Petroleum engineering (PE), being the academic arm of oil and gas exploration and production (E&P), is expected to drive the frontier in petroleum technology research and development (R&D). It is in this environment that I will try to identify and elaborate on five fundamental technological R&D challenges in today’s upstream petroleum industry. The thoughts that follow are my own.
In hard sciences (PE included), quantitative research is divided into three branches. The first is the analytical branch which involves the derivation of close-form mathematical models that describe natural phenomena and processes through symbolic manipulations (in the form α + β = γ ˗ δ). The second branch is the numerical, which involves the use of algorithms for evaluating mathematical models with continuously varying variables. This almost always incorporates using a computer to carry out numerical procedures, solving systems of multiple equations. The third is the experimental branch, which involves laboratory testing aiming at the development of empirical correlations. A well-designed R&D project usually incorporates at least two of the aforementioned branches.
1. “Fail-Safe”: Disaster Response and Technical Protocols
Safety should always come first.
Union Oils’s “A-21” well blowout in the Santa Barbara Channel in 1969 (Yergin, 1990), exposed the vulnerability of our industry to political consequences, lasting even to this day (Michael, 2019), such as the drilling ban for new offshore leases in California. BP’s 2010 “Macondo” disaster (Fig. 1) coming four decades after the offshore drilling safety developments following A-21, manifested once again the inherent dangers of dealing with flammable fluids. Whether the current state of petroleum technology can develop safe schemes for E&P is not the issue. Our risk as an industry is that one mismanaged loss-of-well-control situation will condemn the entire drilling business.
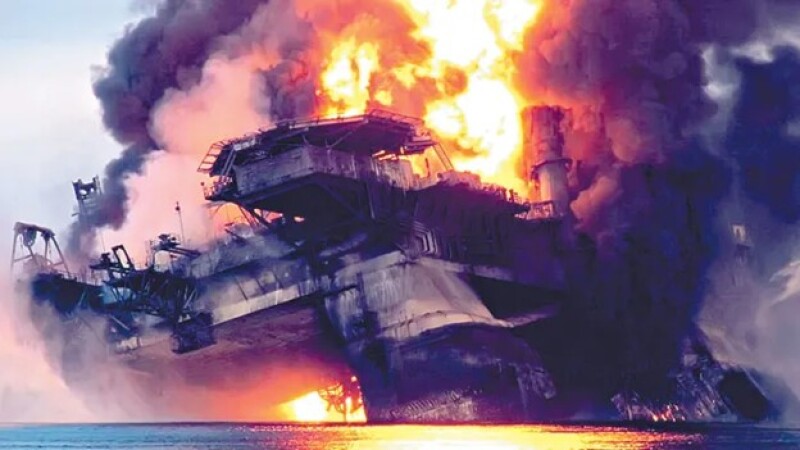
Nevertheless, solutions for improving E&P safety standards are likely to come from within the technical pillars of the industry. In this vein, the industry should pinpoint and examine pitfalls in technical protocols and contingency plans, exhausting every room for improvement. Too many things are at stake with the most overwhelming of all being human life.
2. Profitability: Higher Recovery Factors at Lower Costs
Roughly for every barrel of oil produced worldwide, two oil barrels remain underground.
So where will future oil come from? The state of R&D in the petroleum industry was debated a lot since the Arab Oil Embargo of 1973 (Yergin, 1990). Until the late 1990s, there where arguably two extreme (conventional) reservoir management attitudes: a “big elephant” reservoir type, produced under the proverb that a good reservoir cannot be “destroyed,” and the opposite end-of-the-spectrum, where the technology needed for proper development is not affordable due to low oil and gas prices (Durham, 1999). Fast depletion was never a vice of “new reservoirs” during that era.
The turn of the century brought with it a revitalization of petroleum technology R&D primarily through the US shale revolution and partially through offshore projects in the Gulf of Mexico. For meeting the world’s energy needs, the petroleum industry can coast largely with technology already at hand for some time into the future. However, next generation petroleum (E&P) technology should—among others—encompass industry efforts for driving deepwater developments, complex well architecture design features, and automated production management, all aided by modern day tools.
As public R&D spending traditionally keeps shying further and further from fossil fuel-related technology (Fig. 2), increasing its focus on non-fossil fuel-related themes (such as renewables), the private sector is left as an obvious ground to perform this vital function.
