Artificial lift is a method used to lower the producing bottomhole pressure on a formation to obtain a higher production rate from the well. This can be done either with a positive-displacement downhole pump, such as a beam pump or a progressive cavity pump (PCP), to lower the flowing pressure at the pump intake, or it can be done by injecting gas with high pressure through a downhole gauge near the bottom of the well. The selection of the method depends on many factors such as reservoir characterization, completion design, and operating conditions such as pressure, temperature, and producing rate. In addition, production-fluid properties such as density and viscosity also play a role in the selection of artificial-lift methods.
Market Overview
The market for artificial-lift systems is growing at a compound annual growth rate of more than 4.5% (Fig. 1). Seventy percent of the world’s existing fields are mature, most of which require artificial lift to maintain planned production targets.
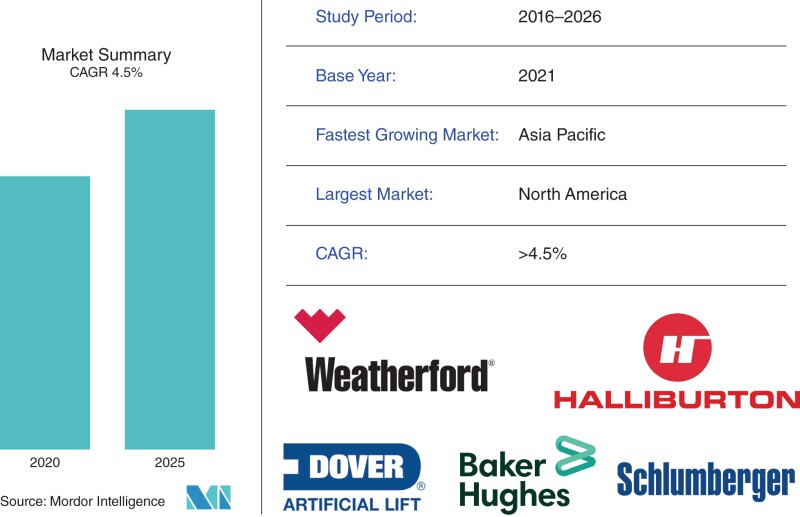
Based on a recent marketing study, Asia Pacific is one of the fastest growing markets for electrical submersible pumps (ESP), with China leading in demand as it works to increase production output from established fields.
North America dominated the global artificial-lift systems market in 2018, owing to its shale discoveries and the associated exploration and production activities. Furthermore, improved oil recovery is expected to support the demand for artificial-lift systems during the forecast period.
Petronas, PTTEP, and Pertamina are the major operators in the Asia Pacific region taking the lead in using new technology and methodology in artificial lift and in adopting digitization.
This article presents the technical approach of Petronas and Pertamina in implementing artificial-lift technology and their vision for the future. It summarizes a panel session organized by the SPE Artificial Lift and Gas Well Deliquification Technical Section in which the authors participated last year.
Overview of Gas-Lift Systems in Malaysia
Artificial lift is required when a well is no longer flowing or when the production rate is too low to be economic. Hydrocarbons will normally flow to the surface under natural flow when a well is newly completed. The fluid production will normally decrease, leading to a reduction in the reservoir pressure and an increase in the fraction of water being produced. These factors may reduce, or even stop, the flow of fluids from the well. The remedy is to include within the well completion some form of artificial lift.
In Malaysia, two types of artificial-lift systems are used: gas lift and ESP.
There are approximately 1,200 gas-lifted strings contributing to almost 40% of Malaysia’s total production. Currently, gas-lift optimization contributes to 5% of total gas-lifted production per year.
In the current challenging times, gas-lift optimization is one of the most cost-effective and impactful options for production enhancement with the highest cumulative gain and lowest unit-enhancement cost (Fig. 2).
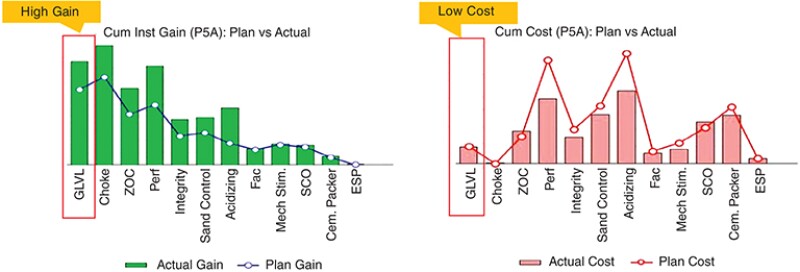
Several key technologies help to improve the success rate of enhancement jobs, one of which is CO2 tracer technology which monitors the number of injection points in the well. The injection points can be either via the gas-lift valves or tubing leaks. This technology also allows an accurate measurement of the amount of lift gas entering the tubing at each injection point.
