At a major industry conference in March in Beijing, Wang Yilin, the chairman of China National Petroleum Corporation (CNPC), took a moment to highlight that just outside the doors to the building were blue skies—a result, he said, of the country’s move to displace coal-fired power generation with cleaner-burning natural gas.
Wang praised his company’s “enormous contribution” to the pleasant conditions by emphasizing CNPC’s role as China’s largest producer of natural gas. In doing so, he underlined how the company, the fourth largest in the world, is being reshaped by China’s multifaceted energy transformation.
The country depends on coal for more than half of its energy needs, while natural gas represents only 7% of the mix, an increasing amount of which is imported as liquefied natural gas (LNG).
Driven by air quality concerns, the country is looking to double that gas figure by 2035. But its national energy security agenda includes reducing dependence on foreign LNG by relying on national oil companies to increase domestic supplies through the commercialization of unconventional resources.
But what is less clear than the skies above the conference is how China’s oil and gas industry will realize this ambition. So far, the unconventional programs have struggled to mature as rapidly as the state had hoped.
In his remarks, made during a keynote address at the International Petroleum Technology Conference (IPTC), Wang emphasized what he views as the chief culprit behind the difficulties: China’s complex unconventional geology, which is unlike anything most US shale explorers have ever had to overcome.
“So it’s not that easy to simply replicate the shale gas technology developments of North America,” he argued. Wang later stressed that his country’s unconventional sector is “urgently in need of technology breakthroughs,” ones tailored to its own geologic fabric.
The technical portion of IPTC offered new case studies that shed light on the increasing role that innovation and technology are playing in overcoming the nature of these unconventional formations. Engineers presenting their research made it clear that without the right tools, they must work through an unpredictable drilling and completions environment, driving up both costs and nonproductive time.
Of more than 500 technical papers presented at IPTC, just over 50 focused on different aspects of China’s domestic programs that are spread across the country. Several were authored by engineers and researchers working at PetroChina. The company sits under CNPC as a wholly-owned subsidiary where it serves as the main arm of its exploration and production business and holds the largest mineral rights for unconventional resources in the country.
Its prized possession is a 20,000 sq km (~7,700 sq mi) swath of land in the Sichuan Basin, located in central China, where there are 20,000 drilling targets. So far, PetroChina has drilled only about 400 wells there, but that work has made Sichuan the only unconventional basin in China to achieve commercial shale gas production.
PetroChina estimates its holdings there include about 14 Tcm of technically recoverable shale gas—just under half of the country’s estimated 31.6 Tcm. This is the world’s largest volume of recoverable reserves, almost 70% more than the US, according to estimates from the US Energy Information Administration.

Blue skies and shale gas: the two things that China National Petroleum Corporation (CNPC) chairman Wang Yilin wants more of for his country. Source: IPTC.
Missing The Target
Cumulative shale gas output in China was just over 10 Bcm last year, and most analyst projections peg the 2020 figure at around 13–15 Bcm. This means the government’s goal for domestic shale gas output of 30 Bcm by 2020 is unattainable.
“In China, the industry is facing a lot of challenges, and in terms of shale gas, it is very difficult to achieve the targets that government has been setting,” said Kaho Yu, a senior political analyst with the global consulting firm Verisk Maplecroft.
He noted that policy decisions at the local level have not done enough to lower the risk posed by community relations in the areas where thousands of wells are planned to be drilled over the next few years. Government incentives at a higher level have also not proven to be fully effective at propping up the nascent sector, meaning it will take more time to build the necessary operational support and gas transportation infrastructure.
Xianhui Zhang, Wood Mackenzie’s eastern Asia upstream research analyst, added that while Chinese companies are committed to the national energy goals, the production goal “is considered very aggressive and hard to reach, by both them and us.”
She emphasized that the national oil companies have put substantial effort into their programs but, “nonetheless, developing shale gas in China is very difficult, and hitting even half of the 30 Bcm shale gas target would be a solid achievement from where we are currently.”