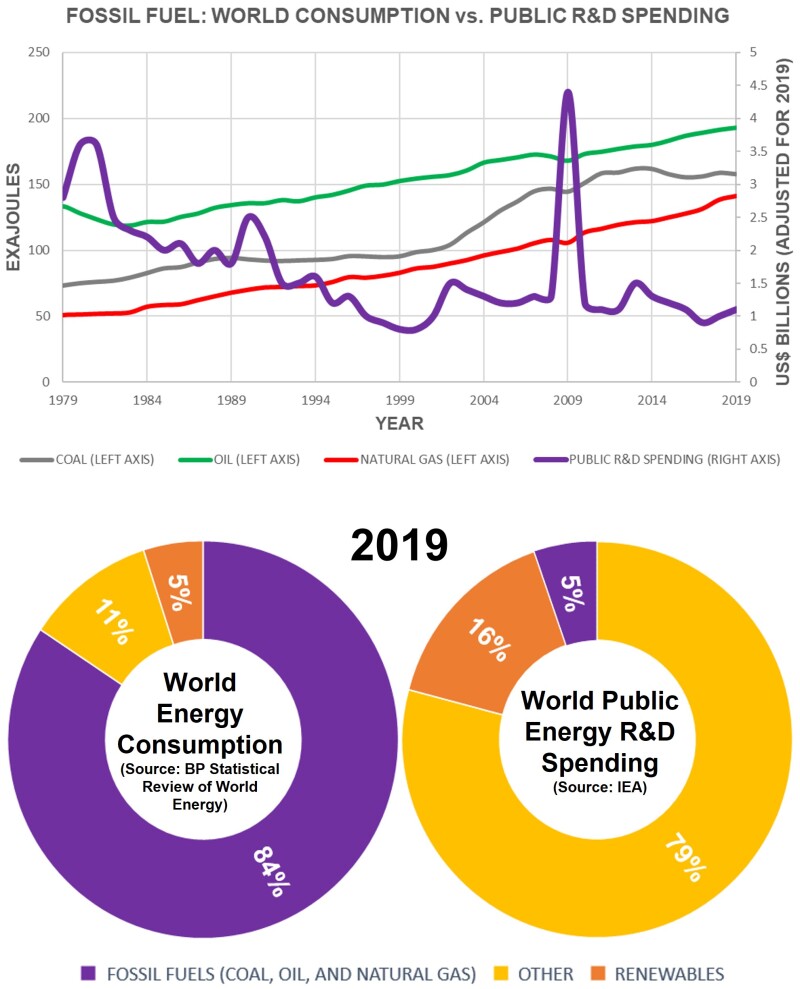
3. Transparent Earth: “Seeing” the Subsurface
The opaque nature of the Earth is a major obstacle for petroleum engineers in recognizing all aspects regarding subsurface phenomena and processes.
This challenge goes beyond “seeing” through miles of reservoir rock and imaging subsurface structures. It revolves around observing the consequences of activities on adjacent rock masses, evaluating the effectiveness of reservoir stimulation procedures, and real-time monitoring of a wide range of subsurface activities.
For instance, the fracture geometry induced in the laboratory experiment on Fig. 3 is hard to visualize with certainty had the specimen material (plexiglass) not been transparent. And this experiment model is just the simple case of a vertical well with a bi-wing hydraulic fracture—things in the subsurface get way more complex with horizontal wells, multiple fractures, and natural (pre-existing) fractures along their propagation pathway interfering.
In a discipline like PE, where almost everything that matters takes place thousands of feet underground, apportioning credit for successes or responsibility for failures is itself a challenge.
This unique-to-PE visional barrier makes technical experience more valuable compared to other fields, as the understanding of what goes on underground requires more than basic critical thinking. The technical ladder must reward technical professionals sufficiently, so that they would want to continue their technical work, rather than becoming managers.
4. Predictability: Simple and Effective Modeling
Keep an eye on the big picture.
This is the natural step following Challenge #3. A model’s complexity is not always correlated with its performance. Correct use of “rules of thumb” may show immediate results very similar to those that take hours to produce by numerical simulation. Going simple is often the best option.
