For years, the oil and gas industry has used autonomous underwater vehicles (AUVs) for simple tasks such as underwater surveys and inspection. However, because of their technical limitations, AUVs have not been able to compete with remotely operated vehicles (ROVs), which are already standard equipment for most offshore projects.
While the market for AUVs remains modest, they are being used in deepwater oil and gas plays around the world. “AUVs are not a commodity yet, but they are getting there,” said Richard Mills, AUV sales manager at Kongsberg Maritime. He added that one Kongsberg customer has a long-term AUV contract with Petrobras for the use of two vehicles offshore Brazil.
High-resolution large-area seabed surveys are the oil and gas industry’s primary use for AUVs today, said Mills. Although ship-towed sonar arrays have been used for decades in ocean floor mapping, the sensors cannot reach the absolute bottom in many cases.
On the other hand, AUVs can glide just a few meters above the ocean floor to create higher-quality images of the seabed and subsurface.
Despite some unique advantages, the power, communications, and launch-and-recovery systems of AUVs will need improvements in order to make the leap from rig jewelry to a trusted tool.
Extended Missions
To fully take advantage of an AUV’s tetherless capabilities, users must be able to operate the vehicle for longer periods of time before needing to bring it to the surface for recharging or recovery. Without advances in this area, the nagging question will be, “Why not use an ROV instead?”
Liquid Robotics’ Wave Glider is an extreme example of AUV endurance. Able to harness energy from the movement of water and from a floating solar panel on the surface, Wave Gliders can travel for months without human intervention. They have even crossed oceans by themselves. But these vehicles travel very slowly and do not operate more than 100 ft below the surface.
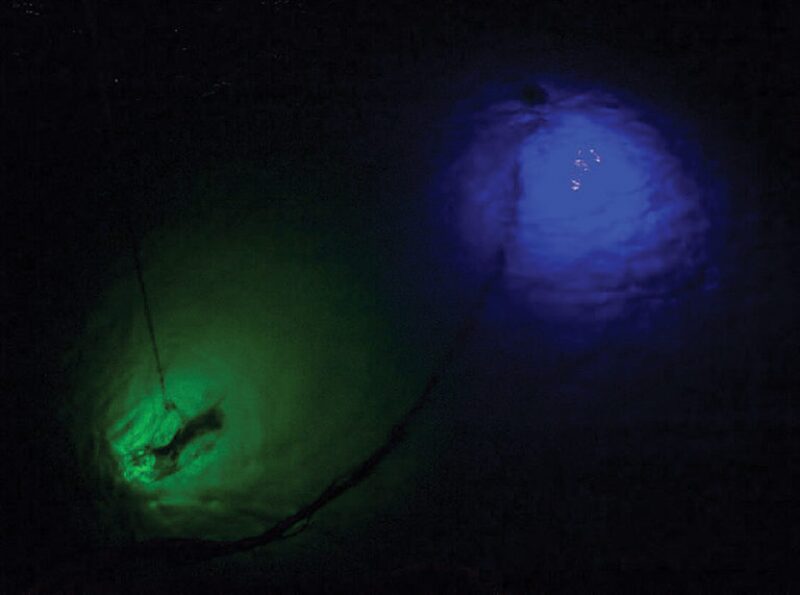
Propeller-driven AUVs, the main class used for oil and gas operations, have more power-intensive propulsion methods and tend to be much heavier than gliders. The most common power sources for light work-class vehicles, such as Kongsberg’s torpedo-shaped Hugin line, are rechargeable lithium ion batteries.
Each year, new variations of lithium-based batteries are developed and tested, each with slightly better chemistry, but so far, they have offered only incremental improvements.
Daniel Gomez-Ibanez, an engineer at Woods Hole Oceanographic Institution (WHOI), said that most propeller-driven AUVs have functional battery lives of 1 to 2 days, even though the total battery life of some are listed as long as 60 hours.
While scientists strive to develop batteries that hold greater charges, developing better recharging methods could be a more fruitful way to extend the length of time vehicles spend underwater.
