The world’s first full-scale subsea gas compression system is in the final stages of construction and is on schedule to be installed in the Åsgard gas field offshore Norway by year’s end. Norway’s state-owned oil and gas company, Statoil, says that the project is the largest and most complex subsea development ever undertaken in both size and scope and represents a leap forward for an industry that has sought to produce hydrocarbons ever farther from shore for more than a century. With the ability to process and compress gas far beneath the harsh surface conditions of the Norwegian Sea, Statoil envisions a future where surface installations are not required to develop subsea fields. The concept is referred to as the subsea factory, and the company aims to install one capable of producing both oil and gas by 2020. If successful, the Åsgard subsea gas compression project will become the latest milestone in proving that the company’s ambitious objective is possible.
Statoil selected Aker Solutions to design and build the system after determining that a subsea compressor station was economically favorable and had a greater technological potential compared with constructing a semisubmersible platform. By installing a compressor train on the seafloor, “you are closer to the reservoir, which means you can do more with less,” said Svenn Ivar Fure, Aker Solution’s senior vice president of strategy and business development. “You don’t have to take the gas up to a platform and then pump it down again. That provides a lot of advantages,” he said.
Fure also noted that, besides requiring less energy to achieve the same end, a subsea system requires far fewer personnel to maintain and oversee its operation. While subsea facilities do require constant monitoring, it can be done remotely and with far fewer people than necessary for a conventional platform. This provides the operator with considerable saving in regard to salaries, logistical services, helicopter transportation, catering services, and power generation. And, because no personnel work directly on the system day in and day out, the risk for injury and loss of human life is greatly reduced. Additionally, Statoil and Aker Solutions claim subsea compressors involve a simpler build and installation process compared with that of a semisubmersible platform.
Boosting Åsgard
To be installed at a depth of approximately 850 ft and scheduled to start up early in 2015, Statoil’s USD-2.7-billion subsea gas compression system will sustain natural gas production from the Midgard and Mikkel reservoirs, two of the largest resources in the Åsgard field. The subsea template will consist of two identical compressor trains producing in parallel and will be used to recover an additional 28 billion m3 of natural gas and 14 million bbls of condensate from the field, equal to 280 million BOE.
First production at the Åsgard field, 124 miles offshore Norway, began in 1999. Current production is supported by two facilities, an oil production vessel, Åsgard A, and a semisubmersible, Åsgard B, for gas production. Produced condensate is stored in a tanker, Åsgard C. The decision to move forward with gas boosting was made because Statoil projects that, within the next few years, reservoir pressure will become too low to maintain a steady rate of gas flow, yet a large volume of technically recoverable reserves remain in the field’s reservoirs.
Some of the project’s equipment has already been installed on the seabed, including the manifold station that will direct the flow of gas and the enormous steel frame that will protect the compressors. Measuring 65 ft tall, almost 150 ft wide, and more than 245 ft long, the compressor frame takes up almost the same area as a soccer field. Remaining work consists of sailing out two compressor trains later this year and connecting all the pieces for the first time. “We have qualified the components. We have built the components, and now we are starting to put the components together and testing it all as a system,” said Rune Mode Ramberg, Statoil’s chief engineer of subsea technology and operations. “It is a big puzzle that is coming together.”
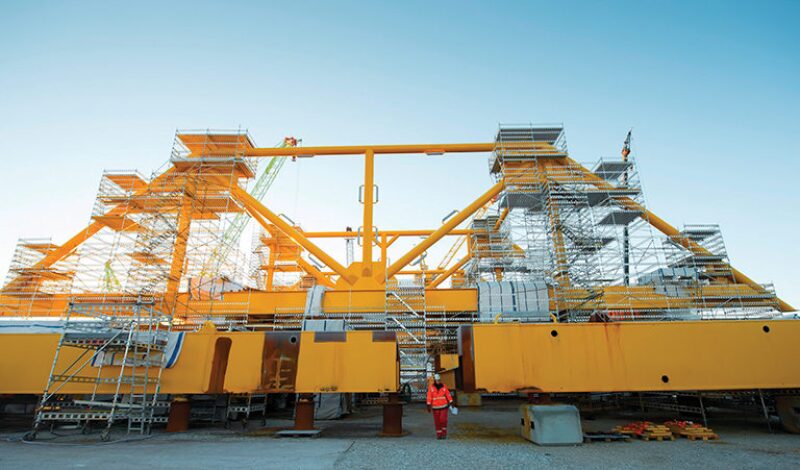
Each train at the Åsgard system comprises approximately 10 different modules that include gas processers, coolers, scrubbers, pumps, and compressors. As the gas leaves each wellhead, it travels through a flowline and into a manifold, where it is directed into a larger pipeline that takes the gas into the compressor trains. At that point, the liquids are separated from the gas. The dry gas is boosted using the compressor, and the liquids are pumped to Åsgard B.
