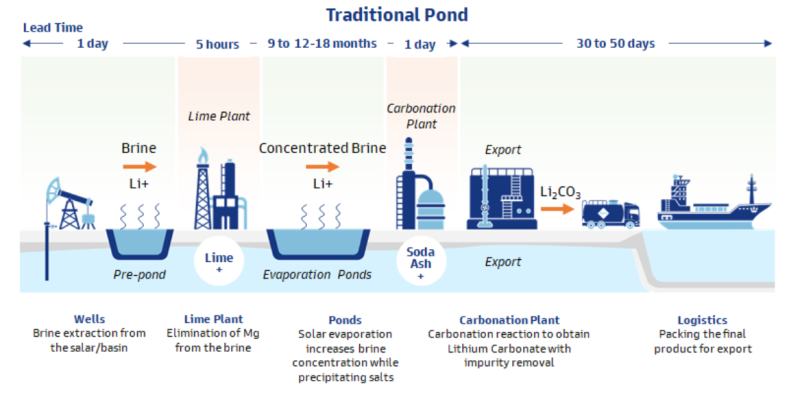
The average cost to produce lithium products via the traditional pond method is USD 5,580/tLCE, which is significantly more expensive than hard rock production (USD 2,540/tLCE).
So why is ExxonMobil interested in the brine of Arkansas? The answer is an almost 2x margin advantage over hard-rock production. Unfortunately, as it stands now, most brine-extracted lithium is not battery-grade material and is used in other markets. To change this, either additional processes must be put in place at the production sites for improved purity, or advances must be made to increase tolerance of the impurities. Neither is an easy fix.
Direct Lithium Extraction (DLE)
So how does ExxonMobil plan to become a leading producer of lithium for EV batteries if Arkansas is a brine extraction region that does not produce the LCE necessary for batteries? According to the November 2023 press release, ExxonMobil’s plan is to use direct lithium extraction (DLE) technology to separate lithium from the brine. The lithium will then be further reacted to battery-grade material, while the brine byproduct will be reinjected back into the formation. If this process sounds familiar, it’s because it mirrors the Smackover bromine extraction process almost exactly.
1. Produce high-brine-content water.
2. Extract desired mineral.
3. Re-inject water back into the formation.
The advantages of DLE are numerous:
- EV-grade lithium: Compared to traditional methods, DLE offers an innovative way to improve processing costs and purification specifications, which will allow brine lithium sources to be used in EV batteries.
- Smaller environmental footprint: DLE takes up less physical space, bypassing the need for large evaporation ponds.
- Fast development: A new lithium mine can take 10 years to develop from first discovery to full operation. Salar ponds require roughly 2 years to produce lithium. DLE takes advantage of already existing processes, which means the 150 fields in Arkansas that are already producing and mature are more easily exploited for lithium production right away.
- Proven technologies: DLE techniques are proven technologies. If you’ve spent any time in a chemical or analytical lab, you may have used some or all of them. Some extraction processes DLE may incorporate include adsorption columns, ion exchange, solvent extraction, and membrane separation.
- Less energy and fewer harsh chemicals required: Following extraction, further purification and concentration of the lithium salt solution, typically LiCl, uses chemical softening and impurity removal processes that are industry standard processes for water and wastewater treatment (e.g., brackish water reverse osmosis). None of these processes are as energy-intensive as the traditional methods, nor do they require harsh chemicals.
- Fast, local production: DLE enables lithium to be converted into battery-grade material onsite, as opposed to the hard rock extraction method, which requires lithium to be exported to distant laboratories for production.
- Proven success: Standard Lithium has been operating an industrial-scale fully integrated DLE demonstration plant at the LANXESS South facility in Arkansas since May 2020 and has had great success producing high-purity lithium. Much of their success can be attributed to knowledge sharing from the Arkansas bromine extraction industry.