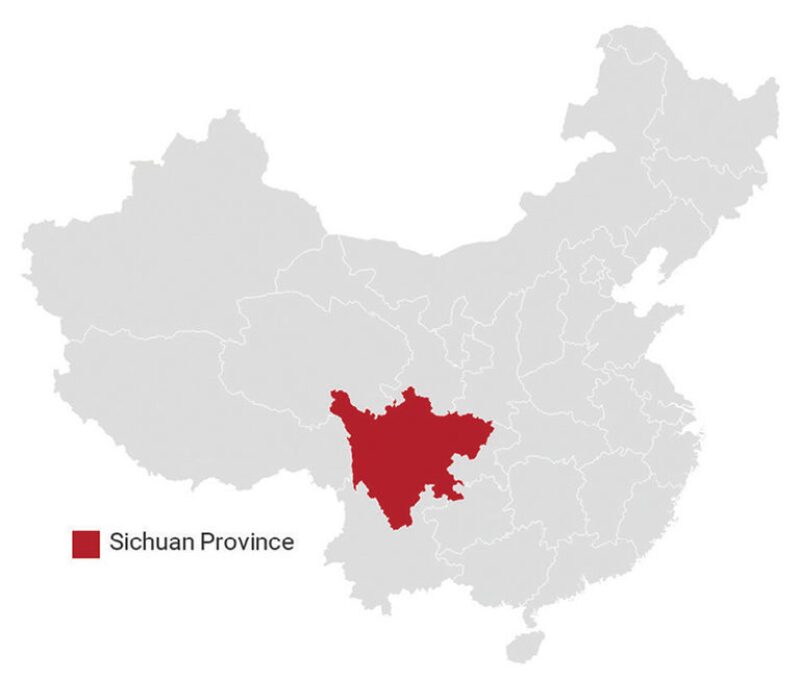
Found in the center of the country, the Sichuan Province holds the most promising geology for shale gas development in the country. PetroChina has three concurrent exploration programs in the Sichuan Basin and is joined by fellow national oil company, Sinopec, which has two producing fields. As the only commercial unconventional developments in the country, their work will serve as the bellwether for the country’s shale gas dream.
Opposite Ends of Shale Spectrum
The knowledge sharing among service companies and operators at IPTC supported Wang’s defense for the pace of progress. While China was inspired by the US shale revolution, its source rocks have evolved very differently. In multiple technical sessions, engineers drew comparisons and contrasts between the two country’s unconventional makeup.
In the US, shale structures have relatively modest, simple inclinations. For instance, a steep dip in the gas-rich Haynesville Shale of Louisiana is considered to be about 15°, conditions found on the fringe of the play, not its core.
As the bit hits the pay zone in Sichuan, China’s most active and promising unconventional basin, it could turn back upwards at an inclination of up to 50°, creating well paths that look like a paper clip being pulled apart.
Most of the biggest shale plays in the US are on flat land. In Sichuan, drilling pads sometimes end up on the top of small mountains. Drilling down from those heights are reservoirs that are deeper than all major gas plays in the US save one.
At the extreme end, Sichuan wells are drilled to around 4,500 m (~14,700 ft). Average wells in the Haynesville land around 3,600 m (~11,800 ft)—making them some of the deepest in the US—while gas wells in the Marcellus Shale in Pennsylvania typically do not exceed 2,600 m depths (~8,500 ft).
Natural fracture networks and faults are a going concern for the effectiveness of horizontal drilling and completions in the US. However, these features appear to be far bigger threats to Chinese operators in Sichuan that plan to drill thousands of wells there. Frequent problems include gas kicks, stuck pipe, and loss of circulation during drilling.
These burdensome conditions are the lasting impressions of several distinct tectonic episodes that took place eons ago, including the period when the Himalaya Mountains were created as modern day India slowly crashed into south Asia.
As continental plates moved around, shale layers in China were transformed from a state of relaxed depression into upwards-thrusting structures. Today’s target formations are rife with deformations, complex stress regimes, and plenty of natural fractures and faults to entice seismic companies and worry drillers for many years to come.