Subsea Reliability
To achieve a high degree of system reliability, Statoil commissioned Aker Solutions to build not just two compressor trains, but three. The first compressor train is submerged at a test facility while it undergoes verification testing before being sent offshore. The second compressor train will also be submerged and subjected to testing. The first two trains will be installed at the field, and the third train will be kept onshore to provide Statoil with replacement modules. Ramberg describes the physical process of compressing gas subsea as not too different from what happens on a platform’s topsides or at an onshore facility. “The big difference is the way the components are put together,” he said. “That is different from what you would have on a platform because (on a platform) we can modify the units instead.”
The idea for a subsea system is that, while the critical components of the system are connected together, they work independently of one another, so that, if one module fails, it can be replaced without replacing the entire production train. The design life for the Åsgard compression system is 25 years, and Statoil wants the major components to operate 2 to 3 years before requiring maintenance intervention.
Once operational, the compressors will increase pressure to compensate for the steady decline in natural pressure. If one of the trains fails, the other will pick up some of the slack and production can be maintained at up to 70% of the full flow rate. At the onset, only one compressor train will be needed to provide the required amount of compression and boosting capacity.
New Subsea Technology
Because of their proximity to the existing facilities, the 11.5-MW subsea compressors will be powered from the existing generators aboard the field’s oil production vessel, Åsgard A. A new 880-ton module with high-voltage electrical equipment has been installed onboard the vessel to run the compressor station. For future discoveries, where there may not be a nearby floating facility to host a power unit, operators likely will rely upon emerging long-distance power transmission technologies to deliver high-voltage electricity from shore-based stations.
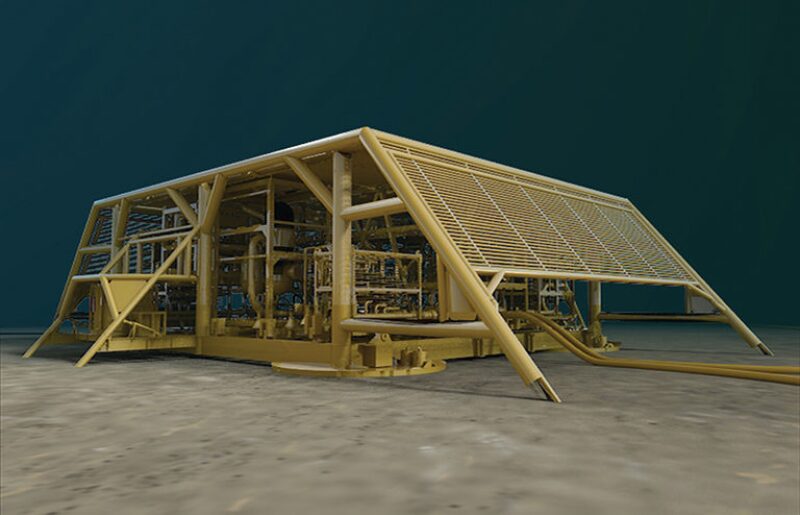
Among the technologies being put to use in a subsea environment for the first time at Åsgard is the compressor’s rotating equipment. The electrical motors that will turn the rotors are the largest ever installed subsea, and, as the natural gas flows into the system, it is compressed by rotor blades elevated and held in place with magnetic bearings. Before Åsgard, Ramberg said that this type of magnetic-levitation technology has only been used effectively in onshore and offshore surface facilities where workers can easily access and recalibrate the machines as needed. “We are using a lot of sensors to measure the distance between the rotor and the stator to detect an imbalance in the system,” he said. “If there is an imbalance, the operators can try to avoid problems by manipulating the electromagnetic field.”
