Behavior-based safety is not a new concept nor is it new at Murphy Oil. But when Murphy launched its Safety Observation Program (SOP) as a digital tool, it revitalized the way the culture of safety spread throughout the company.
The digital SOP is a global health, safety, and environment (HSE) portable application that collects and processes safety observations in real time from employees and contractors across business units. The data is analyzed instantly and converted to graphs and visuals that help the company identify hazards, predict trends, take corrective action, and reinforce desirable behaviors. The result is an increasingly proactive and preventive culture of action across Murphy (NYSE: MUR).
Tom Mireles, senior vice president of technical services for Murphy, said the digital solution required an innovative corporate approach. “The message of safety may be coming from the top, but we knew that follow-through would take a bottom-up approach,” he said. “We provided the right tools and technology that would enable field personnel to look for opportunities to improve safety, and they ran with it. SOP is really a grassroots effort.”
The Beginning

Fig. 1—The previous work flow compared with the new work flow for safety-observation submission.
The effort was sparked during a constructively critical discussion with an operations manager from the onshore business unit. The purpose of the conversation was to examine the existing, months-long safety-observation process, methodically assessing where efficiencies could be introduced throughout the work flow. The routine dialogue—paired with a proactive mindset—initiated a rapid fix to automate a critical business component (Fig 1).
Within days, the SOP app emerged. The previously inefficient work flow involving time-lagging manual Scantron forms, third-party compilations, Excel reviews, report creations, and final email distribution was transformed into an efficient, automated, real-time analysis with robust feedback reporting. In seeking improvement and quickly implementing a functioning solution, the SOP initiative aligned stakeholders, resources, and Murphy’s newly launched corporate mission, vision, and values to enable a faster, better safety-observation process. It signaled a departure from following traditional processes out of habit—and a shift toward challenging the norm to deliver inspired energy solutions.