The technology may be used as an alternate to a flowing gradient survey (FGS), providing the following advantages.
- Minimum equipment hookup and no need to shut in or choke the well, thus minimizing production deferment.
- No wireline tools are introduced into the wellbore, thus eliminating well intervention risk.
- Suitable for wells where an FGS is not possible due to well slugging, significant deviation, or downhole obstruction.
- Possible to run FGS on dual-string wells to determine the gas-lift split factor of a dual completion.
- Possible to determine exactly how much gas is injected through each injection point in a well.
Another key technology, digital intelligent artificial-lift (DIAL) systems, includes tubing-deployed units that are strategically positioned in the well. The units are connected by the TEC which provides power and communication. A surface control system allows local or remote actuation of the DIAL units to adjust injection rate and depth (Figs. 3 and 4).
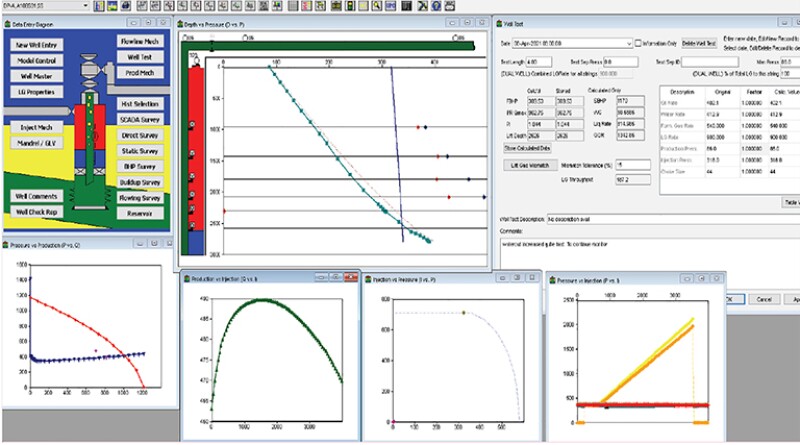
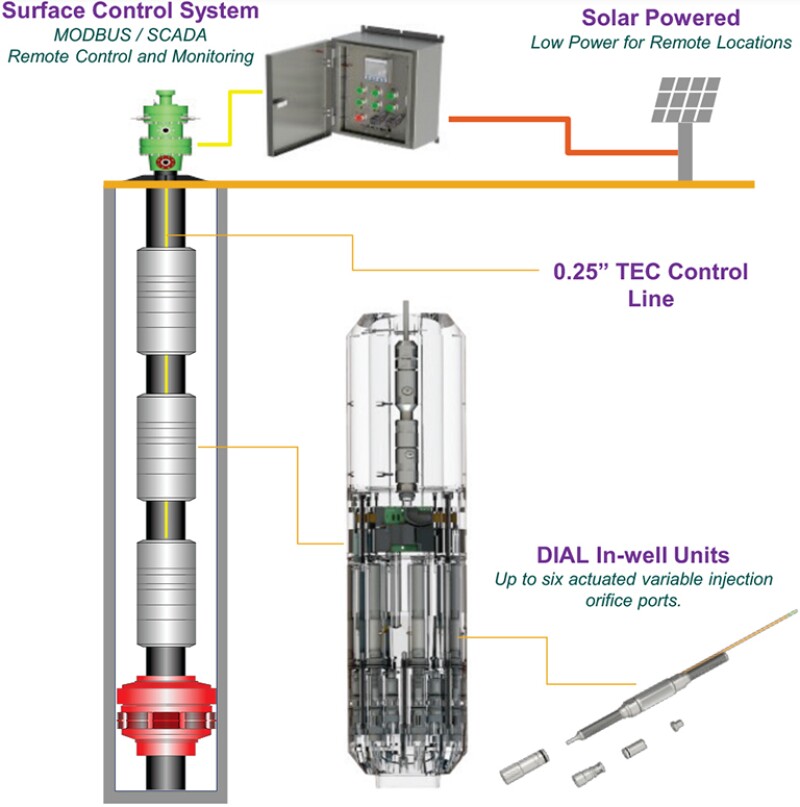
Implementation of DIAL began in 2017 with the first pilot well in the Dulang field in the South China Sea. Since then, there has been much interest for further replication of the technology in Malaysia. Various lessons learned and best practices were captured based on the installation and operation challenges which minimized the risk of failure for future installations (Fig. 5).
