The global energy sector is navigating a critical transition, with decarbonization and energy security emerging as top priorities. Both natural gas and hydrogen play essential roles in this process. Natural gas continues to serve as a reliable, high-energy-density fuel for power generation, heating, and industrial operations. At the same time, hydrogen offers a clean, flexible energy carrier that can significantly reduce greenhouse gas emissions when produced from low-carbon or renewable sources.
Rather than viewing these fuels as competing options, the energy industry is increasingly adopting a combined approach that leverages the strengths of both. Blending hydrogen with natural gas provides a practical, near-term solution to lower emissions without sacrificing energy reliability. Crucially, this strategy takes advantage of the extensive natural gas infrastructure already in place, including pipelines, storage facilities, and compressor stations. Using existing infrastructure avoids the significant costs and time required to build dedicated hydrogen transport networks (Huang et al., 2025). It allows for early hydrogen adoption at scale, providing a realistic, phased approach to decarbonization while preserving system flexibility and energy security. Countries and companies worldwide are pursuing hydrogen/natural gas blending to meet emissions targets, optimize infrastructure investment, and prepare for a low-carbon energy future.
This article focuses on exploring the opportunities, challenges, and industry pathways for integrating hydrogen into existing natural gas infrastructure. It highlights the global shift toward hydrogen/natural gas blending, examines key technical barriers such as hydrogen embrittlement in pipeline materials, and presents ongoing research efforts aimed at ensuring the safe and reliable operation of blended gas systems. The article also introduces practical solutions, including the application of machine learning models, to support decision-making and infrastructure adaptation in the energy transition.
In Europe, the NaturalHy project investigated the technical, economic, and safety aspects of hydrogen injection into gas pipelines. The UK has seen similar efforts, including the HyDeploy and H21 Leeds CityGate projects, aimed at assessing the safe delivery of hydrogen/natural gas blends to consumers. China launched its first comprehensive experimental platform in 2024, designed to evaluate hydrogen blending into municipal gas systems (Mahajan et al., 2022). These efforts demonstrate that introducing controlled amounts of hydrogen into existing pipelines can significantly lower hydrogen transport costs, reduce carbon footprint, maximize the use of current infrastructure, and accelerate the development of hydrogen as a mainstream energy solution.
A study by Huang et al. demonstrated that hydrogen-blended natural gas (HBNG ) usage for power generation significantly reduces carbon emissions, primarily because of hydrogen’s high calorific value and its zero carbon emissions at the point of use. This reduction in emissions yields measurable economic benefits through participation in carbon markets. As illustrated in Fig. 1, the study further revealed that, when the hydrogen blending ratio (HBR) reaches 20%, the HBNG consumption decreases from 0.105 to 0.080 kg/kWh, accompanied by a reduction in carbon intensity from 0.468 to 0.374 kg/kWh. Additionally, the carbon-related economic benefit increases with higher blending ratios, reaching 0.0333 CNY/kg at 20% HBR, underscoring both environmental and economic advantages of hydrogen integration.
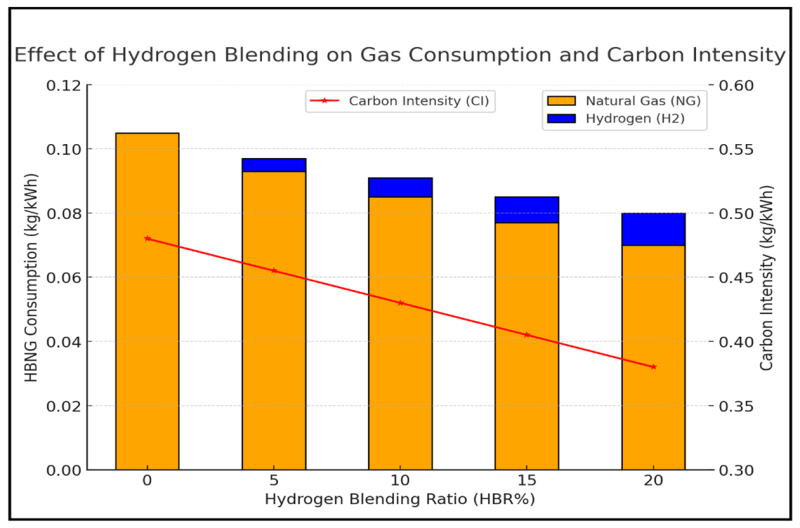
Although hydrogen blending offers notable environmental and economic benefits, it also introduces several technical and operational challenges for existing natural gas pipelines. One of the more critical issues is the risk of material degradation caused by hydrogen embrittlement. Hydrogen embrittlement occurs when hydrogen atoms penetrate metallic structures, especially high-strength steels, leading to a reduction in both ductility and resistance to crack growth. This phenomenon can significantly increase the likelihood of premature cracking or failure in pressurized pipeline systems.
