Digital is replacing manual at Sanchez Oil & Gas. Since its implementation in 2017, the company’s Production Maintenance Tracker (PMT) application has been transforming its operations management.
PMT is critical to managing daily operations in the field. Created within the Microsoft Office 365 ecosystem and using the capabilities of Microsoft PowerApps, Microsoft Flow, and Microsoft PowerBI, PMT brings together all the assets, departments, and routes into one hub to streamline production operations. The application system automatically stores data, facilitates communication, and tracks the progress of tasks.
PMT, a system of mobile applications, was built as a communication system for field-based employees and contractors to facilitate communication between multiple teams involved in operations. It replaces the previous manual system of communicating daily work orders over long email chains, which were generated every morning in the remote operating center and sent to individuals across several teams, including the lease-operator, automation, subsurface, artificial-lift, chemical, and construction teams. Tracking operational activity was difficult, and significant time was lost searching for the right information at the right time.
PMT not only facilitates communication but also stores all the information in an enterprise database. It allows for timely access to the right data and analytics through dashboards and reports, leading to informed everyday decision-making. This kind of visibility into field operations was not possible previously.
Previous manual work flow.
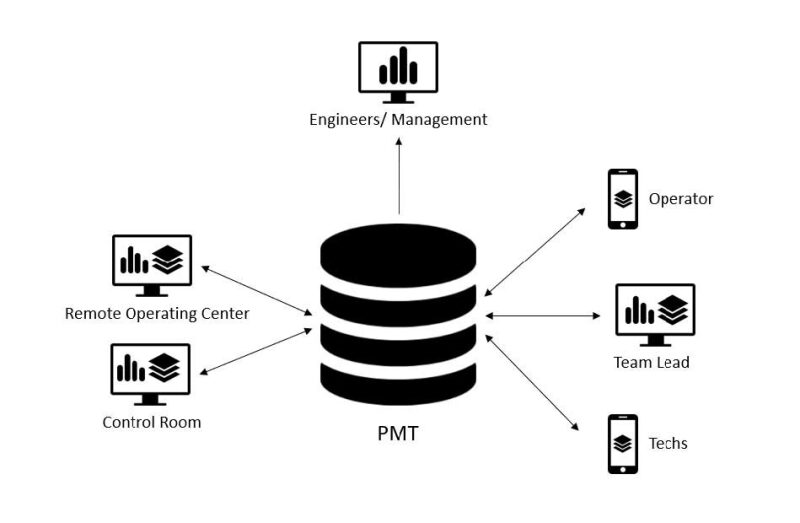
“Because PMT measures our production operation efforts, we can more effectively manage issues and predict outcomes,” Mike Blincow, vice president of production operations at Sanchez, said. “As a result, Sanchez is shifting from reactive to proactive operations.”
The application system was built using the Microsoft Office 365 Power Platform, leveraging the company’s existing information-technology resources to create a solution that is cost-effective and easily deployable. The app comprises four mobile applications built with Microsoft PowerApps and Microsoft Flow and is accessible with computers, tablets, and phones from anywhere over the Internet, making it suitable for use by field personnel. The cloud-based system is not only easily accessible but also seamlessly integrated with enterprise databases within Sanchez, whether through the cloud or on the premises, while remaining securely protected by Microsoft Azure’s powerful security technologies.
Chris Barringer, vice present of information systems at Sanchez, said, “PMT advances our overarching strategy to use mobile, cloud-based software to easily employ modern concepts. It leverages our existing technology capabilities to aid the business in achieving operational targets.”
Determining a Rapid, Scalable Solution
The need for a digital tool was recognized in 2017, when Sanchez acquired a major asset that would quadruple its operations complexity. The goal of production operations at the time was to improve operational efficiency while maintaining a reasonable employee headcount. Sanchez soon realized that a digital replacement for the conventional, manual system of communicating work orders by email was necessary. With a growing understanding of the importance of data analytics and informed decision-making, the operations management team at Sanchez quickly shifted its focus to the insights that can be generated through the captured data.
Leslie Malone, area production manager at Sanchez, said, “Our manual process had naturally progressed to the point of producing daily logs and reports, but we needed a higher level of organization that would help us track the completion of tasks in the new environment—and it was critical to move quickly.”
