Today’s deepwater projects are not just larger and more expensive than in years past. They are the most technically demanding projects the oil and gas industry has endeavored to undertake since stepping out from the continental shelf, and will require more new technology than ever to successfully execute. The extreme environments of deepwater fields are driving the complexity of these megaprojects to new heights, with shorter deadlines to help offset production declines. Among the companies capable of carrying out these record-setting field development projects is installation and subsea construction firm, Technip.
On a recent visit to the company’s North American headquarters in Houston, Thierry Pilenko, chairman and chief executive officer of Technip, said his offshore clients are spending more money to produce the same amount of hydrocarbons they did a decade ago. “Ten years ago, one company was talking about five major projects, which were larger than USD 1 billion,” Pilenko said. “Now, they have several projects that are larger than USD 10 billion and 10 other projects that are more than USD 1 billion.”
The price tags of these projects have “exploded,” Pilenko said, because offshore oil and gas reservoirs are getting harder to find. So too is the challenge of safely producing those hydrocarbons and bringing them to the surface. “Today, we know how to drill at 3000-m depths,” he said. “But we are just learning how to produce it with qualified production systems.” Pilenko explained that the industry is not just pushing the frontiers of technology, but also geography. Offshore Africa, oil companies are proving how subsea fields can be developed with little to no onshore support infrastructure.
One of the latest examples is the Moho Nord field, offshore Congo, where Technip will deploy some of its pipelaying and construction vessel fleet to install the entire subsea production system for operator Total. In terms of the scope of work, the project will be the largest subsea development that Technip has ever been awarded. The company will put into use many of its key assets to make and install the components of the subsea field that include 142 miles (230 km) of rigid pipeline, 14 miles (23 km) of flexible flowlines, and 31 miles (50 km) of umbilicals to deliver chemicals and power to the more than 50 subsea structures to be installed.
Deepwater Facilities Under Construction
Already the uncontested leader in spar development, having delivered 14 of the world’s 17 in operation, Technip is building three new spars simultaneously, including the world’s largest. Spars are deepwater floating facilities that rely on a cylindrical single-column design to achieve optimal stability for drilling and production in an offshore environment.
