In this article, a methodology is presented for the formation of a facilities engineering organization in an upstream operating company and others such as engineering contractors. The goal is to build an internal group that achieves a match of a company’s facilities engineering capability with the support required for the company’s assets/facilities. This is not necessarily an easy thing to do. Many companies experience difficulty with the process because of the division of responsibilities which makes implementation of a coherent strategy difficult. The groups involved are
- The “end users” of engineers such as project teams, engineering line managers, and the assets
- Hman resources
- Learning and development
- Organizational effectiveness
The process described for building a facilities engineering organization should be driven by technical competency requirements rather than by the types of assets. Assets may change with time and cyclical business conditions such as oil and gas prices, which in turn may affect sustainable levels of staffing.
The key variables and decisions involved in the process are discussed below in seven steps.
Step 1: Corporate Asset Portfolio
The facilities engineers required to support a company’s assets depend on the nature of the assets. A facilities asset is characterized in two ways: the processes and equipment involved, and the project/asset life cycle stage.
The assets generally share common elements such as pumps, compressors, heat exchangers, pressure vessels, piping, and instrumentation. However, they may also have distinguishing process-related features and differences in equipment (consider the differences found among onshore sour gas plants, offshore sweet oil platforms, liquefied natural gas [LNG] plants, and large oil pipelines).
The stages of a project/asset life cycle are appraisal, selection, definition, execution, and operation.
Many companies’ starting point for their facilities engineers is an operating asset, preferably at the asset location. As the engineers gain breadth and depth of experience—including exposure to other assets, locations, and the “ways of doing things”—they become better qualified for higher-level project/asset support roles in which a broader, deeper experience is required such as the appraisal, selection, and definition stages, and the optimization/troubleshooting in operation-stage facilities.
Most companies have a mix of assets in various life cycle stages and, therefore, require a range of facilities engineering experience/competencies to support them.
Step 2: Facilities Assets Description
A detailed definition of assets is required to ensure that the facilities engineers have the knowledge/competencies needed to do their job effectively. Many technical skill areas in facilities engineering are broadly applicable across assets (e.g., mechanical rotating equipment and instrumentation and controls), while others are asset-specific (e.g., subsea systems and LNG liquefaction processes). For example, “onshore sour gas plant” is a high level descriptor, but it needs to be defined further as follows:
Actual feed composition and conditions: for example, 30% hydrogen sulfide (H2S) is different from 200 ppmv H2S, though both are classified as sour gas.
The gas sweetening process used
The sulfur recovery (or disposal) process used
The liquid product treating process(es) used
Corrosion/materials selection
Safety
Environmental impact
Community impact
Step 3: Life Cycle Stage
In addition to the type of asset, the engineering support required varies with the life cycle stage of the asset. Table 1 shows the definitions, terminology, and general activities of life cycle stages in a typical project.
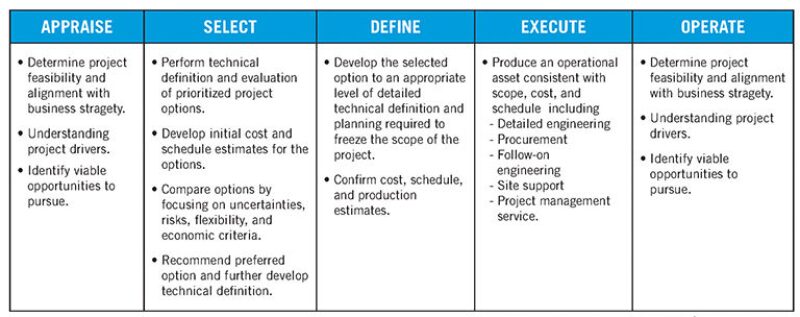
Versions of Table 1 may also be developed for the different facilities engineering disciplines/functions.