PMT was developed from scratch using Microsoft PowerApps, a cost-efficient technology within the Microsoft Office 365 Power Platform. The development methodology was completely agile; the entire system was developed in multiple sprints spanning a total of about 4 months. The incremental development allowed the product to be user-centric and fully customizable.
“Leveraging a user-friendly, in-house resource afforded us the ability to develop and deploy quickly—making instant tweaks based on feedback—without compromising security, service, or function,” Barringer said.
The first version of PMT was successfully deployed within 6 weeks from the start of the project. Nearly 100 people from field operations, including control-room well analysts, remote-operating-center production analysts, and lease operators, embraced the application and immediately ramped up operations. Other teams such as automation, subsurface, and chemical were soon to follow, resulting in the use of PMT by about 300 people across seven teams over three oilfield assets. To date, PMT has helped manage more than 80,000 production tasks.

receive the majority of tickets.
Empowering Oilfield Operations
A primary feature of PMT is the enablement of closed-loop communication between the remote operating center in Houston, the control room in the field, the field operators, and other teams involved in the daily operational routine of the assets. Work order tickets now can be generated quicker because of a reduction in repeat tickets, a result of the availability of the history of previously assigned work through data tracking. Within minutes of ticket creation, the operators can see the work assigned to them in their applications, a process that previously required an hours-long wait every morning while the variance list was sent by email from the control room. Operators no longer need to dig through emails to find assignments. Now they can see in their phone applications the work orders relevant only to them, prioritized by production-effect estimates and age of the tickets. The tool not only improves efficiency at the very top, which trickles down through the entire process, but also brings clarity to tasks that usually involve multiple work flows.
Randal McKee, production analyst at Sanchez, said the app transformed a cumbersome, manual process. “The old process involved cycling through hundreds of wells using Excel spreadsheets and email reports,” McKee said. “Not only does PMT save 2 to 3 hours each day, but analysts and management are equipped to make better decisions based on data rather than assumptions.”
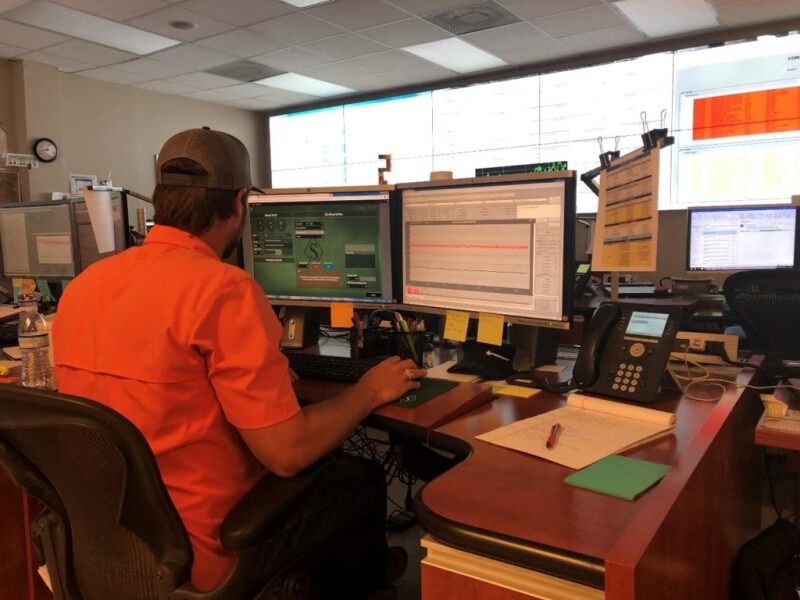
the Comanche control room in Carrizo Springs, Texas.
The ease of the mobile solution allows field operators to communicate critical information quickly. The standardized design—which includes single sign-on and predetermined dropdown menus—is ready for use any time, on any device, and for any skillset. Field operators signal the start of a task simply by pressing a “start work” button.
Fidel Acevedo, lead well analyst at Sanchez, said, “It’s intuitive and self-explanatory. PMT was easy to navigate on Day 1, without training or orientation. We know exactly what to do and where to work, without digging through emails and work orders.”
Justin Bender, manager of enterprise applications at Sanchez, said the app was designed with the end-user in mind. “Whereas traditional software is office-centric, this was intended to be a boots-on-the-ground tool. It’s about empowering the field operators so that they can, in turn, help management make the right decisions faster.”
