The rapid growth in the development of unconventional shale resources has changed business-as-usual for onshore production equipment manufacturers and suppliers. Bill Bowers, vice president of production equipment at Valerus, provided an overview of trends in surface facilities during a luncheon hosted by the SPE Gulf Coast Section’s Projects, Facilities, and Construction study group in April.
Bowers said that shale plays have changed large-scale development in several ways. Conventional exploration and development are characterized by high geologic risk, complex reservoirs, and thin laminated beds. Success is determined by geophysical technology, risk assessment, reservoir optimization, and customized surface facilities. Geologists, geophysicists, and reservoir engineers are the key players.
Unconventionals are characterized by lower geologic risk and net pay thicknesses from 100 to 400 ft. Execution, speed, and efficiency of capital deployment in drilling, completions, and infrastructure determine success. The development mirrors industrial-scale projects, and the key players are facilities engineers and supply chain, safety, environmental, and operations personnel.
Fig. 1 illustrates the accelerated pace of development in shale projects. The time required from stake to completion typically takes from 6 to 12 weeks, Bowers said. The time required from completion to hydrocarbon sale is critical in the success of the project. At an initial production rate of 500 BOPD at USD 93/bbl, each week represents USD 325,000 per well in incremental revenue.
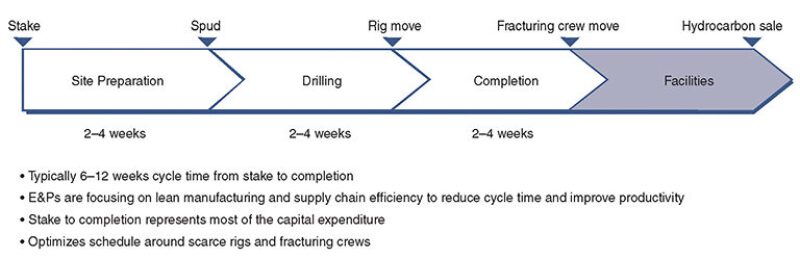
Exploration and production companies are focusing on lean manufacturing and supply-chain efficiencies to reduce cycle time and improve productivity. Table 1 compares the characteristics of onshore conventional and unconventional resource production equipment planning and management.
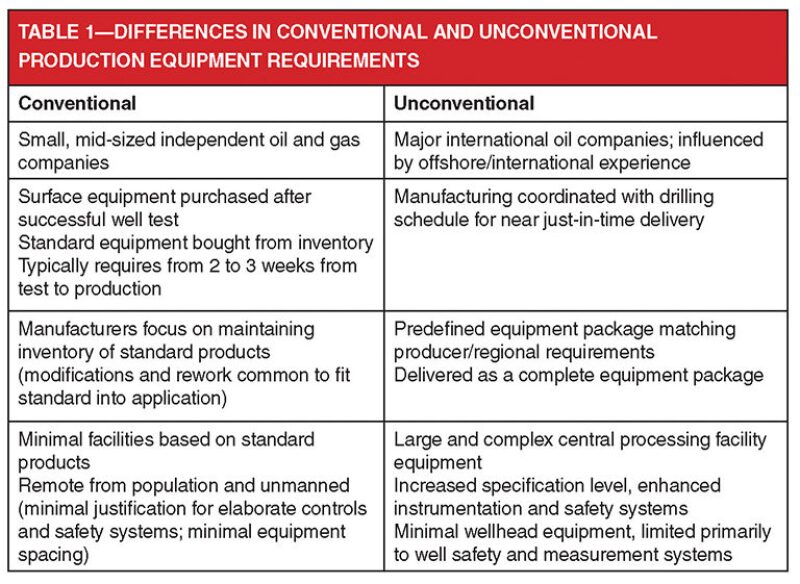
The increased use of packaged, skid-mounted equipment translates into improved quality control and a decrease in the time required for installation, Bowers said. However, the skid-mounted equipment costs more than the installation of equipment, such as a separator, on prefabricated concrete pads followed by the addition of instruments. He said, “Field labor hourly costs are less than manufacturing labor costs.”
Intangible advantages of the skid-mounted equipment include the elimination of the loss of the instrumentation in the field, late deliveries of parts or instruments, more consistent design of the equipment, and safety.
The demands on equipment and service providers reflect the changing needs of operators in the unconventional developments:
- Packaged equipment increases the demand for shop space and manufacturing man-hours and requires different manufacturing skill sets
- High-volume production requires implementation of manufacturing efficiencies
- Manufacturers’ mentality must shift from fabrication to lean manufacturing
Bowers said that manpower and know-how issues also present challenges. Limited trained manpower and field logistical costs create pressures on facilities design similar to offshore projects. Measures to deal with these pressures include shop-packaged equipment to minimize field hookup time, know-how requirements, and redundant safety systems to minimize personnel safety and environmental risks. Remote monitoring is becoming the norm, and remote operations are increasingly being implemented.
Manufacturers and service providers are recruiting personnel from a limited pool of highly trained technical services staff. “We all have to provide similar training and are taking trained employees from each other,” Bowers said.