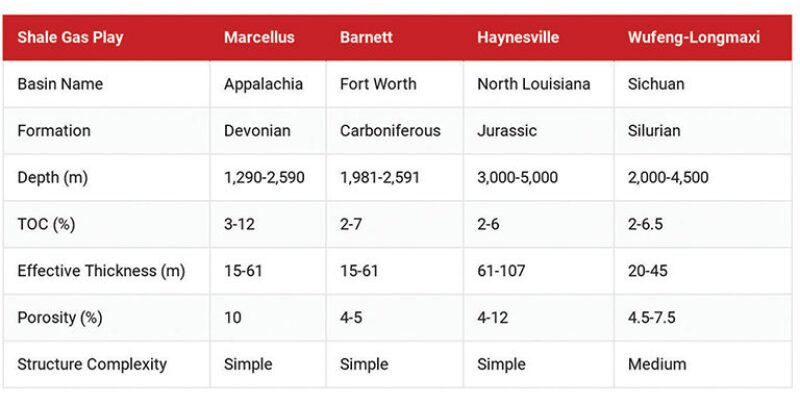
Comparing the reservoir properties of China’s key shale gas target in the Sichuan Basin shows that its closest match is the Haynesville Shale in Louisiana. The geologic structures, however, are not that similar.
Resetting Expectations
In April, the apparent pains of drilling for shale gas in China were manifested with the announcement that BP, one of several international oil companies (IOCs) with stakes in the country, has decided to call it quits.
Zhang said that poor well performance and problems on the surface led to the cancellation of further projects. It was also noted that BP was drilling deeper wells than other operators working in Sichuan.
“The announcement underscores the difficulties facing IOCs looking to build an upstream onshore business in China,” she said, adding that, “Despite a large number of shale agreements being signed with IOCs over the last decade, all have now failed and been abandoned.”
Amid all these hurdles and setbacks, something to keep in mind is that shale gas production was close to nothing at the start of the decade. While unconventional exploration in the US began its teething phase in the 1980s, China’s first horizontal shale well began flowing in 2011.
Though it has struggled for inspiring well economics, there are some signs that Chinese operations are getting a handle on how to tame the shale tiger. A jointly produced PetroChina and Schlumberger paper (IPTC 19371) shared at the conference reported that drilling times have improved by 75% since the start of the great effort.
Meanwhile, Wood Mackenzie estimates that all-in shale well costs are around $8–$10 million, with about $6 million of that going into drilling and completions. “The cost is down around 30% than the first batch of commercial wells in 2014,” said Zhang.
No single breakthrough has led to the improvements. Rather, much like drilling progress made over the years in the US, success has come down to fine-tuning a number of factors. Zhang said well cost reductions have been “primarily driven by a better understanding of the geology, technological innovations, and more experienced crews.”
Further nuances provided by PetroChina and Schlumberger’s presentations at IPTC include better decision making on well plans, the selection of drilling mud, and the extra spend by operators to use sophisticated bottomhole assemblies (BHAs). To improve output, the companies also point out that since 2016 PetroChina has been testing “super laterals” of 3,000 m (~9,800 ft).
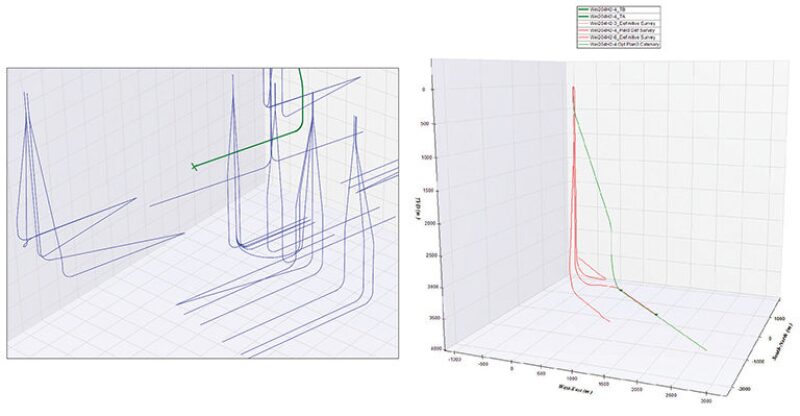
Early well designs (left) called for drilling to total depth with little or no directional drilling before getting there, the easiest and fastest way to reach a target. This increases the chances of wellbore collisions, instability, and general drilling dysfunction. The better option on the table is the well-established “pseudo catenary” well profile (right) now being used to eliminate these issues and achieve longer lateral sections. Source: Schlumberger/PetroChina IPTC 19371.