The heart of PMT is the visibility it provides into daily operations. A dashboard built in Microsoft PowerBI provides the production team—which includes analysts, engineers, a supervisor, a superintendent, and support staff—real-time status updates of open tickets and helps them closely monitor daily operations. To assist with that, they can quickly visualize the locations of field operators on their respective routes spread across multiple oilfield assets. The increased visibility has helped Sanchez implement accountability in the field operations by keeping track of task submissions and completion times. It also helps the operations team identify the key areas where field personnel need further training. Training modules are designed and embedded into the app for completion by analysts and operators with supervisor approval.
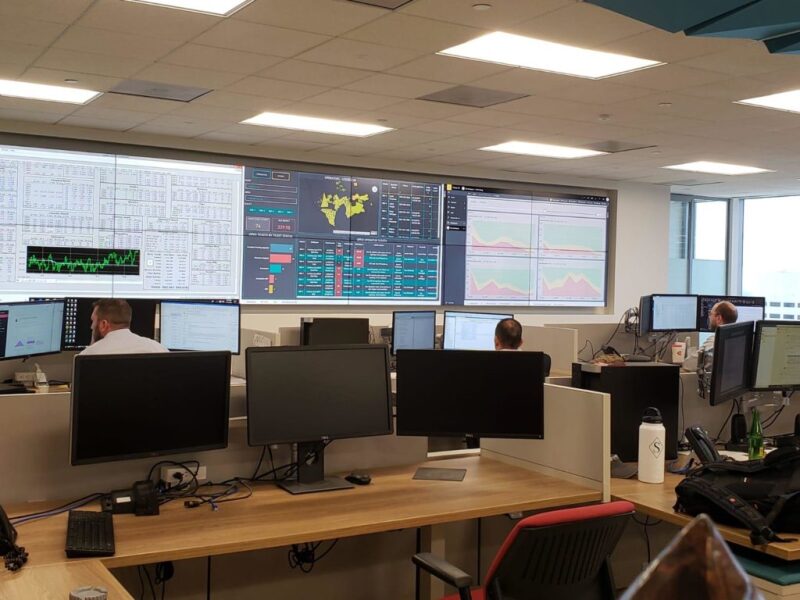
Seve Alaniz, production analyst at Sanchez, said the increased visibility allows for increased accountability. “Because of the speed at which information is now being processed, we’re able to shift our focus from high-level tasks toward meaningful details that were previously missed,” he said. “Within minutes after tasks are completed, we can see how long tasks take to complete, who is completing tasks in the timeliest manner, and what comments are associated with each task.”
The optimized process has reduced the average time for task completion by operators from 2.55 days before 2019 to 2.01 days in 2019, which affects 67% of all work orders. While the average ticket close-out time was reduced by 21%, the average ticket count per day increased by 42.5% in 2019, indicating the ability of operators to manage a heavier workload with increased efficiency. For all other teams, the average ticket count per day increased by 23% while average ticket close-out time decreased by 41% in 2019.
“If we can measure it, we can improve it,” Blincow said. “PMT allows us to see where we are and where we need to be.”
While the PMT assists well analysts and production analysts in managing day-to-day operational affairs, the history of operations activity also assists production engineers and managers in long-term production planning. Many of the tasks associated with daily operations become part of the problem-well report, which identifies longer-term issues and planning needs. The history of well maintenance plays an important role in quarterly well-review sessions, and PMT helps the engineers keep a track of the action items from these well reviews.
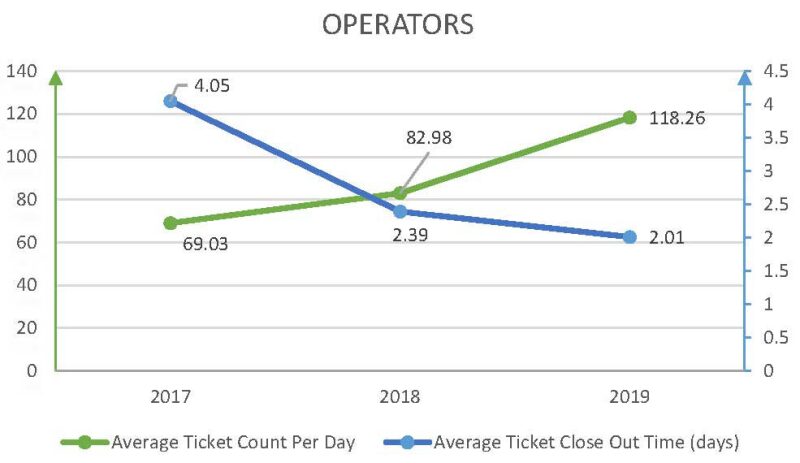
burden in 2019 and a decrease in ticket completion
times for operators.