The SOP app was successfully piloted in US onshore operations and subsequently adopted in both offshore Gulf of Mexico and onshore Canada.
“SOP app is a huge step forward in the real-time sharing of observations,” said Barry Jeffery, vice president of HSE for Murphy. “The program encompasses everything that ties into good safety leadership, including clear expectations, observations, timely feedback, correction, and accountability. It’s an exciting breakthrough.”
Real-Time Observations
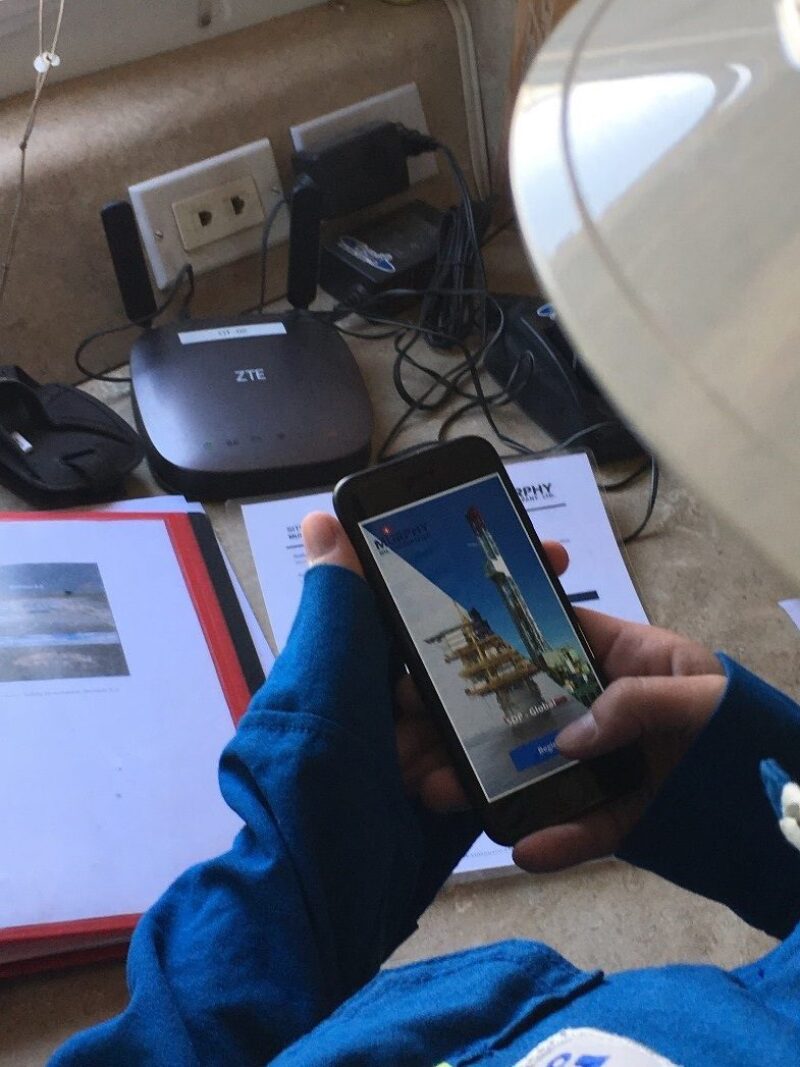
Fig. 2—HSE Field Adviser Chantale Wold prepares to enter her safety observations into the SOP app on-site.
Because a safety observation can occur anywhere—in the field or in the office—the SOP app is available on everyone’s cellphones to expedite the collection of SOP data. When safety practices or hazards are detected, observers initiate observations using the SOP app on their phones or tablets, where they are prompted for information such as date and time, equipment, location, rig, vendor, and business unit. The user-friendly app walks observers through the required information using preset Murphy-specific classifications and allows for supplementary text comments (Fig. 2).
The digital process replaces a manual system in which operators recorded daily observations onto cards by hand. The handwritten documents were scanned and mailed for analysis by a third party, which was a cumbersome, time-consuming process that was further complicated by handwriting that was sometimes difficult to read and documents that were occasionally delayed or lost in the mail. When the information finally reached Murphy, trend analysis still had to be performed manually, making corrections and disseminating the results to thousands of employees. The digital application reduced the time necessary for data analysis and sharing from months to minutes.
For Murphy’s senior onshore operations superintendents Luke Monceaux and Mike Duhon, the real-time observations are transforming onshore operations. The business unit has embraced a culture of operator-owned safety in which their teams can pinpoint and address gaps immediately, clarify policies and procedures, and implement corrections (Fig. 3).
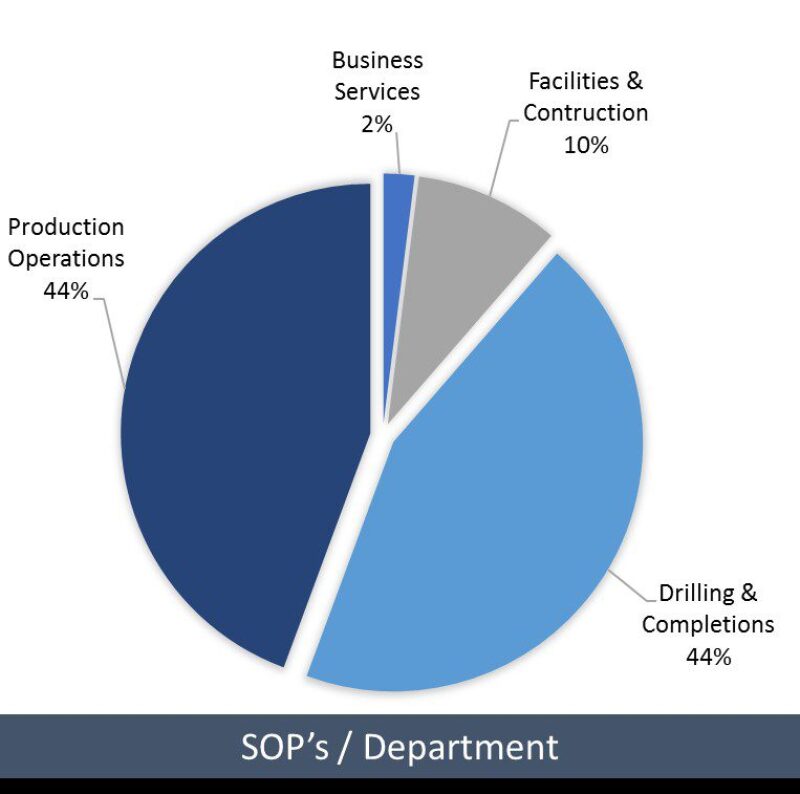
Fig. 3—Departmental breakdown for SOP card submission.
