In the complete paper, the authors present an autonomous-directional-drilling (ADD) framework using an Industry 4.0 platform built on intelligent planning and execution capabilities and supported by surface and downhole automation technologies to achieve consistent directional-drilling operations accessible for remote operations. This ADD framework minimizes operational risk and cost per foot drilled; maximizes performance and procedural adherence; and establishes consistent results across fields, rigs, and trajectories.
Anatomy of ADD
The authors write that they identified a need for technology to support all aspects of the drilling process, not just what happens at the wellsite or the bottomhole assembly (BHA). That meant focusing on intelligent planning and intelligent execution capabilities, along with surface automation that would complement the suite of downhole automation features of the steering tools. Fig. 1 above highlights what the authors term the four pillars of ADD.
To connect these pillars, an integrated data architecture is crucial.
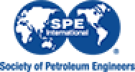