Closed loop drilling (CLD) systems and managed pressure drilling (MPD) are challenging long-held industry ideas about well control. This realignment in philosophy is happening because of a unique ability to precisely monitor, analyze, and control wellbore pressure in real time.
These capabilities are the basis for a growing number of proactive and reactive methods and tools that are solving many conventional well control problems. This is particularly true in the extremes of deepwater drilling, in which managing wellbore pressure plays a principal role in safety, efficiency, and even the ability to drill the well. Fig.1 presents many of the critical issues addressed by advances in MPD.
Although the number of deepwater MPD applications is relatively small, the advantages being achieved with closed loop systems are driving its increased use and the development of specialized deepwater MPD technology and drilling rigs.
Monitoring and Control
MPD reduces well control events and pressure-related wellbore problems by addressing two key challenges associated with conventional methods: the uncertainty of the predrill model and the inflexibility of the resulting well design and mud regimes. These challenges are overcome by a dynamic capability that is counter to static predrill models.
Uncertainty is reduced by very precise measurements of wellbore pressure profiles in real time. Just as important, MPD complements this information with equally precise real-time control. This dynamic solution is proving a key enabler for enhancing safety, efficiency, and operational capabilities in deepwater drilling.
To achieve these capabilities, MPD builds on the inherent characteristics of a closed loop system. Within this contained, pressurized wellbore environment, pressure is closely monitored. Pressure changes, such as those caused by an influx, loss, or ballooning, are rapidly detected and controlled in increments as small as a few barrels. Accurate fingerprinting of these minute pressure oscillations quickly identifies the event, which both informs an effective response and avoids a misdiagnosis that can exacerbate the condition.
The MPD control response is initiated at the surface by automatically or manually varying the annular backpressure by using a specialized MPD choke manifold. These changes within the closed fluid system are used to manipulate downhole pressure without the delay, cost, and imprecision of changing mud weight.
The ability to immediately dial in and hold the desired wellbore pressure changes the well control equation fundamentally with a new set of proactive and reactive pressure management options.
Micro influxes that are the precursor to well control events are quickly managed before they can escalate into a kick. When kicks occur, they are rapidly identified, controlled, and circulated out of the well. This mitigates a significant source of risk and nonproductive time (NPT).
In deepwater wells, precise pressure management is also critical to navigating narrow drilling windows between the pore pressure and the fracture gradient. Similarly, it is central to managing transitions between high- and low-pressure zones to avoid kicks and losses, and to optimizing casing setting depths.
Solution to Riser Gas
MPD monitoring and control is also solving the old deepwater well control problem of riser gas. Gas in the marine riser presents a significant challenge to conventional well control because it is above and beyond the effect of the blowout preventer (BOP) system. While gas handling systems and methods provide a solution, it is reactive in nature and limited in its control ability.
MPD’s proactive and reactive response to riser gas results in a safer, more effective solution. The proactive approach uses early kick detection and control capabilities to achieve a major reduction in the incidence of reservoir gas entering an oil-based mud system at depth and dissolving into it without being detected, only to come out of solution in the drilling riser and above the subsea BOP. Should gas occur in the riser as the result of an influx or entrained gas, the MPD system provides a controlled means of circulating it out of the riser and dealing with any remaining gas downhole of the BOP.
New Rigs and Technologies
This success in solving many of the problems that have stymied conventional well control is driving the development of new technologies, CLD-ready rigs, and industry guidelines. A major technical step in the deployment of CLD systems in deep water on dynamically positioned (DP) drilling vessels was the development of the industry’s first rotating control device (RCD) that is made up below the tension ring and integral to the riser package of a DP drillship.
A below-tension-ring (BTR) RCD was first deployed in 2010. The device contains the annular flow and redirects it to help form a closed loop circulating system, thus making the device a key component of a deepwater MPD system.
The availability of CLD-ready rigs is crucial to the adoption of the technology. To meet the demand, existing vessels can be refitted to accommodate a CLD system, while new CLD-ready designs, such as Stena Drilling’s DrillSLIM semisubmersibles and drillships, are entering the market. Rig availability will also benefit from the development of industry guidelines, procedures, and standards for equipment procurement, rig modification and design, and training.
Driving all of these developments are the impressive results being achieved with CLD rigs and MPD methods in deepwater applications around the world.
HP/HT Drilling
In drilling a high-pressure/high-temperature (HP/HT) well in the North Sea, MPD saved approximately 75 days compared with conventionally drilled offset wells. Five separate influxes were successfully managed over 9 days. The ability to quickly identify high-pressure, low-volume gas stringers while drilling enhanced safety and well control, reduced NPT, and eliminated the need for a planned liner section.
