While storage and logistics are critical elements of the viability of water reuse, if the water chemistry is not fit for gel fracturing formulations, it will not matter how much is stored in centrally located impoundments. Millions of barrels of flowback, produced, and fresh water or brackish waters are available daily for any number of uses, but only a select few exploration and production companies have taken the necessary steps to implement a quality program that works effectively.
In addition, the commitment to instituting such a program is far more simplistic than most producers believe it to be. What is required, however, is a desire to manage for the long term, not just for a period of drought or in a reactionary way because of government regulatory rhetoric.
Background
An estimated average of 5 million gallons of fresh water per well are pumped when fracturing a shale formation. Given the new regulations and increasing droughty conditions, water management has become a crucial step in well planning. Many processes are in place to treat flowback water for reuse or disposal, but various obstacles have also emerged. The distinctive characteristics of organic and inorganic matter in these waters have given rise to various potential risks when reused. Of the various contaminants, boron is especially worrisome because of its use as a crosslinker in the hydraulic fracturing process. The presence of boron poses the threat of prematurely crosslinking the polymer and upsetting the delayed rheology desired in the gel formulation.
For this reason, research on boron removal from these fluids was conducted. The removal of boron from water poses a significant challenge. Many technologies exist to remove boron from water in a clean-water application, but the selective removal of boron is a different issue altogether. Because of the molecular weight of boron and its dissociation, many traditional wastewater treatments leave the substance untouched.
The behavior and chemical composition of boron varies in an aqueous environment. Boron is a metalloid and behaves as a Lewis acid and exists primarily as un-dissociated boric acid or borate ions. The borate ions dominate at higher pH, while boric acid dominates at lower pH (Fig. 1). This nonionic form of boron yields a very stable molecule difficult to selectively remove.
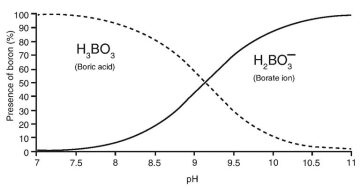
Current Technologies for Boron Removal
Distillation
The most obvious solution to deal with boron is a clean-water approach. The primary method of obtaining fresh water absent a freshwater well or lake is through a distillation process. With advances in efficiency and mechanical vapor recompression systems, distillation to produce fresh water has improved over the years. These thermal systems may be fueled by the gas being recovered or even flare gas, but the low flow rates achieved require that the water be stored for extended periods of time, which will likely trigger bacteria issues.
Reverse Osmosis
Reverse osmosis (RO) reclaims fresh water from brines at higher flow rates than those associated with distillation. The use of RO for oilfield waters is limited by the salinity to approximately 100,000 ppm. A higher salinity would yield a system requiring multiple passes to fully clean the influent.
Additionally, RO at a neutral pH provides poor boron rejection. The boric acid at neutral pH is suspected to diffuse through the membrane in a manner similar to water itself. Therefore, to achieve greater boron rejection, the pH must be elevated.
Although an RO system may be suitable in brackish waters, special seawater membranes along with various pretreatment steps would be necessary in the concentrate brines observed in the Bakken play. In this case, the resulting effluent remains brine water, but is less concentrated. Ideally, the boron would be rejected at 99%. If the water is completely reclaimed, it may be reused in any way deemed suitable.
An additional limitation with RO systems is the efficiency of the process. Typically, two-thirds of the water is reclaimed and one-third is concentrated waste. The concentrate stream must be disposed of, or it may be again treated. Adding RO to the equipment currently employed would be ineffective and uneconomical. Rather, RO should be treated as a separate system with quite high initial capital costs.
These systems that yield fresh water present the opportunity to reuse wastewater in new ways, but the flow rate limitations and initial capital cost are to be considered. Along with clean-water applications, there are various systems to treat the water selectively and include boron in the process.
Several treatment trains have been developed that use new pretreatment technologies, as well as new membrane technologies that are capable of resisting typical fouling issues associated with hydrocarbon contamination.
Ion Exchange
Ion exchange is the most selective of the systems researched. The ion exchange system uses a boron-specific functional group, N-methyl glucamine (NMG), to complex with boron at a neutral pH and provides an effluent with boron concentrations of less than 1 mg/L. The system requires pretreatment to remove suspended solids and large particles of oil in the water. The resin is regenerated, and its estimated life ranges from 3 years to 5 years. The systems are primarily used in clean-water setting, so the high boron concentrations seen in the Eagle Ford and Bakken call for the use of multiple units in line.
