All completions systems should enable the safe and profitable extraction of reserves. Implicit in this statement is the presence of a stable, consistently performing completion system—in other words, a system with reliable hardware. This means that the completion system will enable production (or injection) with no system failures, over an expected span of time. This time span can range from 1 week for unconventional completions (fracturing plugs) to 30 years for deepwater completions. In all cases, reliable operations over some time t, or R(t), is the expectation.
A goal for the completion system designer should be to maximize the useful life of the completion system (Fig. 1). In practice, this is achieved by minimizing what can be termed “infant mortality” and delaying the start of wear out.
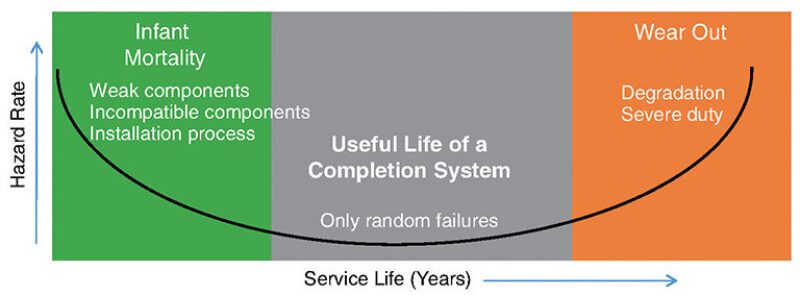
To maximize R(t), reliability of components, configurations, and processes must be maximized.
Component Reliability
Innovation leads to higher performance and optionality for most types of completion components. However, the development of new, innovative components also requires that their reliability be a design priority.
Today, important drivers of component reliability are industry codes and standards (ICS). The American Petroleum Institute, the International Organization for Standardization, and NORSOK are ICS organizations with extensive portfolios of product standards. Each organization routinely updates its legacy standards and creates new ones. The Advanced Well Equipment Standards Group is a newer ICS organization that has recently completed a product standard for inflow control devices and is creating standards for encapsulated cable and degradable materials. Overall, the pace of standards creation is accelerating.
A discussion of component reliability is incomplete without including the role of design for reliability (DFR) or design-assurance programs. These programs ensure that reliability receives due diligence in component development. The use of design failure mode effect analysis (DFMEA) is a cornerstone of an effective DFR program. These programs should be more prominent; this gap presents an opportunity for improvement.
So, considering the question, “Where have we been?”, the answer is that the journey to date has been one of continuing improvements in the reliability of completion components.
Configuration Reliability Is an Opportunity
Of the technical paper abstracts I re-viewed for the Completions feature in the April 2019 issue of JPT, 52% focus on completion configuration or optimization. Few abstracts focus on the ability of the completion configuration to perform reliably over long spans of time. Two critical aspects of configuration reliability are longevity and survivability.
Longevity is governed by material and configuration stability. Longevity can be estimated in the laboratory using information on the downhole environment at the time of design. However, unanticipated changes in the downhole environment over time could compromise the configuration’s ability to perform consistently. An example would be changes in treating programs, which may create unanticipated corrosive conditions that compromise components.
Some aspects of survivability can be assessed during component laboratory testing (run-in-hole speed, for example), but a major factor that affects survivability is the tortuosity of well paths. Tortuous well paths are a more frequent occurrence today, and survivability is exemplified by getting the completion to target depth, in good working condition, through such a path. If not planned for, tortuous well paths will stop the advance of long, rigid completion assemblies. In addition, the high mechanical loads placed on a completion assembly while traversing complex well paths can result in mechanical damage or premature component actuation. However, progress is being made in assessing these scenarios in terms of survivability. Paper SPE 191050, “Geometric Wellbore Analysis for Improved Completions,” by Pile et al., contains information on the use of a newly developed method for assessing installation risks.
Improved outcomes also can be achieved by practicing design-risk assessment on completion configurations routinely. Conducting a system-level design risk assessment in the form of a DFMEA can lead to the discovery of hidden problems related to interfaces, ratings, or operational sequences among components. A DFMEA will identify mitigating actions that eliminate these problems or minimize their impact. Mitigating actions may result in component design changes, configuration changes, changes to installation, or other procedures, but, at a minimum, will enable team members to understand the risks. Identifying and mitigating risks as early as possible is the most cost-effective use of risk assessment (Fig. 2). A few hours spent assessing a configuration using DFMEA in the office will provide insurance against weeks of nonproductive time in the field.
