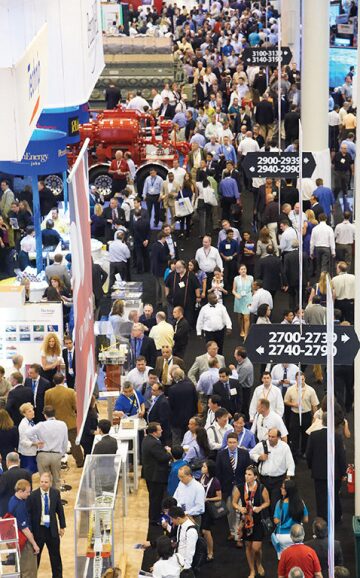
This year’s Offshore Technology Conference (OTC), held 6-9 May in Houston, reflected the offshore oil sector’s health and energy, with attendance hitting a 30-year high and the event attracting top industry names from around the world. The globe’s largest offshore industry event attracted 104,800 people, the second highest in show history and up 17% from last year. Exhibitors represented 40 countries.
Panel sessions, keynote speeches, and technical papers spanned the breadth and depth of the oil and gas industry.
At one panel session, energy ministers and national oil company senior executives shared their perspectives on how the industry should adjust to address energy challenges as well as how the role of companies and governments should change to shape the future. The panel was moderated by Gamal Hassan, chief executive officer of ADHIG and OTC Program Chairman.
The panel began with Jose de Vasconcelos, Angola’s Minister of Petroleum, who highlighted the connection between the need for energy and economic and social development. The industry faces many challenges in the quest to obtain energy security, which he defines as an equilibrium between supply and demand. Several challenges must be addressed to meet production needs: technologic, environmental, regulatory, and financial. Angola, he said, will maintain a permanent dialog with other producers to develop a common approach on energy and energy-related issues.
David Ramsay, Minister of Industry, Tourism, and Investment, Northwest Territories, Canada, said that the role of government is to ensure that resources are “developed in a manner that brings economic development while ensuring the environment and its benefits” and at the same time working with industry and regulatory agencies to achieve this. Ramsay said that there is a renewed interest in the Arctic and northern Canada with opportunities onshore and offshore. The Canadian government is building infrastructure to assist in the transportation of fuels.
Petrobras Chief Executive Officer Maria das Gracas Silva Foster said that exploration is a priority, and major investments that have been sustained over several years have resulted in the development of a diversified and competitive goods and services. Petrobras has benefited from a close association with universities to facilitate research in exploration and development, and the recent major discoveries as well as monetization of these reserves are a direct result of the investments in research and universities.
Carlos Morales-Gil, general director of Pemex Exploration and Production, noted that increasing energy demand calls for greater focus on enhanced recovery, tighter formations, heavier oils, deeper waters, and colder climates—all amid increasing regulations. Demand for energy is increasing around the world because of growing populations and economies, he said.
China: The Future May Be Offshore
Agility Needed Across Project Mix
In a panel session on agile project management, Dick Westney, founder and director of the Westney Consulting Group, said that stage-gate project management methods with heavy front-end loading (FEL) of technical and business objectives may be impeding needed project agility.
The growth in project scope and complexity has pushed megaprojects from the USD 1 billion range of a few years ago into the USD 10 billion range today. “Projects get bigger and they take longer, when you try to optimize the situation that are 10 years down the road,” Westney said. “Maybe we’re actually spending a lot of time and energy that’s not all that well spent. Maybe we need to be more agile.”
While FEL has benefited industry projects, it may have become excessive. “We have a culture in the project management community of, ‘Hey, I’m going to resist change, once I’ve got my scope, once I’ve got my plans. I’m going to pull up the drawbridge,’” Westney said. “Part of the problem is that everybody says, ‘I followed the process.’ And that becomes an excuse for whatever happens.” He said that the needed level of project agility should reflect a balance between conventional best practices and complete flexibility.