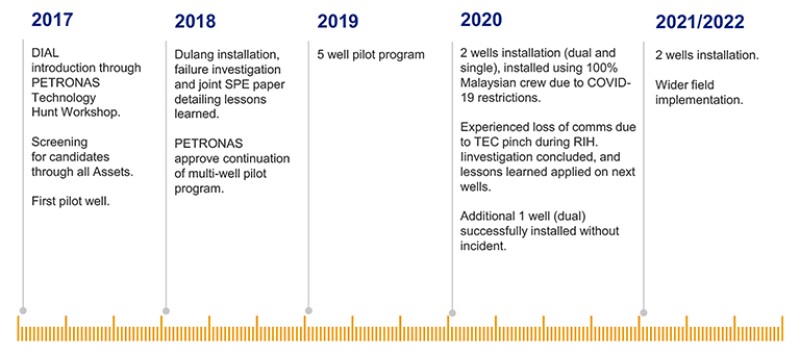
Pertamina Artificial-Lift Technology—Digitalization and Development Gas Lift in Handil Field
Handil is a mature field in Mahakam Delta, East Kalimantan, Indonesia, operated by Pertamina Hulu Mahakam, an upstream subsidiary of Pertamina Hulu Energi. The field has been producing oil for more than 40 years with peak production of 180,000 BOPD in 1977. Today, Handil field produces nearly 14,000 BOPD, of which 92% uses artificial lift and the remaining production is from natural-flow wells.
Handil uses various types of artificial lift, one of which is gas lift introduced and applied since 1995. In 2011, an enhanced oil recovery compressor was revived, allowing a total of four main compressors in the gas-lift system to deliver 85 MMscf/D with pressure 85 Barg into the wells.
Initially, this field had only conventional gas lift, but over time, the technology developed into an unconventional gas lift called REGAL (retrievable gas lift) that was applied on a well-by-well basis as needed and categorized as gas-lift packoff, siphon string gas lift, and gas-lift macaroni (Fig. 6).
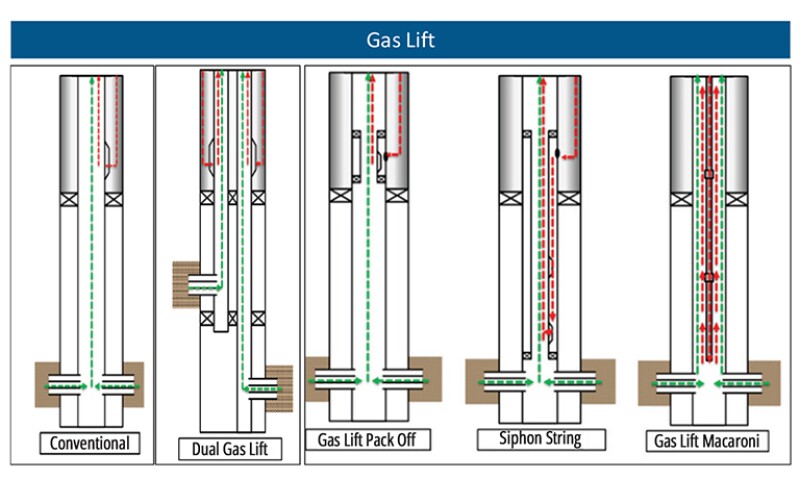
The gas-lift packoff (GLPO) system uses many of the same principles as conventional gas lift. The only difference is that it can be installed at any depth of tubing or even at SPMs (side pocket mandrels). This type of gas lift usually is used when the SPM is broken or unavailable. The GLPO tool-string assembly consists of a packer, sealing element, and gas-lift mandrel. This assembly is installed by a light workover unit; therefore, GLPO has the cheapest operation cost compared to two other REGAL technologies.
Siphon string gas lift has similar principles as GLPO, but it has longer sections of pipe that create a new annulus for a deeper gas-lift injection point. Normally, the siphon string type is used when GLPO cannot be installed due to annulus restriction. Siphon string gas lift consists of upper and top packers that are integrated with upper and lower sealing elements. The space between these sealing elements is where one or more gas-lift mandrels are installed. Due to the need for heavier-string installation, the siphon string assembly is set by a snubbing unit.
