In almost any discussion of hydraulic fracturing, water-related concerns seem to consistently float to the top. Much focus goes toward issues ranging from the risk of groundwater contamination to the large volume of water—up to 8 million gal/well—that is used in the process of extracting oil and gas from shale.
The problem that is probably least understood, and yet can have the most significant effect on the sustainability of the operation, is microbial growth in water. Like other water-intensive advanced stimulation techniques, hydraulic fracturing provides bountiful opportunities for bacterial contamination if not properly controlled with an advanced biocides program.
With sustainable microbial control technology incorporated at the right points of the extraction process, it is possible to stop or prevent bacterial growth in the water. This lessens the degree of risk for a range of potential problems, including pipe corrosion, which is one cause of groundwater contamination. It also contributes to the creation of hydrogen sulfide, which can have a spoiling effect on the hydrocarbons and create emissions that are poisonous or even lethal to those living near the wellsite.
When shale oil and gas producers fully understand the risks of bacterial growth and follow best practices for water usage and treatment to avoid such growth, hydraulic fracturing becomes a safer, more efficient, and more sustainable process. As a result, the operation will be better embraced by the community and helps ensure its long-term viability.
Bacteria Thrive
In hydrocarbon production and processes, the tremendous volume of water used to extract oil and gas creates an environment in which microorganisms thrive. This is especially true when using nonpotable water, a best practice for sustainable hydraulic fracturing operations. Though recommended, nonpotable water contains an abundance of nutrients that foster bacterial growth, introducing an additional hurdle for responsible producers to overcome.
With plenty of sustenance available, a wide range of organisms can grow under fairly intense conditions. Life has been found in extreme temperatures, extreme pH levels, and even extreme salinity. So in the more relevant conditions of a hydraulic fracturing well in which temperatures may range from 60°C to 70°C, life is not merely a possibility, it is guaranteed.
If left unchecked, bacteria can affect the environment and the economic viability of the hydraulic fracturing operation. The presence of bacteria negatively affects both the quality and quantity of oil production as well as the safety of the operation. Microbes can corrode pipelines and equipment and plug reservoir pore throats. These complications are not only hazardous but also very costly. A recent article published in Environmental Science & Technology Letters called it “a multi-billion-dollar problem.”
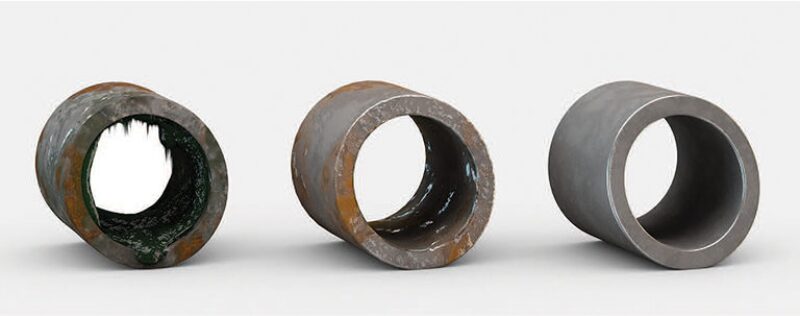
A water treatment plan that incorporates advanced biocide technology helps maximize production quantity and quality and is seen as a standard practice for hydraulic fracturing operations today. However, even for those who know the importance of microbial control, product innovations and best practices continue to evolve and it is essential to keep on top of this rapidly innovating field.
Understanding the Sustainability Priority
Every well and drilling site is a unique and complex biological system, which is why shale oil and gas producers must evaluate each project individually to determine the best path for microbial control.
The goals are to fully understand the environment in order to achieve the level of microbial control required to reduce risks and make the process efficient and effective by choosing the best technologies. Sustainability must be a priority at every step of the way.
What does sustainability mean in microbial control technology? It means that the technology accomplishes three goals. Firstly, the microbial control solution must do its job effectively—i.e., controlling and preventing nuisance and harmful microorganisms, preserving materials and processes, and facilitating safe and sustainable extraction processes.
Secondly, the biocide treatments will disappear completely after doing their job. They should be biodegradable, nonpersistent, and nonaccumulative in the environment.
Finally, the biocides program should do no harm to society, biodiversity, the environment, people, or processes.
Going beyond the biocides, sustainability covers many other aspects of a hydraulic fracturing operation, from sharing information freely with the community (this includes full disclosure of the chemicals used in hydraulic fracturing) to closely monitoring and testing the site before and during the process. A complete baseline evaluation of groundwater quality, near-surface water quality, ground contamination, and air quality is a critical step before the hydraulic fracturing process begins.