Generally speaking, the required level of depth and breadth of experience is higher for the earlier life cycle stages. Most valuable is the engineer who is knowledgeable about what has or has not worked well in the past, the reasons for the success or failure, the feasibility of using new technologies and their associated risks, and the limitations of local infrastructure and workforce capability. These aspects are especially important for “new frontier” project locations as opposed to well-established oil and gas operating areas.
Step 4: Division of Responsibilities
What do you want your people to do? What do you want someone else to do?
These questions are important to the success of an engineering organization. The allocation of responsibilities for engineering, project management, operations, and maintenance may be made among an operating company’s internal departments and/or external companies such as contract service providers. Original equipment manufacturers and consultants may also be involved.
Years ago, many operating companies had large engineering organizations that handled most of the engineering work involved in the execution of a project as shown in Table 1, as well as the ongoing engineering support needed during the operation stage. Some of these companies even had their own drafting department. Today, most of the engineering work, at least for projects, is being outsourced to engineering, procurement, and construction contractors.
Since small operating companies often do not have technical subject matter experts (SMEs), they rely on consultants to provide high-level technical expertise when it is occasionally required.Many companies' setup falls in between these extremes.
Which approach is best? A large number of factors are involved. Although this important subject is not the focus of this article, a few comments are warranted.
Facilities engineering should not be viewed as a commodity service, for which the only factor that matters is the hourly cost. “Excellent” engineering has the potential to provide better life cycle cost and value than “poor” or “average” engineering. Operating companies need to recognize the difference and be willing to pay for it, whether with highly competent internal engineering capability or the selection of good, often more expensive, external engineering providers.
A periodic review of the suitability of the makeup of the company’s facilities engineering organization in relation to the asset portfolio and current/forecast business conditions is also recommended.
Step 5: Two Types of Engineers
Which types of facilities engineers do you need?
The category of facilities engineers consists of “discipline” and “multidiscipline” engineers (Table 2). The discipline engineers have deep and narrow perspectives. They are process, mechanical (rotating and nonrotating equipment), electrical, instrumentation and control, process safety, pipeline, civil/structural, and maintenance/reliability engineers.
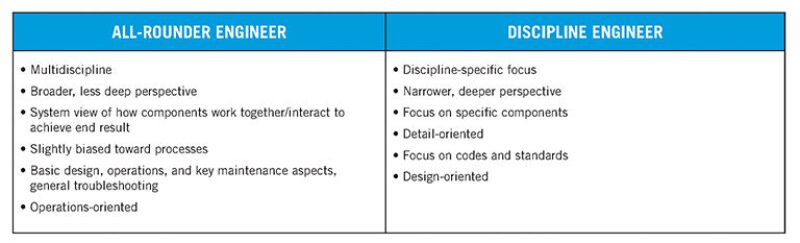
The multidiscipline engineers (all-rounders or jacks-of-all-trades) have broader and less deep perspectives. The jack-of-all-trades term sometimes has a negative connotation because it is followed by "master of none" in the idiom. Although the expression may describe the early years of an all-rounder's career development, over time, he or she may achieve a “skilled” level in multiple areas and even show mastery in one or two areas of expertise. A person’s versatility is valuable to his or her employer.
In addition to the roles and responsibilities of the types of facilities engineers, there is room for flexibility depending on the company’s job requirements or philosophy.
The size of the company, the number of facilities assets in its portfolio, and the local regulatory and professional certification requirements tend to favor the discipline engineer.
Large companies with correspondingly large asset bases can generally justify having SMEs with 25-plus years of experience and deep knowledge in specific technical areas such as welding, gas turbines, sulfur recovery, and advanced process control. These people may also be involved in research and development in their companies and serve as members of industry committees.
Small companies with small asset bases typically cannot justify having SMEs on staff because there is insufficient work that requires such level of expertise. Instead, they will rely on consultants when the expertise is occasionally needed.
Some companies lean toward the discipline engineer and some toward the all-rounder engineer; many rely on both types. Generally, the small companies use the all-rounders, and large companies typically use both.
