Small- and medium-scale liquefied natural gas (LNG) is different from conventional LNG in trading distances, target markets, and application areas. Small- and medium-scale LNG may better coordinate needs between regional gas producers and consumers. Cluster LNG is a new concept of LNG technology suitable for emerging market environments. High performance of cluster LNG originates from higher liquefaction temperature and the adoption of efficient refrigerants for the temperature ranges.
×
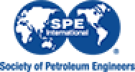
Continue Reading with SPE Membership
SPE Members: Please sign in at the top of the page for access to this member-exclusive content. If you are not a member and you find JPT content valuable, we encourage you to become a part of the SPE member community to gain full access.