The gas-lift macaroni (GLM) technology applies concentric tubing inside the production tubing to inject gas lift. Since the liquid from the well is produced through annular production tubing, GLM requires special downhole safety valve (DHSV) installation. The DHSV is opened by applying hydraulic oil through control lines to push the spring downward, then the polished tube is landed on the lower section and provides continuous communication for the flow from the annular tubing to the surface. It also separates the gas-lift injection line at the concentric tubing from the production liquid that is flowing upward. When there is no hydraulic oil pressure, the spring will move upward and disconnect the polished tube from the lower gas-lift section, and finally, the flapper will fully close, indicating that the DHSV is closed. Gas-lift macaroni also requires a snubbing unit to install the assembly.
The other types of artificial-lift methods used in Handil are ESP and insert progressing cavity pump (i-PCP) (Fig. 7). The ESP is applied only in water-producing wells for a water-injection system that was proposed to maintain reservoir pressure. Meanwhile, i-PCP, or thru tubing PCP, was introduced in 2020. It is applied in shallow oil wells due to low API. On average, i-PCP is able to lift nearly 200 BLPD from each well in 3½-in. tubing.
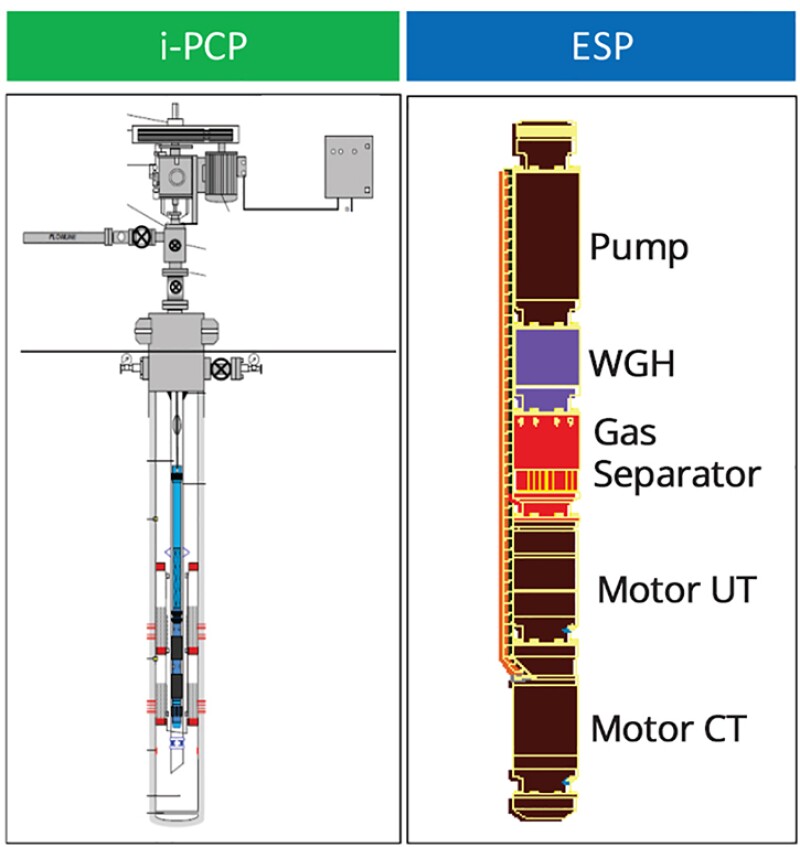
Handil field, located on a 40-km2 swamp area, has more than 100 active wells and is monitored daily by the operator (Fig. 8). Personnel travel 15–45 minutes to each well platform by sea-truck to record wellhead parameters such as pressure, temperature, gas-lift injection rate, choke size, and to perform manual liquid or sand sampling and visually check sampling points to assess the flow of the well (slugging or good liquid flow). These data are collected in a database that can also be accessed from the office by production, reservoir, and facility engineers to monitor and optimize the field’s production (Fig. 9).