Step 6: Development of Engineers
The steps discussed above determine the kinds of facilities engineers required to support a company’s asset base.
Two means of obtaining the engineering competence are the hiring of external engineers and the company’s internal development of engineers. In practice, both options may be necessary, depending on the company and its circumstances.
The “big crew change” in the oil and gas industry is well under way. To compensate for the loss of highly experienced technical personnel to retirement, it will be necessary to accelerate the skill development of the remaining younger staff.
The main components of development are training and the application of the acquired knowledge, on-the-job experience, varied job assignments, a dedicated coach or mentor, and a great deal of reading.
These elements of development are not significantly different from the historical requirements. However, a key difference is that an effective acceleration of competency development is now required, which calls for a more structured and compressed program than was used by most companies in the past
A logical question occasionally asked is “after 4 to 5 years of university to obtain an engineering degree, why is so much additional training still required?” The primary reason is that university engineering programs are by necessity generic. Their goal is not to prepare the enrollees for employment in a specific industry; the graduates could go just about anywhere.
The classical engineering discipline programs offered at most universities align better with facilities engineering in the oil and gas industry than others. For example, the mechanical, electrical, and instrumentation and controls disciplines align with facilities engineering reasonably well. Petroleum engineering is more oriented toward reservoir/drilling/production engineering than facilities.
Graduate chemical engineers align best with process engineering positions, though the match is often not ideal because many university chemical engineering programs are oriented toward the downstream/chemical plant sectors. The all-rounder facilities engineering job is best suited to graduates of chemical engineering followed by mechanical engineering. It is not uncommon for a company to hire engineers in general—especially when there is a shortage of graduates—and then train them for the job responsibilities required. This situation is less than ideal but sometimes a necessity.
Customized programs may be used to develop the expertise and knowledge for specific roles. Fig. 1 shows a customized development program for a gas processing engineer. It reflects a strong all-rounder philosophy with a significant process slant. The individual courses highlight the training component and the complementary activities, such as work experiences, coaching/mentoring support, varied job assignments, and reading must be included to maximize the effectiveness of the training.
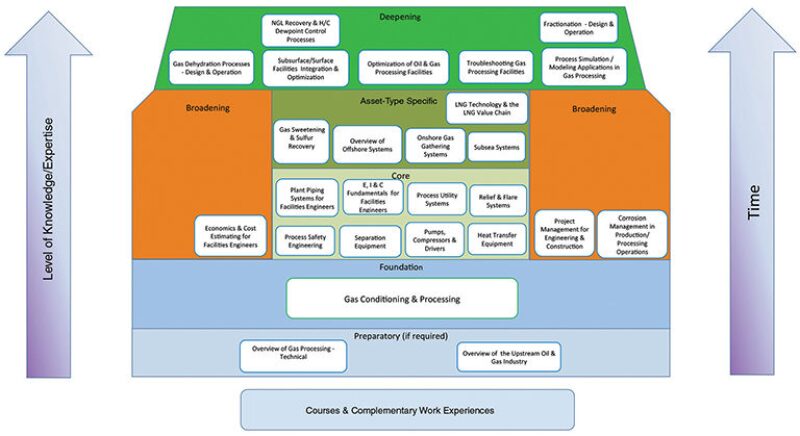
The training courses may be delivered by a classroom instructor, an online course, or a combination of the two. The program would likely be delivered over a 3- to 5-year time frame at the end of which the engineer would be expected to be a competent contributor. Although the program entails significant dedication to training and the complementary activities, the acceleration of the competency development curve demands the necessity.
The training courses are designed to deliver competencies specific to the engineering discipline/job as defined in a series of competency maps (CMAPs), which were developed in a collaboration between PetroSkills and representatives from a cross section of oil and gas industry partners.
The importance of on-the-job experience and coaching/mentoring support are obvious. However, the coaching/mentoring support is often problematic for many companies.There is a shortage of good coaches/mentors (who are not necessarily the same as SMEs) in many companies because many of these people are retiring.
