Oil and gas reserves are so far the world’s most dominant energy sources. Production is predominantly coming from mid- and late-life fields, and this trend will continue well over the next decade.
As mature field contribution increases, oil and gas operators and oilfield services (OFS) companies are relying even more on stimulation treatments to meet the global energy demand. However, reservoir performance is a major challenge, with one in three remedial operations failing to meet the objectives of incremental barrels. This creates a double jeopardy in which both the expected returns on the stimulation investment and reservoir production do not fulfill the projected potential.
While a well might be shut-in briefly for stimulation, this investment should recover lost production during shut-in, rig time for stimulation pumping, and other associated costs with incremental barrels. Whenever this is not the case, the potential loss to an asset owner for an underperforming well is tremendous, and only recoverable by more stimulation and pressure maintenance at even greater cost. Underwhelming stimulation results are primarily due to misdiagnosis of reservoir damage, and therefore misaligned stimulation treatments.
Hydrocarbons within the reservoir flow towards the wellbore, due to a pressure gradient between the reservoir boundaries and the wellbore (Fig. 1). In an ideal situation, these fluids flow unimpeded through the wellbore to the surface; however, energy is expended in flowing through the interconnected pores of the formation, into the wellbore, and through tubing to the surface facilities. Minimizing this pressure loss facilitates efficient recovery (getting as much oil as possible for every unit pressure drop in the reservoir) and this directly impacts profitability. For example, pressure maintenance is needed earlier to sustain production, which increases the cost of production, while the sale price remains subject to market forces and not production inefficiencies.
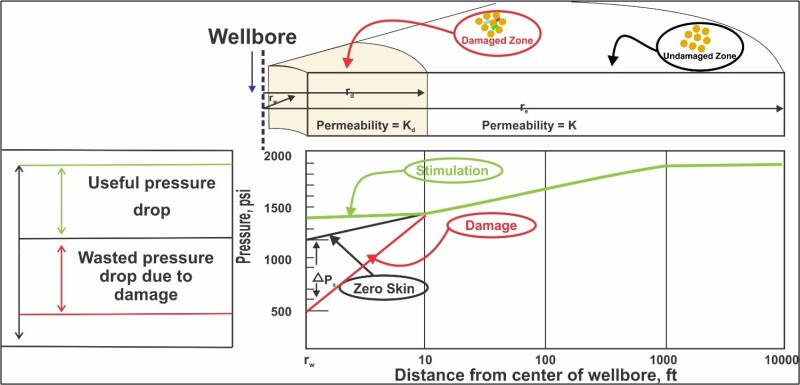
Understanding the Reservoir
Oil and gas reserves reside predominantly in sandstones and carbonate reservoirs (sedimentary rocks). Knowledge about the type of reservoir and specific mineralogy is extremely important because critical decisions such as determining which drilling and completion fluids to use in the reservoir depend upon a thorough understanding of a formation’s mineralogy. For example, low-salinity brines induce an adverse chemical (damage) reaction from hydrophilic clays that cause swelling and restrict fluid flow in the damaged region. Consequently, if investment in formation analysis reveals a high composition of migratory clay (such as kaolinite), gradual production buildup and shutdown must be implemented to optimize reservoir management. In this case, the reservoir must be started up and shut in gradually to avoid shaking loose fine materials (“fines”), since a hard start or stop will dislodge the fines, that will then travel to the wellbore and result in physical (mechanical) damage at the near-wellbore region. These examples are million-dollar impact events, more common than other forms of damage in the early life of a field, and more prevalent in deepwater environments.
Formation Damage Evaluation
The first step to an effective solution is determining whether a damage is “natural” or “induced.” As a rule, the ultimate strategy is to manage natural phenomena and avoid induced damage to the reservoir.
Natural phenomena are damages related to the nature of the reservoir: for example, fines migration is typical of high-clay-content formations; clay swelling affects a type of formation; paraffin, asphaltene, and mixed deposits are natural to specific formations and crude compositions. Because these natural phenomena are not alterable, they must instead be understood and managed. A completion design can incorporate fines migration management strategy by reducing the fluid flow velocity through the installation of a high-flow-area completion, such as an openhole completion or a frac-pack completion. A completion can also include chemical injections which inhibit paraffin, asphaltene, or other deposits.