Common pipeline materials such as API 5L X52, X60, and X70 steel grades, extensively used for natural gas transmission, have shown susceptibility to this form of degradation under specific conditions. The presence of welds, microstructural heterogeneities, and operational stresses further complicate the assessment of pipeline integrity in hydrogen-blended environments. These challenges demand a comprehensive understanding of how hydrogen behaves within the existing infrastructure and how materials and systems respond over time.
Recognizing the technical challenge, numerous studies have examined hydrogen's effects on pipeline steels and material reliability. However, most existing research focuses on pressure vessels or structural materials, leaving typical pipeline operating conditions underrepresented. This is particularly important as hydrogen saturation in carbon steel and the associated risk of embrittlement occurs between 0.1 and 7 MPa, with the embrittlement effect stabilizing around 6.5 MPa, according to a recent study (Ahmed et al., 2024). Additionally, many studies rely on electrochemical hydrogen charging, which does not fully reflect real pipeline conditions where pressure, temperature, and gas composition continuously vary (Giarola et al., 2022; Hoyos et al., 2019). Addressing these gaps requires targeted research under realistic service conditions to better understand how hydrogen affects fracture toughness and ensure pipeline integrity.
In response to this gap, our ongoing research (Gyaabeng et al., 2025) funded by the US Department of Transportation (DOT-PHMSA), focuses on evaluating the fracture toughness of commonly used pipeline steels, including API 5L X52, X60, and X70 grades, in hydrogen environments. The study involves exposing steel specimens to high-pressure hydrogen at varying temperatures, followed by fracture toughness testing and detailed microstructural analysis.
By correlating material composition, microstructural features, and mechanical performance, this research aims to quantify degradation mechanisms associated with hydrogen embrittlement and generate practical data to guide material selection and ensure the integrity of pipelines intended for hydrogen-natural gas blending. Engineers can define an operational window to minimize crack propagation and early failure by precisely measuring and predicting fracture toughness in hydrogen-exposed pipelines.
In addition, Gyaabeng et al. have also developed machine learning models aimed at predicting hydrogen embrittlement in pipeline steels. These models use experimental data, steel composition, and microstructural characteristics to forecast material performance under varying hydrogen concentrations and service conditions.
This approach offers a powerful, nondestructive tool for assessing material suitability and integrity before failures occur. While the application of machine learning enhances predictive capabilities, it also highlights areas of uncertainty, particularly regarding the influence of extreme conditions or rare material defects that may limit the accuracy of purely data-driven models. As such, the combined use of experimental testing and machine learning provides a more comprehensive understanding of material behavior, supporting the safe integration of hydrogen into existing pipeline infrastructure.
For Further Reading
Modeling of Necking Area Reduction of Carbon Steel in Hydrogen Environment Using Machine Learning Approach by N. Ahmed, M. Aldaw, R. Ahmed, et al., University of Oklahoma
The Effect of Hydrogen on the Fracture Toughness of Friction‐Stir Welded API 5L X70 Pipeline Steels by J. Giarola, University of São Paulo, J. Avila, São Paulo State University, O. Cintho, State University of Ponta Grossa
Modeling the Impact of Hydrogen Embrittlement on the Fracture Toughness of Low-Carbon Steel Using a Machine Learning Approach by M. Gyaabeng, R. Ahmed, N. Ahmed, et al., University of Oklahoma
Influence of Hydrogen on the Microstructure and Fracture Toughness of Friction Stir Welded Plates of API 5L X80 Pipeline Steel by J. Hoyos, State University of Ponta Grossa, M. Masoumi, Universidade Federal do ABC, V.F. Pereira, State University of Campinas, et al.
Economic Analysis of Blending Hydrogen Into Natural Gas Pipelines: Supply Chain and Station Modification by H. Huang, X. Sun, China University of Petroleum, J. Li, Yangtze University, et al.
Hydrogen Blending in Gas Pipeline Networks—A Review by D. Mahajan, K. Tun, T. Venkatash, Stony Brook University and Institute of Gas Innovation and Technology, et al.
Blending Hydrogen into Natural Gas Pipeline Networks: A Review of Key Issues by M. Melaina, US Department of Energy, O. Sozinova, M. Penev