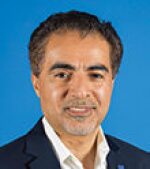
There is no doubt that the world today consumes materials in all domains more than needed, possibly double or even triple what it needs. As a result, part of our world’s natural resources end up polluting the land and sea with a growing trail of waste. Sustainability requires being more efficient—conserving, recycling, and reusing to minimize the impact of everything we do. The developed world must no longer tolerate the buildup of mountains of waste while other places in the world, especially in underdeveloped countries, lack access to energy, food, clean water, and clean air.
The world’s population is projected to increase to 9 billion by 2040, adding 1.7 billion people in 20 years (85 million every year). Sustaining current levels of consumption while population grows that fast will be challenging. Most of the population growth will be in underdeveloped countries, with almost half in Africa, a continent with the highest levels of energy poverty and the lowest economic growth. In 2017, the population of Africa was roughly equivalent to the Organisation for Economic Cooperation and Development’s designated developed countries (each about 17% of the world’s population), but in terms of gross domestic product, the developed countries accounted for 63% of the world, and Africa only 3%. As these countries grow and develop, they will be challenged to overcome the vast disparity and bring energy to their expanding population.
As the oil and gas industry works to make our operations more sustainable, we can adopt the mindset of a “circular economy.” The circular economy is an alternative to the traditional linear economy (i.e., make, use, and dispose) in which we keep resources in use for as long as possible, extract the maximum value from them while in use, then recover and regenerate products and materials at the end of each product service life. The circular economy keeps goods in use as long as possible through recycling and reuse, thereby decreasing the need for raw materials. This, in turn, reduces carbon intensity and our carbon footprint.
Recycling used materials and plastics instead of disposing or burning them as waste is one important way to make better use of valuable resources, and create a new economy through new business opportunities. There are opportunities throughout our value chain from upstream to downstream to deploy new models of energy conservation. We are already making significant progress in recycling and reusing produced and flowback water. But where else can we reuse the fluids, materials, and equipment that go into supplying the world with oil and natural gas? Can we reach a certain target (%) for incorporating circular economy concepts across our industry? I believe that there are numerous opportunities for which a positive business case exists.
In the upstream, there are numerous opportunities for recycling and reuse. Many of our tools and equipment are made from steel—creating opportunities for recycling. When we decommission an offshore platform, companies are already working to remove anything that can be recycled, and in some cases, parts of the substructure are turned into beneficial artificial reefs. Companies are being smarter about recycling or reuse of drilling fluids and chemicals. We are conserving energy in our operations through cogeneration using spent steam, waste gas, and heat exchangers.
Globally, our operations produce several billion barrels of produced and waste water. Much of that water is brine, which can be environmentally damaging if not properly disposed. But brine contains valuable and high-demand minerals that can potentially be extracted for use by other industries. The waste water can be further treated and used in other operations or disposed. Where possible, disposal to the original formation can help to maintain reservoir pressure, increase recovery, and eliminate environmental impact.
The refining segment of our industry has opportunities to address both water use and advanced materials such as catalysts and chemicals. Going forward, refiners need to develop methods for recovering and recycling spent catalysts and chemicals. They can also conserve energy and use spent heat and steam to generate power to meet refinery needs, with the potential to export excess power to a nearby grid. The industry’s procurement strategy should begin to consider the extent to which suppliers take sustainable and circular approaches to products.
The petrochemicals portion of our industry began making R&D investments more than a decade ago to address the environmental aspects of plastics. While plastic has made a huge difference in so many areas of human life and activity, it was purposely designed to be very durable and have a long life cycle. Plastics are nonbiodegradable materials that must be treated, recycled, or disposed of after use.
According to a 2017 study in the journal Science Advances, 75% of all plastic made since its introduction has ended as waste. Of this waste plastic, 9% has been recycled, 12% destroyed (burned), and the remaining 79% has ended up as trash, either in landfills or free-floating in the oceans. The opportunities for recycling more of this plastic waste seem substantial. According to McKinsey & Company, the volume of plastic going to recycling could increase fivefold by 2030. McKinsey also projects that the industry based on recycled plastics could generate a worldwide profit of approximately $55 billion/year by 2030. The business case for recycling is clear.
The McKinsey report outlines three principal approaches to plastics recycling:
- Mechanical recycling, which physically processes used plastic back to pellets, leaving the polymer chain intact
- Chemical recycling, breaking condensation-type polymers down to their monomers
- Processing back to feedstock through catalytic or thermal means (circular)
A good example of the petrochemical industry’s commitment to sustainability and the circular economy is the work being undertaken by SABIC, a leading global chemical company based in Saudi Arabia. (On 27 March, Saudi Aramco signed a share purchase agreement to acquire a 70% majority stake in SABIC.) SABIC built a feedstock recovery pilot project in Germany that uses plastic waste to produce synthetic feedstock. This recycled feedstock can be processed into any desired petrochemical product. The company intends to collaborate with others to build the first commercial plant in the Netherlands to refine and upgrade a valuable feedstock, which will be produced from the recycling of low-quality, mixed-plastic waste otherwise destined for burning or a landfill. I am certain that SABIC is not the only company pursuing such strategies to address the growing challenge of plastic waste. The potential is huge for reducing the growing volume of plastic waste by turning it into other products. I expect to see more R&D investment by our petrochemical cousins in this area.
Tires are another great opportunity to turn waste into value. Some studies show that every year almost 1 billion tires are disposed globally, with 50% of those tires going either to landfills or burners, allowing a valuable resource to go to waste. According to the US Tire Manufacturers Association, modern tires include up to one-quarter synthetic rubber, which is made of polymers that come from crude oil. Tires include steel, carbon black, silica, and other materials that also have recycling potential. Several companies around the world have established sustainability programs and started recovering these valuable resources in waste tires with the goal of recycling a significant percentage of tires. The future of tires is looking even more circular.
Waste to energy can also be a business opportunity. Energy can be created from waste products through primary treatment or processing. This often comes in the form of electricity, heat, or fuel. Recovering energy from waste is both circular and a means of meeting the energy needs of a growing population.
The benefits of pursuing a sustainable, circular approach to consumption are clear. We can reduce the impact on our planet’s resources, reduce our carbon intensity, and decrease the growing piles of waste materials. There can be a clear case for recycling and reuse, creating new business opportunities. Our companies can make these principles part of their core business across the value chain. Significantly reducing waste will require more investment in R&D as we find new ways to reuse things that would otherwise end up in a landfill. Identifying these new opportunities will be key to reducing our industry’s environmental impact.
I hereby challenge our industry to explore breakthrough technologies that will allow us to achieve this noble objective. We must act together and collaborate with governments and technical, operational, academic, and social societies. We must lead by example. We owe that to the future generations living on Earth for hundreds of years to come.
To contact the SPE President, email president@spe.org. Follow him on Twitter: @neaimsa.