Conversely, the moment we penetrate and alter the equilibrium in a reservoir to gain access to hydrocarbons, the reservoir’s life of change begins and never stops. During drilling we introduce solid particles from the drilling fluid into the formation to minimize fluid loss and maintain wellbore stability—these solid particles serve us well during drilling, but become an impediment during production. We also invade the reservoir with filtrates foreign to the reservoir, which, if incompatible, also result in undesirable chemical reactions that result in precipitates that plug formation pore spaces. These are induced damages and are not limited solely to the drilling phase. For example, polymer plugging, wettability changes, emulsions, precipitates, and sludges are all damages resulting from injection fluids during completion and production/pressure maintenance activities.
The various types of damage can be categorized into these four main groups.
- Mechanical Damage: In this situation the root cause of damage is a nonchemical phenomenon, such as fines migration, in which naturally existing fine-grained clay particles are mobilized toward the near-wellbore area.
- Chemical Damage: This occurs when a fluid introduced into the reservoir induces an adverse reaction from the reservoir rock or reservoir fluid, such as clay swelling, which results from the chemical reaction of hydrophilic clays with certain low-salinity fluids. Another example is scale formation, which results from the chemical incompatibility of certain completions fluids with formation water.
- Biological Damage: This is caused by bacterial contamination from drilling, completion, and/or water injection fluids. Microorganisms can secrete polymers, which plug the formation and even facilitate reduction reactions of hydrogen and sulfates, which are corrosive to and cause stress cracking of completion hardware.
- Thermal Damage: Although not very common, this can occur in high-temperature production enhancements, such as steam injection to aid oil recovery. In such operations, temperatures as high as 450°F can result in the degradation of oil and sulfate-containing rock compounds and may produce undesired byproducts such as hydrogen sulfide (H2S) and carbon dioxide (CO2). This range of temperature can also aid mineral transformation, wherein a stable formation rock can be catalyzed to become reactive and swell, thereby reducing permeability.
Natural mechanical and/or chemical damages are most common. These forms of damage result from the nature of things, which must be understood to mitigate their progression and deploy stimulation to remediate when a damage process triggers significant production decline.
Conversely, induced damages are more biological and thermal, and result from the implication of human activity on the reservoir.
A chemical damage can also be induced during stimulation to remediate any of the above stated damage mechanisms. This is possible in cases where the stimulation design did not follow an optimized workflow. For example, the primary reaction in remediating a fines migration problem is the dissolution of aluminosilicates with hydrogen fluoride. However, formation brine cations (Na+, Ca2+) participate in secondary and tertiary reactions that precipitate even more damaging compounds such as calcium fluoride, which is more difficult to clean up anywhere in the reservoir—and even more so in the “near-wellbore area” (5 to 10-ft radial diameter of the wellbore) where the effects of formation damage are most debilitating.
Treatment design is the determination of the type of solution, quality of solution, quantity of solution, and placement of solution to remediate a damage.
- For every damage type discussed above, there is a remedy: Biocides are utilized to eliminate bacteria and related damages, organic and inorganic acids are used to clean up fines migration, clay-stabilizing agents are utilized to keep clays from swelling and flaking, and more.
- For every solution type, there are optimum concentrations, above or below which the desired outcome will not be achieved.
- For every situation, the optimum amount of stimulation fluids needs to be calculated to remediate the near-wellbore matrix of stimulation candidate well.
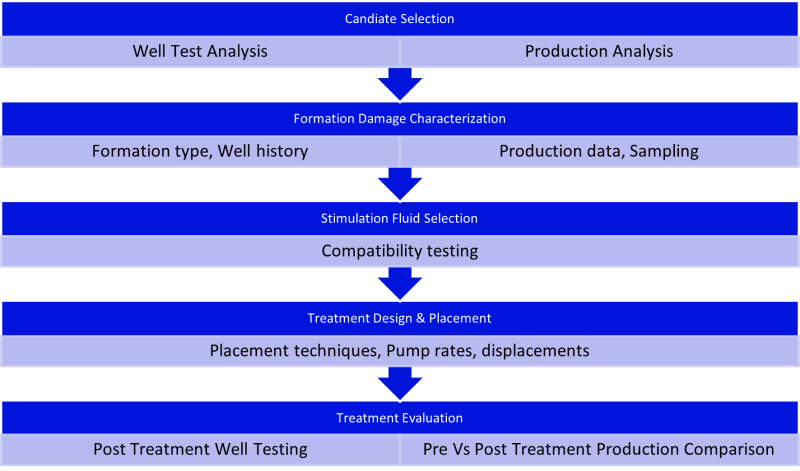
Thus, a treatment design must be optimized by a deep understanding of the problem. In the scenario illustrated by the primary, secondary, and tertiary reactions in fines migration remediation, the primary reaction is the only desired reaction, while the secondary and tertiary reactions are undesirable byproducts. Any action that makes it possible to achieve the primary reaction and interrupt the sequence of reactions thereafter, most especially in the near-wellbore area, is an optimal solution.