Eric Namtvedt, president of FloaTec, contrasted two large tension-leg platform projects that his company had worked on: Chevron Big Foot in the Gulf of Mexico and Petrobras Papa Terra in Brazil’s Campos basin.
Big Foot has taken a “very conventional approach,” Namtvedt said. The operator is directly managing all phases of the project, which involved large FEL and, beginning in 2009, several years of front-end engineering, design, and construction. First production is anticipated in 2014.
On Papa Terra, the operator signed an engineering, procurement, and construction contract with FloaTec in 2009 to design, build, maintain, and install the tension-leg wellhead platform, which FloaTec will operate for 3 years. The heavy-oil project is slated to start production this year.
While the approaches are different, project management in both cases is cohesive, Namtvedt said. “I am not going to value judge and say one is better than the other,” he said. “It isn’t a one solution; there isn’t one answer.”
Agility is necessary in any case, and Namtvedt offered a number of suggestions for achieving it within the project structure. The guidelines are as follows:
- Adapt but accept givens.
- Demonstrate insight, while listening to the client.
- Where appropriate, innovate.
- Build trust.
- Include the younger generation on the project team.
Dennys Campos, manager of integrated project management (IPM) operations in Brazil at Schlumberger, discussed different IPM models used in two Brazilian offshore projects. One was an integrated services model designed to reduce the number of contracts and interfaces, simplify the project structure, create synergies, and reduce nonproductive time. The other was an alignment process in which the contractor project personnel were colocated inside the client’s office. Both models proved successful in execution and exemplify agility in action, Campos said.
Sandeep Kuhrana, manager of development in the major projects group at Noble Energy, said that agile project management requires “always anticipating the need for change.” Project developers must recognize how their development and marketing needs overlap with the needs of partners and suppliers and governments and communities, he said.
Stuart Wheaton, manager of group development and operations at Tullow Oil, said that successful projects are built around clarity of purpose, performance management, people, culture and values, and decision rules.
Gazprom Moving Forward on Arctic Offshore Gas
Subsea Oil/Water Separation Starts
Stakeholder Issues Present Challenge
“Integrating stakeholder interests is the global challenge we all face in our industry today,” said Francisco Vacas, manager of health, safety, environment, and quality at Eni US Operating Company, at a panel session on the integration of stakeholder interests in the global offshore industry.
Stakeholders play “a pivotal role in the success of our activities at our contract development sites,” Vacas said. For the benefit of stakeholders, he said that Eni had shut down production operations in a Nigerian swampland to help authorities combat bunkering, the practice of thieves breaking into pipelines to steal oil. In another country, Eni has built power plants to convert associated gas from oil production operations into electricity for local communities. This and other measures have enabled Eni to reduce gas flaring companywide by more than 50% between 2007 and 2012.
Speaking about the US Gulf of Mexico (GOM), Vacas said that Eni has made “a true commitment to search for the best options to ensure safety for all our stakeholders. We believe that regulatory compliance alone is not what our stakeholders expect from us.”
Doug Morris, chief of regulatory programs at the US Bureau of Safety and Environmental Enforcement (BSEE), discussed his agency’s new regulatory approaches in the aftermath of the Macondo blowout. The regulations take a hybrid approach that combines prescriptive and performance-based requirements, and the agency is taking a lifecycle approach toward the regulation of critical equipment, he said. BSEE will rely increasingly on independent third-party review and verification of cutting-edge technology, Morris said.
“We have become more engaged in the development and review of domestic and international standards,” Morris said. “This will allow us to fill gaps in the current regulatory framework and also to determine if additional regulations are needed.” The agency is also encouraging the development and improvement of offshore safety culture in outer continental shelf operations, he said.
Regulations issued since Macondo include drilling safety rules in 2010 and 2013, and safety and environmental management system (SEMS) rules in 2010 and 2013 (SEMS II). BSEE also issued the first requirements on production safety systems issued since 1988 and will issue a major new rule on blowout preventers and well control later this year, Morris said.
