Nine horizontal wells, including one injector well, were drilled in a marginal oil field in Bohai Bay, China. Seismic inversion indicates that sand properties and connectivity vary dramatically across the field. A multiple-aquifer system was apparent, and the gas/oil-contact (GOC) and oil/water-contact (OWC) levels were unknown. Furthermore, the only well control was from three vertical exploration wells and two directional offset wells. An advanced distance-to-boundary well-placement technique using azimuthal deep-directional electromagnetic logging-while-drilling (LWD) technology was applied to overcome these challenges and to enhance reservoir understanding.
Introduction
The BZ oil field is located in the southern part of Bohai Bay, approximately 160 km southeast of Tanggu, Tianjin (Fig. 1 above). It is a small oil-bearing area (9 km2) isolated by secondary faults generated at different geological periods and by stratigraphic depositional borders.
Two other producing oil fields are located in the northern and western parts of the BZ area. Although the original oil in place (OOIP) of the oil field is estimated at only 1261.89×104 m3, this marginal oil field is expected to be profitable to develop and put into production by sharing the facilities of the other two oil fields.
The BZ structure is part of the complex fault system on the northwest side of the Huanghekou depression on the west side of the Bonan uplift. Because of the oil field’s isolation, a multiple-aquifer system exists. A pilot study based on core and sequence-stratigraphy analysis of multiple wells shows that the reservoirs are distributary channel sands of a shallow lake delta plain. The channel sands have medium-to-high porosity and permeability. The seismic-data analysis suggests that the properties may vary laterally. Meanwhile, uncertainty in the top gas and bottom water levels adds to the complexity of this field. The GOC and OWC levels were unknown before this horizontal-well-drilling program.
Horizontal-Well-Drilling Program
Two platforms were designed to develop this complex oil field: BZ-A platform, to drill 11 wells, and BZ-B platform, to drill five wells. Among these 16 wells, 10 horizontal wells were designed as producer wells, five deviated wells were designed as injector wells for formation-pressure maintenance, and one deviated well was designed to supply water for the injector wells.
The planned cumulative oil production for a 30-year period is 257.3×104 m3, with an expected recovery factor of 24.3%. The planned cumulative gas production after 20 years is 17.7×108 m3, with an expected recovery factor of 60.9%.
Challenges. During the planning stage of the horizontal-well-drilling-program execution, the team identified multiple major subsurface challenges, including the following. For a full list of these challenges, please see the complete paper.
- There is lack of offset well control in the area and increased structural uncertainty.
- The field lies within a highly faulted area, which increased the risk of exit from reservoir and the risk of needing to make adjustments to re-enter the reservoir.
- A multiple-aquifer system may exist, and the OWC was unknown. This increased the risk of approaching the OWC and of early water breakthrough if the lateral section of the horizontal well was not placed properly, close to the reservoir top.
- The uncertainty in the top of gas and GOC might affect the oil production and recovery factor if the lateral section of the horizontal well was not placed properly below the GOC.
Solution. To overcome these challenges and to enhance reservoir understanding, the advanced distance-to-boundary well-placement technique using azimuthal deep-directional electromagnetic LWD technology was applied (Fig. 2).
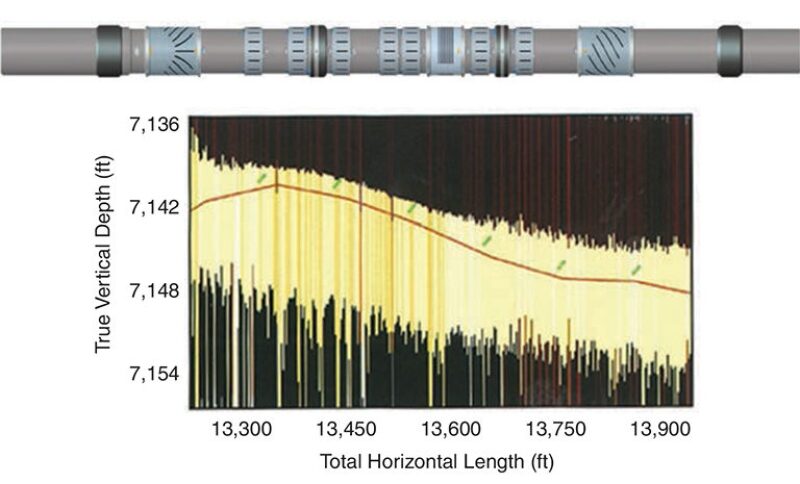
A multifunction LWD formation-evaluation tool was deployed to evaluate reservoir quality and fluid properties where the top of the gas may occur. A real-time density image also was applied to determine the formation dip while drilling. In addition, a rotary-steerable drilling system was assembled to achieve drilling efficiency, smooth trajectory control, and full control of the well path within the drilling or steering window.
