Murphy Exploration and Production Company, the operating subsidiary of Murphy Oil Corporation, currently operates approximately 700 producing rod-pump wells, which require treatments for corrosion prevention. Corrosion prevention is an important part of the production cycle. A rod-pump failure because of corrosion can lead to high repair costs and downtime; rods are especially susceptible to corrosion failure because of high-tensile loads. To make sure the well is operating safely, and that corrosion is prevented, batch treatment is performed on the producing wells. Batch treatment is a process of treating wells using a corrosion-inhibiting chemical and water mixture. The batch treatment process creates a protective film on top of the metal surface, shielding it from corrosion. This process is repeated, and the frequency is based on many well- and production-related variables to prevent rod-pump failure. To optimize the well-treatment program, Murphy developed a Robot Process Automation (RPA) procedure to alter the schedule dynamically using data algorithms and a mobile app.
Introduction
Analyzing the current procedures involved in production is crucial for determining best practices for increasing efficiency both onshore and offshore by maintaining quality of equipment. Incorporating technology not only gets things done quickly but also helps break down the process and deliver better results by efficiently allocating resources.
Murphy’s economical oil extraction depends largely on reducing wear and tear of downhole equipment and tubulars deployed at wells through regular monitoring and batch treatment to cut the risk of corrosion and costly workovers. Batch treatment involves injecting a mixture of corrosion inhibitor (CI) and water to reduce the rate of corrosion, in turn ensuring smooth flow of production at wells without glitches or a complete breakdown.
Being able to do this at lower costs at every single well leads to a major reduction in overall operation cost and ensures higher profits. Having a data-driven approach to scheduling batch treatment can also bring down frequency of treatment and avoid unnecessary use of resources.
Method
Batch treatment is when an imidazoline-based chemical mixed with water is injected and circulated from the head of the well down through the outer casing (OC) and up through tubing, coating all surfaces thoroughly along with the pump-rod surface in order to prevent corrosion, which can degrade the surface of steel, as illustrated in Fig. 1. Batch treatment serves two purposes: monitoring the layer of corrosion inhibitor on the rods and maintaining the coating to slow down the wear and tear of the equipment from corrosion to ensure longevity and smooth functioning.
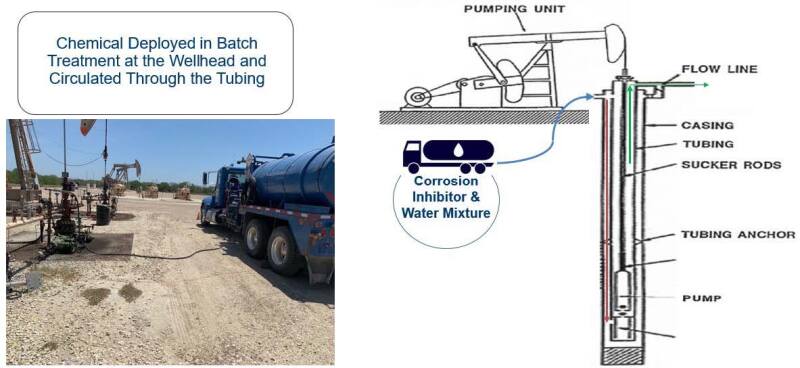
The chemical solution is formulated to protect pumping equipment against exposure to carbon dioxide, hydrogen sulfide, sulfur dioxide, and oxygen. However, overtreatment at wells that do not require it and undertreatment at those that do creates a risk of operations failing at both sites.
Murphy developed a Robotic Process Automation (RPA) to automate the work flows and handle treatment scheduling digitally by studying historical data. This entailed normalizing historical data, analyzing the well depth, tubulars sizes, rod designs, production rates, and application limitations to determine an optimal frequency of treatment and the volume of CI and water mixture required to enable a dynamic schedule. The app was developed as a tool for the field operators to keep track of all the past treatments performed by the vendor and the amount of CI injected. In addition, vendors use the app to keep track of upcoming treatments scheduled, which reduces the average treatment frequency from once every 15 days to approximately once in 28 days. Using data to determine schedules can also result in more personalized and focused attention for the well. The entire approach can be explained by a simple three-stage process, detailed in Fig. 2.
An automated process to schedule and prioritize batch treatment for wells with productivity as the criteria cuts out drawbacks of the current scheduling process. The previous work flow depended heavily on availability of technicians for the process. There was no validation of treatments done in terms of volume of CI injected or the efficacy of treatment. Costs of CI, water, and trucking were all higher because of frequent scheduling.
