The shift toward lower oil prices in the oil and gas industry has resulted in the necessity for more wells to be drilled at lower cost, either to sustain production or to generate new, low-cost reserves. With a continued shift in demand for hydrocarbon energy sources, this development is expected to continue with an improvement goal of 30% or more by 2025.
Because drilling costs are a significant contribution to the cost per barrel, the industry is being pressured into finding ways to lower cost per foot drilled. Numerous other industries have shown that they are able to constantly reduce cost per unit; the aviation sector has reduced the cost per mile and passenger, and the automotive industry has constantly reduced the cost per car produced.
Where do we stand today and what will the future possibly look like?
Thirty years ago, it was common to analyze morning reports, drill a few wells, learn from the results, and improve well time. The famous learn curve concept was introduced by Brett and Millheim (SPE 15362) when they studied entire sequences of wells drilled.
In the past decade, we have reached a level where we observe a rig operation for a few days to obtain sufficient data to improve the rig operation utilizing automated operations detection from time-based rig sensor data (Wallnoefer et al., SPE 99880). Morning reporting is now moving toward an automated process driven by machine sensor data.
With this information it is possible to study the consistency of rig operations (Andersen et al., SPE 119746) following, for example, Six Sigma concepts widely used in the manufacturing industry for decades. Many operators and contractors have learned to optimize rig operations toward well-defined performance targets.
Automatically generated and accurate performance data is used to generate a performance gap analysis, which highlights the improvement potential if a well was delivered targeting performance KPIs removing invisible lost time, eliminating problem time as lost time, and optimizing the process (e.g., drillings shoe to shoe).
Closing the gap, as shown in Fig. 1, would likely result in well cost improvement of more than 30%. The factors creating such a performance gap are documented as a result of a highly automated analysis but are based on surface measurements and observations.
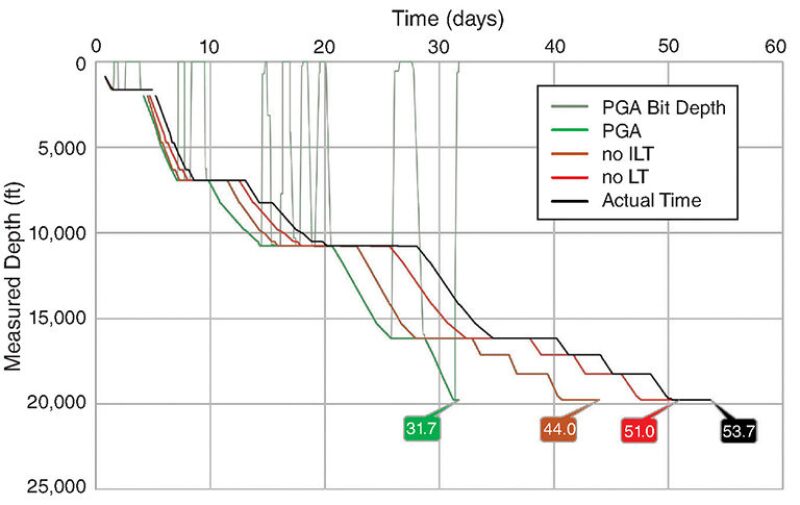
Still, today we hardly see these performance gaps closed from a global perspective. After analyzing more than 25,000 wells, using time-based rig surface sensor data, it is apparent that there are several areas of improvement where surface data-driven analysis is not sufficient to close the gap.
Surface data may be able to generate improvement from 3 to 10%, if used as part of a properly exercised performance initiative focusing on operational consistency, which seems to be accepted in the industry. Evidence for accepting such a limit means “living with” comparably rudimentary rig sensor systems and rather bad surface data quality. In other words, we can accept working with imperfect hookload measurements because even a better measurement would still be a surface measurement.
Step Change in Improvement
The biggest technological and business hurdle to overcome is how to make downhole drilling data available in real time at an affordable price. We need to bring light into the dark. This need was recognized as early as 1939 but increased complexity and cost have been hurdles that prevented breakthroughs in the past.
Currently, the industry does not have data on key factors such as downhole weight on bit and torque available in real time. We do not know the behavior of the drillstring. We are not able to see geometry changes and instabilities of the wellbore over time, or the evolving problems of transporting cuttings. We are not able to recognize losses to or influx from the formation and the type of influx in the well.
We are pretty much driving a car with tinted windows. We get a glimpse of what is going on outside from time to time, in an ideal case every few seconds, but sometimes only after minutes or even hours. As long as you have a straight road without too many obstacles this works pretty well. But with increasing complexity, this method does not work anymore.
Integrated digital downhole drilling systems will close the performance gap, leading toward automating key drilling process steps within a short time, optimizing performance within safe operating windows, and improving HSE. Such systems will offer surface power supply and 10,000 times more data than the best mud-pulsing technology and could be the breakthrough technology to drive drilling automation further. The technology promises precise downhole control and reduces downhole tool complexity and costs significantly while providing downhole power supply from the surface to avoid downhole batteries and turbines.
The disruptive nature of this technology can potentially change existing business models to empower new players or give existing drilling contractors simple, easy-to-run, downhole technology to enable them to deliver an integrated drilling solution with significant cost and performance advantages, the key characteristics of a digital solution.
Persuading end users to embrace new technology is undoubtedly a major challenge because investing in innovation is a high-risk gamble, especially in the volatile oil and gas industry. But the rewards of implementing successful, innovative, and profitable technology, combined with disruptive business models, can be phenomenal, as exhibited in other industries. Make no mistake, digitalization will come, and it will arrive imminently if measurable value can be generated.
![]() | Gerhard Thonhauser, SPE, has more than 20 years of experience providing the industry with disruptive, performance-enhancing technologies in drilling engineering. In 2015 he became head of the Petroleum Engineering Department at Montanuniversitaet Leoben in Leoben, Austria, where he has held the chair in Drilling and Completion Engineering since 2003. Thonhauser has founded several startup companies and, over the past 18 years, has held various management roles in technology companies. He is chairman and chief technology officer of TDE Group, which offers data-driven products and services, artificial intelligence to improve drilling, and downhole technology. He has authored or coauthored more than 100 publications in this area. |