As the oil and gas industry scans the known universe for ways to diversify its portfolio with alternative forms of energy, it might want to look under its own feet, too.
For inside every oil reservoir, there may be a hydrogen reservoir just waiting to get out.
The concept comes courtesy of Calgary-based Proton Technologies. Founded in 2015, the young firm is the operator of an aging heavy oil field in Saskatchewan.
There, on a small patch of flat farmland, Proton has been producing oil to pay the bills. At the same time, it has been experimenting with injecting oxygen into its reservoir in a bid to produce exclusively hydrogen.
Proton says its process is built on a technical foundation that includes years of research and works at the demonstration scale. Soon, the firm hopes to prove it is also profitable.
While it produces its own hydrogen, Proton is licensing out the technology to others. In January, fellow Canadian operator Whitecap Resources secured a hydrogen production license of up to 500 metric tons/day from Proton. Whitecap produces about 80,000 B/D of crude, and thanks to carbon sequestration, the operator has claimed a net negative emissions status since 2018.
Proton says it has struck similar licensing deals with other Canadian operators but that these companies have not yet made public announcements. Where these projects go from here may end up representing the ultimate test for Proton’s innovative twist on the in-situ combustion process known so well to the heavy-oil sector.
“In-situ combustion has been used in more than 500 projects worldwide over the last century. And, they have all produced hydrogen,” said Grant Strem, a cofounder and the CEO of Proton.
Strem is a petroleum geologist by background who spent the majority of his career working on heavy-oil projects for Canadian producers and research analysis with the banks that fund the upstream sector. While his new venture remains registered as an oil company, the self-described explorationist has come to look at oil fields very differently than he used to.
“In an oil field, you have oil—hydrocarbons, which are made of hydrogen and carbon. The other fluid down there is H2O. So, an oil field is really a giant hydrogen-rich, energy-dense system that’s all conveniently accessible by wells,” Strem explained.
But, in those past examples, the hundreds of other in-situ combustion projects, hydrogen production was merely a byproduct, an associated gas of sorts. It was the result of several reactions generated by air injections that producers use an oxidizer to heat up the heavy oil and get it flowing.
What Proton wants to do is to supercharge the hydrogen-generating reactions by using the oil as fuel while leaving the carbon where it is.
That ambition includes doing so at a price point that is roughly five times below that of Canadian natural gas prices and an even smaller fraction of what other hydrogen-generation methods cost.
“If we can produce hydrogen at a very large scale, and cheaper than natural gas, our big obvious market is blending into natural gas pipelines,” Strem said. He noted that that, in the US, displacing just 5% of the natural gas that flows into the country’s pipelines with hydrogen would equate to 30,000 metric tons/day.
Another milestone for Proton will be reached when it produces enough hydrogen to power its facilities. Closing the loop this way would be essential for Proton to earn the coveted low-carbon status of being a producer of so-called green hydrogen.
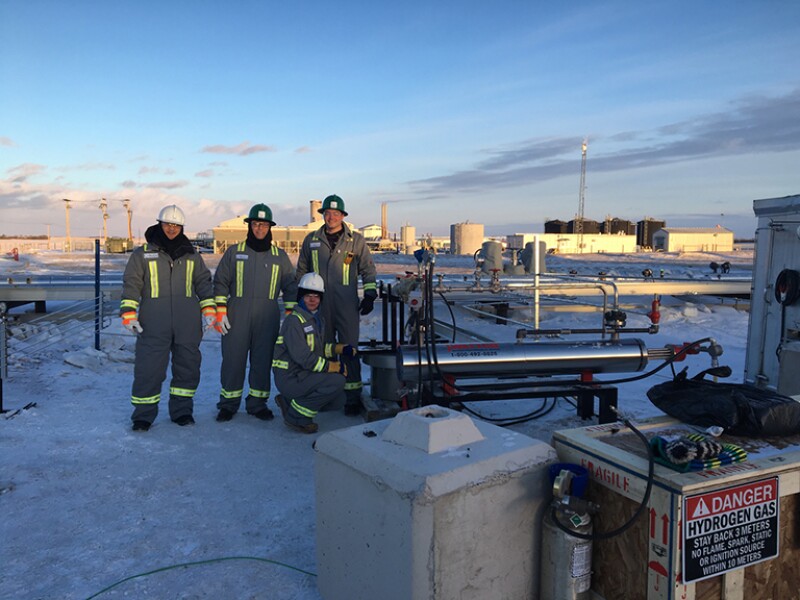
The Geologic Reactor
Proton’s asset is a heavy-oil field, but Strem added that the process is agnostic of API gravity because oxidation will occur wherever there is oil and water present. He did emphasize, though, that “soggy oil fields” should hold above-average hydrogen potential.