Monceaux offered a case in point. “In one instance, during a pumping unit PM (preventive maintenance), our maintenance supervisor witnessed a frayed piece on a lifting cord. The supervisor stopped the job and took the time to change out the equipment. With this observation, we were able to bring in the contractor’s supervision and explain the importance of their employee’s responsibilities of inspecting their tools and equipment before work. This specific observation was also reflected over in all department weekly safety meetings.”
Duhon said, “It matters that operators can instantly communicate daily safety observations. They go to many different places and do many different things every day, and now they can rely on the app rather than on their memory.”
Agile HSE
The flexibility of the app allows easy collaboration with third parties. In particular, the SOP app effectively captures third-party data without the need to complete multiple paper forms. The standard forms that vendors complete for their companies are captured by the SOP app, which allows third parties to fulfill the expectations and policies of their own companies while significantly increasing the set of data that is typically collected by Murphy. The resulting contractor management platform integrates proactive safety measures and at-risk behaviors to provide a more-robust and -realistic view of the safety culture of vendors.
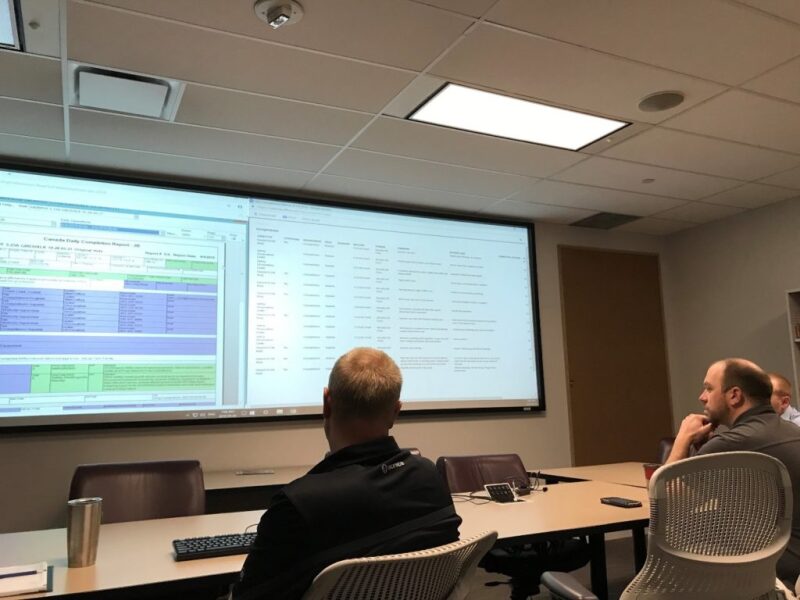
Fig. 4—Completions engineers in Calgary—from left, Jason Baird, staff completions engineer; Adam McConnell, senior water management technologist; and Dan Cave, completions team lead—review safety observations and operational updates during a morning call.
In addition, the real-time nature of the SOP app facilitates increased collaboration with the operational groups. Every morning, each operational group—such as those in drilling, completions, or facilities construction—receives an automated report of the operating conditions from the previous day. This equips them with a better understanding of how the site is performing from a safety viewpoint and provides discussion points for their morning operational calls with on-site leadership. Together, the operational teams and the HSE teams are focusing their efforts on the largest risks as identified in the field (Fig. 4).
Chris Young, HSE analyst for Murphy’s Canadian operations, said, “The SOP app with its reporting capabilities has been a fantastic bridging tool to engage operational groups and equip them to proactively steward safe operations.”