In two estimates, a system operating at 20 bbl/min (840 gal/min), operating 12 hours per day, and removing 100 ppm of boron incurs an initial cost of USD 700,000 for resin. This cost is based on the resin volume and does not include the cost of manufacturing the columns and associated equipment.
The high cost of ion exchange is in part a result of the small loading capacity of the resin. The functional group is very selective, but only removes 5 grams of boron per liter of resin, thus this type of system is best used as a final polishing step, or at much lower flow rates.
Table 1 shows the results of ion exchange resins tested from Purolite and Dow Water and Process Solutions (Amberlite IRA). The tests were conducted by placing 100 mL of clarified flowback or produced water in contact with 120 grams or 60 grams, respectively. The mixture was stirred for a minute prior to filtering and sending to a laboratory for analysis. The fluids tested were from Marathon wells in the Eagle Ford formation.
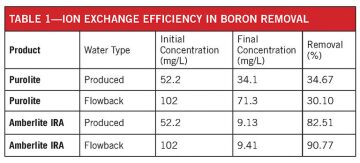
Table 1 shows that the Amberlite IRA resin is very efficient, but the high cost of the resin limits the size of the project. If operating the system at 20 bbl/min and regenerating after a 12-hour work day, the resin cost would be approximately USD 881,263. If the resin were regenerated every 4 hours, the cost would still be approximately USD 250,000 because of the high boron content in the flowback water. The chemical cost of regeneration is approximately USD 0.03/bbl.
Electrocoagulation
Electrocoagulation destabilizes suspended contaminants by contacting the fluid with electric current. The technology is optimal in systems with a fair amount of conductivity, typically resulting from total dissolved solids (TDS), making it applicable in oilfield wastewater.
The suspended contaminants fall out and form sludge, but a smaller volume of sludge is produced when compared with similar chemical processes. The efficiency is dependent on current density, pH, electrode spacing, time, and initial concentration.
Competitors are employing this technology in the field to treat wastewater, but the technology does not specifically target boron.
There is literature that suggests a removal efficiency of 95% is possible by simply adjusting the current density and increasing the pH. An electrocoagulation system may be of interest in the future, but the initial capital cost of building a 20+ bbl/min unit would require working in conjunction with the manufacturer. A pilot-scale system and proper sizing may yield a system with a low operating expense and adequate flow rate.
Chemical Additions to Remove Boron
In addition to these systems, many different materials have been added to waste streams to remove boron, none of which precipitate boron directly. Forming a complex with boron in a manner similar to the NMG functional groups is a common topic in patents.
A patent using polyvinyl alcohol (PVOH) was tested in this study.
Polyvinyl Alcohol
A mechanism similar to the ion exchange functional group is achieved by putting aqueous boron in contact with water-soluble cationic polyelectrolyte, PVOH, and anionic modified PVOH under alkaline condition, followed by removal of the generated coagulation. The invention uses an anionically modified PVOH for lower concentrations, typically less than 30 ppm.
The mechanism is similar in that boron is moved to dehydrate a cis-diol group and when in contact with a tertiary amine group, forms a stable complex. In the NMG functional group, this takes place on the surface of the resin, where the boron adds on the cis-diol group and the attached amine group neutralizes the charge.
With the PVOH addition, the polymer provides the polyol end sites, followed by the addition of polydiallyldimethylammonium chloride (polyDADMAC) to provide the amine group.
Testing of this method for boron removal was conducted on flowback and produced water from the Eagle Ford play (Table 2) and included various PVOH grades, combinations and doses of flocculants, polyacrylamides, pH adjustments, mixing time adjustments, and changes in the PVOH preparation.
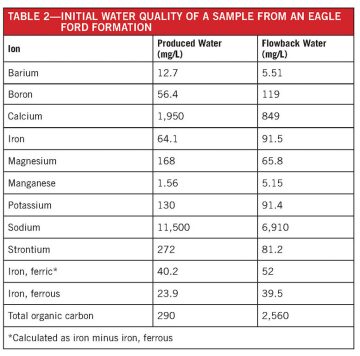
The majority of the testing was done with a two-stage process consisting of 1) iron and suspended solids removal with a flocculent, pH adjustment, and polyacrylamide, followed by 2) PVOH addition, pH adjustment, and polyDADMAC addition. Testing of the PVOH was first conducted on a boric acid solution made by diluting boric acid to a concentration of typically 100 ppm boron.
Initial polymer makeup did not provide a homogenous mixture at 5% w/w (weight-by-weight) or greater.The PVOH grades tested were PVA 105, Mowiol 30-98, and KL-118. After contacting the manufacturer, the three polymers were blended and brought to 90°C to provide a homogenous mixture.