The Technip-engineered Aasta Hansteen spar will be the biggest platform of its kind built, a distinction driven by the harsh environment of the North Sea and the fact that it is engineered for gas processing and storage. The hull will be 640 ft (195 m) from top to bottom and 167 ft (51 m) in diameter. The spar’s topside facilities will have a processing capacity of 812 MMcf/D of natural gas and a storage capacity of 160,000 bbl of gas condensate. The first spar to be installed offshore Norway, the Aasta Hansteen spar will operate at a water depth of 4,250 ft (1300 m) and is under construction in South Korea, with first production planned for the end of 2016.
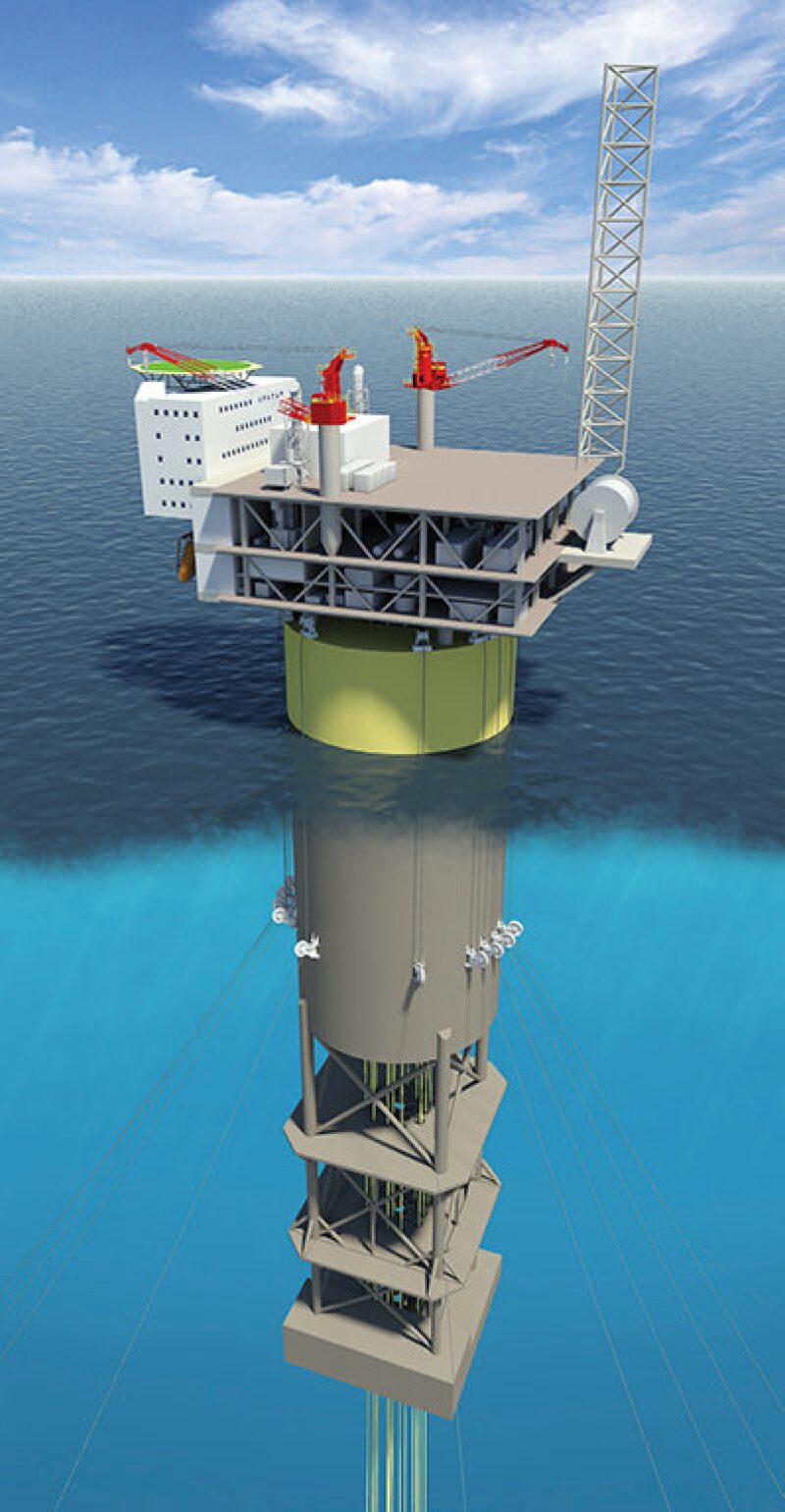
Anadarko selected Technip to engineer, fabricate, and deliver its two largest spar hulls to the US Gulf of Mexico (GOM) as part of a “design one, build two” strategy. While they will operate at different water depths, the two spars share a virtually identical hull that weighs in at 23,000 tons and is 605 ft (184 m) in length, with a diameter of 110 ft (33 m). The construction of the Lucius hull was completed in Finland and the spar is now undergoing final outfitting quayside in Texas prior to its installation and topside integration 274 miles offshore. Operating at a water depth of 7,100 ft (2200 m), the spar will produce a maximum of 80,000 BOPD and 450 MMcf/D of natural gas. The Lucius spar is on schedule for first production of oil in the second half of next year, which would set a company record for Anadarko by bringing a facility online less than 5 years after discovery.
The Heidelberg spar, the sister facility, is under construction in Finland and will operate at a water depth of 5,310 ft (1620 m), and produce 80,000 BOPD, and 2.3 MMcf/D of natural gas. By constructing twin spars one right after the other, Anadarko is attempting to accelerate the commencement of first oil from the Heidelberg spar within 18 months and plans to bring the facility online by 2016.
When Lucius and Heidelberg enter service, Texas-based Anadarko will operate a total of eight spars, the most by any company. They are all operating in the GOM and all were designed and built by Technip. This year, Technip was selected to design and build its first tension leg platform (TLP) in Malaysia for Shell. Known as the Malikai TLP, it will produce 60,000 BOPD and 50 MMcf/D of natural gas in approximately 1,600 ft (490 m) of water, 70 miles (110 km) offshore eastern Malaysia.