Young said that the feedback from third parties has been positive. “They enjoy having this accessibility to data, which wasn’t previously possible,” he said. “It has led to much more meaningful interactions between operations and HSE that are helping to drive safety performance.”
Proactive Communication
The useable data from the field is driving the corporate conversation. In addition to sharing real-time observations, the SOP app automatically disseminates the data across Murphy every morning in a safety report. All contractors and employees—including leadership and management—are notified automatically of pressing behaviors, trends, and other issues observed in the past 24 hours.
The daily report has established a clear bridge of communication between the field and the meeting rooms. Blake Ulmer, an HSE specialist at Murphy, recounted a revision to an operating procedure that was based on an observation made by an entry-level field operator in the SOP app.
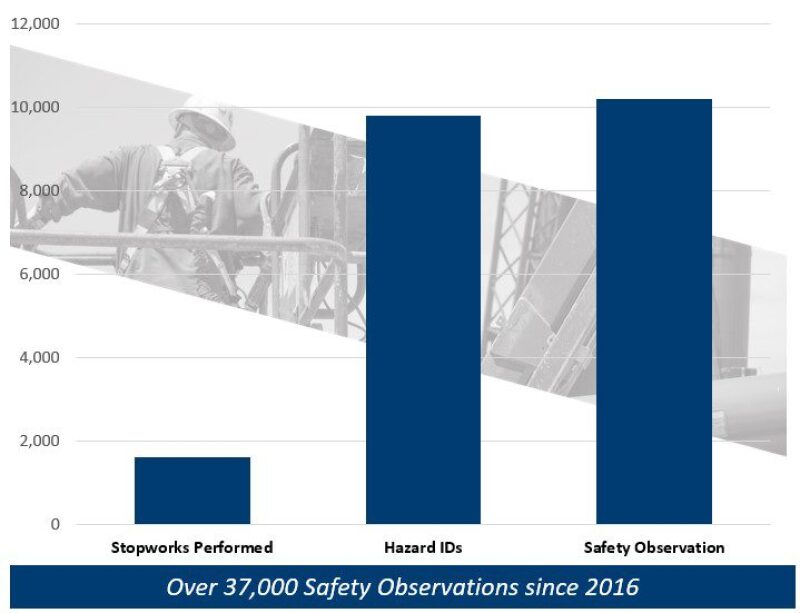
Fig. 5—Commonly collected and processed observations through the SOP App.
“The operator noticed the need to set up a safety perimeter around a work site, so we tested exposure levels over distances and revised our standard operating procedure,” Ulmer said. “I think it’s significant that this new employee’s voice was heard and that he had an opportunity to make such a positive impact.”
This scenario is becoming more common. The observations from field personnel are directly shaping corporate policies and procedures.
Matt Reddin, a rig foreman at Murphy, said, “In the past, the observation cards written at the field level didn’t seem to generate conversations about how to do things differently. There was little transition to the office realm. Now, everyone has a pulse on what’s going on. There are a lot of discussions happening around the digitized content.”
The daily dissemination also helps to concentrate Murphy’s safety efforts where—and when—they are most relevant. While particular details are still fresh on everyone’s minds, safety personnel can provide coaching sessions that are more relevant and impactful. Using SOP data as a mechanism for forecasting incidents allows people to have the opportunity to develop solutions before issues become hazards (Fig. 5).
Aaron Makemson, senior safety training specialist at Murphy, said the effect on the corporate conversation is evident. “I would estimate that the daily automatic report generates 20% of the daily safety meeting topics, due to real-time issues noted,” he said.