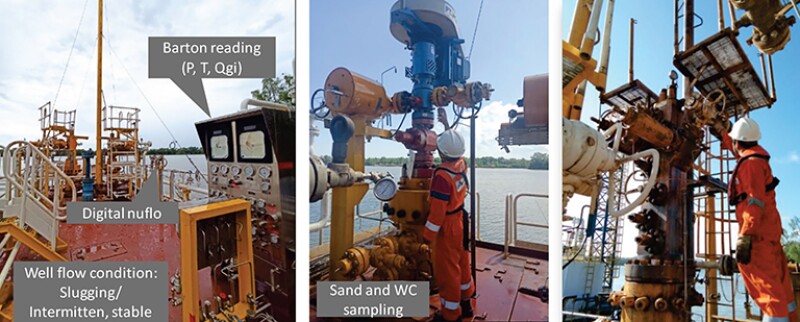
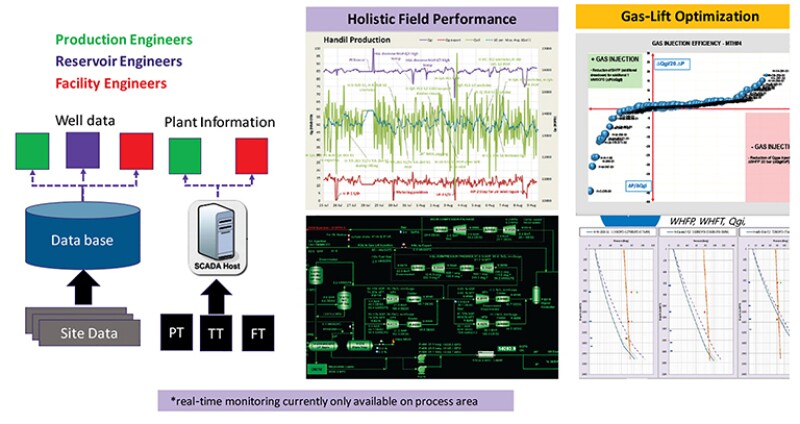
During the gas-lift optimization routine, a production engineer collects the information from well production, the well intervention report, and well completion as input data for third-party software (Petroleum Expert’s PROSPER). The software is connected by open server Macro Excel to automatically input and retrieve results data for multiwell applications.
The first gas-lift optimization tool is used to define optimum gas-lift injection rate. Due to the uncertainty of reservoir data and commingled reservoir production, this tool simulates the effect of different gas-lift rates to bottomhole flowing pressure. The optimum gas-lift injection rate is reached when there is no additional liquid rate at higher gas-lift injection pressures. These optimum gas-lift injection rates from all gas-lift wells are then classified as over, sufficient, or under injection pressure.
The last gas-lift optimization tool is estimation of injection points of gas-lift injection into the well without running a production logging tool (PLT). The analysis is done by plotting tubing and casing pressure traverse to compare casing pressure and valve-opening pressure. When casing pressure is above valve-opening pressure, the gas-lift valve is open and vice versa. The tool was inspired by a previous CO2 tracer program that was proposed to detect gas-lift injection depth. The principle of the tracer is to inject CO2 to annulus then record CO2 content with a gas chromatograph that is installed and connected at the wellhead. The traveling time of CO2 is then converted to the depth of the gas-lift valve.
In general, the main challenges for Handil gas lift are dual gas-lift stability, aging of well completion equipment, mature compressors, limited gas-lift availability, and the absence of production flowmeters on-site. Other challenges are maintenance access, limited electrical power, and even thievery and lack of monitoring systems (Fig. 10).
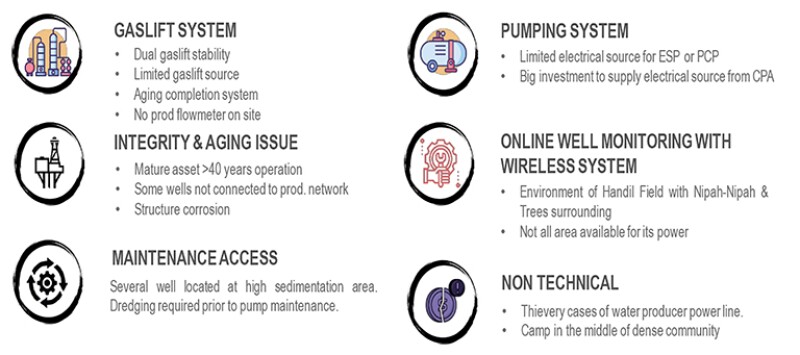
The artificial-lift technology development in the near term for Handil oil wells includes the planned installation of thru tubing ESP. Meanwhile, to overcome monitoring system challenges, a previously broken wireless system will be reactivated to allow for the online reading of well parameters.
The field’s development strategy includes a waterflood program which will be assisted by the drilling of more than 10 water-injection wells and continued with more than 30 water-injection well reinstatements. This waterflood program is projected as an early-stage and preparation phase for chemical enhanced oil recovery.