“Fast Learners”
Making the most of its unrivaled trove of tight gas will require China to master key things such as figuring out how to land a horizontal well where hydraulic fracturing operations work best.
“And that’s very tricky,” said Igor Kuvaev, the chief technology officer of a Houston-based geosteering software startup called ROGII. The firm came to IPTC with more than 200 companies in the US using its technology, which helps guide horizontal drillers through the shale strata.
Recently, Chinese operators have come knocking; Kuvaev describes these new clients as “fast learners” when it comes to the value of well placement. Within the past 5 years, operators in Sichuan have realized that “some layers are easier to frac, and some layers are harder to frac,” he said. “This is why geosteering is so important—you need to stay in a specific window.”
Ibrahim Abou-Sayed, the president of unconventional consultancy i-Stimulation Solutions in Houston, has advised Chinese operators in the past and chaired several technical sessions at IPTC. He has seen the thinking in China evolve from adopting best practices in the US to a realization that the country’s unique unconventional conditions require extensive geoscience and customized approaches.
“They are beginning to adopt the appropriate methodology for development,” he said. “Whether or not they will overcome the tectonics, the faulting, and the depositional environment remains to be seen.”
The subsurface factors may also curb the ability of China’s shale producers from achieving the highest-level goal of so-called factory mode drilling.
Abou-Sayed explained that the dynamism of the geology means that stress fields can rotate constantly in a field, especially in mountainous regions. This dictates that wells located relatively close together may have to have different orientations for optimal hydraulic fracturing—the rule of thumb for which is that stimulated fractures should be perpendicular to the minimum in-situ stress.
“This will probably be the element that will slow them down from attaining the assembly-line approach we use in the US,” he said, adding that a “fit-for-purpose” approach based on geologic data (logs, cores, geomechanics, geochemistry, etc.) will probably be required on a larger basis to accommodate for the shifting reservoir conditions.
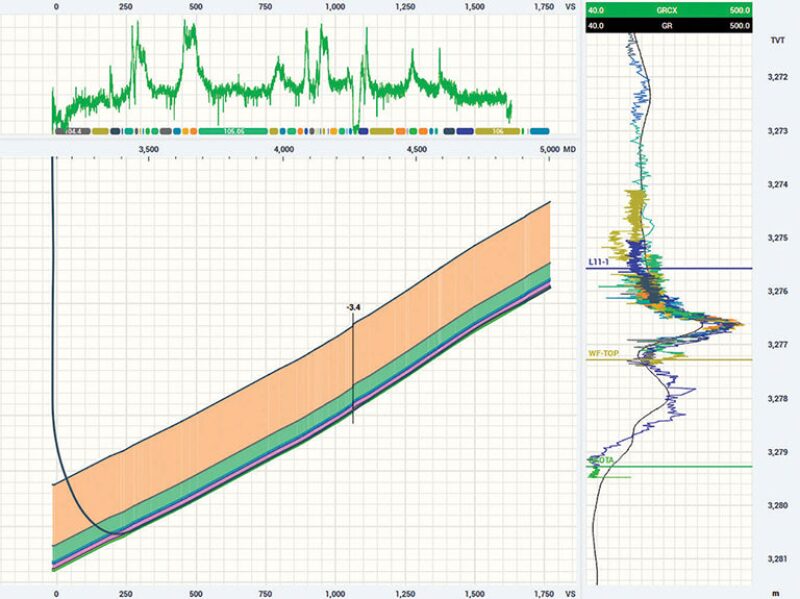
This geosteering screen shot shows a Sichuan Basin well hitting a target zone just 2 m (6.5 ft) thick and turning up at a 45° angle. Faults and dip changes are present throughout the well path. Source: ROGII.