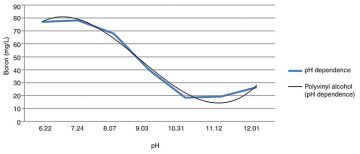
Of the three polymer grades tested for boron removal, all proved to be adequate, with PVA 105 and KL-118 being the simplest to make up. The combination of a PVOH with a PVOH modified with carboxyl groups proved to be the most effective, as expected, but cost-prohibitive. Because the concentration desired does not need to reach zero, the addition of a single PVOH proved sufficient. The findings in the boric acid solution show the most efficient boron removal with a 5% w/w PVA 105 at a pH>10 (Fig. 2).
After testing to find the necessary dose of PVA 105, the preferred method to conduct the experiment is to 1) add 15 mL of 5% w/w PVA 105, 2) raise the pH to 10 with sodium hydroxide, and add 0.8 mL of 20% w/w polyDADMAC.
The 100-mL tests were conducted on a stir plate. The fluid was filtered through a paper towel to remove the sludge produced. A boron removal rate of approximately 75% was achieved with a final boron concentration of 25.3 ppm.
After the ideal doses were found in the boric acid solution, the flowback and produced water were tested in single-stage and two-stage processes.
Hydrogen peroxide and ferric chloride were tested and compared as coagulants, and both were found suitable for clarification of the fluid. The flowback water maintained a yellow hue, even after treatment with both of the coagulants, but the hydrogen peroxide lessened the color more than the ferric chloride treatment.
After further reading, a test was conducted using ferric chloride followed by hydrogen peroxide for coagulation. This method removed more of the yellow tint. With the use of sufficient hydrogen peroxide, the color may be completely removed from the fluid.
An issue encountered during the testing of the PVOH in the produced and flowback waters was the formation of gel. After conducting further testing, it was discovered that in the presence of salt, the PVOH crosslinks further and turns the entire volume into a gel. If left spinning overnight, the gel sheared and the polymer separated from the fluid in the form of a plastic-like ball. Testing with different polymer makeup procedures and additives proved unsuccessful, and the removal efficiency was also affected.
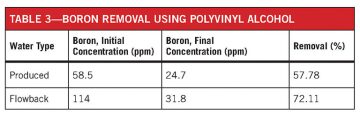
Table 3 shows the results of using PVOH in a two-stage process consisting of clarifying the fluid, buffering the pH back to neutral, and the addition of boron-removal chemistry. The treatment steps were 1) the addition of hydrogen peroxide; 2) the buffering of pH; 3) the addition of polyacrylamide; 4) bringing the pH back to 7; 5) the addition of PVA 105; 6) the buffering of pH to 11; and 7) the addition of polyDADMAC.
The process is efficient when conducted in a boric acid solution, but the high TDS of the wastewater presented a problem. In the presence of salt, rather than achieving a precipitate with the boron entrained, a gel was formed. It is suspected that the gel was the result of enhanced crosslinking in the presence of salt. The resulting gel takes hours to shear, and thus poses a serious problem in the separation process.
More work may be conducted in the future to propose a similar mechanism for boron removal under brine conditions using a different polymer.
Because of the high volumes of chemicals required by this method, an economical evaluation is necessary to see if the invention is cost-feasible. The typical clarification chemistry would carry a chemical cost around USD 0.50/bbl, dependent on the desired pH values. The added cost of boron removal chemistry pushes the price to more than USD 6/bbl. The prices of PVA 105 at USD 5 kg and polyDADMAC at USD 1.40/lb resulted in costs at USD 3.96/bbl and USD 2.03/bbl, respectively. Therefore, alternative chemistries were investigated.
Lime
Lime has been used to remove boron from wastewater and has proven to be very effective. Slaked and unslaked lime have been used and shown effective. Temperature is an issue when using lime. Lime softening is routinely conducted at 90°C, a parameter uncontrolled in the field. Lime at room temperature is inefficient by itself at removing boron. Lime was used rather than sodium hydroxide for pH buffering, but a considerable increase in efficiency was not seen.
Magnesium Oxide
Other chemical additives work by adsorption, coprecipitation, or a combination of the two. The primary limitation in this process is the large dose of adsorbent necessary. As the dose increases, the efficiency increases because of the availability of an increased surface area.
Most of the work done on the adsorption of boron has involved magnesium oxide. By adding magnesium oxide to the water and elevating the pH to its point of zero charge, electrostatic adsorption occurs. The maximum efficiency is noted at pH 10, but the process involves large amounts of chemical per gram of boron removed.