“The biggest challenge is streamlining the recharging process so it can be ignored most of the time. Present day AUVs must be taken out of the water to recharge, but future AUVs will recharge autonomously underwater,” said Gomez-Ibanez.
Solar-powered AUV recharging stations have been used by oceanographic researchers, but the technology is not yet commercially feasible.
The amount of battery power a vehicle requires during idling is the main limiting factor that AUV manufacturers face in their pursuit for longer endurances. This is called hotel load.
Theoretically, an AUV that uses energy efficiently while idling can take breaks to squeeze out extra mission endurance, but improvements in power efficiency are needed first. “Most AUVs now have a high idle power requirement, so that limits the calendar time that they can be out,” said Gomez-Ibanez.
Another complication of AUVs that must be overcome is their current launch-and-recovery methods, which can be cumbersome and time consuming.
Kongsberg’s Hugin AUVs are lowered into the water with a hydraulic ramp and are recovered using a tow line, which must be connected to a winch by a pneumatically launched grappling hook. Other models use cranes. Support vessels may have a difficult time with these recovery processes if weather conditions are poor on the surface.
James Jamieson, an engineering manager at Subsea 7, presented a paper titled “Effective Launch and Recovery of Autonomous Underwater Vehicles” at the 2015 Offshore Technology Conference. The paper detailed a launch and recovery system allowing an AUV to park itself in what is effectively an undersea garage, where it may safely wait once its missions are over.
The AUV is lowered by a winch and basket to the seafloor, at which point it can be activated and perform its prescribed mission. At the end of a task, the AUV is programmed to locate and return to the basket, where it will remain until it receives further instructions. This is especially useful if an AUV is forced to abort a mission early for technical or environmental reasons.
The authors propose a technique called “lobster potting,” which involves a cyclical deployment and recovery of vehicles at different locations for regular monitoring of subsea facilities. There are also plans for a seabed-hosted system, which allows a support vessel to supply power and wired communications to the basket, thereby enabling extended-length dives and data mining without bringing the AUVs to the surface.
Subsea Communication
Although they do not depend on a tether for power, AUVs still rely heavily on outside support for navigation. The first AUVs required scientists to lay networks of transponders on the seafloor before any operation could take place. Vehicles would have to triangulate their locations relative to these transponders.
Today’s vehicles can be monitored and located from support vessels, as long as the AUV remains within a range. This is called ultrashort baseline navigation.
“Navigation underwater is always a big problem,” said Norman Farr, a WHOI engineer. “There is no underwater global positioning system (GPS), so you do need some method to tell a vehicle where it is, or tell you where it is relative to the surface, based on satellite-based GPS data.”
The support vessel, which is able to access GPS because it is on the surface, communicates navigational information to the underwater vehicle using acoustic communication. This means that any pipeline survey, which is a maturing use for AUVs, must involve either a trailing support vessel or transponder modules laid out on the seafloor along the proposed route to assure accurate navigation. To further complicate matters, each transponder has a finite battery life.
Acoustic communication is the most commonly used method for AUVs because of the long range it allows underwater. The downside to this method is that sound waves cannot transmit large amounts of data.
A recent WHOI development called underwater omnidirectional optical communication solves the problem of insufficient bandwidth in AUV communications. Instead of sound, light is used to carry information to and from the vehicles, enabling a significant increase in bandwidth.
The mechanism is similar to the infrared system used in a television remote control, which does not require precise alignment to link the sender and receiver. Omnidirectional modems emit a cloud of light, rather than a narrow beam, thus making it easy for mobile AUVs to connect and stay connected without an aiming and tracking system.
A major use for high-bandwidth communication in an AUV context is the sending of real-time video back to a support vessel. Another is wireless data offload from seafloor sensors. However, optical communication comes with a severe disadvantage: an even shorter communication distance than that of acoustic.
Yet Farr said the technology is practical for operations near seafloor infrastructure. Until recently, optical modems were not commercially available; however, acoustic communication firm Sonardyne is selling an early model.