A novel nonaqueous-fluid (NAF) system was designed to provide stable rheological properties with a nonprogressive gel structure and very good filtration control and filter-cake quality in wells where the expected bottomhole static temperature (BHST) exceeds 400°F. The fluid was successful in providing wellbore conditions capable of being fully logged and evaluated and, at the same time, providing effective hole cleaning with minimum effect on equivalent circulating density. The fluid has been successful in wells with temperatures from 400 to 428°F and mud weights from 11.7 to 14.5 lbm/gal.
Introduction
Historically, conventional NAF systems have had a good performance record in the Gulf of Thailand, providing the necessary fluid and wellbore stability to achieve successful wireline-logging operations. However, when BHST exceeds 400°F, problems have been reported during wireline-logging operation, including difficulties in moving wireline-logging tools to reach the target depth or even getting stuck, which led to nonproductive time (NPT) or loss of tools in several wells. As a result, a more robust NAF that could help minimize the NPT was requested by the operator because numerous wells being planned would have BHSTs considerably above 400°F. The first approach to solve this issue was to review and modify field engineering practices in an attempt to extend the stability of the conventional NAF formulation; however, it was concluded from this initial study that a novel NAF was required for this ultrahigh-temperature condition.
On the basis of extensive laboratory testing during fluid-system development, it was determined that the combination of a new nitrogen-free emulsifier designed for thermal stability in excess of 550°F and a filtration-control package comprising a synthetic polymer coupled with a modified naturally occurring polymer provided the most stable fluid up to 525°F.
Main Components
Emulsifier. A new emulsifier was developed to withstand ultrahigh temperatures and provide low-viscosity, stable emulsions (i.e., low and flat gel structure). The emulsifier also contributes to high-temperature/high-pressure (HT/HP) filtration control and temperature stability of the system. This emulsifier has another benefit over the conventional amine-based emulsifiers because it does not thermally degrade and release ammonia when exposed to ultrahigh temperatures, even if the temperature limit of the product is exceeded.
Modified-Natural-Polymer Filtration-Control Agent. This filtration-control agent is stable to temperatures in excess of 500°F, with minimal effect on the rheological properties of the NAF.
Synthetic-Polymer Filtration-Control Agent. This filtration-control agent provides HT/HP filtration control in extreme high-temperature environments up to 500°F.
Laboratory Study
Extensive laboratory tests were performed before approval was granted by the operator for a field trial. The tests were performed not only to confirm the performance of the new NAF but also to optimize product concentrations for an expected BHST of 425°F and to quantify the product’s benefit over the conventional NAF system for openhole wireline-logging operation.
Key properties used in evaluating the system’s performance were the HT/HP filtration loss, filter-cake quality, and shear strength after static aging at expected BHST. The HT/HP filtration testing was performed at 425°F and 500 psi. The HT/HP test was performed at 425°F to eliminate any product that might survive the normal HT/HP filtration test at 350°F but would deteriorate rapidly should the field trial reach the expected BHST beyond 400°F. The static shear strength was used to determine the condition of the NAF after being exposed to ultrahigh temperatures to simulate field static condition during prolonged wireline-logging operations, which normally take approximately 48 hours. This shear-strength value correlated well with the pressure used to break circulation after static condition—after running tubing to required depth and breaking circulation before performing a cement job. If the pressure is excessive, it could fracture the formation and lead to total lost circulation.
A series of tests was planned, starting with the conventional NAF (Formulation A) to provide baseline performance criteria with which to compare the newly developed NAF (Formulation B). The muds were formulated using a 9.2-lbm/gal cut-back field seed mud that was weighted to 11.0 lbm/gal with barite. Both muds were sheared at 135°F at 7,000 rev/min before determination of initial properties. Each formulation was then split into two samples for rolling and static aging for the indicated hours. From this study, the novel NAF outperformed the conventional system in terms of HT/HP filtration control, filter-cake quality, and shear strength. Moreover, it was found that the novel NAF could be converted easily from the conventional NAF without any dilution required.
Formulation B was set up to determine the properties of the field mud after adding the new product without any dilution. The mud weight was then increased to 11.0 lbm/gal.