Charlie Williams, executive director of the Center for Offshore Safety, discussed the SEMS and SEMS II rules. The rules work as a nontraditional, performance-focused tool for integrating and managing offshore operations to enhance safety by reducing the frequency and severity of accidents. “This is really process safety at another level, because this is process safety where the process is actually managing your whole business,” he said.
The offshore industry uses a large number of contractors, by some estimates more than 5,000 in the GOM alone, Williams said. Since Macondo, “all of our stakeholders … became quite interested in how we manage the relationship between operators and contractors,” he said. As a result of the SEMS rules, operators must now assure the government that all of their contractors have a good safety management vehicle and that contractor staff is trained and capable of performing its assigned work, Williams said.
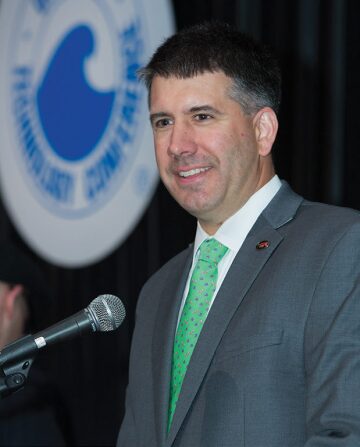
Erik Milito, director of upstream and industry operations at the American Petroleum Institute (API), said that the government is a stakeholder in various technical programs of the Center for Offshore Safety, the International Association of Drilling Contractors, and the API—including API’s standardization and certification programs. At the same time, he noted that these organizations are stakeholders in the government’s safety initiatives. “It’s really critical and beneficial for the government and industry to work together,” he said.
George Nowack, project manager for the German sector of the Nord Stream pipeline, a line crossing the Baltic Sea that links Russian natural gas supplies to Germany, discussed Nord Stream’s management of stakeholder issues during line construction. Economic, environmental, and political opposition to the project emerged from a number of sources across Europe. Nowack said that meticulous regulatory compliance, swift communication response, open community dialogue, and the efforts of an experienced, multidisciplinary management team defused opposition to allow project completion and startup in late 2012.
Saudi Aramco Discusses New Technology Strategy
Technology Standardization Remains Elusive
Global Technology Delivers Value
As the oil and gas industry seeks to meet future energy demand, a number of the technologies that will drive that advance may come from other industries. “There is a tremendous array of technologies across all the industries that we support that can enable us to do really great things inside the oil and gas industry,” said Mark Little, chief technology officer and senior vice president at General Electric, about technology developed in his company within other industrial sectors. Little made his remarks in a panel session on value creation through global technology.
Advances in cancer imaging could bring improvements in oil and gas seismic exploration and facility inspection technologies, he said.
Advanced manufacturing technologies enable prototypes to be built “in the blink of an eye,” Little said, which greatly speeds the development of new materials and products for industrial applications while significantly lowering costs. Tool development is among the areas that could strongly benefit, he said.
The polymer-carbon composite material from which the blades on the latest jet aircraft engines are built could be used to design new composite risers for offshore oil and gas facilities, Little said. Nanotechnology combined with advanced manufacturing has enabled surface coatings to be developed with “corrosion- and erosion-resistance that’s really remarkable,” he said.
High-performance computing is enabling modelers of components and systems to see “levels of detail … we could just not see before,” reducing the modeling and experimentation time needed to develop new components and systems, Little said.
Advances in software and analytics applied to huge networks of operating equipment data are enabling the development of diagnostic and prognostic tools that can detect process disruptions before they happen and allow operators to improve their planning of how equipment is used, Little said.
Gerald Schotman, executive vice president of innovation and R&D and chief technology officer at Shell, discussed a number of new technologies the company is using. The Bully Rig, designed by Shell and Noble, is able to reduce drilling time and enhance safe operations on ultradeepwater wells, he said. Shell is also working with Transocean to develop its seventh-generation offshore drillships, he said.