Case 1: Sand-Boundary Identification. The plan for Well HW5 was to place the horizontal section for 350 m within the middle part of the reservoir. The well was planned near the main fault, and the seismic-impedance profile showed that there was a possibility of discontinuity between the channel sands. A requirement was to avoid entry into the gas cap or bottomwater.
During the landing, the well was placed approximately 5 m below the reservoir top after entering the sweet spot. During the horizontal-section drilling, the target top was mapped by the azimuthal deep-directional electromagnetic tool and subsequently the well trajectory was placed toward the middle of the reservoir. After drilling more than 150 m, the bottom of the sand reservoir was clearly detected and delineated 4.6 m above the boundary. The trajectory was then adjusted accordingly to level off approximately 4 m away from the bottom. Toward the end of the well, the trajectory was intentionally steered toward the upper zone to detect the target top. The target top was eventually detected and mapped toward the total depth (TD) of the well. Without the ability to detect and map the boundaries, the horizontal section might not have been placed along the middle of the reservoir and the trajectory might have exited from the bottom of the reservoir.
Finally, the 346-m horizontal section was drilled with 100% net-to-gross in approximately 7.5 hours, much faster than the 54 hours of the plan.
Case 2: Placing Trajectory Accurately Below the Gas Cap. The unknown GOC level was one of the major challenges in placing the horizontal section for Well HW10. The well was planned near the fault in the crest area of the reservoir controlled by the channel depositional system. The gas cap exists in the crest area, but the GOC level was unknown. The objective of the well was to place the horizontal section within the oil zone approximately 2 m below the GOC. Entry to the gas cap during the horizontal section was prohibited.
The option to drill a pilot well to confirm the GOC level was part of the original plan. However, the team was aware that the real-time gas identification while drilling provided by the LWD tool could be a better alternative than the pilot well and could potentially result in considerable savings in authorization-for-expenditure costs.
It was decided to rely on LWD data and eliminate the pilot well. The team recognized that the precise GOC-level identification during the landing section would be critical to placement of the horizontal section below the gas cap, to avoid entering this prohibited zone. To overcome this challenge, the multifunction LWD formation-evaluation tool was deployed during the landing section. Eventually, the GOC was identified at the level of 1536-m true vertical depth subsea (5 m deeper than the original prognosis), and the well then was landed 2 m below the contact. Then, the horizontal section was continued by keeping the trajectory at the same level all the way to the TD of the well.
The ability of the advanced multifunction LWD tool to perform real-time formation evaluation while drilling allowed the team to identify the GOC accurately, place the well below the gas cap properly, and save the cost of drilling a pilot well.
Case 3: Placement Along the Braided-Channel-Sand Body. Well HW2 demonstrated the complexity of the channel-sand depositional system in the Bohai Bay area. The trend of the channel-sand body is in the southeast/northwest direction and then it turns to the opposite (southwest/northeast) direction. The objective of HW2 was to land the well near the edge of the right wing of the channel sand and place the 800-m lateral section along the northeast/southwest direction. From the seismic-inversion model, the trajectory may approach the edge of the channel’s left wing toward the end.
During the landing section, the well was landed smoothly below the reservoir target top despite the reservoir being shallower by 3 m than originally anticipated.
In the lateral section, the azimuthal LWD bed-boundary-mapper tool clearly delineated the channel-sand-body boundaries along the horizontal section. It was observed that the reservoir body consists of a series of braided channel sands surrounded by shaly sand. The trajectory was finally completed to TD and was optimally placed within the clean channel sands while also setting a new record for lateral-section length in the field. The team recognized that without the detailed information of the boundaries and the reservoir profiles, the trajectory would not have been placed within the clean channel sands and might even have been placed out of the target reservoir body.