Common industry practice to date is flooding the near wellbore with a sweep of flush fluid, which causes the undesired reactions to occur outside the near-wellbore area, where they are less debilitating. However, using more fluids means increasing costs associated with greater pumping and rig time, as well as logistics and other related expenses. In deepwater rigs, where the daily spread exceeds $1 million per day, this can impact strategic decisions. The most optimal solution is interrupting the undesired reactions completely.
In my experience, I’ve seen how reducing pumping/rig time saved nearly $10 million on a deepwater stimulation campaign project.
Additionally, stimulation treatment is often pumped to attend to multiple issues. Even if one of the issues is not of great concern at the time, it is more efficient to put together a fluid train that addresses any other potential issues, to minimize the cost and frequency of interventions.
Fig. 3 illustrates a treatment pump schedule for a well fines migration damage remediation, using a solvent preflush stage to dissolve any existing organic deposits.
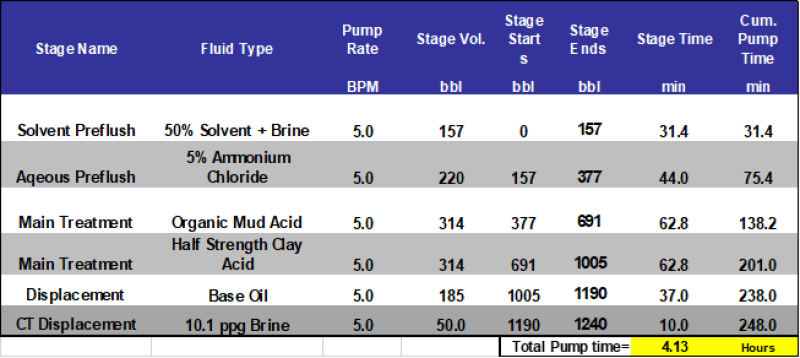
Placement and Flowback
A stimulation design is no good without determining the best method to deliver the fluids across the desired interval. Stimulation fluid placement options range from mechanical “bullheading” fluids directly from the surface through the wellhead, down the tubing to the damaged zone. This method is simple, but has limitations, including
- Inadequate delivery of fluids across the damaged interval. Reservoirs are heterogenous, so if a high-permeability contrast exists in an interval, all the fluids tend to flow preferentially into the high-permeability zones, leaving other sections unstimulated.
- Pushing any existing junk in the tubing into the well.
A coiled tubing can run into the well and can be used to place the stimulation fluids right in front of damaged zones, thereby minimizing fluid loss into “thief zones,” but this placement method is not suitable for “intelligent” completions.
Finally, chemical diverters are a more recent basket of technologies that primarily work by a mechanism in which the total stimulation fluid is divided into stages and pumped with “diverters” placed between the stages.
- The highest-permeability zone takes the first stage of stimulation fluid, which is followed by an agent that temporarily plugs that zone, allowing the next stage of stimulation fluid to “divert” to the next less-permeable zone, and so on.
Stimulation treatments have been performed to remediate damage for more than 100 years, from basic treatments such as hydrochloric acid (HCl), hydrofluoric acid (HF), and mud acids—a combination HCl and HF—to more-advanced chemistries. The success of this effort is based on knowing the reservoir by its original nature, knowing what has happened to the asset from inception to date, understanding how events may have altered the asset, deducing a data-driven damage mechanism, proposing a solution based on the damage mechanism, and deploying treatment to cover the damaged interval.
Managing natural damage phenomena, avoiding induced damage, and enhancing efficiency in stimulation is the formula for getting the most out of oil and gas assets. For optimal results, invest in knowledge: the more you know, the more your stimulation treatment will align with the damage-removal objective. Trying to stimulate a reservoir without the underlying understanding is literally throwing money down a well.