In terms of water usage, best practices in sustainability call for the source water to come from the lowest societal value source, and that it be cleaned and treated as needed so that it will be most beneficial to the efficiency and safety of the hydraulic fracturing operation. Along with this, flowback water and produced waters should be recycled to cut water consumption.
Best Practices Evolve
As the industry’s knowledge of biological systems expands, so does its need for new best practices in sustainable microbial control. We are seeing this already with the advent of extended downhole protection, which is becoming a common and needed offering in the industry. Additives such as glutaraldehyde have been widely used for decades to treat topside water to kill sulfate-reducing bacteria so they are not injected into the well. However, recent advances have shown that microbial control is not only needed for the short term in the topside water, but also for the longer term deep into the well.
The industry is now adopting standards for extended downhole protection against microorganisms so that the well will remain free from bacterial growth for days, weeks, or even months. Driven by enabling chemistry, the apporach is critical to the safety and financial success of a sustainable hydraulic fracturing operation. Without it, the integrity of the infrastructure of these wells and well productivity is at risk.
Chemistry’s Role
Science and chemistry continue to help unlock the potential of hydraulic fracturing, allowing producers to access the resource more safely and efficiently than before. The chemistry of sustainable microbial control is helping operators improve shale oil and gas recovery while minimizing cost and the environmental effect throughout the fracturing process.
Since 2007, shale oil and gas production and proven reserves have risen steadily, according to the US Energy Information Administration. Hydraulic fracturing is not a new innovation; vertical drilling and hydraulic fracturing started in 1947 as a way to stimulate production. It was not until the late 1990s that enabling chemicals became part of the process, making hydraulic fracturing economical for the first time and sparking a revolution in domestic energy supply.
The enabling chemicals, which when combined equal less than 1% of hydraulic fracturing fluid, range from friction reducers that reduce pump engine emissions and decrease surface pressure to gelling agents that improve proppant placement. Accounting for a small portion of these chemicals, biocides aid in reducing the risk of souring and pipe corrosion, both of which can result in negative water implications.
To make hydraulic fracturing work efficiently, effectively, and sustainably, producers must continue to take into account new knowledge and technologies. Extended downhole protection is a prime example. While topside protection is still important to ensure that bacterial growth will not happen for hours or days after the treated water is initially injected into the site, we now know that it is necessary to extend this practice deeper into the reservoir by using biocides as agents that will control microbial growth in the water for as long as several months.
Responsible oil and gas production is the key that will allow hydraulic fracturing to continue making unprecedented contributions to the security of US energy supplies. By focusing on innovative, science-based solutions to operational challenges, the oil and gas industry can work to assure the safe and sustainable recovery of natural resources.
The Glutaraldehyde Question: Is It Genuine?In the more than 6 decades since glutaraldehyde was introduced to the chemical marketplace, it has become known as a versatile molecule with disinfection properties that are highly effective for water treatment and a range of other applications, from medical equipment to cooling towers. But an increase in nongenuine glutaraldehyde blends, which are mixed with less-effective “aldehydes” but labeled deceptively as the real thing, have the makers of the real biocide advising customers to beware. In the hydraulic fracturing process, glutaraldehyde is commonly used to kill microorganisms in topside water, helping to ensure that the microbial contamination of the water that is injected into the well is under control. Besides its efficacy in killing bacteria, the liquid is ideal for hydraulic fracturing in large part because it is readily biodegradable, noncarcinogenic, nonpersistent, and nonbioaccumulative—all key factors that contribute to the sustainability of a hydraulic fracturing operation. Dow Chemical has developed and validated new analytical methods to help customers confidently distinguish genuine glutaraldehyde from nongenuine blends that are labeled incorrectly as “glutaraldehyde.” These methods include an innovative, field-deployable, and easy to use test-kit that provides a rapid detection method. ![]() During the past 5 years, blends of nongenuine glutaraldehyde have made their way into the marketplace. Marketed as glutaraldehyde, these products closely replicate the specific gravity and aldehyde titration results of glutaraldehyde. This is because nongenuine blends are usually mixed with formaldehyde, which is not an effective rapid-kill biocide and is a known carcinogen, placing workers, processes, products, and equipment in harm’s way. Not only do unknowing buyers of nongenuine products not receive what they are paying for, but they are also opening themselves up to potential legal issues if workers are hurt or the environment is compromised. It is critical for companies to ensure they are using genuine glutaraldehyde and not an inauthentic product that fails to comply with approved safe handling guidelines. Nongenuine blends can harm workers and are proven to fall short in efficacy and sustainability, presenting additional dangers and legal implications. |