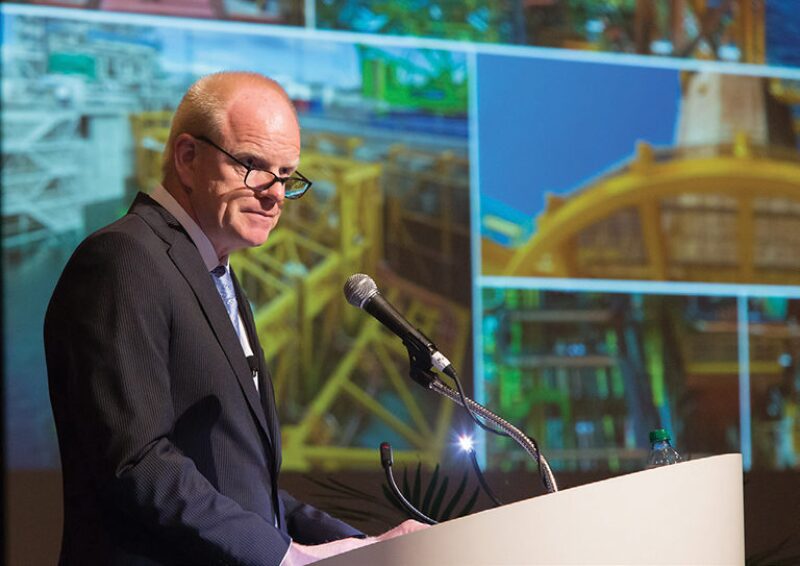
The company is planning to use subsea boosting and compression at the Ormen Lange project offshore Norway, Schotman said, which will mark the industry’s first use of subsea compression.
To enhance rig safety, Shell has developed an emergency separation tool placed in the riser above the blowout preventer (BOP), Schotman said. When activated, the tool severs in milliseconds any tubing that might be located across the BOP, with minimal deformation. The equipment drops into the well and clears the BOP sealing rams, which becomes a secondary mechanism to ensure BOP closure. Shell also has an insert device that is placed below the BOP, he said. The device can collapse the tubing, while maintaining casing integrity, to stop or substantially reduce an uncontrolled well flow, should the BOP fail.
Schotman also discussed the advanced life of field seismic that Shell is using at its Parque das Conchas production complex offshore Brazil and instantaneous 4D seismic, a quick, low-cost method for observing fast reservoir changes.
David Eyton, group head of research and technology at BP, discussed company research and newly developed technology. BP’s Well Advisor uses novel sensors and wired pipe to integrate data with predictive software tools and processes to help operators improve real-time decision making. The company is teaming with university researchers to develop hydrogen-resistant steel to withstand hydrogen embrittlement in deepwater pipe. Another research initiative is in bioscience to develop biological methods of preventing biosouring, the buildup of hydrogen sulfide, in reservoirs.
Megaprojects Bring Broad Impact
A panel session on megaprojects stressed the importance of the industry handling these projects skillfully and striving for improvement in execution.
Clive Vaughan, chief executive officer for upstream at Foster Wheeler, said that megaprojects have been defined as projects costing more than USD 1 billion. “It’s probably greater than that today with inflation,” he said. “These projects can have a significant impact on communities, countries, environments, and the public. They typically have a significant number of stakeholders.” The stakeholder issues, Vaughan said, add challenges of complexity that go beyond project size.
Looking across industries, Vaughan said that more than 80% of megaprojects fail to deliver on time and within budget. “The sheer size and the timelines involved” differentiate megaprojects from others, and health, environmental, and safety issues should always be a top priority, he said.
Megaproject risks can be similar to other projects, but “what is different is the challenges,” Vaughan said. “A 10% overrun on a USD 100 million project is significantly different than the impact of the same percentage on a USD 1 billion project.” Recruiting is critical to success, and with the industry workforce stretched, it is a challenge.