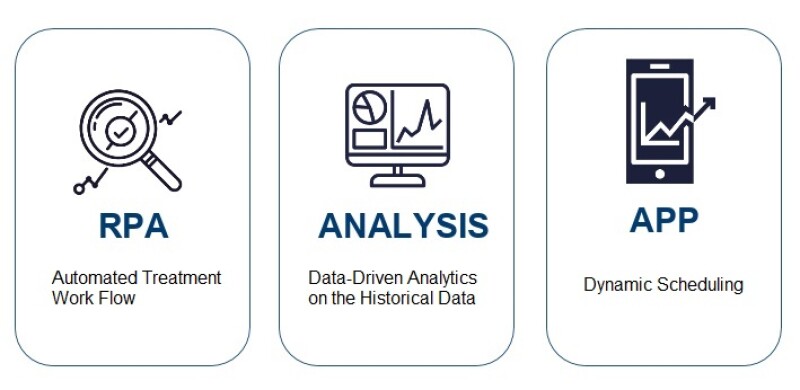
Literature research on batch treatment revealed that 1 gallon of inhibitor is sufficient to keep pumps working smoothly and that, even by conservative standards, 5 gallons is more than enough. Previously, however, the treatments used 10 gallons of CI and 42 gallons of water for the same purpose. Not only did this raise the risk of overtreatment but also every extra gallon that was pumped at each of the 700 wells for a given year cost approximately $150,000.
Having data about the resources, time, and cost used for a process such as this is crucial for communicating priorities, roles, and objectives to every team. Having data about downtime for equipment at a well, its effect on production, and the extra costs it will add can be used to predict which well needs more focus while scheduling batch treatments. The information then can help reveal opportunities at units that can use funding to unlock the true production potential.
The algorithm for dynamic scheduling of treatment is based on three key metrics: well-fluid production rate, depth, and bottomhole temperature.
Monitoring production gives insights into the estimated level of corrosion inhibition as fluid flow rate affects the thickness of the protective CI film applied, illustrated by the following directly proportionate relationship:
(CI)t ∝ Flow Rate (Fluid)
Hence, monitoring flow rate gives an accurate idea about the CI volume requirement for renewing the corrosion inhibitor film on the equipment. Maintaining a sufficient film reduces the risk of pitting corrosion from constituents of produced fluid such as H2S and CO2. According to the research conducted by Sunder Ramachandran on “Film Persistency of New High-Temperature Water-Based Batch Corrosion Inhibitors for Oil and Gas Wells," the layer of inhibitor liquid on the surface of a rod to protect it from corrosion has to be precisely 2.7 μm. If more CI mixture is added for the treatment, then the excess amount of CI will flow out, causing waste of the CI chemical, and, if less than 2.7 μm of mixture is added, then it would form patches of CI and the rod will not be coated fully, which would result in accelerated corrosion. Therefore, treatments should always be scheduled accordingly with the appropriate volume of CI necessary to ensure a thickness of 2.7 μm is maintained.
Not only does basing schedules for anticorrosion treatment on production from wells focus attention on wells with higher production and failure rates but also the process itself is scientific. As per NACE International in “Recommended Practice for Corrosion Control of Sucker Rods by Chemical Treatment,” the dosage of CI should be equal to 25 ppm based on the total fluid production between treatments. For example, a well producing 400 B/D would require 3 gallons of CI per week.
The volume of CI needed based on depth of a well can be calculated using the following equation:
Vol.(CI) = 2πh·CI·(R+2·IC+OC)·0.0043,
where
Vol.(CI) = volume of corrosion inhibitor (US gallons)
h = height of well (inches)
CI = film thickness (inches)
R = radius of pumping rod (inches)
IC = radius of tubing (inches)
OC = radius of outer casing (inches)
0.0043 = conversion factor for cubic inches to US gallons
Monitoring the level of corrosion affecting pumping units (Fig. 3) and threatening the production should continue to be studied to calculate how long each well can sustain without treatment. The proposed scheduling technique will adjust frequency and reduce use of inhibitor based on the data collected from wells while only the truck cost for a treatment may be higher for wells requiring more frequent treatments to produce optimal yield.
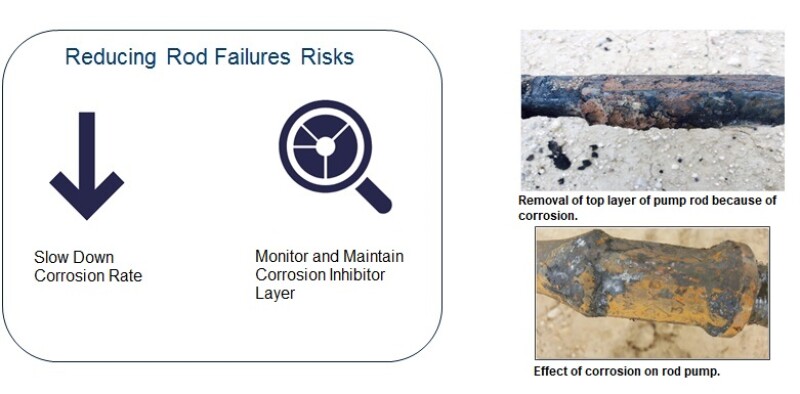
Another key metric that can indicate need for batch treatment is the effect of well temperature on the rate of corrosion. Higher temperature leads to more corrosion in a given time, and regularly monitoring the well status on the app using data analytics aids managers in scheduling the well treatment on time. On-time dynamic treatments frequencies should reduce failure rates.