On the Norwegian Continental Shelf, a surface pressure of nearly 15,000 psi made pore pressure evaluation and kick detection critical to drilling an exploratory well. A key objective was setting the 9⅞-in. production-casing shoe as close to the reservoir as possible, facilitating the drilling of an 8½-in. section to total depth (TD) within a very narrow 0.4 ppg drilling window.
MPD helped avoid well breathing problems while maintaining an overbalanced wellbore. Using the closed loop system saved an estimated 10 rig days and USD 7.5 million while reducing risk and improving safety.
Narrow Windows; Total Losses
When planning a deepwater exploratory well in Indonesia, limited pore pressure and fracture gradient information caused significant uncertainty in the predrill model. MPD was selected as a means to monitor and manage pressure in the difficult conditions. The drillship application was enabled by the industry’s first use of a submerged rotating control device, Weatherford’s SeaShield Model 7875 RCD, which was used in a BTR installation as an integral part of the riser.
To drill the difficult well, the MPD constant bottomhole pressure method was used at first. In early drilling, a 2-bbl influx was detected and successfully processed out of the wellbore. When severe losses occurred deeper in the well, the MPD drilling mode was transitioned to pressurized mudcap drilling and the well was drilled to TD.
Riser gas was eliminated in drilling this and seven subsequent exploratory wells. There was no incidence of formation gas breaking out of solution above the BOP and inside the riser. The MPD control system algorithms detected at least five flow anomalies that were kept to minimal volume and safely circulated out of the well.
There was only one instance in which an influx was circulated out through the riser. The process started with closing the subsea BOP and the MPD annular BOP (located below the RCD at the top of the riser) to isolate the influx. The mud and influx in the riser was then circulated out through the automated MPD choke manifold and the rig’s high-rate mud gas separator. Once the influx was out of the riser, the mud was weighted up, the subsea BOP was opened, and the rest of the well was circulated to a higher mud weight while applying MPD control.
Borehole Instability
Recent experience in the deep waters offshore Ghana further illustrates the advantages of drilling with closed loop systems. While conventional drilling had failed in two attempts because of pressure-related wellbore problems, MPD enabled the well to be drilled without borehole instability issues, underreaming, or contingency liners. Riser gas was routinely mitigated.
The first drilling attempt encountered an unstable rubble zone and sharp pore pressure and fracture gradient changes. The well packed off several times because of sloughing shale and progress stopped. The main wellbore was plugged back and a sidetrack was drilled using a higher mud weight to prevent sloughing. Drilling eventually took a 16- to 20-bbl influx and the sidetrack was shut in.
The next attempt 4 years later used a CLD rig and MPD to control wellbore pressures, provide stability in the rubble zone, and successfully drill the well. In addition, the 14¾-in. section was drilled deeper than the planned objective, which allowed the 13⅜-in. casing shoe to be set deeper and eliminated the need for the 10⅝-in. section.
Deepwater Well Control
Real-time insight into the wellbore pressure environment combined with real-time pressure control form the pivot point for a new way of looking at well control. In deepwater applications, this perspective is quickly gaining ground as the advantages of CLD systems and MPD are fully understood, and the technology and rig systems become available. The operator, rig contractor, and service company work together to integrate the enhanced well control capabilities of the MPD system (Fig. 2), thus bridging the gap between traditional primary and secondary well control.
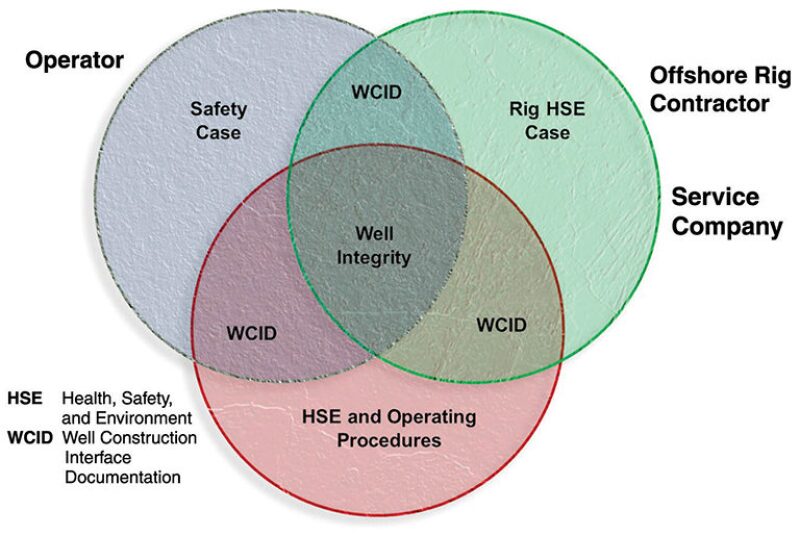