Downhole Technology Proves Essential
PetroChina and Schlumberger presented jointly authored papers that outlined some of the lessons they have been learning together since work began in earnest to access Sichuan’s tight-gas reservoirs about 5 years ago.
One of them outlines a risk-prediction system for drilling in the Sichuan Basin that relies on integrated 3D geomechanical models to identify where problematic natural fractures might be (IPTC 19487). The key output is a map that tells drillers where to expect issues that include gas kicks and mud losses.
Another paper presented at the conference by PetroChina and Schlumberger (IPTC 19464) highlights two other tools required for controlling where the wells go: real-time logging while drilling (LWD) and rotary steerable systems (RSS).
The authors said the use of RSS has “helped to increase drilling efficiency tremendously” and represents a “milestone change” for China’s unconventional program. Without the technology, drilling efforts were incapable of having control over the direction of the bit as it created the lateral section—resulting in noneconomic wells.
It is a notable endorsement since shale producers in the US have historically used LWD and RSS sparingly due to the perceived high cost.
But in Sichuan, the geology is far less forgiving to the Chinese explorers than what their US counterparts must overcome. The primary target formation there—the Wufeng-Longmaxi—has a high-quality zone with a thickness of about 25–40 m (~80–130 ft), but because of how the shale system responds to hydraulic fracturing, the optimal landing zone is really just the bottom 5 m (16 ft) of the formation.
If drillers move the bit out of zone, below the target formation, then they risk coming into contact with a layer of rock high in silicon content which creates borehole instability. Encountering this layer also routinely led to stick/slip, stuck pipe, BHA wear, and a loss of trajectory control. During the drilling of one particular well, engineers and crew spent 2 weeks dealing with stuck pipe issues because of this silicon layer.
These types of problems help explain why at the start of the decade horizontal wells in China took as long as 4 months to drill. But through technology and deeper analysis, the bit is moving much faster.
Per Schlumberger’s numbers, by 2016 drilling times fell to 60 days. At the end of 2017, it took an average of 30 days and this year’s goal is to bring that down to just 20 days. The company’s conference paper covering the topic said, “The next step is to realize the ambition of factory drilling.”
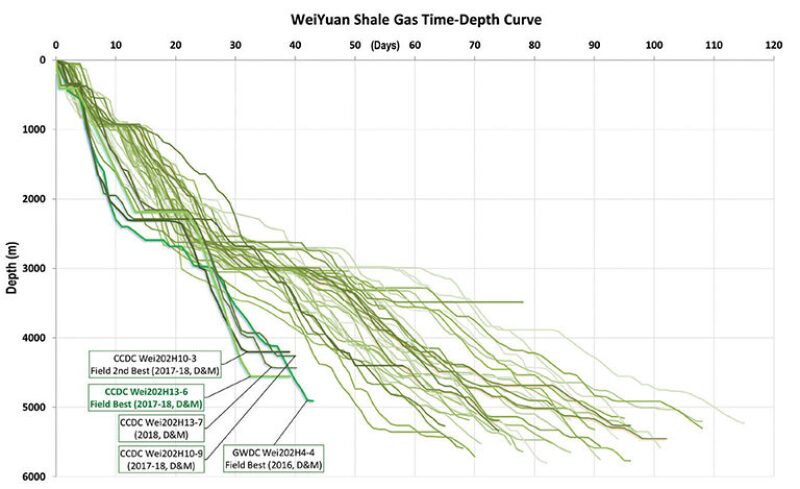
Time-depth curves of shale gas wells in the Sichuan Basin shows drilling times improving from an average of 80 days to about 30 days per well. Source: Schlumberger/PetroChina IPTC 19371.