High Demand for Deepwater Pipe
The elevated demand for steel catenary risers is one indicator of how rapidly the deepwater sector is growing. These deepwater risers are made from the same materials used to make a pipeline, the main differentiator being that steel catenary risers are engineered to be installed vertically, connecting the production line on the seabed to the bottom of a floating production facility, such as a spar or TLP. By the end of next year, Technip will have manufactured and installed just over 100 of the risers since 2001; however, the company is preparing to ramp up production as it works through its backlog of deepwater projects. “What we are seeing here is very sudden,” Raymond Semple, chief operating officer of subsea operations in North America at Technip, said. “In the span of 18 months, Technip will execute, in terms of steel catenary riser scopes, 50% of what it has done in the last 12 years.”
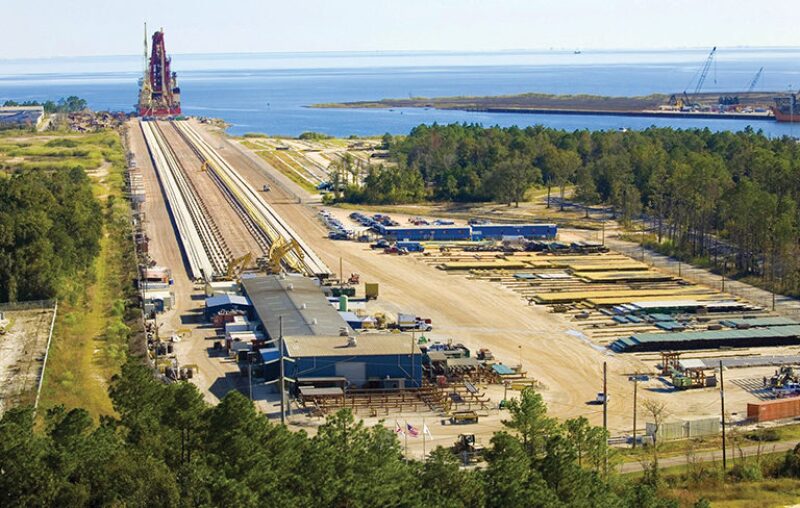
Offshore operating companies looking to increase their reserves and offset production declines no longer can afford a decade to plan and develop new deepwater discoveries. As a result, the subsea technology required for these fields must be proved and qualified in a shorter time frame than was previously acceptable for offshore megaprojects. To handle higher pressures and the extreme conditions of deepwater wells, steel catenary risers and flowlines are being designed with thicker walls and thicker coatings to increase strength and insulation for flow assurance. In response, Technip has had to improve its welding and defect detection technology to respond to the thickness of the latest deepwater pipe. “What for us was a little bit of futurology 3 or 4 years ago is today a reality,” Semple said. “What we are starting to see, almost on a recurring basis for most of these deepwater developments, is a steady increase in the technology being used.”
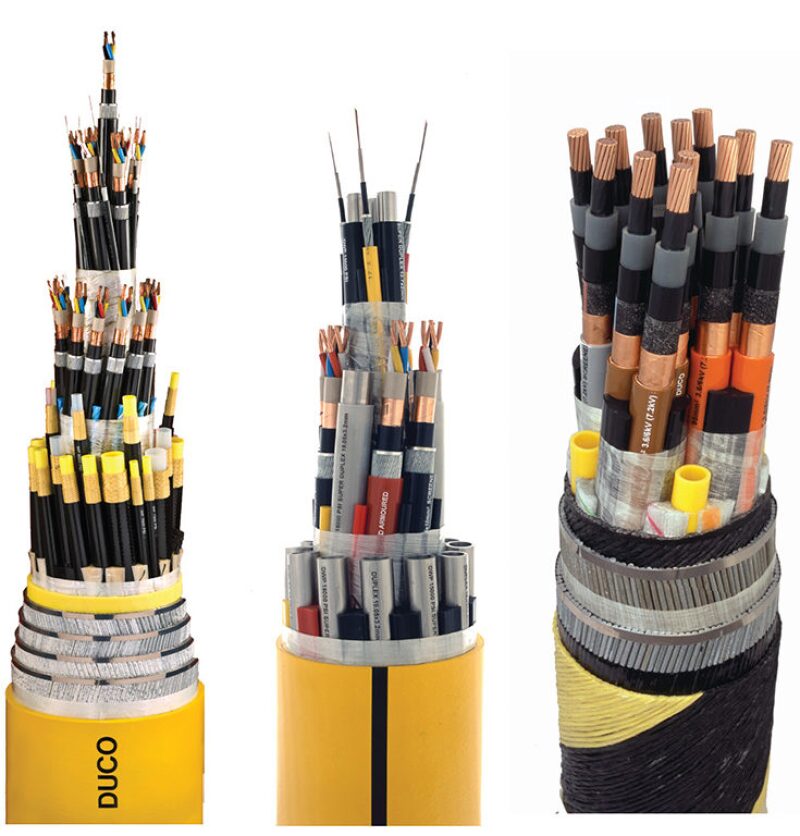
Today, 70% of the umbilicals that Technip makes are designed for the deepwater market, a fact that reflects the shift the offshore industry has made to the new frontier. Umbilicals are designed to specification and provide a link from the surface facility to the seabed in order to deliver chemicals and electricity, and provide operators with control over the systems sitting thousands of feet below the platform. Technip has four umbilical manufacturing facilities that produce all three types of umbilical systems: thermoplastic, steel tube, and power cable.
