In November, a webinar presented by the Society of Petroleum of Engineers titled “Selection and Troubleshooting of Flotation Equipment for Produced Water Handling” covered the varieties of current technology for flotation equipment. It provided an in-depth look into flotation technology and the options surrounding offshore applications.
“There are several types of technologies involved in flotation equipment,” said John Walsh, principal engineer of oil and gas water treating at GHD Group.
His presentation covered the mechanism of flotation and equipment design considerations. He pointed out what designers must account for and what must be avoided when designing flotation equipment for a specific installation. “It is important to understand the differences, and to understand why certain types of equipment work well in certain applications and others do not,” he said.
Selecting flotation equipment is like buying a vehicle, Walsh said. Proper selection depends on the specific needs of a project and the equipment features. There are models that provide 95% separation efficiency. “This equipment is very large and heavy,” Walsh said. He said that these systems have been installed offshore, but with the penalty of weight and space. More compact systems are available that provide only 50% separation efficiency. There is also equipment that provides separation efficiency in the range of 20% to 40%, which is extremely compact and relatively inexpensive.
Depending on the separation efficiency requirements, a system can be designed to fit the specific need of an offshore application. “There are enough options to design flotation equipment based on the desired level of performance required, what a company is willing to invest, and the amount of space that can be sacrificed,” Walsh said.
Some other variations of flotation parameters in the industry are total cost, schedule, operability, and after-sales service. However, separation efficiency remains the most difficult to predict for an operator or designer, Walsh said. In relationship to efficiency and overall cost, flotation equipment varies widely from one technology to another (Table 1).
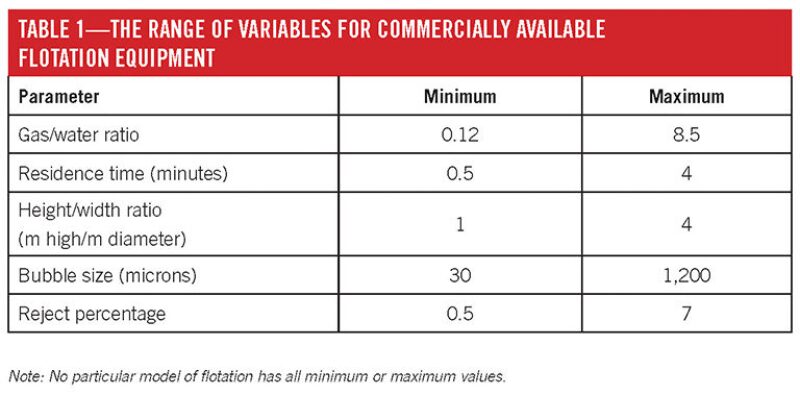
Flotation is a secondary process installed downstream of primary separators. It is typically capable of capturing smaller drops than primary separation and hydrocyclones. “The reject flow rate and oil concentration must be accounted for in the overall process flow,” Walsh said. This means that the separators must be large enough to handle the flotation reject flow rate. According to Walsh, the preferred process lineup ultimately allows the reject from a primary separation to capture the oil contained in the oily water recycle. By routing flotation reject to a slop tank for chemical treating and settling time, operators can reduce recycled chemical. This also provides additional oil/water separation before recycling into the rest of the system (Fig. 1).

Walsh outlined the fundamentals of flotation and separation, chemical treating, and other factors related to separation efficiency. The primary focus was proper selection and design factors when considering flotation equipment. “It’s important to understand what kind of equipment you are considering buying or you have in the field that you are trying to troubleshoot,” Walsh said. (See Fig. 2.)
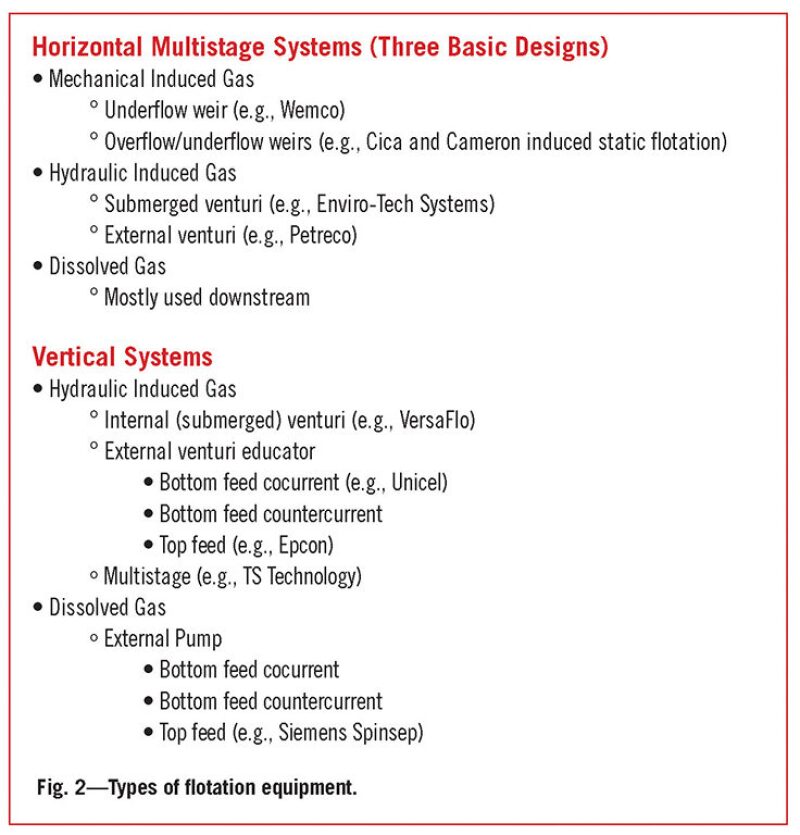
A recording of this webinar can be viewed at https://webevents.spe.org/products/selection-and-troubleshooting-of-flotation-equipment-for-produced-water-treating