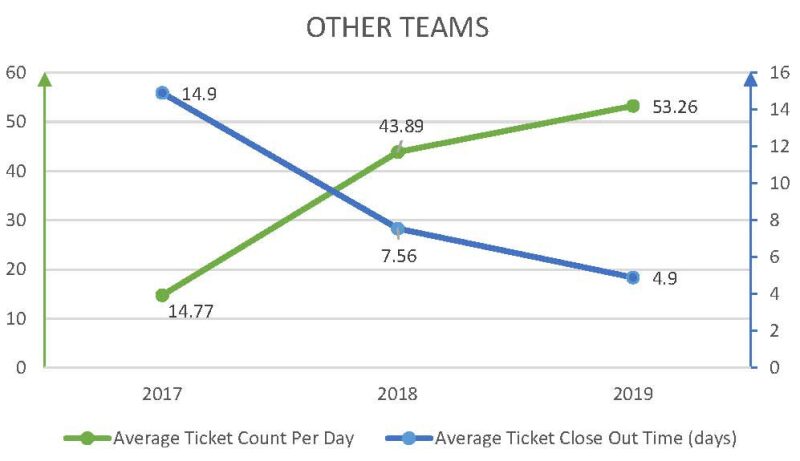
in work burden and decrease in ticket
completion times for teams other than operators.
Ken Dunek, area production manager at Sanchez, said the digital tool is fueling multiple production initiatives at Sanchez. “PMT is definitely an enabler for other products in field operations,” he said. “It makes meaningful connections to other enterprise data sources so that we can realize our full potential as a team.”
Enabling Future Solutions
PMT affects more than the production-maintenance needs at hand. The growing database of operations tickets seamlessly integrates with other enterprise data sources to enable other solutions for production operations at Sanchez.
Khuzema Sunel, operations research analyst at Chirality Research and the developer of PMT, said, “PMT has been purposefully designed to keep track of very important KPIs [key performance indicators] in oilfield operations. It has redefined the way Sanchez operates its assets and will play its part in enabling turnkey solutions with advanced analytics and data science application.”
The historical data identifies areas of improvement in methodology of fixing production issues. Looking back at the data can reveal recurring issues and the steps that were taken to solve those problems, calling for a need for change in the way in which these issues are approached and handled. Moreover, different areas of the field can be compared and better-performing wells can be benchmarked with the increased visibility at hand. By keeping a record of all field personnel and their strengths based on completed jobs, specific jobs can be distributed to specific people rather than the traditional approach of assigning single operators all the tasks in their assigned geographical areas. This eventually leads to fully dynamic routing by considering the severity of the job, the production effect, and the distance of the operator from the well, enabling the right person to be at the right place at the right time.
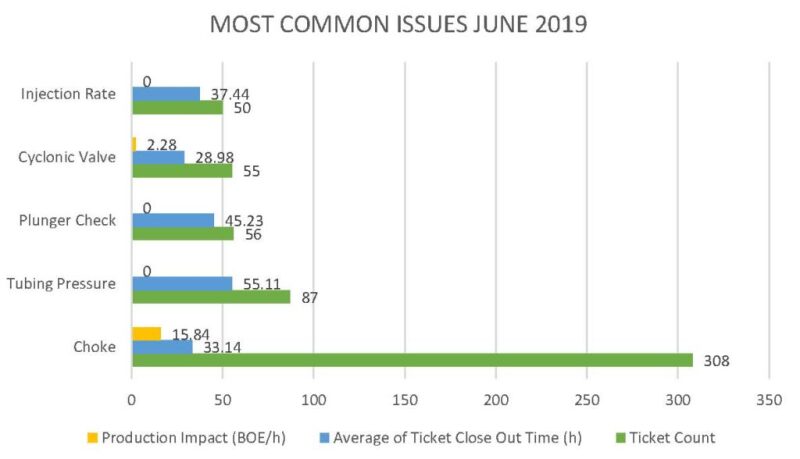
attention in June 2019, along with their average ticket
completion times and average production effect.
