The long-term effects of respirable silica dust have been long known to various industrial sectors, from concrete construction and road building to the manufacture of glass and ceramics. As hydraulic fracturing operations have become a significant part of oil and gas portfolios, companies have begun paying additional attention to the safety of workers exposed to the dust that emanates from large volumes of the sand used.
In March 2016, the US Occupational Safety and Health Administration (OSHA) announced a revised standard that cuts in half the permissible exposure limit (PEL) per cubic meter of air, making employers implement controls that limit worker exposure and access in high-silica areas.
The regulations provide some challenges, but a closer look shows that the oil and gas industry anticipated the effects of crystalline silica as well as the effects of the new regulations. Operators and sand companies have a host of technological approaches to deal with the realities of this harmful dust.
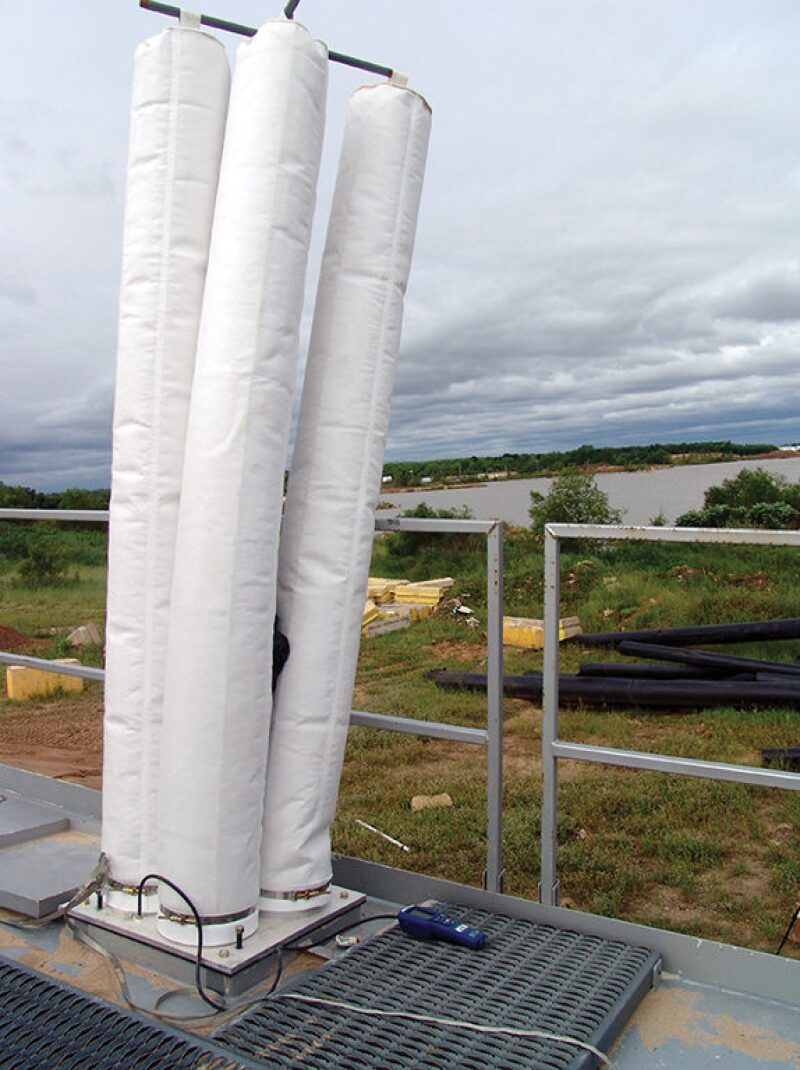
OSHA Regulations
Crystalline silica is used in a wide variety of applications in several industries. It can be used as a filler in plastics, rubber, and paint, and as an abrasive in soaps and scouring cleaners. For oil and gas, silica dust particles are a common hazard when dealing with sand on hydraulic fracturing sites. OSHA estimates that nearly 2.3 million workers in the US are exposed to respirable crystalline silica in their workplaces.
The US Department of Labor determined that workers exposed to silica dust at the previous permissible exposure limits faced increased risks of developing lung cancer, kidney disease, silicosis, and other nonmalignant respiratory diseases. The Department of Labor first set standards to limit worker exposure to respirable crystalline silica in 1971 after it created OSHA, but in recent years it claimed the standards were outdated and did not accurately protect workers from silica-related diseases, nor did it account for new industries.
In 2010, OSHA and the US National Institute for Occupational Safety and Health (NIOSH) examined the risks of worker exposure to silica during hydraulic fracturing operations. The NIOSH identified seven primary sources of silica dust exposure:
- Dust ejected from thief hatches (access ports) on top of the sand movers during refilling operations while the machines are running (hot loading)
- Dust ejected and pulsed through open side fill ports on the sand movers during refilling operations
- Dust generated by onsite vehicle traffic
- Dust released from the transfer belt under sand movers
- Dust created as sand drops into, or is agitated in, the blender hopper and on transfer belts
- Dust released from operations of transfer belts between the sand mover and the blender
- Dust released from the top end of the sand transfer belt on sand movers
OSHA proposed a full review of scientific evidence and industry consensus standards to provide basis for a revised rule. This new rule establishes a PEL of 0.05 mg/m3 of respirable crystalline silica as an 8-hour time-weighted average (TWA), down from the previous PEL of 0.1 mg/m3. It also includes other provisions such as requirements for exposure assessment, methods for controlling exposure, respiratory protection, medical surveillance, hazard communication, and record keeping.