Such fields include those with an abundance of naturally trapped connate water and those in post-waterflood. These otherwise unattractive assets are Proton’s ideal because of their ability to sustain the water-gas shift—the chemical reaction that Proton thinks will ultimately yield the most hydrogen in an optimized system.
To hit the target of 500 metric tons/day of hydrogen, Proton is planning to install an air separator capable of boosting its oxygen injection rates to at least 6,000 metric tons/day. That oxygen will be sent straight to the bottom of the reservoir, where it will instantly oxidize the bitumen and petroleum coke that dominate the formation.
The heat-releasing reaction is needed to start another one called the water-gas shift. This is the reaction that is relied upon to make most of the world’s hydrogen today using steam methane reformers which, of course, are found on the surface.
And unlike in-situ steam recovery projects, Proton is trying to create a more localized reaction area with higher temperatures to drive up hydrogen production efficiency.
With enough heat, the once-long hydrocarbon chains are broken into several component pieces, gasses that include carbon dioxide and hydrogen. But Proton says the water-gas shift will become the biggest contributor of hydrogen by cracking it out of the reservoir’s more plentiful supply of water molecules.
Higher up in the reservoir is a production well to collect the mixed gas stream. Proton is separating the hydrogen using a palladium-alloy membrane, the same kind that has been used for decades in steam reforming. Installed near a production well, the membrane has extracted a 99.9% pure stream of hydrogen in early tests.
Proton will transport hydrogen to its customers initially with trucks and plans to sell power to Saskatchewan’s electric utility via hydrogen-compatible generators. As more is produced, the company said it can blend the hydrogen into natural gas pipelines, making it easier to use for heating homes or for power generation.
Blending hydrogen into gas pipelines remains an area of study for regulators in various jurisdictions, but small-scale projects from Hawaii to the UK show that between 10 and 20% hydrogen by volume can be injected safely without causing issues to the pipeline or consumer appliances further downstream. Though hydrogen burns clean by turning into water vapor, it raises infrastructure concerns because it can lead to the embrittlement of incompatible metals.
Awaiting a Downhole Hydrogen Filter
Most hydrogen used around the world, and especially in the oil and gas industry, is made by breaking down natural gas, or methane.
Known as steam reforming, this popular method can cost more than $5 per gigajoule of hydrogen energy. Proton is seeking to flow hydrogen at a breakeven wellhead price below $0.40 per gigajoule—5 times less than the average price of western Canadian natural gas in 2020.
But, to realize such arbitrage, the company will need more innovation.
The missing piece to its grand vision involves finding a way to take its membrane technology down the producing well and install it within the reservoir. “If we can leave it down there to start with—a downhole filter—then it would have significant benefit from a cost-structure perspective,” Strem said.
In addition to shrinking the surface footprint, separating the hydrogen in the borehole would leave the unwanted gasses trapped inside the reservoir. This includes the produced oxygen. Leaving it in the ground would help sustain the combustion process with less needing to be pumped down an injector.
Downhole separation would also enable better sequestration of the carbon dioxide. If not allowed to go up, the CO2 would be left to precipitate into the reservoir water as carbonic acid. Strem said additives, including oilfield waste water or raw sewage, could be added cheaply to accelerate the transformation of the CO2 into solid carbonates.
Carbon monoxide is also produced by in-situ combustion. Keeping it in the reservoir where it can mix with water vapor is akin to adding fuel to the water-gas shift.
As Strem explains, if Proton’s geologic reactor can be tuned just right, then the CO2 will turn into a solid carbonate material as the hydrogen is continuously removed from the reservoir. This creates an imbalance, which the water-gas shift reaction tries to equalize by breaking apart more water molecules to add more carbon dioxide, and more hydrogen.
“In this sense, the more hydrogen we pull out of the system,” Strem said, “the more hydrogen the system gives us.”