The value of varied job assignments and reading may be less obvious. The purpose of different job assignments is to expose the engineer to different assets and different ways of doing things. Some large assets will have many elements, others will be more one-dimensional. The company must be willing to move engineers to other assignments, and the engineers must be willing to move, preferably every 2 to 3 years initially and more often if the assets are less complex.
Reading may seem like an unusual element of the development program; however, a large amount of knowledge must be assimilated in order to gain competency in a facilities engineering job.
A development program of training and complementing activities may contribute significantly toward achieving the required level of expertise, especially in the first 5 years of the engineer's career.
If the individual remains on a technical development path, the training and coaching/mentoring support may diminish with time and job assignment changes may only occur every 3 to 5 years. To maintain a steady pace of competency development, reading becomes an increasingly important source of knowledge. Conference technical papers, technical books, and industry magazines are sources of useful information. The Internet is another source of technical content, often at no cost.
Reading technical information may not sound exciting, but it is a valuable and underused development tool.
Step 7: Number and Type of Engineers Needed
The determination of the number and type of engineers for a project is based on
- The definition of the facilities asset portfolio.
- The estimation of the facilities engineering manpower required to support the assets for each life cycle stage, which is often the most difficult part of the process. The division of responsibilities must be well thought out.
Fig. 2 shows the hypothetical manpower results for an imagined facilities asset portfolio with a total of 140 onshore, offshore (with and without subsea components), LNG, pipeline, and gas-to-liquids projects in various life cycle stages.
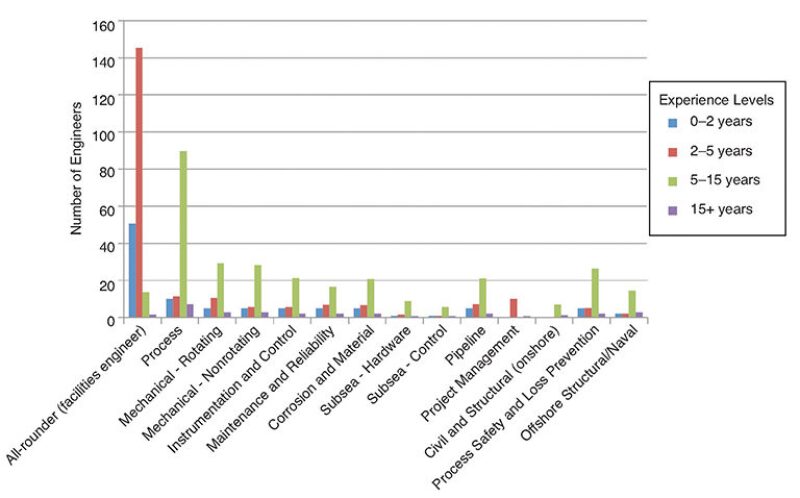
The results of such an analysis may be used to compare the theoretical and actual staffing requirements to identify gaps and overlaps and guide the reallocation of engineering resources or determine the need for new hires.
Conclusion
The methodology discussed may assist in areas ranging from the recruitment of new hires out of university through dealing with the loss of expertise caused by the retirement of senior employees. The process requires input from multiple departments in order to achieve a high-performance facilities engineering organization.
Mark Bothamley is a senior technical adviser at PetroSkills|John M. Campbell. His experience covers the design, operation, troubleshooting, and optimization of offshore and onshore oil and gas production and treating facilities and the development and delivery of facilities training and competency development programs. Before joining the company, he served with BP Amoco for 24 years in several locations around the world. He is a member of the SPE Separations Technology Technical Section, past specialty coordinator/chairman of the SPE Facilities and Construction Subcommittee, and a former member of the GPSA Editorial Review Board. Bothamley holds a BS in chemical engineering from Lakehead University in Canada and a diploma in natural gas and petroleum technology from the British Columbia Institute of Technology in Canada. He may be reached at mark.bothamley@petroskills.com.