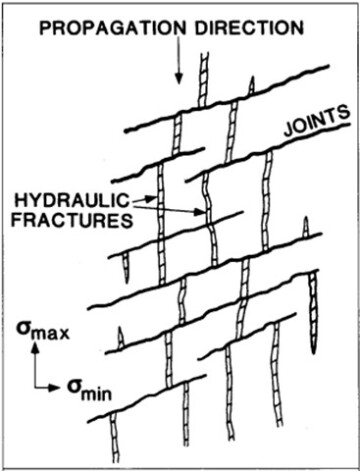
It is natural even for field experts to get overwhelmed and confused with overly complicated models, which converts these tools to “black boxes,” which makes their adoption extremely challenging. Practical workflows that can be easily comprehended by non-experts lead to efficient adoption of new tools. Technical complexities can be streamlined via smart ways through which complex subsurface aspects, such as the interaction of hydraulic fractures with natural fractures (Fig. 4) are treated in a results-focused manner, providing the engineer with a logical and coherent modeling workflow.
The complexity of the hydraulic/natural fracture network displayed on Fig. 4, may be more effectively modeled by targeting the calculation of the final stimulated reservoir volume (SRV) rather than focusing on calculating the geometric dimensions of every single induced fracture.
5. Coherence: Improve Industry–Academia Collaborations
It is fundamental to ensure presence of true industry experience in the academic sector.
Petroleum technology R&D is what brings industry and academia together when it comes to E&P (Fig. 5). Young professionals with strong educational background can bring a lot to their companies. They should know enough to appreciate what is new and may be more inclined to try new technologies than their more senior colleagues. They provide a pool for good future educators (Fig. 5).
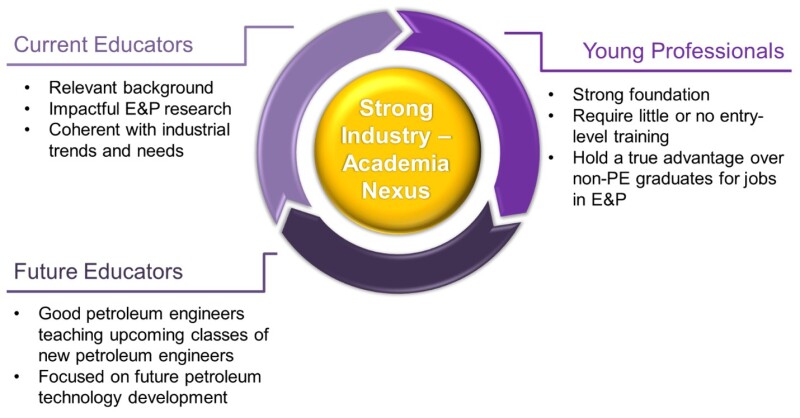
A strong research effort was always quintessential to an academic program in an applied field. Few professors would envision a university career without performing research. Academics without industry experience can be off-target and may lack essential connections. A fundamental question is how a professor can teach state of the art in a technology field, without an active participation and leadership in the development of this technology.
There are many within and outside the PE discipline who question the need for the existence of PE academic programs. I strongly object to the PE discipline having to rebrand to “energy engineering” as the reason students enroll in PE programs is to develop expertise in solving E&P problems. E&P is still big business and there are many challenges. Non-petroleum concerns are clearly a miniscule portion of the bottom line. Rebranding to “energy engineering” will make more harm than good, diluting any competitive advantage for PE graduates within E&P.
References
BP. 2021. BP Statistical Review of World Energy.
Durham, L. S. (1999). Gulf R&D Funding a Capital Idea - Professors Look for Government Push. AAPG Explorer.
Frash, L. P., Hood, J., Gutierrez, M., Huang, H., and Mattson, E. (2014). Laboratory measurement of critical state hydraulic fracture geometry. In 48th US Rock Mechanics/Geomechanics Symposium.
Michael, A. (2021). The True Market Value of a Good Petroleum Engineer: A Technical Perspective. In SPE Annual Technical Conference and Exhibition.
Michael, A. (2019). The Past, Present, and Uncertain Future of California’s Oil Business. The Way Ahead.
Warpinski, N. R., and Teufel, L. W. (1987). Influence of Geologic Discontinuities on Hydraulic Fracture Propagation (includes associated papers 17011 and 17074). Journal of Petroleum Technology, 39(02), 209-220.
Yergin, D. (1990). The Prize: The Epic Quest for Oil, Money & Power. Simon & Schuster.