Further tests were conducted to optimize concentrations of the newly developed product for economic reasons. Two 11.0-lbm/gal field-drilling-fluid samples containing 6% low-gravity solids (LGS) (Formulations C and D) and 3% LGS (Formulations E and F) were used as seed mud for these laboratory tests. The final fluids were within specifications and were very stable after hot rolling at 375°F (expected circulation temperature) and after static aging at 425°F (expected BHST). The HT/HP fluid-loss and shear-strength values were extremely low and almost identical for all four formulations.
Exceptional filter-cake quality, both after hot rolling and after static aging (Fig. 1), was achieved from the proposed treatment. This confirmed the drilling-fluid performance under expected hole conditions in the field trial.
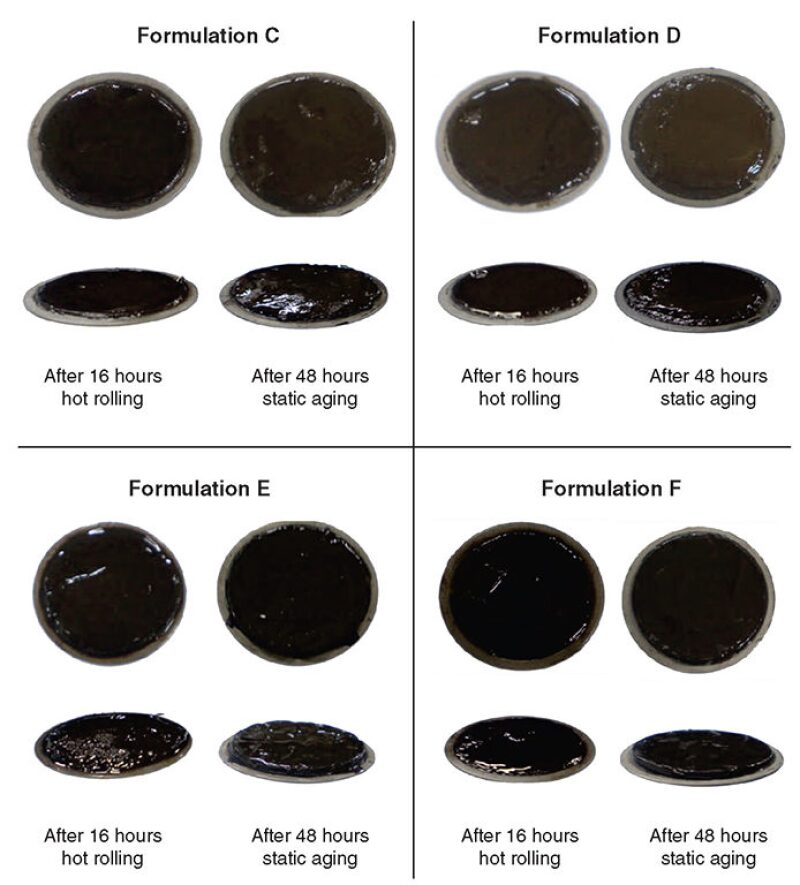
On the basis of test results, the recommendation was to add 5 to 10 lbm/bbl of the new emulsifier and required HT/HP fluid-loss-control agents to the conventional NAF without any dilution. This could be performed gradually once the circulating temperature approached 350°F before tripping out to remove the measurement-while-drilling (MWD) tools. The LGS should be maintained as low as possible because they are a major cause of fluid gelation under ultrahigh-temperature conditions.
Field Trials
Two wells (Development Well A and Exploration Well B), each in southern fields of the Gulf of Thailand, were selected for the first field trials of the novel NAF system. The system was to be used in the 6⅛-in. sections (open hole).