Pankaj Sharma, manager of data engineering at Sanchez, said, “Apps like PMT play a big role as we move toward a big-data approach, a culmination of cloud computing and predictive analytics that provide valuable insights from previously unexplored enterprise data. It’s an exciting new phase of data technology in which we can make the best use of data to make decisions very quickly.”
Another aspect is the improved ability to track lease-operating costs (LOE). Production tasks can be assigned associated costs, which helps define the baseline value and priority of tasks. The cost of the task comprises two main components. The first component is the physical cost that was spent to perform the task, which can include operators’ hourly wages and cost of parts replaced. The second component is the loss of production incurred, if any, because of the problem, which includes the well’s hourly production and the time taken to remedy the problem. The resulting data helps provide insight into the true cost of operational upsets, including minor but impactful details that are generally missed. Also, the app’s integration with production data can be used to prioritize work on the basis of deferred production as well as identify possible safety issues.
Ultimately, PMT has inspired the development of several other applications at Sanchez that aim to automate work flows and gather data that is usually lost or difficult to track with manual processes in place. It has helped spark and strengthen the concept of self-service business intelligence across the organization.
Malone said, “PMT opened our eyes to the power of this modern way of developing business intelligence, particularly that which can be cultivated in-house by our own teams. It got the ball rolling in our minds.”
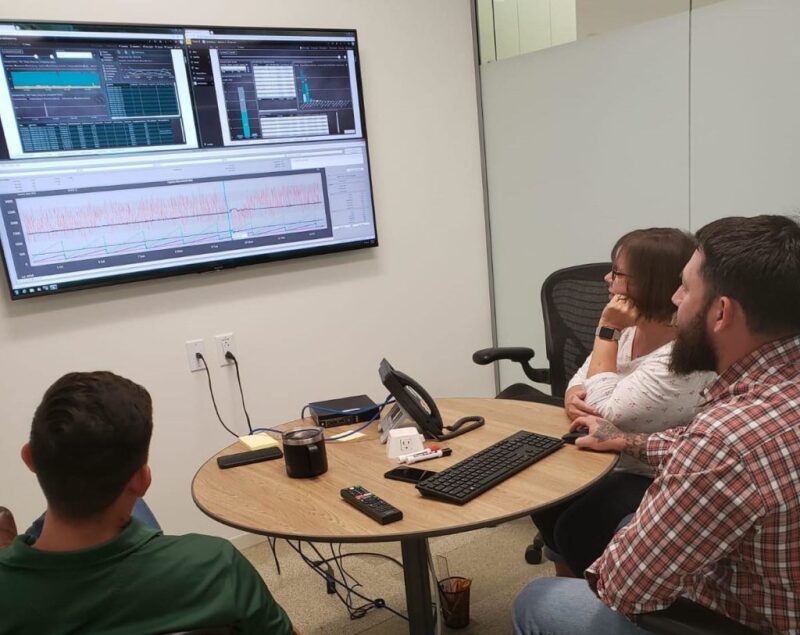
information from PowerBI reports and well details from
SCADA system.
Khuzema Sunel, operations research analyst, Chirality Research, has engineered various automated digital solutions for manual oilfield operations processes using application development and advanced data analytics. He holds a master’s degree in electrical engineering and a specialization in applied data science, which gives him a broad base to address oil and gas industry challenges with data-driven solutions.
Leslie Malone, area production manager, Sanchez, has more than 10 years of experience managing a diverse team of engineers, production analysts, and support teams in all facets of production operations and automation. She holds a bachelor’s degree in petroleum engineering and is a leader in digital transformation in the oil and gas industry, predominantly focused on intelligent operations.
Justin Bender, manager of enterprise applications, Sanchez, has more than 15 years of experience in information technology in the oil and gas industry and holds a bachelor’s degree in management information systems. He specializes in application portfolio management to improve business processes, reduce costs, and ensure end business users always receive the right information from the right source at the right time.