Invented more than 30 years ago, thermoplastic umbilicals are used for shallow-water development. They consist of plastic tubes wrapped around a centralized wire cable for strength, and are enclosed inside a larger fiber-reinforced plastic tube. Second in the evolutionary chain is the steel tube umbilical, which replaces plastic tubes with high-grade steel tubes to handle higher pressures in deeper waters. Technip is researching hybrid umbilical technology that combines thermoplastic material with steel tube technology to achieve a “best-of-both-worlds” product.
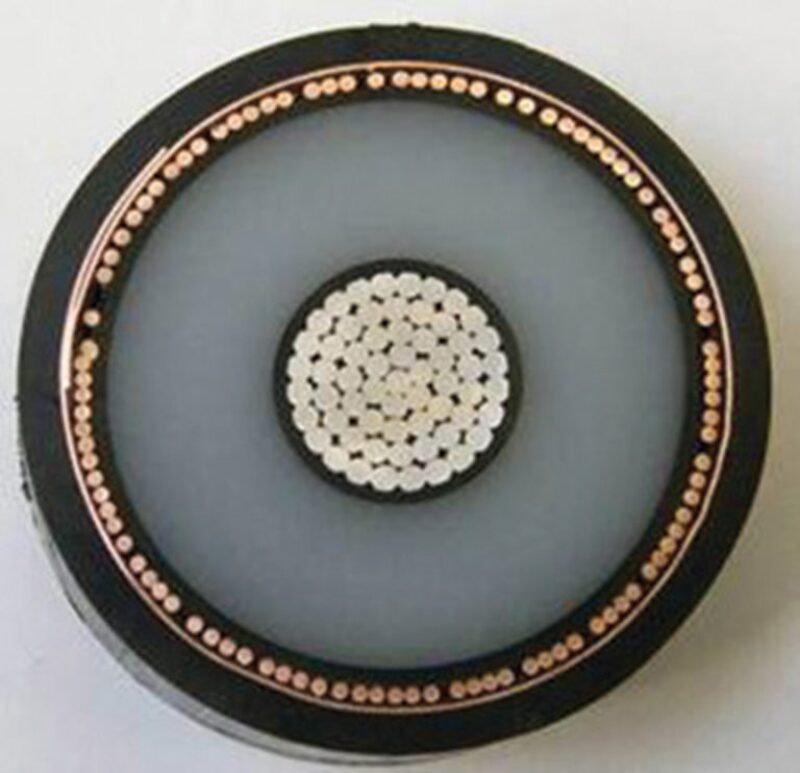
Power cables, the youngest generation of proven umbilicals, have been developed to provide low to medium levels of voltage to power subsea equipment. One of the latest advancements in subsea power cable technology is being qualified by Technip in preparation for the next step change in the offshore industry—the installation of whole production trains on the seafloor instead of on a surface platform. Aluminum power cables are under development by Technip to support the intense megawatt needs of emerging technologies, such as subsea pumps, processors, and separators. Technip is studying the strength, fatigue life, and corrosion characteristics of high-quality aluminum for these subsea applications. Aluminum is significantly lighter than copper and more resistant to corrosion, yet it is comparable in terms of electrical conductivity and thus could provide the designers of floating production facilities with more flexibility in regards to weight restrictions.