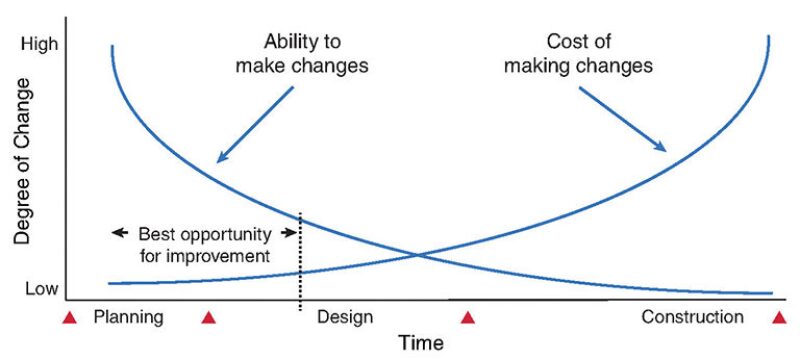
Process Reliability
Many oilfield activities involve processes that are low-frequency but high-impact. Many completion installations fit into this category. Even though a process may seem straightforward, the consequences of failing to execute it correctly can be costly. A poor process can lead to human injury or fatality, and damage to assets and the environment.
Which process presents the highest risks in your completions? What causes that process to fail to deliver the intended outcome time after time?
Assume for a moment that an operator has had mediocre results installing a completion system in difficult wellbores. In this scenario, high nonproductive time has been the result. The component suppliers have been told to redesign their components to fix the problem, but even after they comply, some of the problems persist. What, then, is the root cause of these failures? The answers may not be obvious until a process failure mode effect analysis is conducted. That analysis will enable the discovery of erroneous process steps and identify mitigating actions that eliminate or reduce the probability of the error occurring.
Humans create and execute processes. Regardless of the process, tasks that are not crafted properly will lead to human error; it isn’t a matter of if, but a matter of when. However, that analysis can be used to discover when human error is likely in a given task, and can identify mitigations that eliminate or reduce the probability of the error. As with design, mitigating process risks as early as possible is preferred.
Where Should We Be Going?
Fundamental to reliability is the idea of expectations. What are your expectations for completion-system reliability? Is your completion system designed with reliability in mind? Have design-risk assessment and process-risk assessment been used to discover and mitigate risks? Will your completion system deliver repeatable results in the second, third, or tenth installations? Do you have a process in place for reporting failure and managing corrective actions? Such a process enables organizational learning and continuous improvement.
So, instead of answering the question “Where are we going?”, I would rather give you some ideas about where we should be going.
What our industry practiced yesterday is not necessarily optimal for today’s business environment. My recommended path forward includes elevated focus on design and process-risk assessment. Completion components and systems should be rigorously assessed for design risks. Processes related to completions, such as installation, should also be rigorously assessed for risks related to human error; health, safety, and environmental incidents; and damage to assets. Risk assessment should be conducted as early as possible in the completion-design process. It should also support organizational goals related to continuous improvement and organizational learning. When implemented properly, design and process-risk assessment will minimize nonproductive time.
![]() | Doug Lehr, SPE, is senior manager for DFR activities at Baker Hughes, a GE company. His current focus is driving reliability improvement in new products. Previously, Lehr was global director of technology, wellbore intervention. He has 39 years of experience in the development of downhole tools for completion and intervention applications. Lehr’s research interests include high-pressure/high-temperature applications, advancing reliability in downhole tools, and accelerating innovation. He has authored or coauthored eight technical papers and holds 28 patents. Lehr holds a BS degree in mechanical engineering from The University of Texas at Austin and an MBA degree in finance and marketing from the University of Houston. He was an SPE Distinguished Lecturer for 2012–13 and is a member of the JPT Editorial Committee. Lehr can be reached at douglas.lehr@bhge.com. |