Attempting to coprecipitate also poses issues, since a pH of less than 2 is required to fully dissolve the magnesium oxide. Additionally, dissolving the magnesium oxide is an exothermic process, which generates a large amount of heat—an undesired health, safety, and environmental concern.
Testing conducted with anhydrous magnesium oxide showed high chemical consumption, as well as a high cost. Magnesium oxide successfully treated the produced and flowback water to levels of boron below 20 ppm, but at a cost-prohibitive dose. Cost was estimated at USD 65/bbl.
Magnesium Chloride
An alternative to magnesium oxide may be magnesium chloride. Research suggests that magnesium chloride yields a higher removal efficiency, and its use is not temperature-dependent. Anhydrous magnesium chloride is difficult to dissolve and exothermic, therefore, the hexahydrate form was used for testing.
The magnesium chloride hexahydrate may be added directly or dissolved in water and added as a solution. When the pH is brought up to 11, brucite (the solid mineral form of magnesium hydroxide), magnesium chloride hydroxide, and boron are precipitated.
The suggested mechanisms are that the boron adsorbs onto the precipitate, or it is entrapped during the precipitate formation. This method of boron removal was proven to be effective at room temperature.
The limitations of this method included reduced efficiency in the presence of silica and a high chemical consumption. For every gram of magnesium chloride added, a gram of sludge was produced. The optimum pH for boron removal ranged from 10 to 11 (Fig. 3).
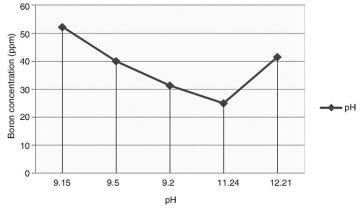
The testing conducted with magnesium chloride proved successful in the removal of boron at two-thirds the dose and one-sixth the cost of raw product when compared to magnesium oxide. The produced water with an initial boron concentration of 60 ppm was treated effectively at a cost of approximately USD 2/bbl. The cost of the magnesium chloride at USD 0.22/lb puts the flowback water treatment at USD 2.31/bbl, excluding the coagulant and caustic soda.
Addition of magnesium chloride in a single-stage process is a viable option for boron removal from produced and flowback water, but the chemical consumption and sludge production must be kept in mind.
Conclusion
The testing conducted on boron removal proved that it can be selectively removed from flowback and produced waters. The testing also showed that the processes required are complex and typically can be expensive if no thorough investigation has been done to mitigate costs. Boron removal via chemical additives is possible, but large chemical demand is involved.
Further studies are necessary to develop an efficient polymer or highly selective media to remove boron. Precipitation using softening may be a viable option, but temperature control is necessary. With appropriate testing and sizing, alternative processes such as RO or electrocoagulation can be used for boron removal.
There has been work conducted on water reuse for hydraulic fracturing, and the obstacles encountered are being resolved. Alternatively, salt-tolerant polymers have been developed to allow contaminated brines to successfully stimulate a well for a high rate of hydrocarbon recovery. Also, crosslinking polymers are being developed by pressure pumping companies to control the rheology of a gel in the presence of boron. Given these new developments, water reuse is sure to remain a priority within the oil and gas industry for years to come.
A treatment train was developed to effectively remove boron to acceptable gel fracturing formulation levels in waters with moderate TDS for less than USD 2/bbl. This level of pricing associated with pretreatment and subsequent removal of boron and other constituents from a water source is superior to current water-sourcing methods, such as the trucking of fresh water or deep-well construction.
For Further Reading
Ezechi, E.H., Isa, M.H., and Kutty, S.R.B M. 2012. Boron in Produced Water: Challenges and Improvements: A Comprehensive Review. Journal of Applied Sciences (Faisalabad), 12 (5): 402–415.
Rahman, I.Y., Nelson, Y., and Lundquist, T. 2009. Removal of Boron from Produced Water by Co-Precipitation/Adsorption for Reverse Osmosis Concentrate. MS thesis, California Polytechnic State University, San Luis Obispo, California (August 2009). http://digitalcommons.calpoly.edu/theses/156/.
Suzuki, H. and Yabusaki, K. Agent for Removing Boron and Method for Removing Boron. Patent EP 1900409 A1. http://www.google.com/patents/EP1900409A1?cl=en.
Dennis Rodarte is a staff chemist and technical adviser at Express Energy Services, and Robert (Robby) S. Smith is the water resource business development director at Express Energy Services.