The final rule became effective on 23 June last year, but general industry does not have to abide by its requirements until 2018, allowing a 2-year period for facilities to conduct exposure assessments and implement administrative and engineering controls.
Dust Mitigation
As the industry works to adapt to the new regulations, operators are looking at ways to minimize the presence of dust at their hydraulic fracturing sites.
George King, a distinguished engineering advisor with Apache, noted two types of coating methods that his company has found effective. One method involves the application of a resin, or any organic material that attracts and bonds silica particles, at a rail transfer station. King said he prefers the application of coating on-site at the sand mine because it is a better way to ensure minimal dust buildup at every transfer point.
King said he liked coatings because they do not require people on-site to do anything to ensure dust is being contained. However, it is still not a foolproof means of completely eliminating the presence of dust.
“As you transfer a material with a coating on it, you will break down some of the coating and you will generate a little bit of the dust, particularly if you have air transfer systems,” King said. “Any time sand changes direction in its flow—when it drops onto a belt, when it drops off a belt into another belt, or when it drops off into the hopper, you’re going to liberate some of the dust. You’re trying to minimize the dust as much as possible and some of the coatings do a better job than others.”
Beyond coating methods, King said Apache has made some “good advances” by making various changes to transfer devices. For instance, the company examined a vacuum system in which dust is sucked into a gathering sock. It also tried moving sand through screw conveyors, mechanisms where a rotating helical screw blade pushes the sand through a pipe.
Covered transfer belts have also proven effective. Instead of allowing dust to build up by allowing sand to fall on a belt, the company has fitted the chutes with skirts and covered some of the other areas where it would normally see dust. Apache has also experimented with different materials used for transporting dust, such as leather (which King called “very durable”) and plastic, which attracts and holds some particles in the sub-40‑micron range, a size smaller than the OSHA requirements.
“Basically, we’re just trying to do this to eliminate as much of it as we can,” he said. “Our target is a little bit lower than what they’re talking about. You will never get it all. You’ve got background dust out there right now in one of our West Texas locations that’s blowing around.”
Another mechanism Apache has examined is the pre-operation installation of silos, each storing approximately 500,000 lb of sand. King said the company has purchased several such silos for use on its sites.
“While there are a minimum number of people on location, you load these silos and then, when the [fracturing] gets ready to go, you’re simply pulling out of the silos. You don’t have a lot of trucks rolling out and unloading sand via air into storage tanks or whatever. With a combination of reasonable good coverage or coating, a reasonable good masking, skirting, and covering of the direction change points, and the use of silos, we’re at a point where I’m pleased,” he said.
Lessons From Other Industries
The OSHA regulations may provide an opportunity for companies familiar with coating technologies in other industries to enter the oil and gas market with new products.
ArrMaz, a chemical production company primarily focused on fertilizer coatings and the mining industry, launched its SandTec technology for hydraulic fracturing in September 2015. SandTec is a biorenewable, biodegradable silica dust control proppant coating technology that works by hydrogen bonding. The proppant coats sand and binds the dust onto the silica particles.
John Suldickas, a commercial manager for oil and gas at ArrMaz, called SandTec an “attrition-resistant” coating because it adds a property of lubricity to the sand, so as it is handled throughout the supply chain, it suffers from less attrition due to abrasion and breaking.
Suldickas said ArrMaz applied several lessons learned from its work on fertilizer coatings in the development of SandTec, but that fertilizer and sand provide slightly different challenges in treatment. Silica particles are smaller, and because the crush strength for fertilizer is significantly lower than that for sand, not as much force is needed to apply the coating.
“You can take the best coating chemistry in the world, and if you don’t spread it on your granules that you’re trying to control the dust on, it’s not going to work,” Suldickas said. “Being able to optimize the spreading of the coating onto your medium is just as important as the chemistry itself. Typically we’re applying between 2 and 3 lb of coating per ton of sand. It’s not a lot of liquid for a whole lot of granules.”
ArrMaz put SandTec on the market after the start of the oil price downturn and prior to OSHA’s announcement of the revised crystalline silica regulations. Because of this, Suldickas said the company has taken a patient approach when selling the coating system to operators.
“We went ahead and decided to release the product into the market, but we knew it was something we’d have to launch and then cultivate for a while,” Suldickas said.
Another company, Hexion, recently released its Sentinel dust suppressant, a chemical system designed to trap fine dust particles during transportation and transfer. Sentinel is a liquid dust control agent capable of reducing respirable silica dust below 0.025 mg/m3 as an 8-hour TWA, and its chemistry is compatible with most fracturing fluids. Hexion claims the sand is resistant to degradation during multiple proppant transfers.
Hexion has created resin-coated proppants for well stimulation as well as performance additives for oil fields, but in a press release announcing the launch of the product, Jerry Kurinsky, senior vice president and general manager of the company’s Oilfield Technology Group, said the company’s primary experience in handling respirable silica dust came from its work in the foundry industry.