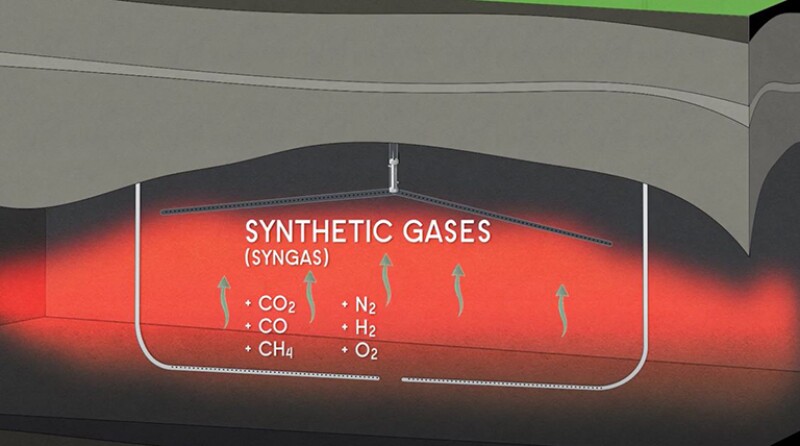
Aging Oil Fields Reborn as Hydrogen Greenfields?
Proton’s business model is owed to a friendly meet up between Strem and a professor he kept in touch with nearly a decade after studying under him in a master’s program at the University of Calgary.
“We were having breakfast one day, and he was showing me some results from an in-situ combustion project where the hydrogen percentage got up to 40%. That astonished me,” said Strem, who, by this time, had just started his first oil company.
That professor, Ian Gates, would soon become the cofounder of Proton. While he serves on the company’s advisory committee, he continues to research heavy-oil and oil-sands recovery processes at the university’s department of chemical and petroleum engineering.
Some of the theories Gates was discussing with Strem at that diner in Calgary are featured in a technical paper (SPE 122028) from 2009 that he coauthored with other university researchers. When Strem took the big idea to his investors, they liked it.
“We stopped focusing on oil and started focusing on Proton,” he said.
The anecdote is a reminder that the processes behind in-situ hydrogen generation are native to the petrotechnical sector. The question is whether the oil and gas industry will fully embrace the idea.
Proton says the answer is already in, and it’s a yes.
The company has sold 4 of its 15 licenses to oil and gas operators. Most of the other deals are with renewable energy companies seeking to address intermittency issues without resorting to high-cost batteries.
Proton plans to continue selling licenses while it endeavors to become a major hydrogen producer.
If the concept pans out, perhaps the upstream industry will find more interest because there appears to be considerable overlap with its reservoir management capabilities and production technologies.
One aspect oil companies may find compelling is that Proton believes mature oil reservoirs are best suited for its brand of in-situ combustion. “The world is full of them, and they show up as abandonment liability on someone’s balance sheet,” Strem said of the aging assets.
“And, when oil fields are abandoned, most of the oil is still in the ground. It is hard to get those molecules to a production wellbore, but it’s really easy to move gas around in these old, high-porosity oil fields,” he continued. “The oxygen finds the oil and water very easily; the hydrogen then finds our production well very easily.”
Another reason oil producers may find the concept attractive is because, thus far, Proton’s day-to-day operations appear very similar to theirs.
Proton acquired its field and much of the in-situ combustion infrastructure from its previous operator out of receivership. It continues to rely on the same kind of service providers for pipefitting, tubing installation, and for workovers.
When new injection and production wells are needed, tenders will come from the same contractors drilling oil wells in western Canada.
There are adjustments to be made, for sure, including the use of hydrogen-resistant wellheads and more oxygen-tolerant tubing in the injectors. Another change is that, in the in-situ hydrogen business, there is no need for exploration.
As someone who spent the bulk of their career working on that front, Strem said “this is the heartbreaking part for me.” He is alluding to the fact that the seismic work for brownfields is long done—we know where the energy is.
“It’s hard to fathom how much we already have behind pipe that’s uneconomic as an oil producer but would be hugely valuable for this,” he said.
For Further Reading
SPE 122028 Potential for Hydrogen Generation during In-Situ Combustion of Bitumen by Punitkumar Ramanlal Kapadia, Michael Kallos, Leskiw Chris, and Ian Donald Gates, SPE, University of Calgary.