Performance optimization was demonstrated in thermoplastic sealing systems for oil and gas equipment using emerging technologies in 3D printing to manufacture multicomponent composite structures. A custom 3D printer was equipped with a patented print head designed for dynamic mixing of individual feed materials and paired with advanced print-planning procedures to enable fabrication of novel thermoplastic structures. In addition to supporting fabrication of sealing components for rapid response in oil and gas equipment, this technique provides a means of improving the overall performance of sealing systems without an increase in the size or complexity of the sealing assembly.
Introduction
The purpose of this study is to demonstrate the potential for performance improvements in sealing connections through innovation in flat-backup-ring (FBUR) architectures. A component-level approach to functional testing was taken with supplementation from more-traditional materials analysis.
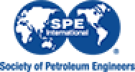