Vaughan closed the session by asking a question, which he did not answer: “Are some projects too big, so that they produce diseconomies of scale?”
Rob Kretzers, executive vice president of projects and technology at Shell, said that the resources being developed in megaprojects are often remote, possess high levels of H2S and CO2, and lie in high-pressure, high-temperature reservoirs.
Notwithstanding the industry’s successes with megaprojects, Kretzers said he was concerned with “the quality of our work, a problem that was not prevalent 10 to 20 years ago. “We have leaking wells and pressurized equipment,” he said, and it is often detected only as project ramp up or after startup. “We need to fix that very quickly,” he said. The industry should recognize “the same need for quality as we have for safety.”
Kretzers also discussed nontechnical project risks. “In Africa, the local content requirements are ever growing, and rightfully so,” he said. To meet this challenge, Kretzers recommended “that we as an industry work more jointly together than as individual contractors and international oil companies.”
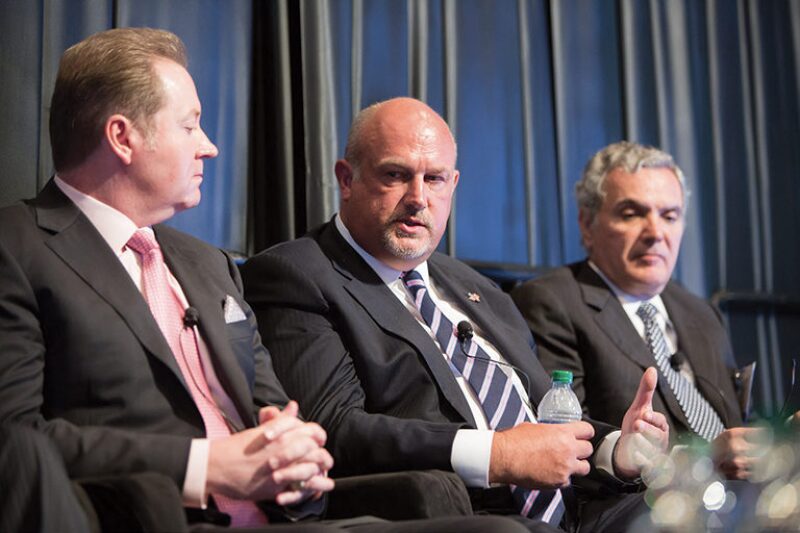
Lee Tillman, vice president of engineering at ExxonMobil Development Company, discussed Arctic oil and gas. “There is no doubt that the Arctic is a poster child for megaprojects,” he said. “But our industry is confronted with one very fundamental question. Can we explore, develop, and produce in the Arctic responsibly, ensuring high levels of safety, environmental standards, as well as integrity? From the ExxonMobil perspective, our answer is an emphatic yes. And that’s based on essentially 90 years of experience in the Arctic.”
Luc Messier, senior vice president of projects, supply chain, and aviation at ConocoPhillips, spoke about his company’s major projects, including the Canadian oil sands and the Curtis Island LNG development in Australia. “The successful projects always have good engineering up front,” Messier said. Good relations and collaboration with major project contractors, he said, is also a key element. ConocoPhillips is reducing the cost of the Australian and Canadian projects through modularizing the construction. Messier also noted the potential of manufacturing approaches to the development of major North American shale projects.
Carlos Tadeu da Costa Fraga, an executive manager at Petrobras, said, “Megaprojects are ‘mega’ because they have mega investment. …. They are always complex—sometimes technically complex, sometimes complex because of other reasons. But in our opinion, more important than that, they are ‘mega’ because they have much, much higher stakeholder expectations.” When industry megaprojects fail to make their final schedules, Fraga said, almost 80% of the time, it is because of stakeholder-related issues.
JPT staff members Stephen Rassenfoss, Abdelghani Henni, Robin Beckwith, Trent Jacobs, Mika Stepankiw, and John Donnelly contributed to this report.