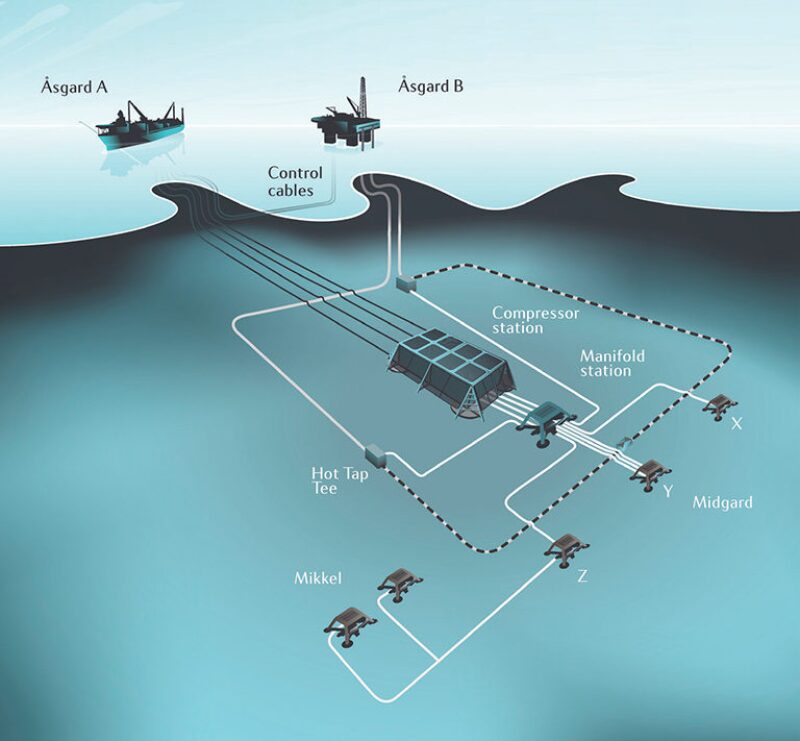
The concept of producing hydrocarbons hundreds or thousands of feet beneath the water’s surface raises new questions about environmental safety. One of those questions is: How to know if gas is escaping from the system? To address concerns over hydrocarbon leaks, the subsea system at Åsgard is being equipped with environmental monitoring sensors that will use acoustics to detect the sound of gas or other liquids venting into the water. Statoil says that it is “the most sophisticated leak detection system there is.”
Other integrity management systems will provide the ability to monitor the various components and their condition around the clock using a high-bandwidth fiber-optic communications network to deliver large amounts of data in real time. In the event of a system shut down or failure of any kind, Statoil has an onshore support facility and contracted a specialized vessel to provide immediate support for replacement or repair operations. To reduce the number of moving parts and increase response reliability, all of the subsea compressor’s valves at Åsgard will be activated using an electrical control system instead of a hydraulically controlled system—a notable achievement in itself, according to Ramberg. “This is the first time that a subsea system like this is totally electric,” he said.
Ormen Lange and Beyond
The Åsgard subsea compression project is the culmination of more than 15 years of subsea research and development by Statoil and its partners, beginning in 1997 with the company’s first installation of subsea pumps. As Statoil pursues the ultimate goal of installing the world’s first subsea hydrocarbon plant, Ramberg noted that the company needs time to gain the experience of operating the subsea compressor at Åsgard as it develops more complex subsea systems for the future. “We are moving step by step toward the subsea factory by increasing the capabilities of each building block,” he said.