US Gulf of Mexico Booming
In 2010, the year of the Macondo well blowout, capital expenditures on deepwater projects in the GOM topped out at about USD 5 billion, according to data from Infield. This year, drilling activity reached record levels, and combined spending by oil companies in the area was about USD 11 billion. Next year, annual spending on deepwater projects in the GOM is expected to surpass USD 12 billion and stabilize around that level for the next few years when companies plan to begin producing oil and gas from at least 20 new major developments in water depths beyond 3,000 ft (1000 m).
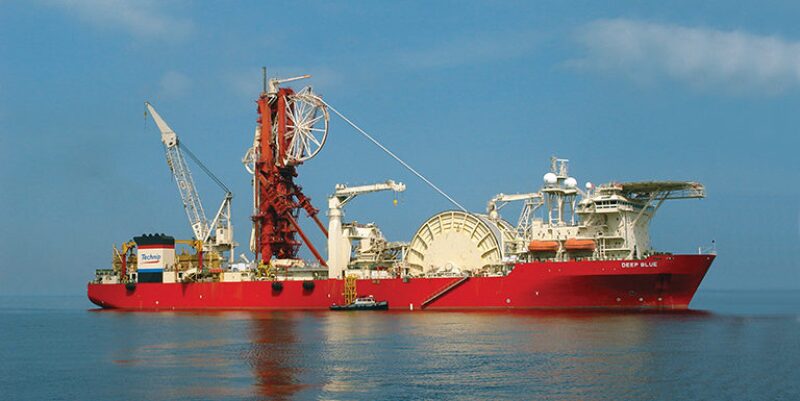
While onshore shale resources garner most of the headlines regarding US upstream activity, GOM drilling is at an all-time “industry high,” according to Technip executives. As of November, 57 rigs were operating in the GOM and subsea wells were producing at a rate of 1.49 million BOPD and 1.92 Tcf of natural gas, representing 14% and 9% of total US production, respectively. And over the next several years, oil companies operating in the GOM will begin work on the deepest developments ever planned. Technip’s vessels, engineers, and subsea systems will be involved in most of them at some stage.
In August, Technip was awarded a contract by Shell to engineer and carry out the world’s deepest pipeline installation at the Stones field in the GOM. At a depth of 9,576 ft (2919 m), the field will be host to the world’s deepest floating production, storage, and offloading (FPSO) unit, which will become only the second FPSO to operate in the GOM. Next year, Technip will begin installation operations of the subsea production system and pipelines and fabricate the lazy-wave production risers for the deepwater development. An alternative to steel catenary risers, lazy-wave risers deliver oil and gas to a floating facility by distributing buoyancy with large buoys along the length of the pipeline to create a relaxed-wave shape in order to reduce motion fatigue on the pipe’s ends.
Positioned for Mexican Reform
The deepwater business in the GOM is limited to the fields located in US territorial waters, leaving the Mexican deepwater fields almost totally unexplored. However, that may change as Mexico is perhaps closer than ever to reforming its energy laws to allow for direct foreign investment in the country’s upstream operations. Amid the uncertainty of the ratification of new energy policies, Technip sees an opportunity to forge a stronger commercial partnership with Petróleos Mexicanos, commonly known as Pemex. Technip is already involved in downstream activities in Mexico; however, the real prize is the country’s untapped deepwater reserves. “The compelling market for us as we look forward is Mexico,” said Deanna Goodwin, chief operating officer of offshore North America at Technip.
If Pemex is to take a significant step into the deepwater fields of the GOM, Technip believes the expertise gained from decades of projects immediately to the north will be indispensable. “We’re going through a learning process together, in terms of sharing information, objectives, and capabilities,” Goodwin said of Technip’s relationship with Pemex.
The company opened offices in Mexico City 18 months ago, and from its 2011 acquisition of Global Industries, Technip inherited an office in Ciudad del Carmen, located on the Bay of Campeche and considered the hub city for Mexico’s offshore industry. Mexico’s declining hydrocarbon production is no secret and, according to Technip, Pemex has suffered a reduction of 1 million BOPD over the past 10 years. “And yet their spending has doubled,” Goodwin said. In July, Mexico produced 2.48 million BOPD, the lowest monthly amount in nearly 18 years, despite spending nearly USD 20 billion annually in support of exploration and production operations.