Materials
Data collected in 2019 shows that the current scheduling patterns resulted in approximately 15,000 treatments a year. Meanwhile, the proposed scheduling determined through data optimization and application of theory at wells brought down the number of annual treatments to approximately 7,000 and resulted in spending approximately 51.1% less on batch treatment. Fig. 4 illustrates a sample dashboard used to track and compare metrics on the batch treatment work flow.
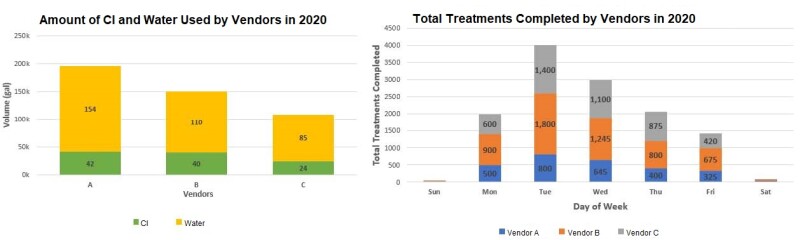
Constantly reworking processes and introducing data-driven, technology-based solutions to explore every opportunity to spend less is a step closer to business growth. All assumptions need to be carefully dissected and reviewed to make sure we evolve with times without also trusting forecasts too much.
Results
Scheduling treatments is a technology-driven process with an in-house app developed to capture only the most critical data such as the inhibitor to be used, the well to be treated, and the vendor responsible for the treatment. It is also intended to be used as a tool for the field operators to keep track of all the past treatments performed by the vendor, their frequency, and the amount of CI injected. Vendors can use the app to keep track of upcoming treatments scheduled. This transparency helped reduce the frequency of treatments to approximately once in 28 days, depending on the production of the well, compared with the previously fixed schedule of every 15 days. Using data to determine schedules can also result in more personalized and focused attention for the well.
Its user interface (Fig. 5) contains a display screen (Wells) that shows a list of all the wells and which of them have been validated after treatment or scheduled to be treated.
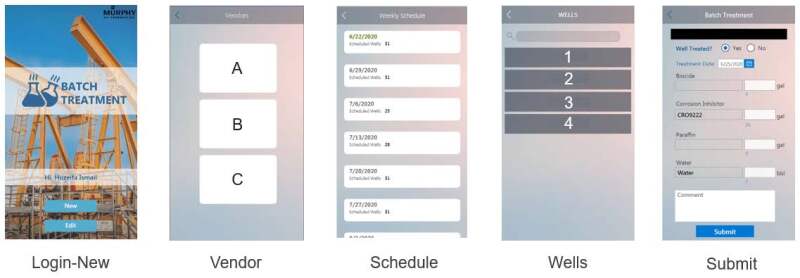
Historical records about when a well was treated and the frequency at which it has required treatment also will be reflected on the app. This can also play a role in monitoring the resources and time spent on a well in comparison to the fluid it has been producing. Keeping track of treatment costs and productivity at a well can help managers address problems with equipment inhibiting yield and to make necessary replacements or modifications to the process.
Conclusion
Safety at extraction sites is a major factor, especially during the coronavirus pandemic. Having regular data about equipment as well as production at wells through an app reduces need for technicians to visit the field. Information-driven treatment and maintenance of facilities also make sure there are not glitches or well failures to be addressed. Validation of wells after conducting batch treatment also becomes quicker and requires less manpower in the field if data about productivity and schedules are available. The app also speeds up the process by allowing a single person to make swift, more-informed decisions by integrating all historical and real-time updates on one platform.
Having a new approach and work flow in place for existing wells and extraction sites can prove to be revolutionary for setting up future projects. The data on fluid flow rates and its effect on CI can help in adopting more cost-effective methods to treat machinery at wells for new operations. While overall truck costs for batch treatment may increase, the long-term frequency of scheduling inhibitor injection goes down with increasing health of the equipment. The volume of inhibitor, along with the extra cost and manpower requirements, also goes down, and that is much higher compared with a potential increase in transportation costs. Current practices are driven by conservative estimates and routine procedures are not focused on optimizing results from the activity.
The proposed data-driven procedures aim to create a dynamic maintenance cycle that simultaneously looks at the past, analyzes real-time progress, and creates new strategies for future operations. In addition to generating higher production with lower costs, a small shift to data-driven processes makes a larger difference for current business operations and new projects in store for Murphy. A technology-savvy work culture also opens doors to easily move ahead toward a post-pandemic future where businesses will adapt to a new normal.