This paper describes a comprehensive field study of eight horizontal wells deployed in the stacked Niobrara and Codell reservoirs in the Wattenberg Field (Denver-Julesburg Basin). The overall goal was to understand the geometry of the hydraulic fractures (propped) and the producing volume with respect to completions design, target reservoirs, and well spacing. Through this understanding, the asset can be developed more effectively and economically.
Field Description
The Wattenberg Field is a basin-center petroleum accumulation located northeast of Denver, from which hydrocarbons have been extracted over the last 50 years. Development in the Wattenberg Field began in 1970 from vertical J‑Sandstone wells, with production of the Niobrara following in 1976. In 2009, horizontal development began in the Niobrara formation. The Upper Cretaceous sequence from Codell to Niobrara is the current focus of horizontal development in the Wattenberg Field.
Petrophysical Model
A robust 3D mechanical Earth model (MEM) provides the framework for data integration and physical simulations.
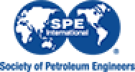