Conclusion
Artificial-lift design and optimization is a key element of production optimization, especially in mature fields and offshore fields. As demonstrated by Petronas and Pertamina and many other operators already using the advanced technology for measuring and optimizing gas-lift injection or other types of artificial lift, there is still room for improvement and innovation. Service companies have the opportunity to fill the existing gaps and challenges highlighted in this article such as lack of energy power, monitoring downhole measurement by creating workflow, and developing new technologies.
Adopting new technologies is becoming easier with digitization. Among the operational benefits is the availability of information to production engineers and technicians even when they are not physically in the fields. Artificial-lift and production optimization solutions are tending toward digitization and automation, bringing high value for operators by reducing risk and OPEX, and increasing the visibility of well and artificial-lift performance. This is needed specifically for downhole equipment safety and performance tracking.
Editor’s Note: Pertamina recognized the increase in oil and gas production in the Handil field using REGAL with its Upstream Improvement and Innovation Award, Jakarta, 2018.
To learn more about SPE resources for artificial lift, join the SPE Artificial Lift and Gas Well Deliquification Technical Section and follow the section on LinkedIn.
For Further Reading
J.F. Lea, Artificial Lift Selection, Chapter 10, Production Operations Engineering, SPE Petroleum Engineering Handbook, Vol. IV.
Canada Artificial Lift Systems Market 2022–2027 Industry Share, Size, Growth, Mordor Intelligence.
Gas Lift Technology Guidance for Better Decision Making Based on 40 Years Proven Implementation for Handil Field, Delta Mahakam by A.S. Ashfahani, G.L. Wijaya, Sulistiyo, et al. Proceedings of the Indonesian Petroleum Association 42nd Annual Convention and Exhibition, 2018.
Retrievable Gas Lift System To Unlock Oil Potential in Well Without Artificial Lift by A. Krishna, P. Noverri, M.N. Jamal, et al. Proceedings of the Indonesian Petroleum Association 40th Annual Convention and Exhibition, 2016.
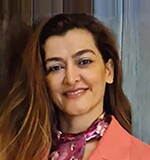
Fatemeh Mehran, SPE, has more than 22 years of experience in the oil and gas industry. Prior to joining Halliburton as industry solutions advisor for Asia, she worked in multiple projects as a technical advisor in the Middle East and held various roles as production engineering solutions champion for Schlumberger in Asia. Mehran also has been an instructor for NExT, a gas lift optimization solution consultant, digital oilfield champion, integrated operations projects advisor, and flow assurance global leader in Schlumberger. She is a board member of the SPE Technical Advisory Committee for Production and Facilities. She is member of the SPE International Production and Operation Award Committee and serves as regional champion for the SPE Artificial Lift Technical Section for Asia. Mehran received the 2021 SPE Service Award for the SPE Asia Pacific region. She holds an MSc in petroleum engineering from Heriot-Watt University and a post-graduate diploma in digital strategies for business from Columbia University.

Khairul Nizam Idris, SPE, is principal, production technology, for Malaysia Petroleum Management, Petronas. He has more than 18 years’ experience working in the oil and gas industry, particularly on production engineering and well completion. He has been working in multiple assets for Petronas domestic and international operations, as well as in specialized study and technical advisory roles. He is also the discipline resource person for production technology, line trainer for skill group courses in Petronas, and an external industry examiner for final year projects for local universities in Malaysia. He also serves as a member of the SPE Asia Pacific Regional Technical Advisory Committee and actively supports SPE events in the region. He holds an MSc in petroleum engineering from University Technology Petronas and a BEng in mechanical engineering from University Kebangsaan Malaysia.
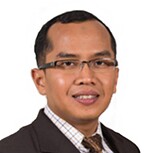
Dadik Hendra Kusuma, SPE, well performance leader in Pertamina Hulu Mahakam–East Kalimantan, has 17 years of working experience in the upstream (E&P) oil and gas industry, with 5 years in well intervention and 12 years in well-performance engineering. He has technical experience in in-well intervention operations (perforation, gas lift, zone shut-off, N2 unloading, surfactant capillary string, cementing, fishing/milling). He worked for 2 years at Total for various projects (artificial lift, R&D, network modeling), including projects in Dubai and Pointe Noire Congo. Kusuma also has experience in sand management, well and network modeling, and production monitoring of swamp and offshore oil wells and gas wells with gas-lift systems.