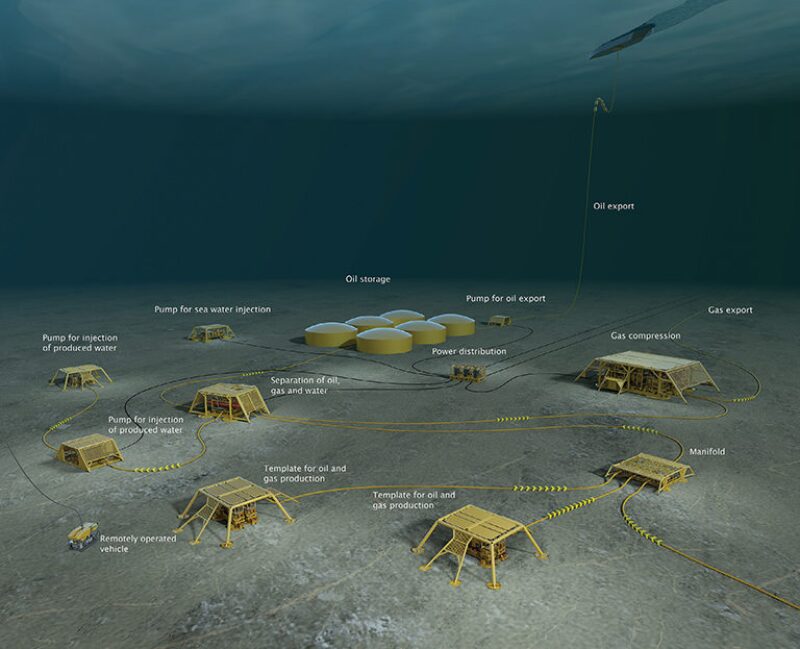
He added that some of those building blocks included inside Åsgard’s compressor trains were first qualified through the Shell-operated Ormen Lange pilot program, of which Statoil is a nonoperating partner. Statoil had responsibility for technical qualification of the Ormen Lange compressors. Ormen Lange is Norway’s second-largest gas field, and, like Åsgard, the field is predicted to begin losing pressure in the coming years. Shell is evaluating whether to build a tension leg platform designed to host more than 32,000 tons of equipment and materials on its topsides or to move forward with a subsea facility capable of the same compression capacity but that would weigh approximately 8,000 tons.
In some respects, the Ormen Lange compression project could prove to be more complex than the Åsgard subsea compressor project. The Ormen Lange pilot system is submerged and operating at a test facility in Nyhamna, Norway. But once a full-scale system is installed, it will be operating at a greater depth of 2,950 ft. and approximately 75 miles from its onshore power source, more than twice the distance between the Åsgard subsea compressor system and its power source. Building upon its experience with both systems, Aker Solutions is working with Statoil, Shell, and others to study the use of subsea compression on greenfield gas projects and to debottleneck existing subsea gas fields. Some of the area’s operators are expressing interest in deploying similar systems, including offshore Australia, eastern Africa, India, and west of the Shetland Islands in the North Sea. “The Åsgard and Ormen Lange projects have attracted a lot of attention from international oil companies with similar types of issues,” Fure said.
If subsea compression technology is adopted on a wider scale, Åsgard and Ormen Lange projects might prove to be the exception rather than the rule, in regard to their size and volume of gas compression. The industry, Fure said, is looking for more-compact solutions that are lighter and cheaper than the first-generation systems. “Going forward, I think we will see a few of these large projects, such as Åsgard and Ormen Lange are, and a lot the smaller and midsized ones,” he said.
To miniaturize current subsea processing technology, more work will be needed to simplify the power units, remove as many parts as possible without losing efficiency, and standardize components to reduce manufacturing costs. Representative of this trend is Statoil’s next compression project at its Gullfaks field, where it plans to install two 5-MW subsea compression units. For this project, Statoil selected OneSubsea to design subsea gas boosters on the basis of technology derived from multiphase subsea pumps.
For a full-scale subsea factory to become a reality, Statoil and its offshore partners must combine a suite of technologies that have been qualified through other projects and deploy a system that is fully independent of a surface structure. For areas such as the Gulf of Mexico or offshore Brazil, the systems must be built to withstand the extreme pressures of deep water. In the Arctic, the challenges will involve mitigating the very serious risks posed by ice floes and icebergs at shallower depths. For the concept to work in such an environment, companies likely will have to take the extra precaution of excavating deep pits in which to place the processing components and wellheads to avoid being scoured off the seabed by slow moving chunks of ice. Ultimately, the exact requirements for each subsea factory will be based on field economics.
Regarding human resources, Statoil is using the Åsgard subsea compressor project and other ongoing subsea projects not only to qualify the components, but also to train its staff on how to maintain and operate the systems optimally. Statoil also wants to integrate more advanced subsea systems into its normal operations, which it believes will increase its personnel’s familiarity with the technology.
Another issue that needs to be resolved is how to increase the capability of subsea oil separation. Subsea bulk separation of oil, gas, and water has been successfully demonstrated by a number of companies but remains a young technology. Subsea factories will require much more sophisticated processing than what is currently available. Statoil is interested in units capable of two and three stages of oil separation to be able to reintroduce clean produced water directly back into the environment without transporting it beyond the field.