The complete paper reviews the existing planning process for decommissioning projects on the UK Continental Shelf (UKCS) and explores an alternative approach of planning with reference to facility removal date rather than to cessation of production date. This approach aims to enable a more-effective planning in a high-oil-price and limited supply-chain-capacity environment to achieve cost reduction.
Introduction
Largely because of the implementation of the Maximizing Economic Recovery (MER) strategy, one prime focus of planning for decommissioning involves moving the cessation of production date as far out as possible to comply with the strategy. What this also means is that cost has been placed as the first priority in decommissioning in the UKCS landscape
However, it must not be forgotten that any project delays or business interruption can also affect the overall cost of decommissioning. Project management can arguably be even more important than engineering innovations considering the complexity of the project.
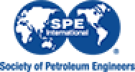