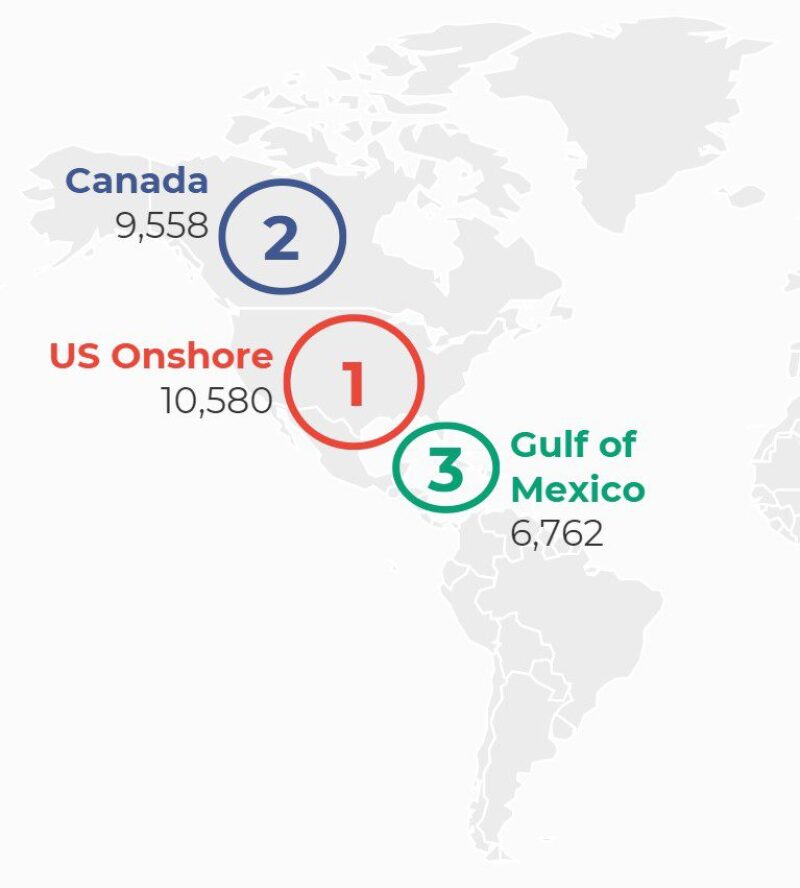
Fig. 6—Distribution of usage across North American assets since launching in 2016.
Global Corrections
Ultimately, the SOP app is facilitating faster solutions for corrective actions among a wider audience at Murphy. Observations that occur on similar equipment or task other assets across the globe can be discussed in real time while they are fresh rather than waiting for safety alerts or lessons learned much later (Fig. 6).
“When an unsafe condition is observed, the app prompts the user to designate whether further action is required—and who is responsible to follow up,” Reddin said. “This provides peace of mind and a level of accountability between departments.”
The SOP app is enabling Murphy to reach beyond its employees to include third-party contractors in the culture of safety. The flexibility of the app—including multiple languages and compatibility with different systems—allows robust, readily available data such as automated reports, lists of hazards, and the tracking progress of follow-up items. As a result, communication with contractors has increased and corrections are made more swiftly and efficiently.
Ulmer said he has seen a reduction in at-risk behaviors and conditions associated with contractors. He recounted a meeting in which he discussed a widespread procedural issue that had been brought to his attention by the SOP app.
“An employee observed a hazard, took ownership of that hazard, and communicated the key details through the SOP app,” Ulmer said. “His actions ultimately allowed us to implement a solution which improved the safety of operations across the field. It’s great to have data to back up what employees are seeing; it’s firsthand information that allows us to evaluate behaviors and conditions in real time.”
But the purpose of the SOP app is not just about fixing what is wrong; it is fundamentally about doing more of what is right, such as creating increasingly efficient and effective hiring practices. Third-party companies are now tracked and graded on internal safety policies and records, which provides Murphy with a history of compliance and a risk-ranking on each contractor. Internally, the SOP app is optimizing business operations by promoting the sharing of knowledge in real time.
“I’ve been a safety specialist for 15 years, so I know a few tricks that I share with others through the SOP app,” Makemson said. “Likewise, I’m learning from my peers. The safety metrics of all locations are visible in the app, so when I notice one location achieves a higher safe percentage; I find out what they’re doing differently. We’re sharpening each other.”