Case 4: Well-Type Adjustment While Drilling Based on Real-Time Information. Well Inj2 was designed as an injector well for reservoir-pressure maintenance (Fig. 3). The plan was to drill a directional well from the top to the bottom of the reservoir.
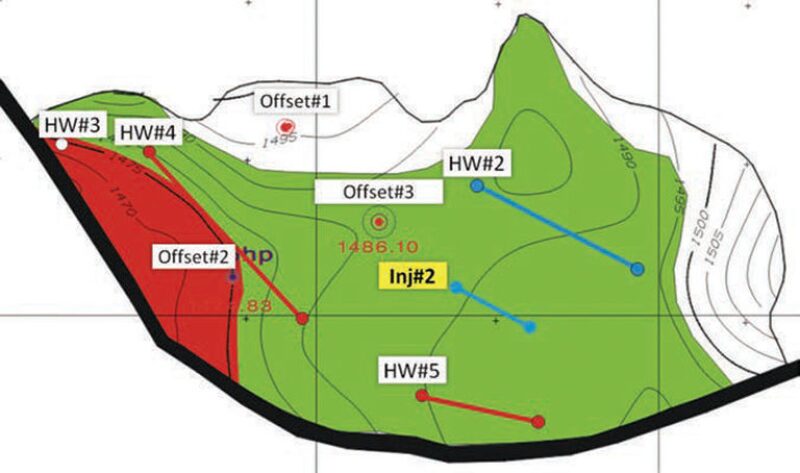
The multifunction LWD formation-evaluation tool was used to evaluate the reservoir while drilling. Eventually, during the drilling operation, the team decided to change the directional well into a horizontal well on the basis of real-time formation-evaluation data. The team determined that the quality of some intervals in the reservoir zone is not as good as was expected, which may affect the efficiency of the injector well. Therefore, the decision was made to extend the reservoir exposure by drilling a horizontal well rather than a directional well. After 500 m of lateral section was achieved, the trajectory was intentionally drilled down the structure to tag the bottom, thereby covering the entire reservoir section.
Successfully shifting the directional injector well into a horizontal injector well has ensured the effectiveness of the injector well within the area. The team also evaluated the adequacy of this injector horizontal well to provide pressure maintenance within this particular oil-trap compartment. Cost savings were achieved by eliminating the need to drill another injector well in the future.
Results
A total of 4303 m of horizontal section was drilled and placed within the target reservoir with 100% net-to-gross.
The injector well was begun as a directional well and then was shifted to a horizontal well. One of the producer horizontal wells was retracted upon discovery that the target sand was not developed within the targeted area, and another producer horizontal well was canceled because of engineering considerations.
Despite the reduction in the number of producer wells from the original plan of 10 wells to eight wells, the total production from the eight producer wells is even higher than the set goals for the total production of the 10 wells. The total production rate of the eight producer wells exceeded the expected total production rate of the 10 wells by 3.3%. This represents 30% additional production per well compared with the original set goals.
Furthermore, the capability to increase the drilling penetration rate and avoid adjustments or sidetracks because of reservoir exits led to a 60% improvement in drilling efficiency, equivalent to a savings of USD 32 million.
This article, written by JPT Technology Editor Chris Carpenter, contains highlights of paper IPTC 16669, “Development Optimization of a Marginal Oil Field in Bohai Bay, China—Integrated Solutions To Overcome Challenges in Offshore Horizontal-Well Construction,” by Chaomin Nie, Yongsheng Zhao, Lv Tan, Yong Jia, and Gang Zhai, China National Offshore Oil Corporation Tianjin, and Parlindungan Monris Halomoan, Xu Chong Hui, Wang Yong, Wang Fei, and Dong Jianyi, Schlumberger, prepared for the 2013 International Petroleum Technology Conference, Beijing, 26–28 March. The paper has not been peer reviewed. Copyright 2014 International Petroleum Technology Conference. Reproduced by permission.