- During the planning stage, the following were identified as potential problems in these wells:
- Extremely high BHST—up to 425°F in Well A and up to 415°F in Well B
- High CO2 level—up to 40% in Well A and up to 30% in Well B
- Trouble running wireline logs because of extensive viscosities and gelled drilling fluid
- Extended exposure of drilling fluids to formation because of long openhole sections and multiple bit trips
The operator and business partner had agreed to the following criteria as the key performance indicators (KPIs) for these high-temperature wells:
Well A. The 6⅛-in. section in Well A was drilled from 5,766 to 13,990 ft, which was the planned total depth (TD). The novel NAF was recommended as the fluid for the high-temperature and CO2-rich drilling environment in the deeper portion of the 6⅛-in. section. The conventional system was gradually converted to the new system below 9,831-ft measured depth (MD)/8,103-ft true vertical depth (TVD), and the planned product concentration was met at approximately 12,829-ft MD.
Well B. The conventional NAF system was converted to the novel system at 9,300-ft MD/8,401-ft TVD to achieve a fully treated system before the MWD temperature-limitation trip at 9,400-ft TVD. Before treating the active system, a series of pilot tests was conducted to evaluate the effect of the planned treatment.
A reduction in rheological properties was observed after the conversion, except for the plastic viscosity. The decision was made to treat the system with the high-temperature chemicals during three to four circulations, along with organophilic clay. This was done to keep the fluid within specification and to avoid any sudden changes in drilling-fluid behavior. The entire circulating system was converted successfully before pulling out of hole at 9,840-ft TVD. Before each trip and logging phase, the active system was treated with 5 to 6 lbm/bbl of lime to counteract any CO2 influx.
A decrease in yield point and a 6-rev/min dial reading were noticed after the addition of the high-temperature chemicals at 9,300-ft MD. Therefore, a drilling-fluid treatment with the addition of a viscosifier for the logging phase was performed.
Even when the drilling fluid contained up to 20% of corrected solids and 4.5% of LGS, the gel structure of the system was nonprogressive and values of the 10-second, 10-minute, and 30-minute gels were lower than those of the conventional system.
Improvement in HT/HP fluid loss and stable electrical-stability values were observed after the treatment with high-temperature chemicals.
Field-Trial Summary
The 6⅛-in. intervals were drilled successfully in both wells without any drilling-fluid-related issues, and all of the KPIs were met. The BHST was estimated at 410°F by wireline logging inside 2⅞-in. tubing in Well A. During openhole logging in Well B, the BHST was recorded at 390°F. Good hole conditions were recorded during multiple trips, with minimal tight spots. Optimum hole cleaning was maintained, with good drilling practices. A 6-rev/min reading between 7 and 9 lbm/100 ft2 indicated good to very-good hole cleaning achieved, in accordance with the advance hydraulics simulations.
The novel NAF confirmed expectations and delivered excellent rheological properties, filtration control, and filter-cake quality while drilling the 6⅛‑in. intervals. While logging, the system maintained its properties and provided a superior logging environment.
Recommendations
To ensure optimum rheological properties, the rheology checks should be performed at three different temperatures to determine the stability across the temperature range.
On critical ultra-HT/HP wells, equipment to monitor particle-size distribution in the field should be used. Tracking the degradation of drilled--solids particle size will help to determine when ultrafine solids become excessive and dilution or other action is required to maintain the optimum performance of the NAF.
Field samples from different conditions—before fluid conversion, at TD, and after static conditioning—should be collected and sent to the local laboratory for quality control. Rheological properties at different temperatures and pressures can also be determined with an HT/HP viscometer.
The NAF should be conditioned thoroughly before encountering the anticipated downhole conditions by circulating through the bit and monitoring properties at the surface, keeping in mind that rheological properties will change because of the extreme high temperature during extensive wireline logging.
This article, written by Special Publications Editor Adam Wilson, contains highlights of paper SPE 158680, “Pushing the Envelope of HT Drilling Fluids: Development and Field Applications of a Novel Nonaqueous Drilling Fluid in the Gulf of Thailand,” by Kerati Charnvit, SPE, Abhijart Kongto, Fransiskus Huadi, and Sunil Sharma, SPE, M-I Swaco, and Gerard Simon, SPE, Brent Estes, SPE, and Neil Trotter, SPE, Chevron, prepared for the 2012 SPE Asia Pacific Oil and Gas Conference and Exhibition, Perth, Australia, 22–24 October. The paper has not been peer reviewed.