The Future of the SOP App
The continual sharpening of people and of the program itself is the reason that SOP app will continue to drive the safety culture at Murphy.
One reinforcing factor is a built-in incentive program that recognizes people in real time who are performing extraordinarily well. Employees are rewarded for positive safety behaviors, such as thinking quickly on their feet, stopping a potentially bad situation, recognizing potential for improving procedures, saving downtime, and, most importantly, preventing injuries. As a result, they are replicating behaviors that are acknowledged as important to the company.
“The ‘attaboy’ matters. Everybody can’t be everywhere. We get to brag on our coworkers and bring things to light that may otherwise go unnoticed,” Reddin said.
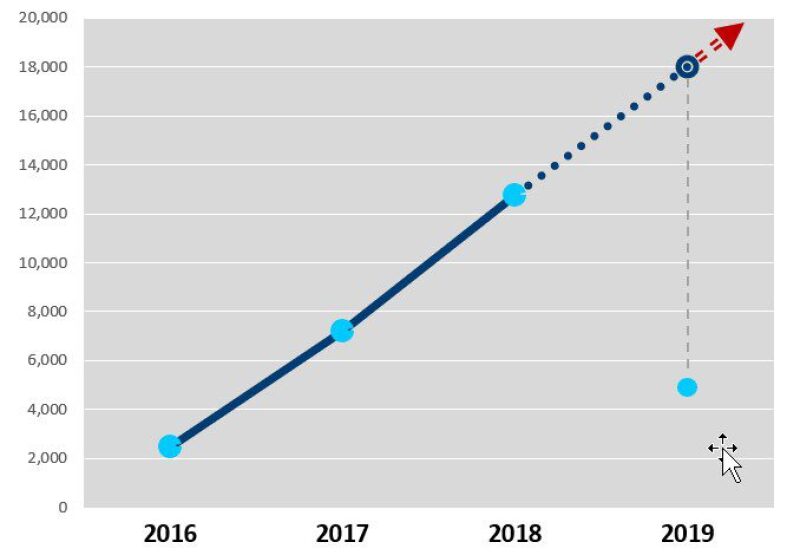
Fig. 7—Murphy is forecasting upward of 18,000 safety observations by the end of the year based on the 2019 year-to-date usage.
Another reason the program is becoming entrenched in the company is the reinforcement of the app itself. While the safety observations are shaping the behaviors of Murphy employees, the people are shaping the functionality of the app through surveys and conversations. The digital program is increasingly effective because of the continual feedback, which has included requests to fine-tune the way observations are categorized and prioritized.
The change in the people and in the approach has revitalized the outlook of safety at Murphy, but it’s also bigger than that. As the open-sourcing of data actively engages third parties and draws critical conversations, operational groups beyond Murphy are becoming part of the solution. The digital safety culture has the potential to spread across the industry.
“The amount of data pouring in is phenomenal. In 2018 alone, we received 13,000 observations through the SOP app. That number will likely increase as the tool becomes more widely utilized,” said Jessica Jackson, Murphy’s senior manager for global offshore HSE and regulatory (Fig. 7). “The HSE data transformation is moving us in the right direction and taking our company to the next level in identifying HSE leading and lagging indicators. We’re excited about what is happening and what is to come.”
Aaron Makemson, Senior Safety Training Specialist, Murphy Oil, has more than 18 years of experience in the oil and gas industry production, construction, drilling, and workover. Makemson is certified as an occupation safety specialist (COSS), radiation safety officer, and emergency medical technician paramedic.
Chris Young, HSE Analyst, Murphy Oil, has worked in industrial safety for more than 8 years, specializing in data-driven safety science. Young holds bachelor’s and master’s degrees from McGill University in biochemistry and bioinformatics.
Huzeifa Ismail, Data Scientist, Murphy Oil, has more than 10 years of experience addressing challenges for the oil and gas industry in the area of engineering and data science. Ismail holds bachelor’s and master’s degrees from Brandeis University and a PhD degree in chemical physics from the Massachusetts Institute of Technology and has authored numerous technical articles and patents.