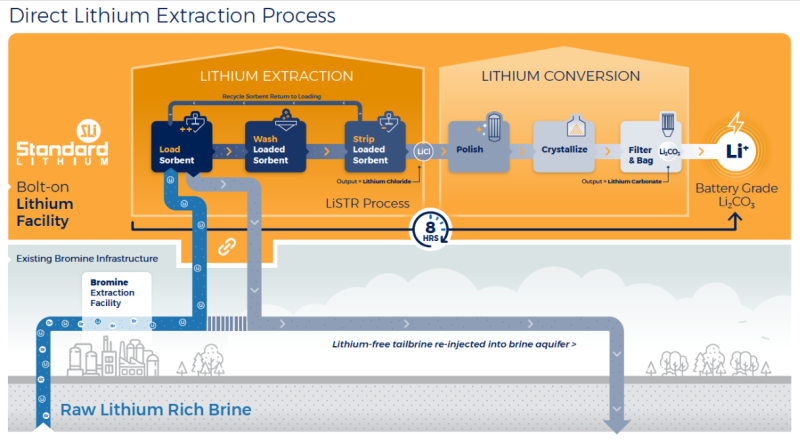
Will DLE in Arkansas Succeed?
Despite all the good news about DLE, it is still an expensive endeavor. Will the investment be worth it? Within their LANXESS lease parcels, Standard Lithium reports a Measured and Indicated Resource of 2.8 Mt LCE at an average lithium concentrate of 148 mg/L and Proven and Probable Reserves of 208 Kt LCE at an average concentration of 217 mg/L. Recall that conventional estimates call for a concentration of >80 mg/L to be viable. If these numbers are correct, that is extreme viability.
But does the Smackover have enough supply to support the increasing demand for EV technology?
The answer is maybe. There have been somewhat contentious debates over how much lithium actually goes into an EV battery. It seems the true amount of lithium in a battery isn’t clearly reported by manufacturers. Paul Martin has an interesting 2017 LinkedIn post that lands on ~160 g Li metal per kWh of battery power (~850 g LCE). A typical EV battery with 50 kWh capacity equates to 40 kg LCE per battery. Assuming there are 40 million vehicles on the road in 2030 (at 50 kWh/vehicle), that puts demand at 1.7 Mt LCE in 2030.
Good News, Well Timed
ExxonMobil’s news comes at an opportune time. Once the largest producer of lithium in the world, the US has steadily lost market share in lithium production for over 30 years, landing it in eighth place in 2021. Whether it is oil, gas, or renewables, it is critical that the US achieves energy independence soon. Increasing lithium production will be a strong move in the right direction. ExxonMobil’s activity in the Smackover will also help to soften the blow in the predicted 2025 lithium shortage.
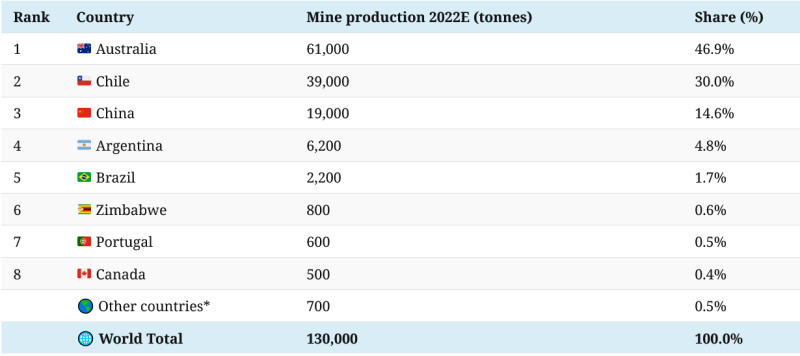
ExxonMobil’s partnership with Arkansas is particularly exciting, as Arkansas is one of the few states with well-established production and brine extraction. Arkansas brine laws should also offer an easy transition and avenue for producers wanting to operate in Arkansas and for other states wanting to attract local business for the development of lithium production.
Will Arkansas be the future capital of the EV revolution? There are many unpredictable variables at play, and time will tell. The Chris Stapleton song does ring true though: “What I found in the Ozark mountains I ain't ever seen. It sure does feel like you're sittin' on top of the world to me.”
For Further Reading
Firm Claims Texas Well Holds Highest Lithium Concentrations in North America by T. Jacobs, JPT.
Equinor Takes Ownership Stake of US Lithium Brine Projects by T. Jacobs, JPT.
Electric Rush: ExxonMobil To Drill Enough Lithium Wells To Make 1 Million EVs a Year by T. Jacobs, JPT.
ExxonMobil Drilling First Lithium Well in Arkansas, Aims to be a Leading Supplier for Electric Vehicles by 2030, ExxonMobil.
Arkansas Smackover Projects, Standard Lithium.
How Much Lithium Is in a Li-Ion Vehicle Battery? by P. Martin.
Oil in Arkansas—The Smackover Field, Historical Marker Database.